CNC Plastic Machining Services – Custom Machined Plastic Parts Manufacturer in China
CNC Plastic Machining Services – Custom Machined Plastic Parts Manufacturer in China As a China-leading CNC parts manufacturer, Junying is specialized in fabricating various custom-machined plastic parts using CNC equipment and technologies, our CNC plastic machining services provide the most efficient and economical solutions for rapid prototyping and mass production runs. Extensive experience and skilled experts enable us to work with complex shapes and rare materials, and produce customized plastic CNC machining parts according to customers’ needs. We’ll select high-quality and high-performance plastic materials, whether you want ABS, PS, PC, Nylon, PEEK, PA, POM, or other types to make the products. Junying is a CE and ISO 9001 certificated CNC manufacturer and is able to offer high-precision CNC machined plastic parts with tight tolerances and premium properties required in critical industries.
Why Choose Junying Plastic CNC Machining Services?
-
A wide selection of high-performance engineering plastic materials in stock
-
State-of-the-art machining, manufacturing, and measurement facilities
-
Complete quality management system and professional inspection before shipment
-
Premium quality CNC plastic parts with custom specifications and high accuracy
-
Strong capacity for CNC programming, 5-axis machining, and precision production
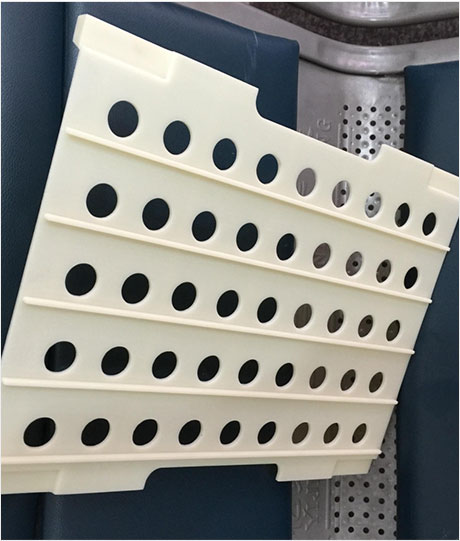
CNC Plastic Machining Materials at Junying
- CNC Machining ABS (Acrylonitrile Butadiene Styrene)
- CNC Machining POM (Polyoxymethylene)/Acetal/Delrin
- CNC Machining PE (Polyethylene)/HDPE/LDPE/UHMW-PE
- CNC Machining PMMA (Polymethyl Methacrylate)/Acrylic
- CNC Machining PA (Polyamide)/Nylon
- CNC Machining PC (Polycarbonate)
- CNC Machining PEEK (Polyetheretherketone)
- CNC Machining PTFE ( (Polytetrafluoroethylene)/Teflon
