The 7018 welding rod is a staple in shielded metal arc welding (SMAW), known for its versatility and robust weld characteristics. Here we will explain the meaning behind the numbers, the composition, and the mechanical properties that make the 7018 a preferred choice for various applications. We also break down its benefits, and suitable amperage settings, and compare it to other electrodes like the 7014, providing a complete overview of this essential welding tool.
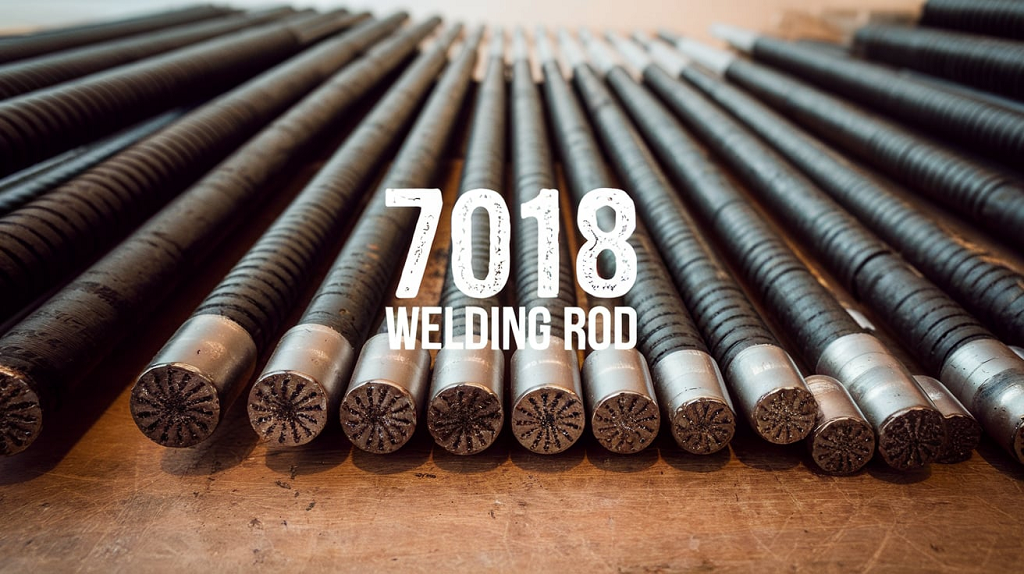
7018 Welding Rod Meaning
The 7018 welding rod is an electrode used in shielded metal arc welding (SMAW). But what does the 7018 on a welding rod mean?
70: The first two digits ’70’ indicate the tensile strength of the weld that the rod can produce. This is measured in thousands of pounds per square inch (psi). Therefore, a ’70’ means the weld can withstand 70,000 psi.
1: The third digit in the sequence, ‘1’, denotes the positions in which the rod can be used to weld. A ‘1’ signifies that the rod is versatile and can be used in all positions including flat, horizontal, vertical, and overhead.
8: The last digit ‘8’ describes the type of coating on the electrode and, by extension, the current type it is compatible with and the flux composition. The ‘8’ in 7018 indicates that the rod is coated with low-hydrogen potassium and iron powder flux.
Chemical Composition of 7018 Welding Rod
7018 welding rods are characterized by their low hydrogen potassium iron powder coating. The core wire generally consists of:
Carbon: Low percentage, usually less than 0.15% to ensure weldability and prevent brittleness.
Manganese and Silicon: These elements help to deoxidize the weld and manage its fluidity.
Iron Powder: Improve deposition rate and efficiency by adding to the coating.
Other Elements: Improve particular qualities like toughness or corrosion resistance, may incorporate minute amounts of nickel, chromium, or molybdenum.
Mechanical Properties of 7018 Welding Rod
Tensile Strength – ~70,000 psi, indicating the maximum stress the weld metal can withstand while being stretched or pulled before failing.
Yield Strength – ~58,000 psi is the stress at which a material begins to deform permanently.
Elongation – ~22%, reflecting the ductility of the weld metal, or its ability to stretch before breaking.
Impact Toughness – High impact resistance at low temperatures qualifies it for conditions with cold weather.
Polarity – Usually used with DC+ (Direct Current Electrode Positive) polarity, the 7018 welding rod offers
consistent arc and deeper penetration. For variety, particularly in cases when only AC power is accessible, it can also be utilized with AC (Alternating Current).
Temperature – The operating temperature range of 7018 welding rod is 0-45℃. In addition, the operating temperature of 7018 welding rod can reach below 510℃ during welding, which is suitable for welding low alloy steel, such as 15Mo and other materials. The storage temperature of 7018 welding rod is required to be between 15~30℃, and the humidity should be ≤50%RH. These storage conditions help ensure the quality and performance of the welding rod.
Benefits of 7018 Welding Rod
High Tensile Strength: High Tensile Strength 7018 Welding Rod guarantees that welds can resist loads up to 70,000 psi.
