Understand Chrome Plating: Definition, Process & How to Remove Chrome Plating | CNCLATHING
High-Quality Electroplating Services for Precision Parts
At CNCLATHING, we pride ourselves on offering top-tier electroplating services tailored to meet the most complex industrial needs. Specializing in a wide range of finishes, including gold, nickel, silver, copper, rhodium, and palladium plating, we ensure that your parts achieve the highest quality surface finishes. Whether you need plating for intricate CNC precision-machined components or large-scale parts, our expertise spans across various industries, including medical, aerospace, and automotive sectors. Utilizing advanced electroplating techniques, such as selective plating and engineered solutions, we optimize the durability, conductivity, and corrosion resistance of your products. With a focus on precision and flexibility, CNCLATHING works closely with customers to develop innovative, custom plating solutions that meet stringent industry specifications. Trust us to enhance the performance and appearance of your parts with our reliable, high-quality electroplating services.
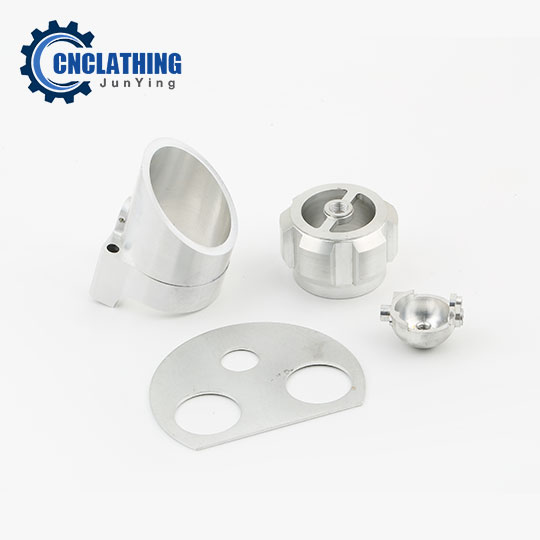
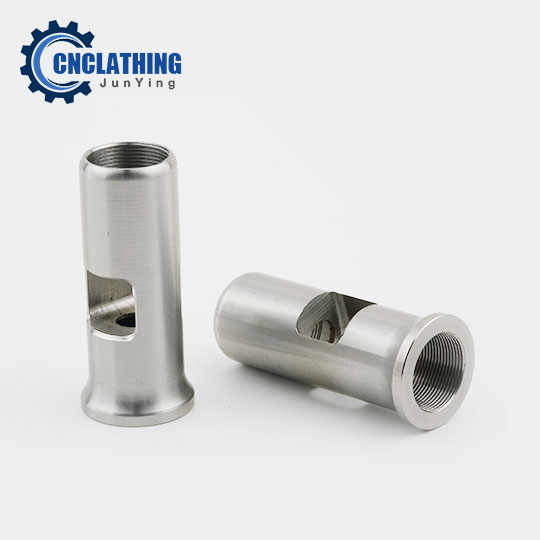
What is Electroplating (Plating)?
Electroplating, also known simply as plating, is process that uses electrical current to coat the surface of an object, typically metal, with a thin layer of another metal for both functional and decorative purposes. The object to be plated (cathode) is submerged in an electrolyte solution containing metal ions, and a second metal (anode) provides the ions that deposit onto the object’s surface when current is applied. This technique enhances properties like corrosion resistance, electrical conductivity, wear resistance, and aesthetics, making it widely used in industries such as automotive, electronics, and jewelry. Electroplating is cost-effective, allowing manufacturers to use expensive metals like gold or silver as thin coatings rather than solid materials, but it requires precise control for uniformity and adhesion, and involves environmental considerations due to the chemicals used.
Benefits of Electroplating Finish
Corrosion Resistance: Protect your parts from harsh environments with durable metal coatings.
Enhanced Appearance: Achieve a lustrous, polished finish that improves the aesthetic appeal of your products.
Improved Electrical Conductivity: Metals like gold and silver can significantly boost the conductivity of electrical components.
Cost Savings: Electroplating finish at CNCLATHING allows you to use less expensive base materials while applying high-performance coatings only where needed.
Electroplating (Plating) Process Methods
Electroplating is a versatile process that can be applied using different methods depending on the desired outcome, the materials involved, and the specific industrial requirements.
Electroplating Materials & Color
Color: Reddish-brown.
Usage: Used in electrical components, as a base layer for other metals, and decorative items.
Color: Silvery-white with a slight yellowish or bluish tint.
Usage: Used as a base layer for other metals (like chrome). Also used for corrosion resistance and decorative purposes.
Color: Ranges from yellow to rose, depending on the alloy used.
Usage: Jewelry, electronics (due to its excellent conductivity and resistance to corrosion), decorative finishes.
Color: Bright, shiny white.
Usage: Jewelry, cutlery, electronics (as a conductor), mirrors.
Color: Bright, mirror-like silver.
Usage: Automotive parts (like bumpers and trim), tools, and hardware due to its high durability and resistance to corrosion.
Color: Dull grayish-silver.
Usage: Primarily used for corrosion protection (galvanization), especially for steel items like bolts and outdoor structures.