- CNC Machining PS (Polystyrene)
- CNC Machining PP (Polypropylene)
- CNC machining PVC (Polyvinyl Chloride)
- CNC machining Garolite G-10
CNC Plastic Machining Services & More Capabilities at Junying
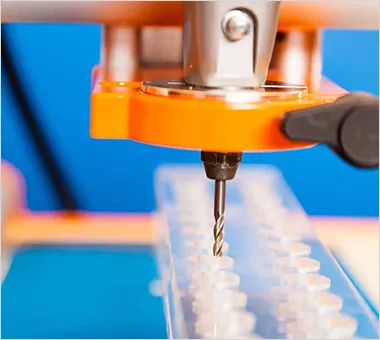
Plastic CNC Fabrication
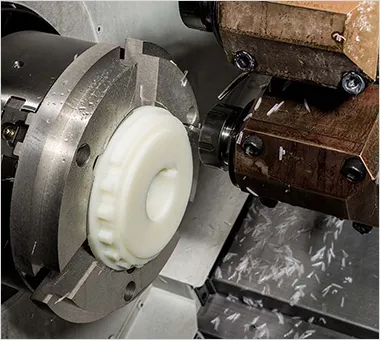
Plastic CNC Turning
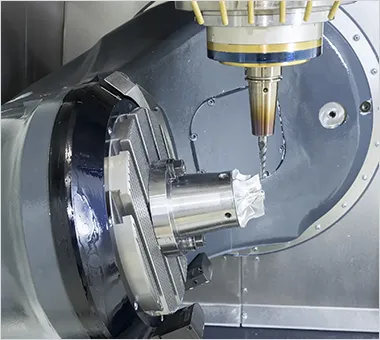
5-Axis Plastic Machining
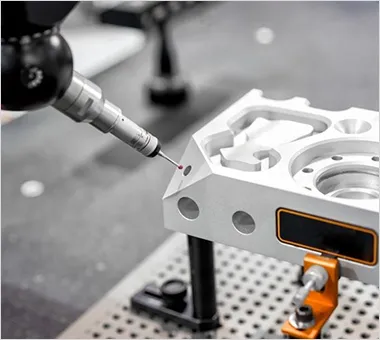
Full 3D CMM Measurement
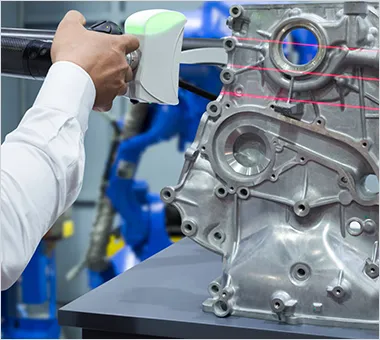
Laser Scan and Reverse Engineer
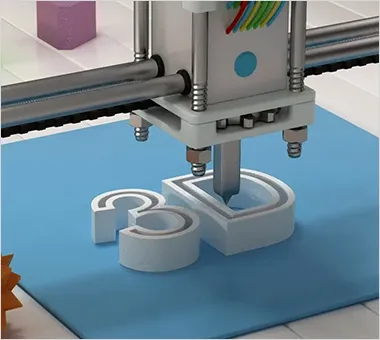
3D Printing Services
Common Plastic Manufacturing & Fabrication Techniques
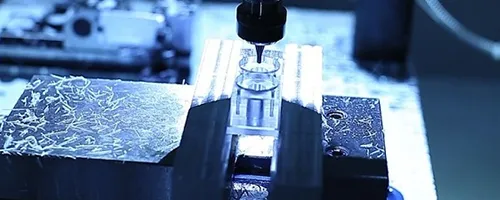
a machining process that involves removing material from a plastic workpiece using a rotating cutting tool. The workpiece is secured to a work-holding device such as a vise, clamp, or fixture. The cutting tool is brought into contact with the workpiece and rotated at high speeds. As the cutting tool rotates, it removes material from the workpiece, producing the CNC milled plastic parts with desired shape and size.
Sizes: 1-14,000 mm (length), 1-2,500 mm (width), 1-730mm (thickness), up to 3,500 mm (ø)
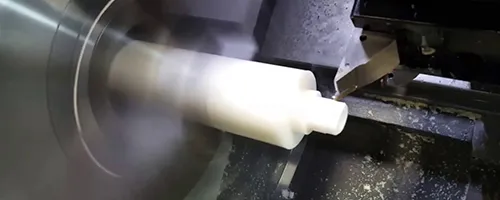
a machining process used to shape a plastic workpiece on a lathe. Turning involves rotating the plastic workpiece on a lathe while a cutting tool removes material from the workpiece to create the desired shape and size. The cutting tool can be a single-point cutting tool, a parting tool, a boring tool, or a grooving tool.
Sizes: 0.5-2,000 mm (ø), max.2,300 mm (length)
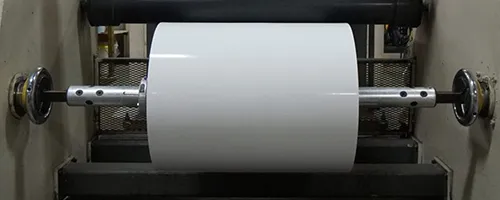
a process used to produce continuous lengths of plastic profiles with a constant cross-section. The process involves feeding plastic material (usually in the form of pellets or powder) into an extruder, which melts and mixes the material and then forces it through a die to form the desired shape.