Low Hydrogen Content: Particularly in high-stress and safety-critical uses, minimizes the possibility of hydrogen-induced cracking.
All-Position Versatility: Highly flexible for many welding situations since all-position versatility allows one to use flat, horizontal, vertical, or overhead welding positions.
Smooth and Clean Welds: Beneficial for both structural integrity and aesthetic needs, smooth and clean welds create superior finish.
Crack Resistance: Particularly useful for welding materials prone to cracking or where the weld connection is under great strain is resistance against cracking.
7018 Welding Rod Types
Because of its adaptability and robust weld qualities, the 7018 welding rod is a common choice for many different welding projects. It comes in a variety, each appropriate for particular needs and conditions. The following are several varieties of 7018 welding rods:
7018 Welding Rod AC
7018 AC is intended especially for use with AC (Alternating Current) welding machines. Perfect for welders needing the qualities of a 7018 rod but without access to DC capability.
7018 Welding Rod DC
7802 DC is tuned especially for DC+ (Direct Current Electrode Positive) for use with DC (Direct Current) welding machines. Designed for applications needing less splatter and deeper penetration, they provide more consistent arcs.
7018 Welding Rod H4R
“H4R” means the rod has moisture-resistant properties and a hydrogen concentration judged at 4 milliliters per 100 grams of weldment. Ideal for settings where rods might come into contact with moisture, therefore lowering the chance of hydrogen-induced cracking.
7018-1 Welding Rod
Slightly deviating from the normal 7018, it offers improved lower-temperature toughness. This type is perfect for colder regions or chilled spaces where materials are more likely to become brittle and break.
7018 Low Alloy Welding Rod Versions
To improve particular characteristics such as toughness, high-temperature strength, or corrosion resistance, these variations of the 7018 rod are alloyed with other elements, including nickel, chromium, or molybdenum. Applied in high-temperature settings, pressure vessels, petrochemical, and maritime sectors where corrosion resistance is needed.
7018 Exotic Welding Rod Variants
These include rods that might be modified for very specific industrial applications, possibly with very low or high alloy contents or specialized flux compositions. Specific to industries or processes that have unique requirements not met by standard welding rods.
What Amperage for 7018 Welding Rod?
The diameter of the rod and the particular welding operation, that is, the kind of joint, location of the weld, determine the suitable amperage for welding with a 7018 electrode. Commonly employed for its strong welds and neat, clean look, the 7018 welding rod is particularly preferred for its low-hydrogen properties, which help prevent weld cracking.
Here’s a general guideline chart for the amperage range based on the sizes of a 7018 welding rod:
7018 Welding Rod Amperage & Size Chart
7018 Welding Rod Size | Diameter (mm) | Amperage Range | Typical Applications |
1/16 7018 Welding Rod | 1.6 mm | 20-40 amps | Thin sheet metal, intricate or small jobs |
5/64 7018 Welding Rod | 2.0 mm | 30-50 amps | Slightly thicker sheets, small parts welding |
3/32 7018 Welding Rod | 2.4 mm | 40-125 amps | General fabrication, repair work |
1/8 7018 Welding Rod | 3.2 mm | 75-185 amps | Structural steel, heavy repair, construction |
5/32 7018 Welding Rod | 4.0 mm | 110-220 amps | Thicker materials, heavy equipment repair |
3/16 7018 Welding Rod | 4.8 mm | 140-305 amps | Shipbuilding, heavy-duty manufacturing |
1/4 7018 Welding Rod | 6.4 mm | 210-430 amps | Extremely thick materials, maximum penetration |
Tips for Selecting the Right Amperage & Size:
Material Thickness – The thicker the material, the larger the diameter typically required to achieve adequate penetration, and the higher the amperage needed. This ensures deep penetration to create a strong weld.
Welding Position – Smaller diameters are easier to handle when welding in vertical or overhead positions. Overhead and vertical welding typically require lower amperages compared to flat and horizontal positions to control the weld pool.
Joint Type – Different joint types may require adjustments in amperage to accommodate variations in metal thickness or joint geometry.
Power Source – Ensure that your welding machine can handle the current requirements of the rod size you choose.
Skill Level – Larger diameter rods require good technique and are generally recommended for more experienced welders due to the higher heat and deeper penetration.
7018 Welding Rod Uses
When To Use 7018 Welding Rod?
The timing of choosing to use 7018 welding rods for welding mainly depends on the object and specific requirements. The following situations are suitable for using E7018 welding rods:
Welding of low carbon steel or low alloy steel – E7018 performs particularly well when welding low carbon steel or low alloy steel, such as bridges, buildings, shipbuilding, and pressure vessel manufacturing.
Welding of important structures – Suitable for welding of important structures built with carbon steel or low alloy steel and A, B, D, and E grade steel for ships, such as boilers, pressure vessels, bridges, pipelines, etc.
