Reaming is a machining process used to refine and perfect holes to precise dimensions, ensuring smooth surface finishes and accurate tolerances. Proper selection of cutting speed and feed rate is essential for achieving optimal performance, preventing tool wear, and maintaining workpiece quality.
Here we provide a detailed reference for reamer speeds and feeds, including recommended revolutions per minute (RPM), feed rates, and allowance charts for different reaming materials and cutting tools. It also covers the key factors that influence these values, such as material properties, tool geometry, and machine characteristics. That will help in selecting the best cutting conditions for different reamer types, including high-speed steel (HSS) and carbide reamers. Additionally, formulas and calculation methods for determining optimal speeds and feeds are included, ensuring a practical approach to achieving better machining results.
Before presenting the Reamer Speeds and Feeds Charts, let’s explain some key concepts so that you can read them more easily.
What are Reamer Speeds and Feeds?
Reamer speed refers to the rotation speed of the reamer during the reaming process, usually expressed in revolutions per minute (RPM). The feed rate indicates the distance the reamer advances with each rotation, typically measured in millimeters per minute (mm/min).
What is Reamer RMP?
Reamer RPM (Revolutions Per Minute) refers to the rotational speed at which a reaming tool (reamer) is operated when enlarging or finishing a hole in a workpiece. Proper RPM selection for reaming is critical to achieving high-quality finishes, maintaining dimensional accuracy, and prolonging tool life.
Why Speeds and Feeds Are Important in Reaming?
Speeds and feeds are important in reaming, the process of enlarging a pre-drilled hole to achieve a precise diameter and a smooth finish. Choosing the right cutting speed and feed rate ensures efficient material removal, longer tool life, and high-quality hole finishes. Running a reamer too fast can lead to excessive wear and tool breakage, while improper speeds and feeds may result in rough, inaccurate holes and dimensional inaccuracies, causing oversized or undersized openings. Additionally, optimizing these parameters improves machining efficiency, leading to better cycle times and lower machining costs.
What Factors Affect Reamer Speeds and Feeds?
Before we choose the right speeds and feeds for our upcoming reaming process, we first have to understand what factors affect it. Although some general parameters may allow you to achieve the cutting effect, the following factors may cause deviations:
- Material Being Cut: Harder materials require slower speeds and lower feed rates to minimize tool wear and ensure effective cutting.
- Reamer Material: The type of reamer material significantly influences performance; carbide reamers can handle higher speeds compared to high-speed steel (HSS) reamers.
- Hole Diameter: Larger reamers typically necessitate lower RPMs to maintain stability and cutting efficiency.
- Coolant and Lubrication: Adequate lubrication is essential for improving tool life and achieving a better surface finish during reaming operations.
- Machine Rigidity: The rigidity of the machine setup affects speed selection; less rigid configurations may require slower speeds to reduce vibration and maintain precision.
- Hole Type: The characteristics of the hole, such as whether it is a blind hole or through-hole, necessitate different considerations for optimal speeds and feeds.
- Cutting Conditions: Recommended cutting conditions for various materials and reamer types can guide the selection of appropriate speeds and feeds.
- Tool Geometry: The design and geometry of the reamer, including flute shape and cutting edge design, can influence cutting performance and dictate speed and feed settings.
- Workpiece Condition: The condition of the workpiece, including surface finish and hardness variations, can impact the choice of speeds and feeds.
- Chip Removal: Effective chip removal is crucial for preventing buildup and ensuring consistent cutting, influencing the selected feed rate.
- Type of Cutting Fluid: The specific cutting fluid used may require adjustments in speeds and feeds for optimal performance.
- Machine Type: The capabilities and limitations of the machine tool can affect the feasible speed and feed settings.
- Cutting Speed Recommendations: Guidelines for cutting speeds, typically provided in charts, assist in determining the appropriate RPM for various materials and reamer sizes.
- Reamer Wear: As the reamer wears over time, adjustments to speeds and feeds may be necessary to maintain cutting performance and quality.
