When it comes to high-end tool steels used for cutlery, industrial tools, and knives, D2 and 440C steel are two of the most popular choices. Both have unique properties that make them suitable for different applications. Here’s a detailed comparison of D2 steel and 440C steel to help you understand their differences and select the right material for your needs.
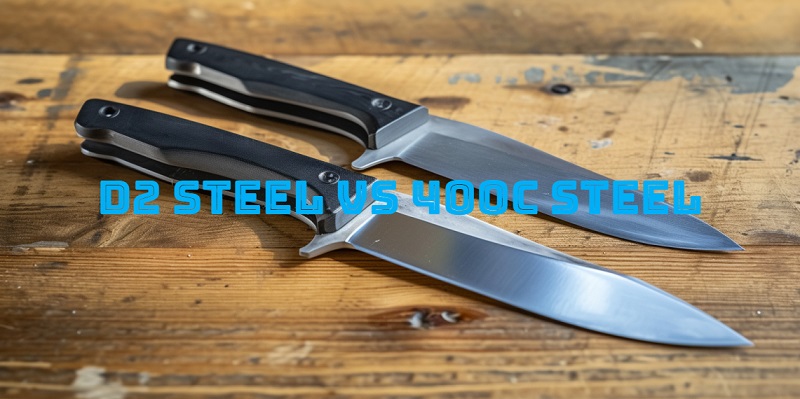
What is D2 Steel?
D2 steel is an air-hardening, high-carbon, high-chromium tool steel. It has high wear and abrasion-resistant properties. It is sometimes referred to as semi-stainless, as it contains a significant amount of chromium, which is not enough to qualify as a true stainless steel. D2 is known for its hardenability and toughness when heat treated, which makes it a popular choice for knife makers. It’s capable of achieving a high degree of sharpness and maintaining it under sustained use.
D2 Steel Composition:
- Carbon: 1.4-1.6%
- Chromium: 11-13%
- Molybdenum: 0.7-1.2%
- Vanadium: 0.5-1.1%
- Iron: Balance
- Other elements: Small amounts of manganese, silicon, and phosphorus.
D2 is known as a semi-stainless or high-carbon, high-chromium tool steel. It is not considered a true stainless steel due to its lower chromium content compared to true stainless steels.
What is 440C Steel?
440C steel is a high-carbon martensitic stainless steel. It is the highest carbon content grade from the 440 series and is known for its strength, moderate corrosion resistance, and ability to be polished to a high gloss. The high carbon content is instrumental in providing high hardness and wear resistance. Unlike D2, it contains enough chromium to warrant the stainless steel classification, which means it has a substantial resistance to rust and corrosion.
440C Steel Composition:
- Carbon: 0.95-1.20%
- Chromium: 16-18%
- Molybdenum: 0.75%
- Manganese: 1%
- Silicon: 1%
- Iron: Balance
- Other elements: Small amounts of phosphorus and sulfur.
440C is a high-carbon stainless steel with a higher chromium content than D2, which gives it its stainless properties.
D2 Steel vs 440C Steel, What is The Difference?
To compare D2 and 440C steel methodically, let’s look at their characteristics side by side in a table.
Property | D2 Steel | 440C Steel |
Carbon Content | High (1.4-1.6%) | High (0.95-1.20%) |
Chromium Content | High (11-13%) | Higher (16-18%) |
Hardenability | Very good | Good |
Hardness | 55-62 HRC | Up to 60 HRC |
Wear Resistance | Excellent | Very Good |
Toughness | Good but less than 440C | Better than D2 |
Corrosion Resistance | Moderate but less than 440C | High |
Sharpening Difficulty | More difficult than 440C | Easier than D2 |
Edge Retention | Excellent | Very Good |
Common Uses | Cutting tools, knives, dies | Knives, surgical equipment, bearings |
Price | Moderate | Slightly higher than D2 |
Availability | Widely available | Widely available |
Now following us to dive into more detailed comparison:
Hardness and Wear Resistance
D2 steel is renowned for its hardness and high wear resistance, traits that are attributed to its high carbon and chromium content, as well as the presence of vanadium and molybdenum. It can achieve a Rockwell hardness of around 55-62 HRC after proper heat treatment.
440C steel also offers excellent hardness and wear resistance, though it typically falls slightly below D2 in terms of wear resistance. It can reach a hardness of up to 60 HRC, making it one of the hardest stainless steels available.
Toughness
Toughness refers to a material’s ability to absorb energy and plastically deform without fracturing. D2, despite its high wear resistance, can be somewhat less tough than 440C, especially at higher hardness levels. The higher chromium content in 440C can lead to improved toughness compared to D2, which can be advantageous in applications where impact resistance is important.
Corrosion Resistance
440C, with its higher chromium content, offers superior corrosion resistance compared to D2 steel. This makes 440C a better choice for applications that require exposure to corrosive environments or require regular washing, such as in food processing or marine-related applications.
D2, on the other hand, with its semi-stainless designation, can resist corrosion to some extent but is more prone to rust than 440C if not properly maintained.
Sharpening and Edge Retention
D2 is well-known for its excellent edge retention due to its high hardness and wear resistance. However, this can also make sharpening more difficult, requiring more time and effort to achieve a fine edge.
440C, while still providing good edge retention, is generally easier to sharpen than D2. It strikes a balance between maintaining a sharp edge and not being overly difficult to sharpen.
Applications
D2 is often used for industrial cutting tools, dies, and high-end knives that require high wear resistance and can handle less corrosive environments. It’s a popular choice for tactical and outdoor knives where edge retention is critical.
440C is chosen for applications that require a combination of high hardness, wear resistance, and corrosion resistance. It’s commonly used for ball bearings, high-quality pocket knives, and in medical instruments.
Price and Availability
The price of the steel can vary depending on market conditions and the form factor (e.g., sheets, rods, custom blanks). Generally, D2 is moderately priced, while 440C can be somewhat more expensive due to its stainless properties.
In terms of availability, both D2 and 440C are widely available in various shapes and sizes from metal suppliers and specialty steel companies.
D2 Steel vs 440C Steel, Which is Better?
The answer to “which is better” between D2 steel and 440C steel is not straightforward and depends greatly on the intended application.
D2 Steel is often the preferred choice for tools that require high wear resistance and those that are subjected to heavy use where edge retention is critical. It is also typically easier on the budget and is an excellent choice for heavy-duty knives and industrial applications.
440C Steel, on the other hand, is often chosen for applications where a high polish is desired, along with a greater degree of corrosion resistance. It’s a popular choice for kitchen cutlery, high-end pocket knives, and medical tools because it is easier to maintain in environments where moisture or corrosive substances are prevalent.
In essence, neither steel is objectively better than the other; it ultimately comes down to what the steel will be used for. For environments where the tool will be exposed to corrosive elements, 440C’s stainless properties may be more beneficial. In contrast, for tasks that demand the utmost in wear resistance and where corrosion is not a significant factor, D2 would likely be the superior choice. It is always critical to consider the specific needs of the application when choosing between these two high-performance steels.
Both D2 and 440C steels have their place in high-end tool and knife making. Choosing between them depends on the specific requirements of the application. If you need exceptional wear resistance and can handle some maintenance to prevent corrosion, D2 could be the ideal choice. Conversely, if you need a balance between wear resistance, hardness, and corrosion resistance, and are willing to pay a little extra for stainless properties, 440C might be the better option.
When selecting a steel, it’s important to consider not just the properties of the steel itself, but also the conditions under which the tool or knife will be used and the maintenance it will receive. Both D2 and 440C have proven their worth in numerous applications, and understanding their differences will help you make an informed choice for your specific needs.