All-position welding – AC and DC dual-use, can be used for all-position welding, with excellent low-temperature toughness and crack resistance
Welding of high-strength steel – Suitable for welding of light steel and high-strength steel, in accordance with ASME/AWS A5.1 E7018 standards
Welding of offshore platforms and mining machinery – Especially suitable for important welding applications including offshore platforms, shipbuilding, pressure vessels and mining machinery.
Welding of cracks in cast iron engine body – If the engine body is cast steel, E7018 welding rod can be used to weld the engine body cracks.
Applications requiring high-quality welds: Suitable for application scenarios requiring high-quality welds, such as ship hull manufacturing, pressure vessels, boilers, pipelines, heavy equipment and other fields.
What is 7018 Welding Rod Used For?
7018 welding rods are commonly used for projects requiring robust, clean, and crack-resistant welds, making them good for:
Bridge construction: 7018 welding rods are widely used in bridge construction due to their excellent crack resistance and high-quality weld characteristics. These welding rods can provide strong and high-quality weld joints to ensure the safety and durability of bridge structures.
Construction: In the construction field, 7018 welding rods are used for welding of various building structures, including high-rise buildings, large public facilities, etc. Its excellent low-temperature toughness and crack resistance make it an ideal choice in construction.
Shipbuilding: 7018 welding rods are also widely used in shipbuilding, especially in the welding of hulls and cabins. Due to its good mechanical properties and crack resistance, it can effectively improve the overall quality and safety of ships.
Pressure vessel manufacturing: 7018 welding rods are suitable for important structures built with carbon steel or low-alloy steel and ship A, B, D, E grade steel, such as boilers, pressure vessels, etc. These welding rods can provide high-quality weld joints to meet the requirements of use in high-pressure environments.
Construction machinery maintenance: 7018 welding rods are also commonly used in the maintenance of construction machinery such as bulldozers, agricultural equipment, and mining equipment. Its efficient welding performance and good forming effect make the welding process more convenient and reliable.
Pipeline engineering: In the oil, gas, and chemical industries, 7018 welding rods are used for pipeline welding. Its low hydrogen potassium type coating and moisture absorption resistance ensure the stability and reliability of the welded joints.
Other applications: In addition, 7018 welding rods are also used in the manufacture of chemical, fertilizer, food machinery, and equipment. These applications usually require high-strength and high-toughness welding materials to ensure the long-term operational stability of the equipment.
7018 Welding Rod Price
The price of 7018 welding rod in the European and American markets is usually between 3-10 US dollars, which is affected by the brand, size, and purchase quantity. For example, the E7018. 3/32 in Stick Electrode suitable for smaller currents usually costs 5-10 US dollars per pound. The most popular Lincoln Excalibur 7018 MR ED032589 1/8″ Stick Electrodes in the market costs 30-50 US dollars per 10 pounds.
What is the Difference Between 7014 and 7018 Welding Rods?
The 7014 Electrode is also one of the most used in the welding industry, but it has different characteristics and is suited for different applications than the 7018 Electrode. Here are the top 5 main differences between these two types of electrodes:
1. Coating Composition and Type
7014: This electrode has an iron powder-titanium oxide coating. The iron powder in the flux increases the deposition rate. It is easier to weld with, especially for less experienced welders, and can be used with both AC and DC currents.
7018: This electrode is coated with a low-hydrogen, iron powder flux. It is known for producing tough, crack-resistant welds. It requires special storage conditions to prevent moisture absorption, which can lead to hydrogen-induced cracking.
2. Welding Properties and Performance
7014:
Easy Slag Removal: The slag from a 7014 rod is easy to remove, which is helpful for beginner welders.
Smooth Arc: It has a very smooth arc with a moderate to high deposition rate.
Versatility: Suitable for all positions, though it is particularly good for welding in flat and horizontal positions.
Appearance: Produces a smooth bead with fine ripples.
7018:
Low Hydrogen Content: Crucial for welding high-strength steels where hydrogen embrittlement could be a concern.
Crack Resistance: Provides excellent resistance to cracking, making it ideal for critical structural applications.
Strong and Tough Welds: Suitable for applications requiring high quality, ductile welds.
Storage Requirements: Needs to be kept in a rod oven or a sealed container to prevent moisture absorption.
3. Applications
7014: Often used for sheet metal welding, light structural work, and general fabrication. Because of its easy handling and smooth finish, it’s a favorite for non-critical applications where speed and ease of welding are important.
7018: Widely used in industrial and construction applications where high strength and crack resistance are necessary. Common in the construction of bridges, buildings, and pressure vessels.
4. Positional Welding
7014: Performs well in all positions, but its slag features make it particularly effective for horizontal and flat welds.
7018: Also capable in all positions, but its low-hydrogen characteristics are essential for vertical and overhead welding in addition to flat and horizontal positions.
5. Skill Level
7014: Easier to use for beginners due to its forgiving nature and easy slag removal.
7018: Requires more skill to handle properly, especially in maintaining the electrode’s low moisture content and achieving optimal weld quality.