How to Calculate Reamer Speeds and Feeds?
Reamer Speed Rate: The rotation speed for reaming is generally lower to reduce cutting heat and cutting force. For steel parts, the speed generally does not exceed 5 m/min; for cast iron parts, the speed can be increased to 8-10 m/min.
Reamer Feed Rate: The feed rate is usually larger than that used for drilling, typically 2-3 times the drilling feed rate. A feed rate that is too large can increase surface roughness, while one that is too small can cause reamer wear and vibration.
1. Cutting Speed (V) Calculate Formula
Cutting speed is the velocity at which the reamer rotates along its circumference. It is calculated as:
V =πDN / 1000
Where:
V = Cutting speed (m/min)
D = Reamer diameter (mm)
N = Reamer rotation speed (RPM)
2. Feed Rate (Vf) Calculate Formula
Feed rate determines how fast the reamer advances into the workpiece. It is typically higher than that of drilling to ensure cutting rather than rubbing.
Vf = f x N
Where:
Vf = Feed rate (mm/min)
f = Feed per revolution (mm)
N = Reamer rotation speed (RPM)
A general rule is that the feed rate for reaming is 2-3 times higher than for drilling.
3. Feed per Revolution (f) Calculate Formula
Defines how much the reamer advances per spindle revolution:
f = Vf / N
Too low a feed rate leads to rubbing, excessive heat, and premature tool wear.
Too high a feed rate increases cutting forces and can cause poor hole quality.
4. RPM Calculate Formula
To calculate RPM: RPM = (V×1000) /πD
Reamer Speeds and Feeds Chart (Metric)
First of all, we show you the table provides recommended spindle speeds (RPM) and feed rates (mm per revolution) for different reaming cutter types (End Mill, Ball Nose Cutter, and Tapered Cutter) when machining various materials, including cast iron, aluminum, graphite, and wood.
