Steel is the backbone of modern industry and plays a pivotal role in the manufacturing of tools and blades. Among the various types of steel, 80CrV2 and 1095 are two prominent grades known for their distinctive properties and applications. Today, CNCLATHING experts discuss with you the characteristics, applications, and differences between these two steel types, helping you decide which might be better suited for specific uses.
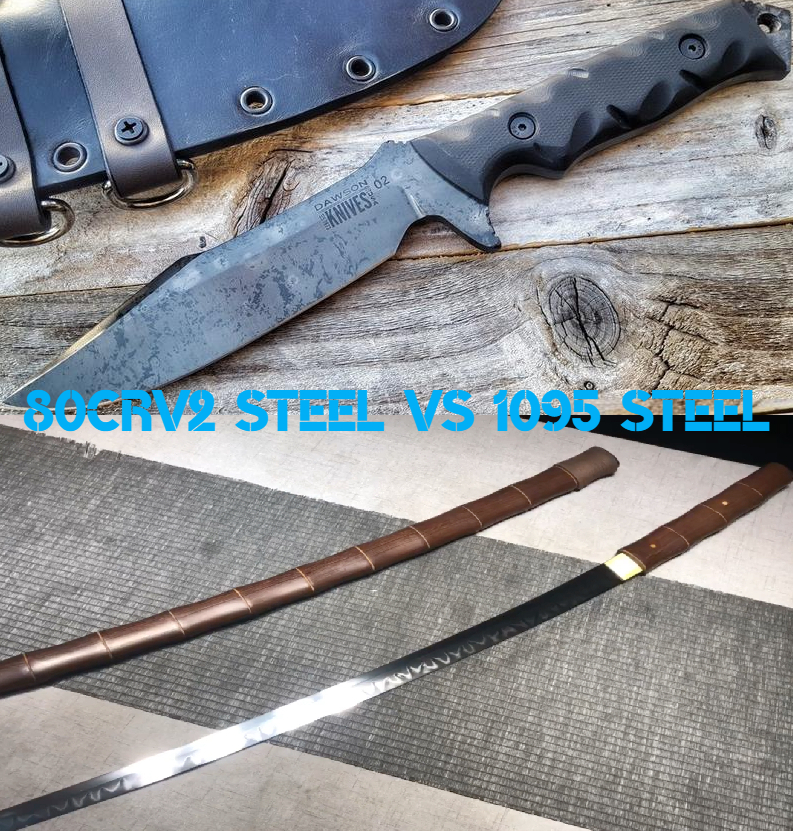
1. What is 1095 Steel?
1095 steel is a high carbon steel that contains approximately 0.95% to 1.03% carbon, making it one of the most carbon-rich steels in the 10XX series. It also includes minor amounts of manganese, phosphorus, and sulfur. This steel is known for its simplicity and high carbon content, which significantly enhances its hardness and edge retention capabilities.
1095 Steel Composition
The primary components of 1095 steel include:
- Carbon (C): 0.90 – 1.03 – The high carbon content gives 1095 steel exceptional hardness and cutting properties, making it ideal for making blades and other tools that require sharp edges. The high carbon content also means the steel can be more brittle without proper heat treatment.
- Manganese (Mn): 0.30 – 0.50 – The presence of manganese increases the hardness and wear resistance of steel, which is critical to improving the overall strength and durability of knives and tools. Manganese also helps improve the hardenability of steel.
- Sulfur (S): ≤ 0.05 – Although sulfur is an impurity, it can improve the cutting performance of steel to a certain extent. However, excessive sulfur content may reduce the steel’s toughness and weldability.
- Phosphorus (P): ≤ 0.04 – Phosphorus is also an impurity. Excessive phosphorus content will reduce the toughness and impact resistance of steel. Nonetheless, moderate amounts of phosphorus can enhance the hardness of steel.
- Iron: Remainder – Iron is the main component of 1095 steel and gives it essential mechanical properties and structure.
1095 Steel Mechanical Properties
- Hardness: When heat treated, 1095 can achieve a Rockwell hardness of 56-60 Rc. The carbon content allows it to harden well with quenching.
