65Mn is a type of steel material that excels in a lot of applications, understand the properties of 65Mn carbon steel and its differences when compared to other steels, such as 72A, 1095, and D2.
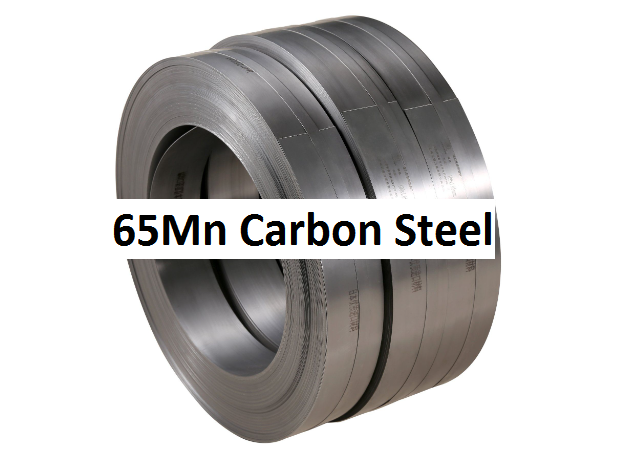
What Is 65Mn Carbon (Spring) Steel?
65Mn steel is a high-carbon-manganese steel known for its impressive combination of hardness and toughness. Conforming to the GB/T 1222 standard, the 65Mn spring steel variant contains approximately 0.65% carbon and is widely recognized for its excellent wear resistance and good toughness, particularly after heat treatment. Commonly utilized in the manufacturing of springs, cutting tools, and wear-resistant components, 65Mn steel also finds significant application in the knife industry due to its balance of strength and resilience.
65Mn carbon steel is available in various forms, including solid bars, which are prevalent for manufacturing springs and components requiring high strength and hardness; sheets, useful for applications needing flat pieces of steel; round bars, available in different diameters for machining and fabrication; hex bars, often used for specific shapes in fittings and connections; square bars, utilized in various structural applications; and flat bars, which are versatile for numerous construction and manufacturing purposes.
65Mn Equivalent Grades
What is 65Mn carbon steel equivalent to? The common 65mn equivalent grades include ASTM/AISI/SAE 1065 and JIS SUP6.
65Mn Steel Chemical Composition
- Carbon (C): 0.62 to 0.70%
- Chromium (Cr): 0.25%
- Manganese (Mn): 1.10 to 1.20%
- Silicon (Si): 0.15 to 0.40%
- Nickel (Ni): 0.35%
- Copper (Cu): 0.25%
- Sulfur (S): ≤ 0.03%
- Phosphorus (P): ≤ 0.03%
Properties of 65Mn Steel
- Density: 7.85 g/cm3
- Tensile Strength: 930 to 1200 MPa (air cooled), 785 to 1030 MPa (quenched and tempered)
- Yield Strength: 785 to 835 MPa (air cooled), 570 to 785 MPa (quenched and tempered)
- Hardness: Achieves an average hardness of around 58 HRc after heat treatment, with maximum hardness reaching up to 64 HRc.
- Edge Retention: Provides adequate edge retention suitable for both home and restaurant use, outperforming many German knife steels at a similar price point.
- Toughness: Exhibits excellent toughness, allowing it to absorb shock without chipping, making it ideal for kitchen tasks and robust applications.
- Wear Resistance: Offers fair wear resistance, capable of withstanding scratches and wear over time, though it may require polishing.
- Sharpening Ease: Easily sharpened with standard whetstones, requiring minimal effort to achieve a refined edge.
- Rust Resistance: Lacks sufficient corrosion resistance due to low chromium content, necessitating proper maintenance to prevent rust.
Applications of 65Mn Steel
- Automotive Springs: Ideal for automotive suspension and clutch springs due to its excellent spring properties.
- Agricultural Machinery: Preferred for plow blades, harrow teeth, and rake tines thanks to its wear resistance.
- Cutting Tools: Widely used in manufacturing saw blades and knives in the industrial sector.
- Construction Materials: Employed in high-stress components within the construction industry.
- High-Quality Blades: Utilized in crafting durable knives and swords, leveraging its exceptional hardness.
- Industrial Applications: Commonly found in heavy-duty springs and wires for various industrial uses.
65Mn Steel vs 72A Steel – Differences Between 65Mn and 72A Steel
Difference | 72A Steel | 65Mn Steel |
---|---|---|
Chemical Composition | C: 0.69%-0.76%, Si: 0.15%-0.35%, Mn: 0.30%-0.60% | C: 0.62%-0.70%, Si: 0.17%-0.37%, Mn: 0.90%-1.20% |
Hardness | Generally high, varies with treatment | 3860 HRC after treatment |
Strength | Higher strength, specifics not detailed | Tensile: 980 MPa, Yield: 785 MPa |
Toughness | Lower toughness, for small-section springs | Good toughness, suitable for impact applications |
Applications | Springs, elastic components in machinery | Small springs, tools, and fixtures |
Price | Generally higher due to quality | Lower, economical for general use |
Production Process | Strict control in smelting, rolling, treatment | Simpler process, suitable for mass production |
Heat Treatment | Quenching and tempering for strength | Quenching at 830±20°C, tempering at 540±50°C |
65Mn Steel vs 1095 Steel – Differences Between 65Mn and 1095 Steel
Difference | 65Mn Steel | 1095 Steel |
---|---|---|
Chemical Composition | C: 0.62-0.7%, Mn: 0.9-1.2%, Si: 0.17-0.37% | C: 0.95%, Mn: 0.4% |
Hardness | High hardness for heavy-duty use | Max HRc66, typically tempered to 56-58 HRc |
Strength | High strength, good resilience | Superior edge retention due to higher carbon |
Toughness | Tougher due to higher manganese | Can be brittle if not properly treated |
Application Areas | Springs, blades, heavy-use tools | Knife blades, cutting tools |
Price | More affordable, widely available | More expensive due to specific applications |
Production Process | Suitable for forging, hot-working characteristics | Conventional steelmaking processes |
Heat Treatment | Quenching and tempering for optimal properties | Quenching followed by tempering to reduce brittleness |
65Mn Steel vs D2 Steel – Differences Between 65Mn and D2 Steel
Difference | 65Mn Steel | D2 Steel |
---|---|---|
Chemical Composition | 0.60-0.70% C, 0.60-0.90% Mn | 1.50-1.60% C, 11-13% Cr, 0.70-0.80% Mo, 0.80-1.00% V |
Hardness | 50-60 HRC | 58-64 HRC |
Strength | Good strength but lower than D2 | Higher strength due to alloy content |
Toughness | Good toughness, impact-resistant | More brittle, can chip under extreme conditions |
Application Areas | Springs, blades | Cutting tools, dies, food processing knives |
Price | Generally less expensive | More expensive due to alloying elements |
Production Process | Standard steelmaking, quenching, and tempering | Complex processes, precise heat treatment |
Heat Treatment | Austenitize at 800-850°C, oil or water quench | Austenitize at 1850-1950°F, air cool or oil quench |