As the industrialization process continues to develop, the application of aluminum materials in various fields is becoming increasingly widespread. Aluminum materials have advantages such as low density, high strength, corrosion resistance, and good thermal conductivity, making them widely used in the manufacturing of aircraft, automobiles, electronic products, and more. Surface treatment of aluminum components is an essential part of these applications. Among them, black anodizing is an important surface treatment method that can provide aluminum components with advantages in corrosion resistance, hardness, wear resistance, and aesthetics.
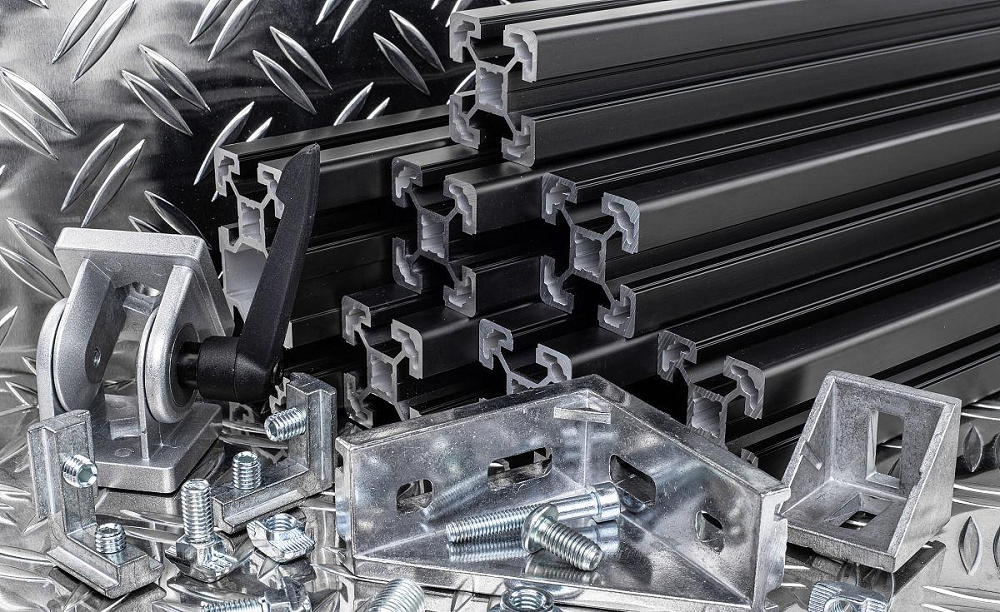
What is Anodizing?
Anodizing is an electrochemical reaction that forms an oxide layer on the surface of aluminum. The basic principle involves using the aluminum component as the anode in an electrolyte solution, passing an electric current through it, and creating an oxide film on its surface. This oxide film has high hardness, corrosion resistance, and good insulation properties. The thickness and color of the oxide film can be controlled by adjusting factors such as the composition of the electrolyte and the electrolysis conditions.
What is Black Anodizing?
Black anodizing is a process that uses an electrochemical process to form an oxide film on the metal surface to improve the performance and appearance of the metal surface. This oxide film is usually a variant of aluminum oxide (Al2O3) and comes in different colors, including black.
What is the Purpose of Black Anodizing?
Its main purpose is to enhance the corrosion resistance, hardness, wear resistance, and aesthetics of aluminum components. In the aviation sector, aluminum components treated with black anodizing can be used for manufacturing aircraft shells, engine components, and other critical parts. In the automotive industry, black anodized aluminum components are used for manufacturing car bodies, engine parts, and more. In the electronic product industry, black anodized aluminum components find applications in the production of mobile phone casings, computer enclosures, and more.
What Metals can Black Anodizing be Used On?
Black anodizing is commonly used on the following metal materials:
- Aluminum: Aluminum is one of the most common metals to be black anodized. This treatment improves the corrosion resistance, hardness and wear resistance of aluminum, while also improving its appearance. As a result, black anodized aluminum is commonly used in automotive parts, aerospace components, electronic equipment, motorcycle parts, and a variety of outdoor products.
- Magnesium: Black anodizing can also be applied to magnesium to increase its corrosion resistance and hardness. Magnesium alloys are commonly used in aerospace, automotive manufacturing and electronic equipment.
- Titanium: Black anodizing of titanium metal improves its surface properties, such as hardness and wear resistance. Therefore, it is also frequently used in medical devices, aerospace and industrial applications.
- Zinc: Although less common than aluminum, magnesium, and titanium, zinc can also be black anodized to improve its surface properties and is used in specialty applications such as military equipment, electronic equipment, and some construction materials.
Generally speaking, black anodizing is usually used in areas where the corrosion resistance, hardness, wear resistance and appearance of metal materials need to be improved. Different metals may require different process parameters and processing conditions during this treatment to meet specific requirements.
What Metal Products use Black Anodizing Finish?
Black anodizing is widely used on a variety of metal products to improve their performance and appearance. Here are some common metal products and areas where black anodizing is used:
- Auto parts: The automotive manufacturing industry often uses black anodizing to improve the corrosion and wear resistance of auto parts. This includes brake system parts, suspension components, exhaust systems, wheels, engine parts and exterior bodywork.
- Motorcycle Parts: Similar to cars, motorcycle parts can also benefit from black anodizing to enhance their performance and appearance. This includes motorcycle frames, exhaust pipes, brakes and suspension components.