- Yield Strength: The yield strength ranges from 241-483 MPa when annealed. It can reach over 800 MPa when properly heat treated and hardened.
- Tensile Strength: The tensile strength is approximately 550-650 MPa when annealed. Heat treating increases it to 900-1000 MPa.
- Ductility: 1095 steel has good ductility. The elongation is around 20-30% when annealed and 12-15% when heat treated.
- Fatigue Strength: Fatigue strength is around 275-413 MPa for annealed 1095 steel at 10^7 cycles. Hardened has higher fatigue strength.
- Impact Toughness: Charpy impact values are around 27-37 Joules for annealed 1095 and 15-25 J when quenched and hardened.
- Wear Resistance: Very good wear resistance when heat treated due to high hardness. Used for knives, axes, swords and other tools.
1095 Steel Advantages & Disadvantages
- Pros: Excellent sharpness and edge retention, affordable, widely available.
- Cons: High maintenance due to rusting.
1095 Steel Applications
1095 steel is frequently used in making large chopping knives, traditional European hunting knives, and military knives like the famous KA-BAR knife used during World War II. Here are some common applications of 1095 steel in the current industry:
- Cutlery – 1095 is very commonly used for high quality knife blades, axes, hatchets, etc. due to its strength, hardness, and edge retention.
- Tools – Tools like chisels, punches, punches, cold cuts, etc. benefit from 1095’s wear resistance and hardness when heat treated.
- Hardware – Applications like bolts, screws, nuts, and other fasteners utilize 1095 for its mechanical properties and availability.
- Agricultural equipment – Parts for equipment like plow blades, shovels, tillage tools are often made from 1095 since it stands up well to abrasive soils.
- Mechanical components – Gears, pins, springs, and other small mechanical parts are produced from 1095.
- firearms – Barrels, bolts, firing pins, and other parts of guns can be made from 1095 steel for its strength.
- Ropes and cables – High tensile strength wire ropes use 1095 core wires due to affordability and mechanical traits.
- Blades – Hunting/utility knives, machetes, swords, axes, and other edged blades/tools favor 1095 for edge retention.
- Outdoor/tactical gear – Knives, multi-tools, axes, and gear benefit from 1095’s rust resistance and durability.
Is 1095 Steel Suitable for Making Knives?
Absolutely. The toughness and hardness make 1095 an ideal choice for combat knives and outdoor tools. It has been used in famous applications like the KA-BAR military knife.
2. What is 80CrV2 Steel?
80CrV2 steel is often considered a reinforced version of 5160 steel, incorporating elements like chromium and vanadium into its composition, which enhances its overall performance. It is a high-carbon steel recognized for its toughness and abrasion resistance.
80CrV2 Steel Composition
This steel includes a mix of:
- Carbon (C): 0.75 – 0.85 – The high carbon content gives 80CrV2 excellent hardness and wear resistance, which makes it ideal for making tools and blades. Its hardness enables it to cut and process a variety of materials.
- Silicon (Si): 0.15 – 0.35 – Silicon helps improve the plasticity and workability of steel, which makes 80CrV2 suitable for workpieces that require precision machining, such as bearings and gears.
- Manganese (Mn): 0.3 – 0.5 – The presence of manganese increases the strength and wear resistance of steel, which is important for manufacturing high-strength parts, such as machine parts and tools.
- Chromium (Cr): 0.4 – 0.6 – The addition of chromium improves the corrosion resistance of steel and makes it stable in harsh environments, which is useful in fields such as aerospace and marine engineering.
- Molybdenum (Mo): ≤ 0.1 – Molybdenum provides additional hardness and wear resistance, which makes 80CrV2 particularly suitable for applications that need to withstand high impact and pressure, such as automotive parts.
- Vanadium (V): 0.15 – 0.25 – Vanadium increases the toughness of steel and improves its impact resistance, which is essential for manufacturing high-load tools and machine parts.
- Nickel (Ni): ≤ 0.4
- Phosphorus (P): ≤ 0.025
80CrV2 Steel Mechanical Properties
- Hardness: When properly heat treated, 80CrV2 can achieve a hardness of 55-62 HRC. This level of hardness provides good wear resistance.
