What is Anodizing & Anodization | Junying Custom Metal Finishing Services
Durable and Beautiful Anodizing Services
We offer comprehensive surface treatment solutions including anodizing, micro-arc oxidation, color anodizing, and anodic sealing processes. Our technical team can customize these treatments to meet your specific product requirements and performance needs.
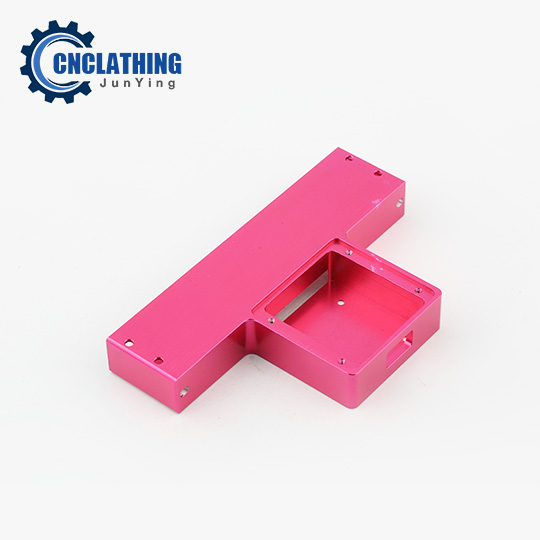
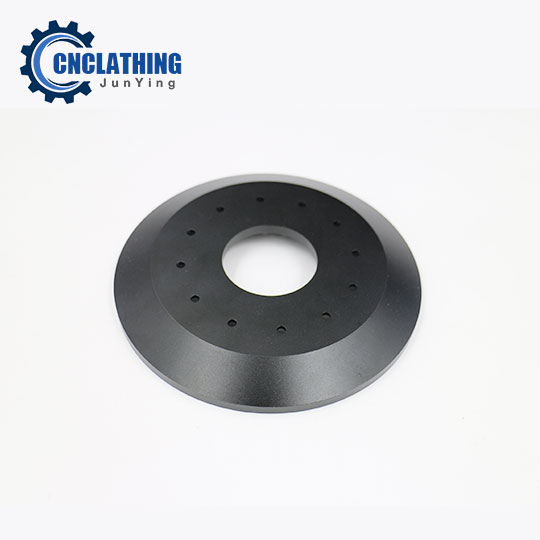
What is ALODINE and what are its process details?
Anodizing is an electrochemical surface treatment process primarily used for aluminum protection and decoration. In this process, aluminum workpieces serve as anodes immersed in acidic electrolyte (typically sulfuric or chromic acid). When current flows, the cathode attracts positive ions from the aluminum while the aluminum surface attracts oxygen ions from the solution, forming an oxide layer. The initially formed oxide film is relatively loose, but as the process continues, the film thickness increases until the oxide formation rate reaches equilibrium with the chemical dissolution rate.
The resulting oxide film has a porous outer layer that can absorb dyes for coloring and decorative purposes. Through subsequent sealing treatment (using hot water, steam, or nickel salts), the oxide film's corrosion resistance, hardness, wear resistance, electrical insulation, and heat resistance can be further enhanced.
Type I, II, III Anodizing
Type I Anodizing (Chromic Acid Anodizing)is the earliest developed and widely used anodizing process, which forms a lightweight film with average protective ability.
Type II Anodizing (Standard Sulfuric Acid Anodizing)refers to the standard anodizing process using sulfuric acid as the electrolyte. Compared to chromic acid anodizing, sulfuric acid forms a denser oxide film with better barrier protection. It is currently the most commonly used process type.
Type III Anodizing (Hard Anodizing)also known as hard anodizing, is a specialized process designed to impart greater hardness to the product. By extending process time and tighter controls, a thicker and harder oxide film can be grown. Thanks to its exceptional wear resistance, this film coating sees wide use in durable applications.
Process Type | Electrolyte | Thickness | Structure | Barrier Protection | Main Application | Color | Gloss |
---|---|---|---|---|---|---|---|
Type I Anodizing | Chromic acid | 2~10μm | Loose | General | Common anodizing | Light color | Low gloss |
Type II Anodizing | Sulfuric acid | 5~25μm | Dense | Better than Type I | Industrial application | Light to medium color | Medium gloss |
Type III Anodizing | Sulfuric acid | 5~50μm | Dense and porous | Strongest | Wear and corrosion resistant applications | Deep color | High gloss |
Standard Anodizing Color Options
At CNC Lathing, we provide a range of standard anodizing color options for your projects. If you require specific RAL or Pantone color matching, please don't hesitate to contact your sales engineer or reach out to us at [email protected] for personalized assistance. Our technical team will work with you to select the most suitable coloring solution and ensure the final product meets your color specifications.