General Reamer Speeds and Feeds Chart for Different Cutters & Machining Materials
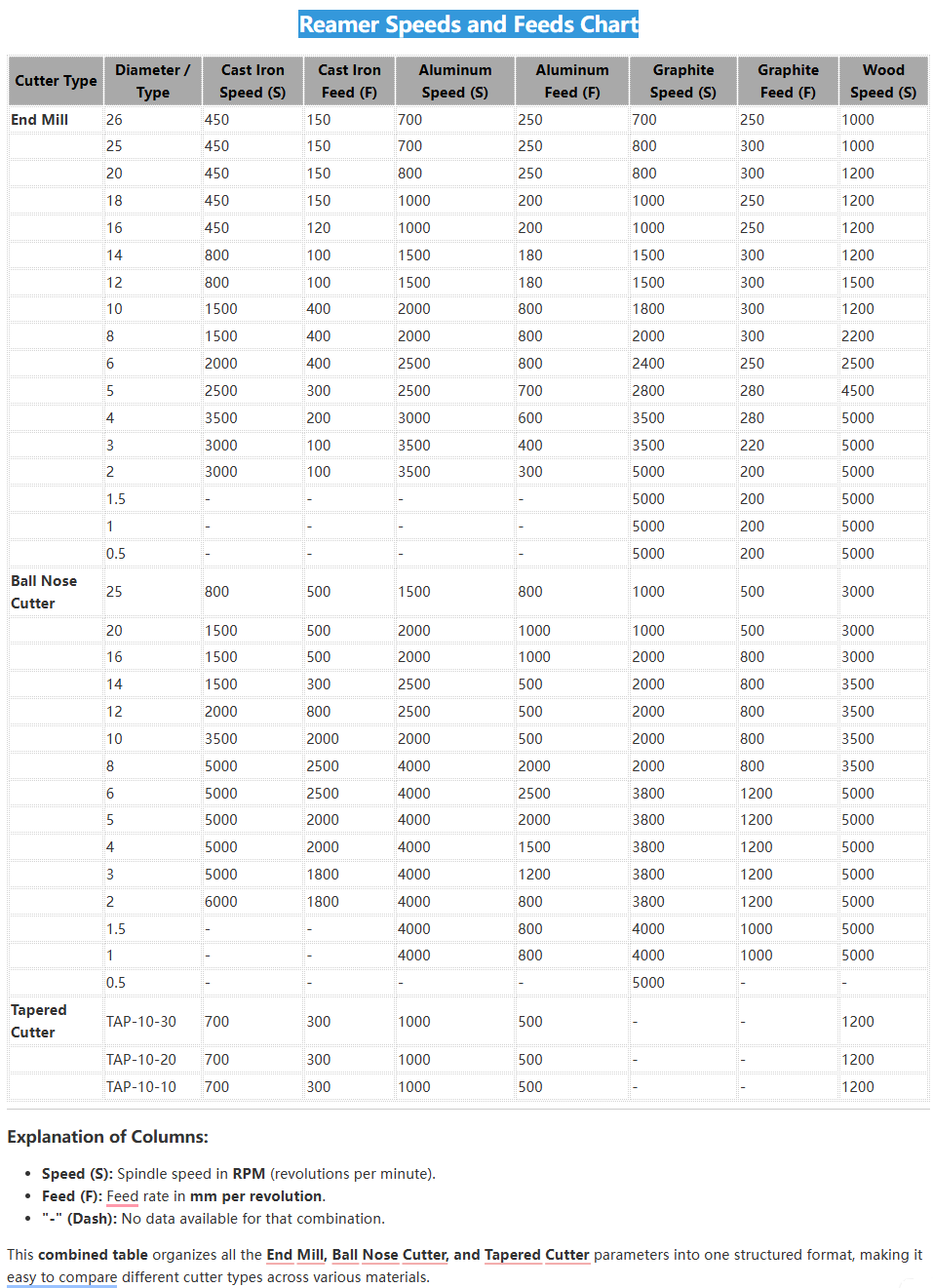
We have detailed the factors influencing reamer speeds and feeds rate above. However, in practice, our choices primarily depend on the material of the reamer itself, the type of drill bit, and the various types of cutting materials. Therefore, we will present several reaming speed and feed rate charts for different types of reamer for your reference.
High-Speed Steel (HHS) Reamer Speeds and Feeds (RPM) Chart
Work Material | Cutting Speed (m/min) | Feed per Revolution (mm/rev) | Cutting Fluid | Surface Finish |
---|---|---|---|---|
Ø4 | Ø6 | Ø10 | ||
Carbon Steel (~700 N/mm²) | 10–12 | 0.08 | 0.12 | 0.20 |
Carbon Steel (700–900 N/mm²) | 6–8 | 0.08 | 0.12 | 0.20 |
Carbon Steel (900 N/mm² and above) | 4–6 | 0.08 | 0.12 | 0.18 |
Alloy Steel (~900 N/mm²) | 4–6 | 0.08 | 0.12 | 0.18 |
Alloy Steel (900–1,060 N/mm²) | 3–5 | 0.08 | 0.12 | 0.18 |
Alloy Steel (1,060 N/mm² and above) | 1–3 | 0.08 | 0.12 | 0.18 |
Heat-Resistant Steel, Stainless Steel | 4–8 | 0.08 | 0.12 | 0.18 |
Cast Steel | 4–8 | 0.08 | 0.12 | 0.18 |
Cast Iron | 10–20 | 0.08 | 0.12 | 0.20 |
Ductile Cast Iron | 6–12 | 0.08 | 0.12 | 0.20 |
Electrical Copper | 12–20 | 0.08 | 0.12 | 0.20 |
Brass | ||||
Soft | 14–20 | 0.12 | 0.16 | 0.25 |
Hard | 8–12 | 0.12 | 0.16 | 0.25 |
Aluminum Die-Cast Material | 14–20 | 0.12 | 0.16 | 0.25 |
Aluminum Alloy | 10–14 | 0.12 | 0.16 | 0.25 |
Silicon Content <10% | 6–10 | 0.12 | 0.16 | 0.25 |
Silicon Content ≥10% | 4–6 | 0.12 | 0.16 | 0.25 |
Magnesium Alloy | 20–30 | 0.20 | 0.30 | 0.50 |
Titanium Alloy | 2–6 | 0.08 | 0.12 | 0.18 |
Thermosetting Resin | 4–8 | 0.15 | 0.20 | 0.30 |
Cutting Speed (m/min): Recommended cutting speed in meters per minute.