- Electronic devices: Many electronic products, especially cell phones, tablets, laptops, cameras, etc., use black anodizing to improve appearance and wear resistance.
- Jewelry: Black anodizing is also used in jewelry manufacturing to create black metal jewelry with style and durability.
- Outdoor equipment: Outdoor equipment such as fishing rods, hunting guns, outdoor knives, and camping equipment are often black anodized to improve their corrosion and wear resistance.
- Military Equipment: Black anodizing is useful for military equipment as it provides corrosion resistance, abrasion resistance, and low visibility for weapons, military vehicles, and other military uses.
- Aerospace: Aircraft parts, spacecraft components and aerospace equipment often use black anodizing to improve their performance, especially under extreme environmental conditions.
- Medical Devices: Medical device manufacturers use black anodizing to improve the corrosion resistance of their products, especially where a high level of hygiene and durability is required.
These are just some examples, black anodizing can be used in many other areas and products to improve the performance and appearance of metal materials. Key factors in choosing to use black anodizing often include product design needs, environmental conditions and cost considerations.
What are the Advantages of Black anodizing?
Black anodizing has some significant advantages in many applications that make it a popular surface treatment. Here are some of the key benefits of black anodizing:
- Improved Corrosion Resistance: Black anodizing significantly improves the corrosion resistance of metal, making it more resistant to oxidation, chemical attack, and other environmental aggressors.
- Increase Hardness: This treatment increases the hardness of the metal, thereby improving its resistance to scratches and wear. This is especially important for mechanical parts and equipment.
- Improved Appearance: Black anodizing gives the metal surface an even, consistent black appearance, thereby improving the aesthetics of the product. This is very important in areas such as consumer electronics, automotive parts and accessories.
- Conductivity Control: Although the oxide film itself is typically an insulator, its conductivity can be controlled by adjusting process parameters, which is useful for applications requiring conductivity.
- Thermal Stability: Black anodizing typically maintains its properties in high-temperature environments, making it useful in engine parts, heat exchangers, and other high-temperature applications.
- Environmentally Friendly: Typically, black anodizing uses environmentally friendly process fluids and materials, which helps reduce environmental impact.
- Low Maintenance Requirements: Once black anodizing is completed, metal surfaces generally require less maintenance because of the extra protection provided by the oxide film.
- Multi-Material Applicability: Black anodizing is suitable for a variety of metals, including aluminum, magnesium, titanium, etc., so it has a wide range of uses in a variety of material applications.
These advantages make black anodizing a powerful tool for improving the performance and appearance of metal materials. It has been widely used in many fields such as automobile manufacturing, electronic manufacturing, aerospace, military, and medical equipment. However, choosing to use black anodizing still requires weighing the pros and cons based on specific project needs and cost considerations.
How Does Black anodizing Work & Process?
The process for black anodizing is similar to regular anodizing but involves differences in the selection of electrolytes and control of electrolysis conditions. Typically, special additives are added to the electrolyte used in black anodizing to control the color and hardness of the oxide film. Control of electrolysis conditions is also a crucial factor in achieving the desired black anodizing effect. Generally, black anodizing requires higher voltage and longer electrolysis times to form a thicker oxide film. However, excessive voltage and prolonged electrolysis can lead to defects such as white spots and pores on the oxide film’s surface.
The following are the steps typically used for black anodizing:
- Preprocessing: Clean metal surfaces: Before you begin processing, make sure the metal surface is clean and free of grease, dirt, or other impurities. This usually involves using an alkaline or acidic cleaner to clean the metal.
- Pickling: Sometimes, after cleaning, the metal may need to go through a pickling process to remove the oxide layer and other unwanted materials from the surface. This can be done using an acidic solution.
- Anodizing: Metal parts are immersed in an electrolyte solution containing an oxidizing agent. The metal piece itself acts as the anode (positive electrode), while an auxiliary electrode acts as the cathode (negative electrode). By applying an electric current, the oxidant initiates an oxidation reaction on the metal surface, forming an oxide film. This membrane is usually a variant of aluminum oxide (Al2O3). The current density and treatment time are controlled to ensure the desired oxide film thickness is obtained.
- Coloring: To achieve black anodization, it is usually necessary to introduce dyes or pigments onto the oxide film. This can be done by dipping, spraying or other methods.
- Sealing treatment: After completing the above steps, the oxide film usually needs to be sealed to improve its stability and durability. Sealing usually involves soaking the metal piece in a sealant so that the pores of the oxide film close, preventing the intrusion of moisture and other substances.
- Cleaning and drying: Treated metal pieces need to be cleaned to remove any remaining treatment agents or impurities. Afterwards, the metal needs to be thoroughly dried to ensure the quality and stability of the oxide film.
The principle of black anodization is based on electrochemistry and redox reactions. By controlling parameters such as current density, treatment time, electrolyte composition, and dye selection, the color and performance of the oxide film can be adjusted. This process is often used to improve the appearance and performance of metal parts, such as increasing their resistance to corrosion and wear.
Black anodizing is an important surface treatment method with advantages in terms of high hardness, wear resistance, corrosion resistance, and aesthetics. Its applications are extensive and cover various fields, including aviation, automotive, and electronic products. With ongoing technological advancements, black anodizing techniques are continuously evolving, and it is believed that in the near future, black anodizing will have even wider applications and more refined processes.