In the realm of manufacturing and construction, where metal and alloys reign supreme, welding emerges as the artistic fusion of science and craftsmanship. It is the process of melding materials together, creating bonds that endure the test of time. Welding finds its applications across a wide spectrum of industries, playing a pivotal role in shaping the modern world. Here we will discuss the fascinating world of welding, exploring its diverse types, their advantages, disadvantages, and the fields in which they excel.
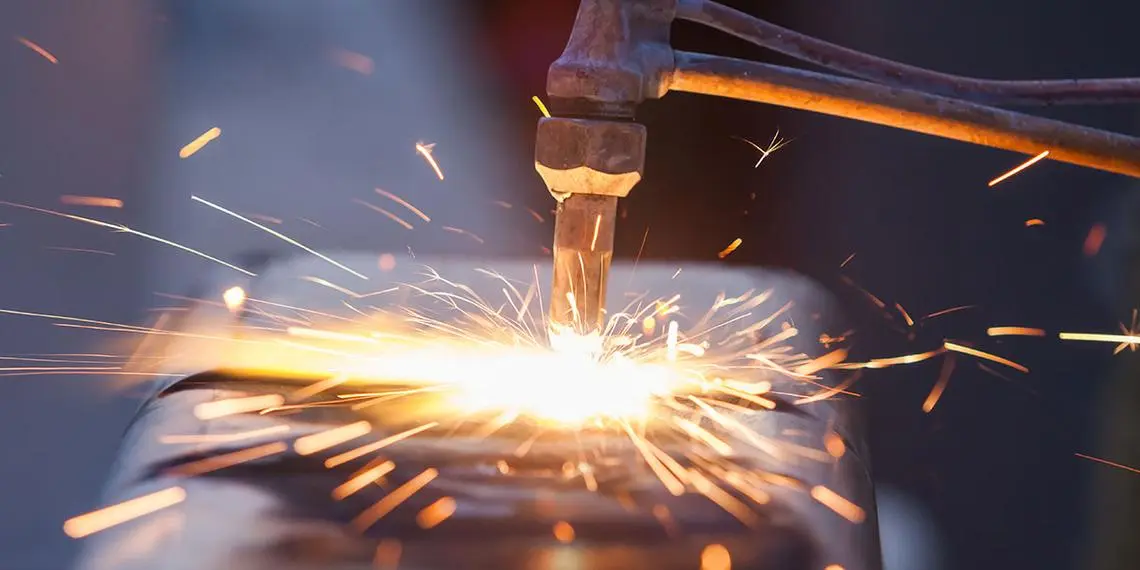
What Welding is Used For: Creating the Fabric of Civilization
Welding, in its essence, is the technique that brings together materials, predominantly metals, to form a solid joint. This artful fusion serves as the backbone of various industries, enabling the creation of everything from towering skyscrapers to intricate machinery. Welding is indispensable in the fields of construction, aerospace, automotive manufacturing, shipbuilding, and even artistic sculptures.
The versatility of welding extends beyond the realms of functional applications, finding its way into artistry as well. Like a master painter wielding a brush, a skilled welder weaves molten metal into intricate designs, producing awe-inspiring sculptures that stand as a testament to human creativity.
Different Welding Types & Applications
Welding, akin to an alchemical process, comes in various forms, each with its own unique properties and applications. Let’s journey through some of the most prominent welding techniques:
1. Arc Welding – The Electric Symphony
Arc welding, resembling an electric symphony, utilizes an electric arc to melt the base materials and a filler rod, creating a joint. Shielded Metal Arc Welding (SMAW) or stick welding, and Gas Metal Arc Welding (GMAW) or MIG welding, fall under this category. SMAW is renowned for its portability, making it ideal for outdoor construction projects. On the other hand, GMAW offers speed and precision, making it the choice for automobile manufacturing.
Advantages:
– Suitable for a wide range of materials.
– Versatile in various working conditions.
Disadvantages:
– High skill requirement.
– Slower compared to other methods.
Application Fields:
– Construction.
– Automotive industry.