Feed per Revolution (mm/rev): Recommended feed rate per revolution for different reamer diameters (Ø4, Ø6, Ø10, Ø20, Ø30).
Cutting Fluid: Type of cutting fluid recommended for the material.
Surface Finish:
12S / 6.3S: Surface roughness values indicating the smoothness of the finished surface.
H7 / H7~H8: Hole tolerance class for precision hole finishing.
Carbide Reamer Speeds & Feeds Chart (RPM) Chart
Speeds & Feeds Rate For Carbide Reamer Model Numbers: SEC-HR / SEC-HSPR / SEC-HP-SPR / TSC-XHR / CHR / CHRL
Blade Diameter (D) (mm) | Soft Steel / Carbon Steel (SS・SC) (10–18 m/min) | Alloy Tool Steel (SKD, SUS, SCM) (8–15 m/min) | Pre-hardened Steel (35–40HRC) (HPM, NAK) (5–15 m/min) | High-Hardness Steel (40–60HRC) (5–10 m/min) | Aluminum Alloy (15–25 m/min) |
---|---|---|---|---|---|
Speed (m/min) | Feed (mm/rev) | Speed (m/min) | Feed (mm/rev) | Speed (m/min) | |
1 mm | 3,190 | 0.05 | 2,550 | 0.05 | 1,590 |
2 mm | 1,590 | 0.10 | 1,270 | 0.10 | 790 |
3 mm | 1,060 | 0.15 | 850 | 0.15 | 530 |
4 mm | 790 | 0.20 | 640 | 0.20 | 400 |
5 mm | 640 | 0.25 | 510 | 0.25 | 320 |
6 mm | 530 | 0.30 | 420 | 0.30 | 270 |
8 mm | 400 | 0.35 | 320 | 0.35 | 200 |
10 mm | 320 | 0.40 | 250 | 0.40 | 160 |
The above cutting conditions apply to SEC-HR (Straight Blade).
SEC-HSPR and SEC-HP-SPR (Helical Blades) can be processed at 30–50% higher than the above conditions.
For high-precision types (CHR-HP, CHRL-HP), neck relief types (CHRZ, CHRLZ), and high-precision neck relief types (CHRZ-HP, CHRLZ-HP), refer to the above conditions and use the same settings.
Always use cutting oil, especially for deep hole machining, ensuring continuous and sufficient supply to the machining area.
The recommended values in the cutting conditions table can be optimized within a range of ±30%.
Use high-rigidity, high-precision machines and chucks.
Speeds & Feeds Rate For Carbide Reamer Model Numbers: SEC-RMSC / SEC-RMSRC / SEC-RMSCC / SEC-ECHR / SEC-HP-RMS□□ / SEC-RMS□□L / SEC-RMS□□Z / SEC-ECSPHR
Blade Diameter (D) (mm) | Soft Steel / Carbon Steel (SS・SC) (10–18 m/min) | Alloy Tool Steel (SKD, SUS, SCM) (8–15 m/min) | Pre-hardened Steel (35–40HRC) (HPM, NAK) (5–15 m/min) | High-Hardness Steel (40–60HRC) (5–10 m/min) | Aluminum Alloy (15–25 m/min) |
---|---|---|---|---|---|
Speed (m/min) | Feed (mm/rev) | Speed (m/min) | Feed (mm/rev) | Speed (m/min) | |
0.3–0.5 mm | 17,000 | 0.02 | 15,900 | 0.02 | 12,700 |
1 mm | 6,400 | 0.05 | 5,900 | 0.05 | 3,800 |
1.5 mm | 4,200 | 0.05 | 3,500 | 0.05 | 2,100 |
2 mm | 3,200 | 0.10 | 2,700 | 0.10 | 1,600 |
3 mm | 2,100 | 0.15 | 1,600 | 0.15 | 1,000 |
5 mm | 1,300 | 0.25 | 1,000 | 0.25 | 600 |
8 mm | 800 | 0.35 | 600 | 0.35 | 400 |
10 mm | 600 | 0.40 | 500 | 0.40 | 300 |
16 mm | 400 | 0.50 | 300 | 0.50 | 200 |
High-precision type (SEC-HP-RMS□□), long type (SEC-RMS□□L), and neck relief type (SEC-RMS□□Z) should be processed under the same conditions as the standard types listed above.
