Take 3D printing manufacturing technology as an example. As a integration of information technology and manufacturing technology, 3D printing can achieve mold-free, fast, full density of high-performance complex structure metal parts. Its mechanical properties are equivalent to that of forgings, and it has become the best new technical approach to deal with technical challenges in the aero-engine and gas turbine fields.
Compared with traditional manufacturing technology, additive manufacturing technology has the following potential advantages:
1. Low manufacturing costs. For traditional manufacturing, the more complex the product shape, the higher the manufacturing cost. 3D printing will not consume more time or cost due to the increase in the complexity of the product shape. For the manufacture of a large number of complex shapes of aeroengine parts for the pursuit of performance, 3D printing undoubtedly has advantages.
2. Suitable for product diversification. The aero engine itself is a “tested out” product, and the development process requires repeated changes to the design. Traditionally, each round of improvement needs to modify the mold and increase the manufacturing cost. 3D printing does not need to modify the mold for the shape of the product.
3. Minimize assembly and weight reduction. Through topology optimization design, 3D printing can print combined parts, reduce product assembly and reduce product weight.
4. Instant delivery. 3D printing can be printed on demand, which greatly reduces the trial production cycle of some long-cycle parts of aeroengines.
5. Traditionally, the manufacture of many parts of aeroengine has high requirements on the skills of operators, and there have even been situations where individual parts can only be manufactured by one person or a few people. 3D printing obtains various instructions from design documents to manufacture the same complex products. The operating skills required by 3D printers are far lower than those of traditional casting.
6. Traditional casting and forging can generally only manufacture products smaller than the equipment. After the 3D printer has been debugged, the printing equipment can move freely to create a product larger than its own equipment.
7. Contrary to traditional processing and subtractive manufacturing, 3D printing manufacturing belongs to additive manufacturing. A large number of traditional metal processing used in aero engines and gas turbines, a large number of raw materials are discarded in the processing process, and the “net shape” of 3D printing greatly reduces metal manufacturing waste amount.
8. For traditional aero engine and gas turbine manufacturing methods, it is very difficult to combine different materials into a single product. 3D printing has the ability to integrate different raw materials.
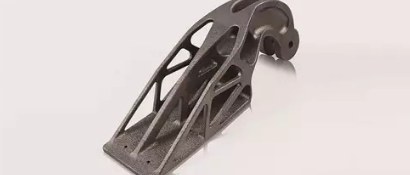