2. TIG Welding – The Delicate Dance
Tungsten Inert Gas (TIG) welding, akin to a delicate dance, employs a non-consumable tungsten electrode to create the arc. Often used for high-quality and precision work, TIG welding is exceptional in producing clean, strong joints. Its ability to work with exotic materials like titanium and stainless steel makes it a favorite in industries demanding exceptional corrosion resistance.
Advantages:
– High precision and clean welds.
– Ideal for thin materials.
Disadvantages:
– Slow process.
– Requires a high level of skill
Application Fields:
– Aerospace
– Medical equipment manufacturing
3. MIG Welding – The Swift Fusion
Much like a swift fusion, Gas Metal Arc Welding (GMAW), or MIG welding, employs a continuous solid wire electrode and a shielding gas to protect the weld from contaminants. This method offers rapid and efficient welding, making it suitable for mass production scenarios like automotive assembly lines.
Advantages:
– High welding speed
– Suitable for a variety of metals
Disadvantages:
– Not ideal for outdoor applications
– Limited in overhead welding
Application Fields:
– Automotive manufacturing
– Fabrication shops
4. Laser Welding – The Precision Symphony
Laser welding, resembling a precision symphony, utilizes a concentrated beam of light to create incredibly precise and controlled welds. This technique is employed in micro-welding applications, such as electronics manufacturing, as well as in joining thick sections of materials.
Advantages:
– High precision and control
– Minimal heat-affected zone
Disadvantages:
– Expensive equipment
– Limited to certain materials
Application Fields:
– Electronics manufacturing
– Jewelry production
5. Resistance Welding – The Solid Bond
Resistance welding, akin to a solid bond, relies on passing an electric current through the materials being joined, creating heat and pressure that fuses them together. Spot welding and projection welding are common examples. This method is efficient for joining metal sheets, wires, and tubes.
Advantages:
– High production rate
– Minimal distortion
Disadvantages:
– Limited to certain materials
– Not suitable for thick materials.
Application Fields:
– Automotive industry
– Appliances manufacturing
Welding as Art and Science: Blending Form and Function
Much like an artist sculpting their masterpiece, welders blend the principles of science with artistic finesse to create joints that are not only structurally sound but also visually appealing. The sparks flying and metal melding serve as a metaphorical dance, where the welder’s expertise shapes the outcome.
Advantages and Disadvantages: Weighing the Trade-offs
As with any artistic endeavor, each welding technique comes with its own set of advantages and disadvantages. These intricacies must be carefully considered to select the most suitable method for the task at hand.
The artful fusion of SMAW offers versatility across diverse environments, though it demands a significant level of skill. GMAW, in contrast, bestows swiftness upon welders’ hands, enabling mass production, yet it falls short in outdoor applications. TIG welding, much like a delicate waltz, produces precise and clean welds but requires ample patience. Laser welding, a precision symphony, excels in fine work but demands substantial investment. Resistance welding, embodying solid bonds, achieves high production rates while having its limitations.
Applications Across Industries: Building Dreams and Beyond
Welding, the craft of melding, plays a role as fundamental as the foundation of a skyscraper. Across various industries, its significance cannot be overstated.
In the realm of construction, SMAW and GMAW reign supreme, bringing together steel beams that bear the weight of towering structures. The aerospace industry finds solace in TIG welding, crafting components that soar through the heavens. MIG welding’s swift fusion fuels the assembly lines of the automotive industry, stitching together the vehicles that navigate our roads.
Beyond the realms of utility, welding transcends into artistry. Sculptors channel their creativity through welding, molding metals into enchanting forms. Jewelry makers, wielding the precision of a laser, craft intricate ornaments that adorn and captivate.
The Welder’s Symphony
In the grand orchestra of industry, welding stands as a conductor, bringing together materials to compose the symphony of modern life. From the molten dance of arc welding to the delicate waltz of TIG welding, each technique adds its unique notes to the composition. The choice of welding technique, much like the choice of instrument, depends on the desired tune and the artist’s skill. As we gaze upon the towering structures, intricate machinery, and awe-inspiring sculptures, let us remember that behind these marvels lies the art and science of welding – the craft that weaves dreams into reality, one molten bond at a time.