The above conditions apply to SEC-ECHR (Straight Blade).
SEC-ECSPHR (Helical Blade) can be processed at 30–50% higher than the above conditions.
Solid Carbide Short Taper Pin Reamer (S-CSTPR) Speeds & Feeds Chart
Diameter (mm) | Non-Ferrous Metals (Aluminum, etc.) | Carbon Steel (FC, FCD, S50C, etc.) | Alloy Steel (SCM, SKD, SUS304, etc.) | Pre-Hardened Steel (HPM, NAK, etc.) |
---|---|---|---|---|
Cutting Speed (12–18 m/min) | Cutting Speed (8–12 m/min) | Cutting Speed (5–8 m/min) | Cutting Speed (5–8 m/min) | |
Spindle Speed (rpm) | Feed (mm/rev) | Spindle Speed (rpm) | Feed (mm/rev) | |
1 mm | 3,820 ~ 5,730 | 12 | 2,546 ~ 3,820 | 8 |
2 mm | 1,910 ~ 2,864 | 12 | 1,273 ~ 1,910 | 8 |
3 mm | 1,273 ~ 1,910 | 12 | 849 ~ 1,273 | 8 |
4 mm | 955 ~ 1,432 | 12 | 637 ~ 955 | 8 |
5 mm | 764 ~ 1,146 | 12 | 509 ~ 764 | 8 |
6 mm | 637 ~ 955 | 12 | 424 ~ 637 | 8 |
8 mm | 477 ~ 716 | 12 | 318 ~ 477 | 8 |
10 mm | 382 ~ 573 | 12 | 255 ~ 382 | 8 |
12 mm | 318 ~ 477 | 12 | 212 ~ 318 | 8 |
Short Taper Pin Reamer (S-TPR) Speeds & Feeds Chart
Diameter (mm) | Non-Ferrous Metals (Aluminum, etc.) | Carbon Steel (FC, FCD, S50C, etc.) | Alloy Steel (SCM, SKD, SUS304, etc.) | Pre-Hardened Steel (HPM, NAK, etc.) |
---|---|---|---|---|
Cutting Speed (12–18 m/min) | Cutting Speed (8–12 m/min) | Cutting Speed (5–8 m/min) | Cutting Speed (5–8 m/min) | |
Spindle Speed (rpm) | Feed (mm/rev) | Spindle Speed (rpm) | Feed (mm/rev) | |
1 mm | 3,193 ~ 4,789 | 12 | 2,546 ~ 3,820 | 8 |
2 mm | 1,910 ~ 2,864 | 12 | 1,273 ~ 1,910 | 8 |
3 mm | 1,273 ~ 1,910 | 12 | 849 ~ 1,273 | 8 |
4 mm | 955 ~ 1,432 | 12 | 637 ~ 955 | 8 |
5 mm | 764 ~ 1,146 | 12 | 509 ~ 764 | 8 |
6 mm | 637 ~ 955 | 12 | 424 ~ 637 | 8 |
8 mm | 477 ~ 716 | 12 | 318 ~ 477 | 8 |
10 mm | 382 ~ 573 | 12 | 255 ~ 382 | 8 |
12 mm | 318 ~ 477 | 12 | 212 ~ 318 | 8 |
Ultra-Hard Tip Spiral Reamer (C-SP-MR) Speeds & Feeds Chart
Work Material | Cast Iron (FC250) | General Structural Steel (SS400–S45C) | Tool Steel (SKD) | Stainless Steel (SUS) | Aluminum Alloy |
---|---|---|---|---|---|
Outer Diameter (mm) | ≤ Ø3 | ≤ Ø5 | ≤ Ø10 | ≤ Ø16 | ≤ Ø20 |