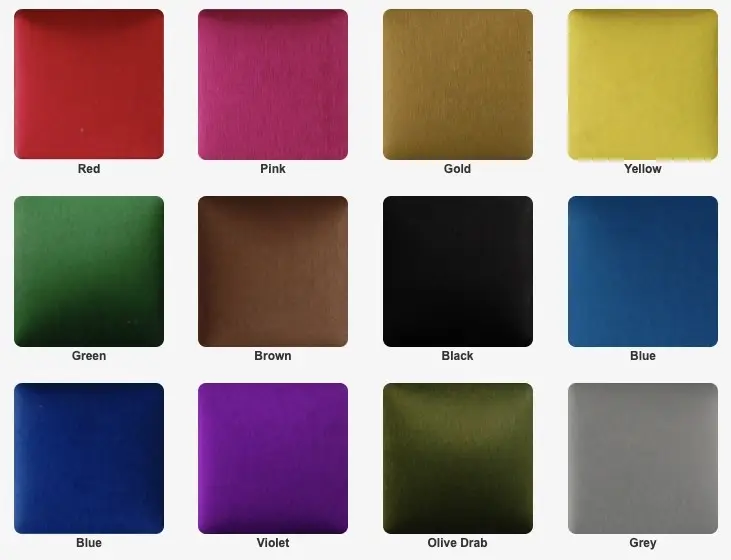
Surface Finishing News
FAQs
Can I provide my RAL or Pantone color code?
Can I provide my RAL or Pantone color code?
Yes, you can specify your desired RAL or Pantone color codes. Please share your color requirements with your sales engineer or contact us at [email protected]. Our technical team will evaluate the feasibility and provide you with the closest possible color match.
Our technical team typically completes color code evaluation within 1-2 working days after receiving your request. The evaluation includes color matching feasibility, process parameter adjustments, and sample testing requirements. If your project is time-sensitive, please let us know when contacting us, and we will prioritize your request.
What aspects of anodizing treatment do users mainly focus on?
What aspects of anodizing treatment do users mainly focus on?
Color: Color is an important component of the appearance effect, and different color options will bring users different experiences.
Glossiness: A smooth and glossy surface looks high-end, which is also one of the requirements that many users like.
Weather resistance: Surface treatment needs to have good weather resistance, without fading or foaming due to long-term use. This directly affects the service life of the product.
Hardness: High hardness ensures a strong and easy to clean surface. A surface that is too soft is prone to friction damage.
Rust prevention ability: Metal products often require rust prevention treatment, which is related to the product’s service life. Good rust prevention ability is highly praised by users.
Environmental factors: Modern users are increasingly concerned about the environmental impact during product production and use. Adopting environmentally friendly treatment processes will receive higher praise.
Cost: Although quality is the top priority, users still prefer to choose processing solutions with relatively lower costs, provided that quality allows.
Processing cycle: The processing process should not be too complicated or cumbersome, as it may affect the product delivery time. While ensuring quality, optimizing processes is also important.
What are the main process equipment standards for anodizing?
What are the main process equipment standards for anodizing?
The major standards include electrolytic tank standards, power source standards, transmission line standards, and temperature and time control standards.
What are the main testing standards for anodizing?
What are the main testing standards for anodizing?
The key testing standards are film thickness testing standards, hardness testing standards, transparency testing standards, corrosion resistance testing standards, color matching testing standards, and mechanical property testing standards.
How to maintain and extend the service life after anodizing treatment?
Regularly clean the cross-section and hard to reach areas to prevent dirt and corrosion.
For areas that frequently come into contact with moisture, rust inhibitors or corrosion protection films can be applied appropriately.
Avoid long-term storage in high temperature and high humidity environments to prevent a decrease in the quality of the crystalline film.
It is best to rinse with clean water before cleaning to remove acidic components from dirt. Choose cleaning agents that do not contain harmful acids.
Prevent high-intensity mechanical friction, be careful to avoid impact and abrasion damage to the surface.
Regularly check the condition of the film layer, and repair and maintain it immediately if cracks or detachment are found.
What metals can be anodized?
In addition to aluminum, other metals that can be commonly anodized include titanium, molybdenum, zinc, vanadium, cobalt, nickel alloys, steel, cadmium, tantalum and zirconium.
Among them, the anodizing processes of titanium and molybdenum are also well established. Zinc is widely used for corrosion protection and anodizing forms a durable protective layer. Vanadium and cobalt see more use in specialized mechanical or aerospace applications. Steel also has industrial value. Meanwhile, cadmium, tantalum and zirconium are typically used in high temperature, corrosive environments.