Color: Shiny, reflective silver (bright finish) or dull grayish-silver (matte finish).
Usage: Used for corrosion resistance, solderability, and non-toxicity in industries such as electronics, food packaging, and automotive components.
Color: Bright, reflective, silvery-white.
Usage: Commonly used in jewelry (especially over silver and white gold) and for mirrors due to its high reflectivity and durability.
Color: Silvery-white, similar to platinum but slightly darker.
Usage: Jewelry, electronics, and as a cheaper alternative to platinum.
Electroplating (Plating) Finish Color Chart by Metal
Plating Type | color |
---|---|
Gold Plating | Yellow/Gold |
Silver Plating | White/Silver |
Nickel Plating | Silvery/Gray |
Copper Plating | Reddish-Brown |
Chrome Plating | Bright Silver/Blue |
Rhodium Plating | Bright White |
Palladium Plating | White/Silvery |
Zinc Plating | Dull Gray/Blue |
Tin Plating | White/Silver |
Brass Plating | Golden/Yellow |
Black Nickel Plating | Black/Gray |
Zinc-Nickel Plating | Silvery/Gray |
Titanium Anodizing | Multi-Colored(Rainbow) |
Applications of Electroplating Services from CNCLATHING
We offer a wide spectrum of metal finishes that can be applied to various parts. Our electroplating services are employed across a broad spectrum of industries, including:
Aerospace: Enhance the corrosion resistance of critical components such as landing gear and turbines.
Medical and Dental: Improve the hardness and longevity of surgical instruments and medical devices.
Automotive: Protect and beautify components like wheels, exterior panels, and steering columns.
Electronics: Boost the conductivity of circuit connectors and other small electrical components.
Jewelry: Apply precious metals like gold and silver for decorative and functional finishes.
Related News
FAQs
How Does Electroplating Work?
Electroplating works by using an electrical current to coat an object (the cathode) with a thin layer of metal. The process begins by submerging the object to be plated in a solution called an electrolyte, which contains dissolved metal ions of the metal to be deposited. A second metal piece, known as the anode, is also placed in the electrolyte and serves as the source of metal ions. When an electrical current is applied, metal ions from the anode are drawn toward the cathode, where they gain electrons and deposit as a solid metal coating on the object’s surface. The thickness of the coating is controlled by adjusting the strength and duration of the current, as well as the temperature and composition of the electrolyte solution. This process allows for precise control of the final metal layer’s properties, such as hardness, conductivity, and corrosion resistance.
What is Electroplating Used For?
Corrosion Protection: Common metals like iron and steel are plated with zinc, nickel, or chromium to protect them from rust and corrosion.
Aesthetics and Appearance: Items such as jewelry, watches, and decorative objects are plated with precious metals like gold or silver to improve their appearance and value.
Enhanced Properties: Electroplating can enhance certain properties of the base material, such as wear resistance, electrical conductivity, and surface hardness.
Electrical Conductivity: Metals like copper and gold are plated onto electrical components to improve conductivity in connectors and other components.
How Long Does Electroplating Take?
The duration of the electroplating process can vary significantly depending on several factors, including the type of metal being deposited, the desired thickness of the plating, the size and complexity of the parts, and the specific electroplating technique used.
What are the best Electroplating Methods for the money?
The best electroplating method for the money depends on the specific needs of your project, including the type of material being plated, its intended use, and budget constraints. However, if you’re looking for an electroplating method that offers the best balance between cost and performance, these eletroplating methods are the best ones for the money:
● Nickel plating stands out as one of the most cost-effective electroplating options due to its excellent balance between affordability, durability, and versatility. It provides superior corrosion resistance, wear resistance, and a smooth, attractive finish, making it suitable for a wide range of industries, including automotive, aerospace, electronics, and consumer goods. Additionally, nickel can serve as a base layer for more expensive coatings, further enhancing its value in both functional and decorative applications.
● Zinc Plating is also highly cost-effective for corrosion protection, especially on steel parts, but it lacks the aesthetic appeal and durability of nickel. It’s often used for fasteners, bolts, and automotive parts.
● Copper Plating is another affordable option, particularly for enhancing electrical conductivity or as a base layer for other plating processes.
What is the typical cost range for electroplating?
The cost of electroplating services can vary widely depending on several factors. Here are some key determinants that influence the pricing:
Factors Influencing Electroplating Costs:
Material Used for Plating: Different metals have different costs. Precious metals like gold and platinum are more expensive than more common metals like nickel or copper.
Surface Area and Part Size: Larger parts or those with more surface area generally cost more to plate due to the increased amount of plating material needed.
Complexity of the Part: Parts with complex shapes or intricate details may require additional preparation or special handling, which can increase the cost.
Thickness of the Plating: Thicker plating layers require more time and more material, which increases the cost.
Type of Electroplating Method: Different methods (e.g., barrel plating vs. rack plating) have different costs associated with them. Rack plating, which is often used for delicate or large parts, tends to be more expensive than barrel plating.
Quantity of Parts: Economies of scale can apply; larger orders might reduce the cost per unit.
Preparation Processes: Additional processes such as cleaning, masking, or post-plating finishing can add to the overall cost.