Carbide rotary burrs that are attached and used with manual rotary tools such as hand grinders and air grinders have various blade shapes, sizes, and cut types. Each type has different applications and preferred machining shapes, allowing a wide range of machining when used properly.
This article introduces the types and characteristics of carbide rotary burr cut shapes, as well as suitable materials for each cut.
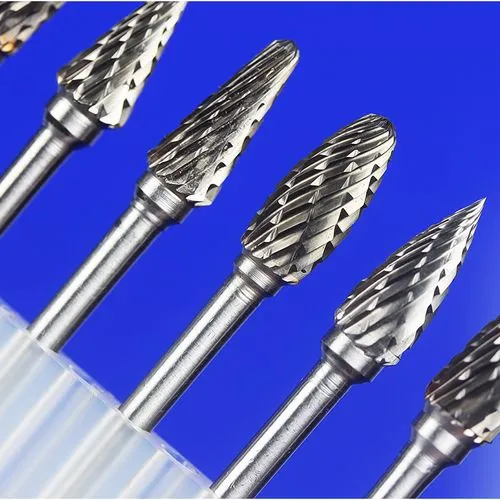
Types of Cuts for Carbide Rotary Burrs
The pattern of irregularities on the blades of carbide rotary burrs is called the cut (blade type). There are three major types that can be distinguished. When selecting a carbide rotary burr, it is important to understand the characteristics of each type.
Double Cut Carbide Rotary Burr (Herringbone)
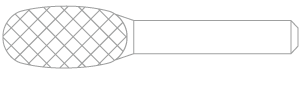
The most common cut shape. Compared to standard, cutting resistance is lower, so chattering (vibration) and tapping where the rotary burr jumps significantly are less likely to occur.
It is also not difficult to control the force applied to the grinder, so it is widely used. The cut chips are powdery, which reduces clogging.
There are types with different cut sizes such as coarse, standard (medium), and fine. Larger cuts with fewer blades remove more material but produce rougher finishes, while finer cuts remove less material but produce better finishes.
Single Cut Carbide Rotary Burr (Standard)
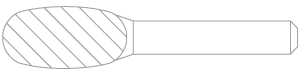
The standard cut has a higher metal removal rate, allowing faster machining. Although cutting resistance is higher compared to double, machined surfaces are good. The shape of discharged chips is needle-like.
As with double, coarse, standard (medium), and fine cut sizes are available in several steps, allowing more efficient operation when using the size suitable for the task.
Wide Single Cut Carbide Rotary Burr (Aluminum)
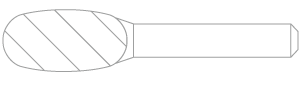
Aluminum cut carbide burrs feature wider chip pockets. This improves chip ejection and prevents clogging.
As the name suggests, they are suitable for machining lightweight metals like aluminum, improving machining efficiency on soft non-ferrous metals.
Cut Carbide Rotary Burr Cut Differences Due to Cut Size
In addition to the shape, carbide rotary burrs have sizes distinguished by cut coarseness. The appropriate coarseness depends on the purpose and workpiece material, so proper selection based on characteristics and suitable uses is important.
Fine Cut (Fine)
The finest cut, useful for smoothly finishing machined surfaces. Metal removal is low so machining takes time, but this is easy to use when incremental material removal is needed.
Workpiece pulling is minimal for easy control, but care must be taken to prevent workpiece and blade burning from cutting heat.
Standard Cut (Medium)
Standard coarseness allows some reduction in machining time while still permitting easy operation control. Its wide applicability makes it useful from rough to fine machining.
Coarse Cut (Coarse)
The coarsest cut gives rougher finishes but good machinability, allowing faster operation. The large chip pockets suit sticky materials like welded steel that produce long chips.
A common technique is to machine most of the workpiece quickly with this cut, then finely finish the surface with a fine cut.
Differences in Suitable Materials for Carbide Rotary Burr Cuts
The suitable workpiece materials differ depending on the carbide rotary burr cut type. Here are the materials each cut type handles well:
Suitable Materials for Double Cut
Double cut carbide burrs are suited to machining high hardness steels like carbon steel, alloy steel, and stainless steel, but not non-ferrous metals like copper and aluminum.
Double Cut Suitable Materials:
- – Carbon steel
- – Alloy steel
- – Heat resistant steel
- – Stainless steel
- – Cast iron
- – Titanium alloy
- – Welded steel
Suitable Materials for Standard Cut
Standard cut carbide burrs can machine a wide range from tough materials like titanium alloys to resins, but are not suited to extremely soft or hard materials like aluminum alloys and welded steel.
Standard Cut Suitable Materials:
- – Carbon steel
- – Alloy steel
- – Heat resistant steel
- – Stainless steel
- – Cast iron
- – Copper
- – Bronze, brass
- – Magnesium alloy
- – Titanium alloy
- – Plastic
Suitable Materials for Aluminum Cut
Aluminum cut carbide burrs are suited to soft, sticky non-ferrous metals like aluminum and copper. Their wide chip pockets also allow machining of plastics that tend to produce large chips, but they are not suited to steel materials like carbon steel and cast iron.
Aluminum Cut Suitable Materials:
- – Copper
- – Bronze, brass
- – Magnesium alloy
- – Aluminum
- – Aluminum alloy
- – Plastic
- – Hard rubber
Using Burrs with Cuts Suited to the Workpiece Material is Important
Using carbide rotary burrs with cuts suited to the workpiece material can improve machining efficiency, extend tool life, and produce good finishes. It is recommended to prepare burrs with different coarseness and blade shapes for roughing through finishing, and switch between them as machining progresses.