Feed (mm/rev) | 0.02 | 0.03 | 0.04 | 0.05 | 0.06 |
Cutting Fluid | Not Required | Not Required | Not Required | Not Required | Water-Soluble |
Half-Pin Gate Reamer (HPGR) Speeds & Feeds Chart
Cutting Speed (m/min) | Cast Iron (FC250) (7–10 m/min) | Mild Steel / Structural Steel (SS400–S45C) (5–8 m/min) | Tool Steel / Mold Steel (SCM–SKD) (5–8 m/min) | Stainless Steel (SUS) (5–8 m/min) | Aluminum Alloy (10–15 m/min) |
---|---|---|---|---|---|
Machining Diameter (mm) | Feed (mm/rev) | Feed (mm/rev) | Feed (mm/rev) | Feed (mm/rev) | Feed (mm/rev) |
≤ Ø2 | 0.004 | 0.004 | 0.002 | 0.002 | 0.004 |
≤ Ø3 | 0.004 | 0.004 | 0.002 | 0.002 | 0.004 |
≤ Ø5 | 0.006 | 0.006 | 0.004 | 0.004 | 0.006 |
≤ Ø8 | 0.008 | 0.008 | 0.006 | 0.006 | 0.008 |
≤ Ø12 | 0.010 | 0.010 | 0.008 | 0.008 | 0.010 |
Cutting conditions depend on hole size, with larger diameters requiring lower feed rates.
Rough & Finish Taper Pin Reamer (RF-TPRT) Speeds & Feeds Chart
Work Material | Cast Iron (FC250) | General Structural Steel (SS400–S45C) | Tool Steel (SKD) | Stainless Steel (SUS) | Aluminum Alloy |
---|---|---|---|---|---|
Call Size (mm) | ≤ Ø5 | ≤ Ø10 | ≤ Ø20 | ≤ Ø30 | > Ø30 & ≤ Ø50 |
Feed (mm/rev) | 0.02–0.03 | 0.03–0.04 | 0.05–0.06 | 0.07–0.08 | 0.08–0.10 |
Cutting Speed (m/min) | 5–10 | 5–8 | 4–7 | 3–6 | 2–5 |
Helical Machine Taper Pin Reamer (H-TPRT) Speeds & Feeds Chart
Work Material | Cast Iron (FC250) | General Structural Steel (SS400–S45C) | Tool Steel (SKD) | Stainless Steel (SUS) | Aluminum Alloy |
---|---|---|---|---|---|
Call Size (mm) | ≤ Ø5 | ≤ Ø10 | ≤ Ø20 | ≤ Ø30 | > Ø30 & ≤ Ø50 |
Feed (mm/rev) | 0.02–0.03 | 0.03–0.04 | 0.05–0.06 | 0.07–0.08 | 0.08–0.10 |
Cutting Speed (m/min) | 5–10 | 5–8 | 4–7 | 3–6 | 2–5 |
Notes:
- When determining the finishing hole diameter, it is calculated based on tip diameter (small diameter) and large diameter (maximum work diameter).
- The cutting conditions for Machine Taper Pin Reamer (TPRT, S-TPRT, SP-TPRT, H-TPRT, RF-TPRT, RF-TPR-S) are based on drill processing conditions.
- Reamers, taper reamers, step reamers, and taper drill processing require different cutting conditions.