Investment Casting Services & Parts Supplier – China Lost Wax Investment Castings Manufacturer
If you focus on the shape complexity and surface finish of the parts, investment castings are where you can go. In order to meet the mass production requirements of some customers and reduce the cost, we work with our suppliers to assist your project. Junying investment casting services can reduce the processing time and cost of CNC machining parts, as we can manufacture a large number of prototypes in batch quickly and modify the appearance with CNC techniques to deliver the final desired parts. Whether you want to look for an investment casting manufacturer casting stainless steel, carbon steel, aluminum, or brass, professional technicians will perform investing casting process with a wide variety of metals, and be able to offer complex detail, smooth surface finish, and high definition in an economic way for clients. Our investment casting parts are used across broad fields, such as energy, automotive, gas, and oil, food, etc. ISO 9001 certification and multiple-stage quality inspection implementation will ensure the quality and performance of the lost wax casting products to be delivered.
Why Choose Junying Investment Casting?
- Close design review on tolerances, undercuts, and more details for higher production yields and lower cost.
- If CNC services are required, advanced equipment and extensive experiences will work on less budget and time.
- From concept to prototype to end-use products, our experts will help you with an advantage of speed and reliability.
- Metal surface finishing, quality assurance testing, and more services can be provided to make the castings fit specifications.
- Full-service investment casting factory and high automation reduces the time of each step, ensure the shortest lead time.
Materials Used in Lost Wax Casting – Types of Investment Castings
- Stainless Steel Investment Castings: 410, 416, 420, 303, 304, 304L, 316, 316L, 17-4PH, etc.
- Alloy Steel Investment Castings: 1045, 1050, 4130, 4140, etc.
- Copper Alloy Investment Castings: CDA 872, CDA 875, CDA 903, etc.
- Aluminum Investment Castings: 356
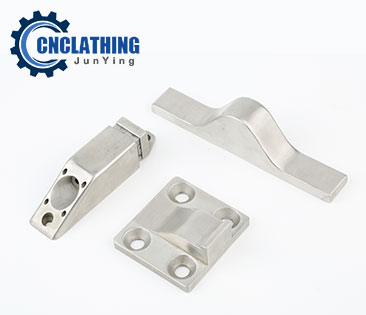
What is Investment Casting?
Investment casting, also known as lost-wax casting, is one of the oldest known metal-forming techniques. The reason why investment casting goes its name is that the process invests the wax pattern with refractory materials to form the mold, and the molten material is cast into the die. The shape of the cavity inside the mold is an exact duplicate of that of the desired product. Common materials used in investment casting including stainless steel, carbon steel, aluminum, and brass. Investment casting has been used in the last 5000 years, in the earliest time, beeswax was used to form the patterns, later, more advanced waxes are applied to make the wax mold. Most of the wax used in lost wax casting can be recycled. Investment casting is a popular manufacturing way because it is capable of producing parts with high accuracy, repeatability, and integrity in a variety of metals and alloys.
How Does Investment Casting Work? – Investment Casting Process
Investment casting (lost wax casting) is the process of using wax to make the mold of the parts to be cast, and then the wax mold is coated with mud, which is called clay mold. After the clay mould is dried, heat and melt the inner wax mould. Take out the clay mold after melting the wax mold and bake it into a ceramic mold. Generally, the gate system is left when making the mud mold, then the molten metal can be poured into the mold. Cool it until the part solidifies, the required parts are made.
Steps of Investment Casting Process
- Inject wax into a permanent die form wax pattern with the same details of the cast part.
- Assembly multiple wax components to form the gate and runner system.
- Immerse the entire wax assembly in refractory material like ceramic slurry, make it fully covered with the stucco, and forms a ceramic shell, which is built around a tree assembly by repeatedly dipping a pattern into a slurry.
- Heat the entire assembly to melt away the wax.
- When the residual wax pattern and gate material have been removed, the ceramic mold remains with a cavity in the shape of the part.
- Preheat the metal and pour the molten metal into the mold.
- Once the castings cooled, remove the part from the mold.
- Post-processing and machining to achieve required specifications.
- Dimensional and quality inspections and other testings before shipment.
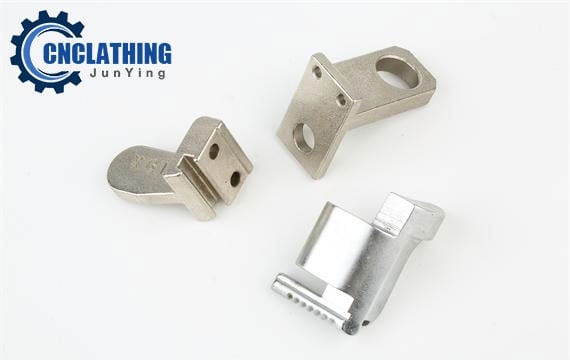
Advantages of Investment Casting
- Investment casting can provide complex configurations of various alloys, such as intricate passages and contours with consistent close tolerances. Some of them can hardly be done with machine tools.
- Even though most investing castings are in relatively small sizes, some investment casting companies with advanced machines and special expertise have the ability to make cast parts weigh more than 1000 pounds.
- Multiple components can be combined into a single investment casting at one time through lost wax casting, which makes it a good alternative to welding. This also gives higher dimensional accuracy and lower complexity.
- The high integrity of investment castings enables it to serve various applications for a long time, including chemical, medical, defense, automotive, and more.
- The ceramic shell is created using refractory coating made of high temperature resistant special binder and refractory material, which is coated on the wax mold. The inside surface of the cavity which is in direct contact with the molten metal is smooth. Therefore, the surface finish of investment castings is higher than that of ordinary castings.
- Good dimensional accuracy and surface finish reduces the needs of post-machining work, only leave a little machining allowance in the parts with higher requirements, investment casting can save a lot of cost of equipment and shorten the whole processing time.
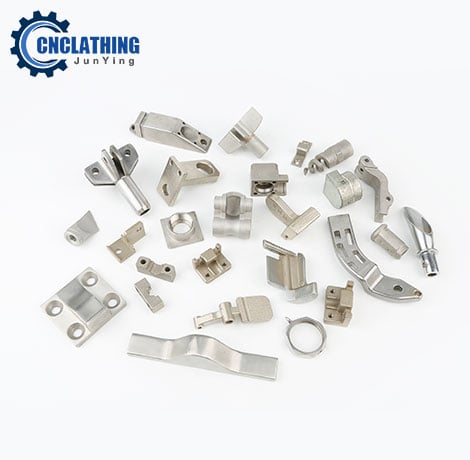