Sizes: ranging from 0.25” wide and .0005” thick to 12” wide and 4” thick
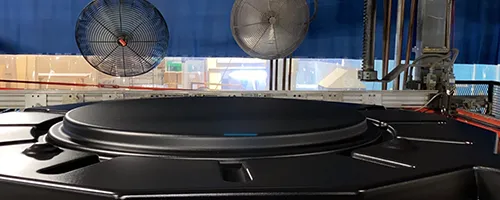
a manufacturing process used to form thin sheets of plastic into three-dimensional shapes by heating and molding the plastic material. During the process, the plastic sheet is heated to a specific temperature until it becomes pliable, and then shaping it into the desired form using a mold.
Sizes: max. 1,600 mm (length), max. 1,200 mm (width), max. 30 mm (panel thickness)
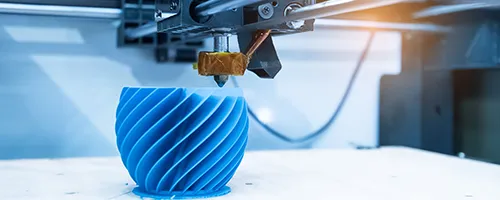
a process of creating three-dimensional plastic objects by adding layer upon layer of plastic material. The process involves using a computer-aided design (CAD) file to guide the printing process and create the desired object. Typical 3D printing technologies include FDM, SLA, SLS, etc.
Sizes: varies based on the technology and material, for example, 750 x 550 x 550 mm of SLS
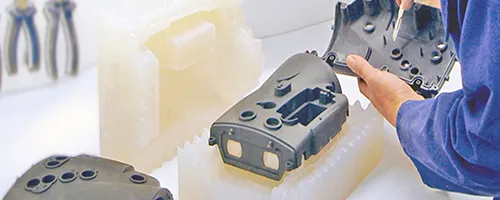
also known as Urethane casting or Polyurethane casting, a process that uses silicone molds to make plastic and rubber components by pouring liquid plastic material into the mold under a vacuum.
Sizes: min. 0.75 mm (mold wall thickness), max. 1900 x 900 x 750 mm.
Surface Finishing & Treatment Processes for Plastic Parts
A variety of surface finishing and treatment processes can also be performed on plastic products, sometimes the surface finish can even be comparable to metals.
Painting | applying a layer of paint or coating onto the plastic surface, which adheres to the plastic and forms a protective layer. |
In-mold Decoration (IMD) | putting the printed film into the mold in different types to obtain a molded part with printed texture after the plastic injection molding. |
Plating | immersing the plastic part into an electrolytic bath containing metal ions, and then applying an electrical current to deposit the metal onto the surface of the plastic. |
Printing | printing the required patterns on the surface of plastic parts through different methods, including pad printing, screen printing, and water transfer printing. |
Laser Engraving | also known as laser marking, label or mark the plastic components using a laser machine, to type of pattern on the surface of the product. |
Thin Film Deposition | a process by which very thin layers are deposited on a substrate |
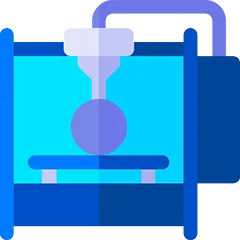
Plastic CNC Machining Parts Required
Contact UsWhat Plastics Can Be CNC Machined?
In plastic CNC machining, the final product is made by removing excess materials from a plastic block using digital computer control machines. A wide selection of plastic and polymers can be machined on CNC equipment, check out some of the common CNC machining plastics, with their characteristics and applications.