- Yield Strength: Typical yield strength ranges from 1200-1600 MPa when heat treated. The exact number varies depending on the heat treatment process.
- Tensile Strength: Tensile strength also varies with heat treatment but is generally in the range of 1500-1800 MPa.
- Ductility: 80CrV2 has good ductility for a hardenable steel. Elongation is usually around 15-20% after heat treatment. This allows for some plastic deformation.
- Fatigue Strength: Fatigue strength at 10^7 cycles is around 600-800 MPa depending on surface condition and other factors.
- Impact Toughness: Charpy V-notch impact testing typically yields values of 15-30 J at room temperature after heat treating.
- Wear Resistance: Very good wear resistance due to high hardness from proper heat treatment. Commonly used for applications like gears and other components subject to sliding wear.
80CrV2 Steel Advantages & Disadvantages
- Pros: Excellent toughness, good forging and grinding properties, suitable for various applications.
- Cons: Requires maintenance to prevent rusting.
80CrV2 Steel Applications
80CrV2 is used extensively in tool manufacturing, mechanical engineering, the automotive industry, and even in aerospace and marine engineering due to its robust properties. Here are some common applications of 80CrV2 steel in current industry:
- Gears – The high hardness and wear resistance of 80CrV2 make it well-suited for gear applications like transmission gears in vehicles, heavy machinery, etc.
- Dies and metal forming tools – Punches, dies, extrusion dies rely on 80CrV2 for its ability to withstand the high pressures and friction of metal forming operations.
- Cutting tools – Knives, shears, wood/metal cutting tools, drill bits benefit from the hardness and edge retention of 80CrV2.
- Wear parts – Components that experience sliding or abrasive wear like conveyor rollers, chutes, hoppers, excavator buckets are made from 80CrV2.
- Bearings – Cage, balls and rings for heavy-duty or high-speed bearings use 80CrV2 to reduce wear.
- Mining equipment – Parts that contact ore/aggregates like shovel teeth, pulverizer hammers, screw conveyors, etc. are made of 80CrV2.
- Press components – Match plates, bolster plates, ram guides in presses need the strength and hardness of 80CrV2 to endure millions of cycles.
- Plastic mold components – Pins, plates and cores in mold die sets demand 80CrV2’s heat treatment properties.
- Railways – Parts like rail fasteners, crossing frogs benefit from 80CrV2’s abrasion resistance.
Is 80CrV2 Steel Suitable for Making Knives?
Yes, its properties make it an excellent choice for durable knives that are expected to endure heavy use, such as tactical and survival knives.
3. 80CrV2 Steel vs 1095 Steel: Which is Better?
80CrV2 steel and 1095 steel are two commonly used high-carbon tool steels, and they have some significant differences in chemical composition, performance characteristics, and application fields:
Composition Comparison
- 80CrV2 Steel: This is an alloy tool steel whose main components include about 0.80% carbon, 1.0-1.5% chromium, and about 0.20-0.50% vanadium. The content of chromium and vanadium in this steel provides better hardness and wear resistance.
- 1095 Steel: This is a high-carbon steel with a carbon content typically around 0.95%, with lower content of other alloy elements. The high carbon content gives 1095 steel very high hardness and strength but may sacrifice some toughness and corrosion resistance.
Mechanical Properties Comparison
- Hardness:80CrV2 steel contains chromium and vanadium. These elements increase the hardness and wear resistance of the steel, making it generally harder than 1095 steel.The high carbon content of 1095 steel provides good hardness but can be brittle without proper heat treatment.
- Hardenability:80CrV2 contains chromium-vanadium alloy elements, has higher hardenability than 1095, and can harden larger cross-sections.1095 mainly relies on high carbon content to obtain high hardness, low hardenability, and is suitable for thinner tools.
- Wear resistance:After quenching and tempering, 80CrV2 forms fine carbides and has higher wear resistance.The wear resistance of 1095 is slightly inferior to 80CrV2.