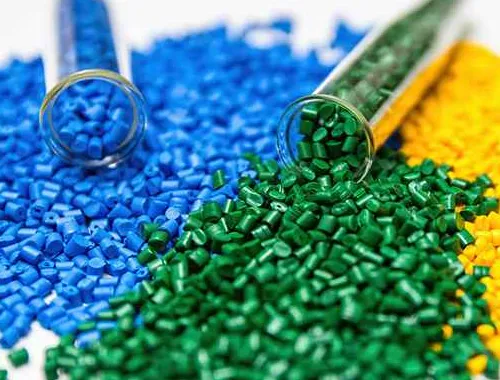
ABS
It has excellent impact resistance, heat resistance, low-temperature resistance, chemical resistance, and electrical properties. It also has the characteristics of easy machining, stable sizes, and a good surface finish. ABS plastic is easy to paint, and a range of secondary processing can be performed on ABS plastic parts such as surface metal spraying, electroplating, welding, hot pressing, and bonding. CNC machining ABS is widely used in machinery, automobile, electronics, instruments, meters, textiles, and construction. ABS is usually light yellow or milky white granular amorphous resin. ABS is one of the most widely used engineering plastics.
Polyamide (PA or Nylon)
There are two types of Nylon commonly used in CNC plastic machining: Nylon 6 and Nylon 66. Polyamide Nylon 6 has the most superior comprehensive properties, including mechanical strength, stiffness, toughness, mechanical shock absorption, and wear resistance. These characteristics, together with good electrical insulation and chemical resistance, make it a general-purpose material for the manufacture of mechanical structure parts and maintainable parts. Compared with Nylon 6, Nylon 66 has better mechanical strength, stiffness, heat resistance, wear resistance, and creep resistance, but its impact strength and mechanical damping performance are reduced. It is very suitable for automatic lathe machining. PA66 is more widely used in the automotive industry, instrument shells, and other products requiring impact resistance and high strength.
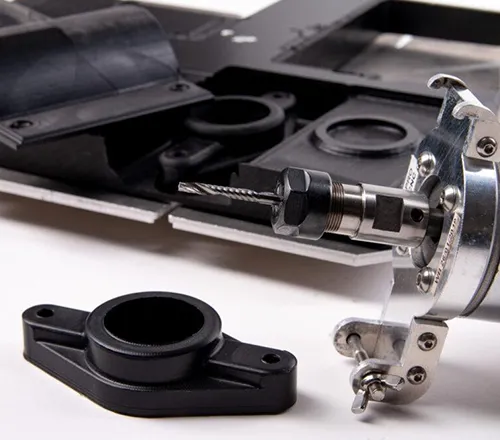
POM
also known as Delrin or Acetal, is a tough and elastic material, which has good creep resistance, geometric stability, and impact resistance even at low temperatures. The high crystallinity of POM leads to its high shrinkage. POM has a very low friction coefficient and good geometric stability. It is especially suitable for making gears and bearings. Because it also has high-temperature resistance, Therefore, it is also used for pipeline devices (valves, pump housings), lawn equipment, video recorders, radios, headphones, stereos and other audio machines, printers, keyboards, CD-ROM drives, washing machines, hairdryers, and other household appliances, mechanical parts of safety belts, automobile parts such as door external handles, mirrors, and engine rooms, as well as precision parts such as cameras, clocks, and watches, as well as building materials, toys such as game consoles.
PMMA
also known as Acrylic, is an important thermoplastic developed earlier. PMMA has the advantages of good transparency, chemical stability, mechanical properties and weather resistance, easy dyeing, easy processing, and beautiful appearance. Plexiglass is also called gelatin glass, acrylic, etc. The material is widely used in the production of advertising light boxes, nameplates, etc.
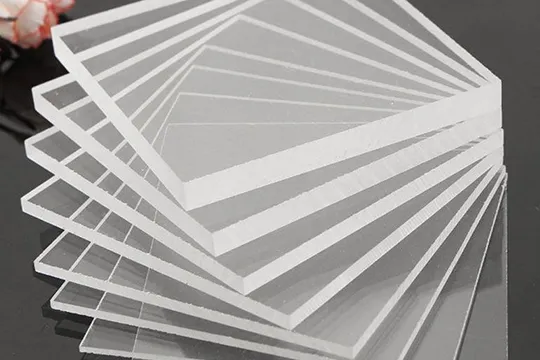
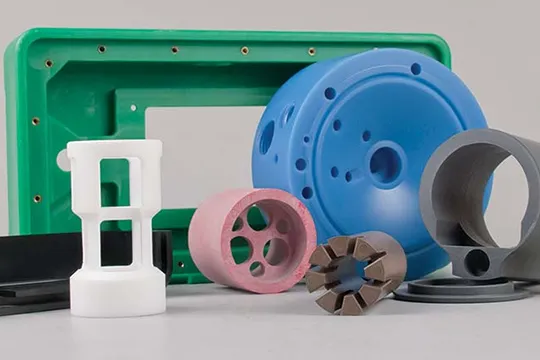
PC
PC is a high molecular polymer containing a carbonate group in the molecular chain. The three application fields of PC engineering plastics are the glass assembly industry, automobile industry, electronics, and electrical industry, followed by industrial machinery parts, optical discs, packaging, computer and other office equipment, medical and health care, film, leisure, and protective equipment, etc.
PEEK
Polyether ether ketone (PEEK) resin is a kind of special engineering plastic with excellent performance. Compared with other special engineering plastics, it has more significant advantages, such as positive high-temperature resistance of 260 ℃, excellent mechanical properties, good self-lubrication, chemical corrosion resistance, flame retardancy, peeling resistance, wear resistance, nonresistance to strong nitric acid, concentrated sulfuric acid, radiation resistance, and super mechanical properties. It can be used in high-end machinery Nuclear engineering and aviation technology.
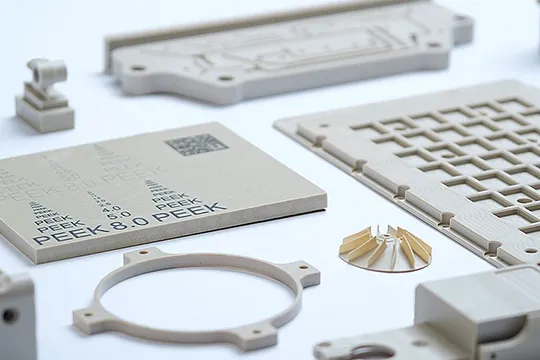
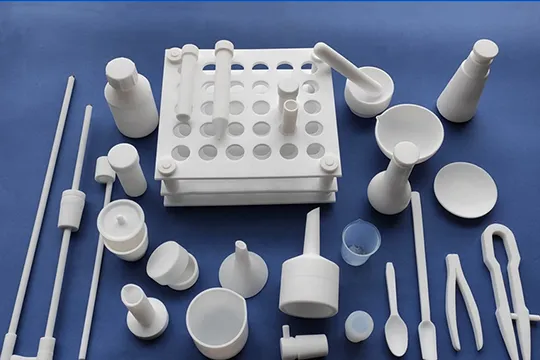
PTFE
Teflon is a synthetic polymer material that uses fluorine to replace all hydrogen atoms in polyethylene. This material has the characteristics of acid resistance, alkali resistance, and resistance to various organic solvents, and is insoluble in almost all solvents. At the same time, polytetrafluoroethylene has the characteristics of high-temperature resistance and its friction coefficient is very low, so it can be used as a way of lubrication. It has also become an ideal coating for the inner layer of nonstick boilers and water pipes.
PE
Polyethylene is a widely used thermoplastic material that can be easily melted and reformed, PE materials can be produced in various forms, such as high-density polyethylene (HDPE), low-density polyethylene (LDPE), and linear low-density polyethylene (LLDPE), each with its unique properties and applications. Polyethylene is a popular choice for CNC machining due to its excellent machinability, low cost, and good mechanical properties. It can be easily machined into complex shapes and parts. HDPE is commonly used for making water pipes, packaging, and chemical containers due to its high strength and resistance to chemicals, while LDPE is used for making plastic bags, films, and sheets. A typical type of polyethylene is UHMW-PE (Ultra-High Molecular Weight Polyethylene), it has a higher tensile strength, impact resistance, abrasion resistance, low coefficient of friction, and excellent chemical resistance. UHMW-PE is also an ideal material for plastic CNC machining.