- Toughness:The toughness of 80CrV2 is usually better than that of 1095, and it is less prone to brittle fracture.1095 has high hardness but low toughness. If it is not properly quenched and tempered, it is more likely to be brittle.
- Processability:The alloy elements contained in 80CrV2 will form hard carbides, resulting in poor grinding performance.1095 has high purity and relatively good cutting performance.
- Price Differences80CrV2 Steel: Due to the presence of multiple alloy elements, production costs are higher, usually more expensive than 1095 steel.1095 Steel: As a simpler high-carbon steel, it has lower production costs, thus it is relatively cheaper.
Application Comparison
- High-End Cutting Tools: 80CrV2 is often used for high-end kitchen knives, outdoor knives, EDC knives, etc. Its excellent overall performance is suitable for making high-quality cutting tools that require a balance of hardness, wear resistance, and toughness.1095 is also used for knife making but more commonly seen in lower-end products. High-end 1095 knives need very good heat treatment and surface treatment to compensate for performance deficiencies.
- Industrial Uses: 80CrV2 is widely used to manufacture various industrial molds, punches, and dies. Its high hardness, wear resistance, and compressive strength are very suitable for making cold work molds.1095 is rarely used in the industrial field due to its low hardenability, making it difficult to ensure consistent performance in large section workpieces.
- Other Applications: 80CrV2 is also used to manufacture high-strength fasteners, precision transmission parts, etc. It is also used in aerospace, racing, and other fields.1095 is mainly limited to the field of cutting tools, with few applications in other areas.
4. Differences Between 80CrV2 Steel and 1095 Steel
Let’s sum up the table comparing 80CrV2 steel and 1095 steel:
Property | 80CrV2 Steel | 1095 Steel |
---|---|---|
Composition | 1.8-2.1% C, 0.8-1.1% Cr, 0.3% V | 0.95% C, 0.2-0.3% Si, 0.4-0.6% Mn |
Hardness (HRC) | 55-62 | 56-60 |
Yield Strength (MPa) | 1200-1600 | 241-483 (annealed), 800+ (heat treated) |
Tensile Strength (MPa) | 1500-1800 | 550-650 (annealed), 900-1000 (heat treated) |
Ductility (% elongation) | 15-20 | 20-30 (annealed), 12-15 (heat treated) |
Fatigue Strength @ 10^7 cycles (MPa) | 600-800 | 275-413 (annealed) |
Impact Toughness (Joules) | 15-30 | 27-37 (annealed), 15-25 (heat treated) |
Wear Resistance | Very Good | Very Good (when heat treated) |
Applications | Gears, dies, wear parts | Cutlery, tools, hardware, agricultural equipment |
5. 80CrV2 Steel vs. 1095 Steel: Which One to Choose?
Choosing between 80CrV2 steel and 1095 steel primarily depends on the specific requirements of the tools or products you plan to manufacture with the material. Here are recommendations based on different applications:
If you need to manufacture the following types of tools or products:
- High sharpness tools: Such as kitchen knives, hunting knives, and handcrafted knives, which require extremely high sharpness and precise cutting ability.
- Fine-edged tools: Especially those that require regular maintenance and where the user is willing to perform routine rust prevention.
- Recommended choice: 1095 steel
If your needs are more inclined towards:
- Outdoor tools: Such as axes, camp knives, or any tools that may be exposed to harsh environments.
- Impact-resistant and wear-resistant tools: Suitable for applications requiring higher durability and toughness, such as industrial blades, saw blades, etc.
- Tools requiring less maintenance: Although 80CrV2 steel is not stainless steel, its corrosion resistance is better than that of 1095 steel, and it has lower maintenance requirements.
- Recommended choice: 80CrV2 steel
Choose 1095 steel: If your main requirement is extreme sharpness and cutting performance, and you do not mind performing additional maintenance to keep the tools in optimal condition.
Choose 80CrV2 steel: If you need a material that is more durable, has good impact resistance, and is relatively easy to maintain, especially in outdoor or harsh conditions.
The final choice should be based on the specific application requirements and the specific circumstances of the individual or project. We hope this information helps you make the appropriate choice!