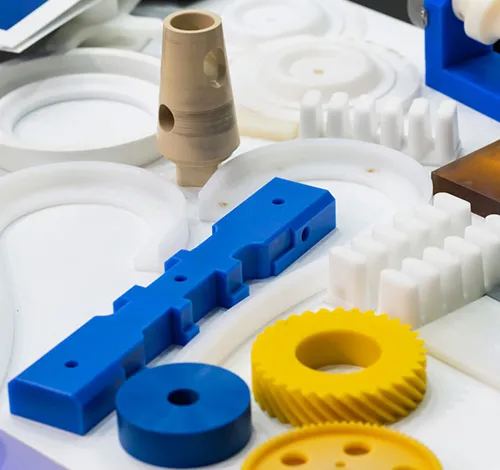
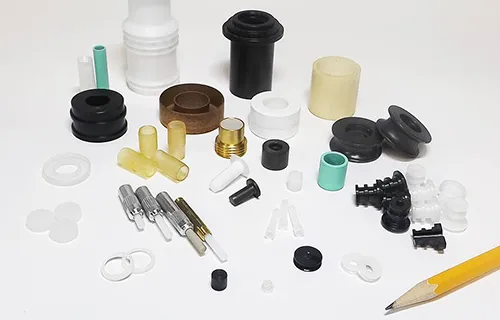
PP
Polypropylene is a thermoplastic material that is lightweight, durable, and inexpensive, also resistant to many chemicals, and has a high melting point, PP is suitable for use in high-temperature applications. The excellent machinability, low cost, and great mechanical properties make PP plastic ideal for CNC machining, especially making complex shapes and parts. Polypropylene is often used in automotive, packaging, and electronics, commonly machined PP parts such as sockets and switches.
Both CNC machining and laser cutting are popular techniques for cutting plastics, and each of the processes has its own advantages and disadvantages. The better option is determined by the specific requirements.
– CNC machines are known for their accuracy and precision in cutting. They can cut plastics of various thicknesses, sizes, and shapes. CNC machines can also perform different types of cuts, including drilling, routing, and engraving. Plastic CNC machining can be used for both 2D and 3D cutting and can work with a wide range of materials. If precision and accuracy are the most important factors, CNC machining may be the better choice.
– Laser cutters are very precise and accurate as well, and are particularly good at cutting thin sheets of plastic. Laser cutters can produce intricate designs with a high level of detail, and can cut through thick plastics quickly and efficiently. They also leave a clean, polished edge on the cut surface, which can be an advantage in some applications. If intricate designs and clean edges are needed, a laser cutter may be the better option.
There is a wide range of cutting speeds for plastics according to the type of material, thickness, cutting method, equipment, and more factors. If you are using a CNC machine to cut plastic, the cutting speed can range from a few inches per minute (IPM) for thicker materials like acrylic or polycarbonate to several hundred IPM for thinner materials like PVC or HDPE. As a general guideline, the cutting speed for plastic on a CNC machine can range from 50 IPM (1,270 mm/min) for thicker materials such as acrylic or polycarbonate to 500 IPM (12,700 mm/min) for thinner materials such as PVC or HDPE.
Generally, plastic CNC machining can range from a few dollars for simple parts to several hundred or even thousands of dollars for more complex and larger parts. Welcome to upload your drawing on CNCLATHING.COM to get a free online quote quickly. The cost of plastic CNC machining is affected by various factors.
– Material cost: The cost of the plastic material used for CNC machining can vary widely depending on the type, grade, and quantity needed.
– Machining time: The amount of time required to machine the part will affect the total cost. The longer the machining time, the higher the cost.
– Labor cost: The cost of the labor required to program and operate the CNC machine will also impact the overall cost.
– Tooling cost: The cost of the cutting tools used for CNC machining will be different because of the type, size, and the number of tools.
– Post-processing and finishing costs: Additional processes such as polishing, sanding, or coating may be required after machining, which can also increase the cost.