Dowel pins, despite their simple appearance, represent a crucial component in modern manufacturing and engineering. Understanding the characteristics, types, applications, and standard sizes of dowel pins is useful for professionals and manufacturers.
What Is a Dowel Pin?
A dowel pin is a solid, headless cylindrical fastener typically machined to precise tolerances, used primarily in manufacturing, metalworking, and precision engineering applications. Dowel pins, which can be made from metal, plastic, or wood, serve multiple functions including alignment, location, and joining of components while absorbing lateral stress. They can also function as pivots, shafts, or hinges. Dowel pins are designed with chamfered or beveled ends to facilitate insertion and can come in various styles including straight, tapered, slotted, or grooved variations. Their precision manufacturing ensures repeatable installation results in high-volume production environments, particularly in industries such as automotive, aerospace, tool and die, prototyping, electrical components, and military applications. The pins are inserted into pre-drilled holes without requiring additional mating hardware, effectively preventing lateral movement of adjoined components while maintaining precise alignment between assembled parts.
Types of Dowel Pins
There are three main types of dowel pins covered in the ANSI/ASME B18.8.2 standard.
Hardened Ground Machine Dowel Pins
Feature cylindrical sides with precision grinding, distinguished by a slightly pointed end for easier hole entry and a rounded or crowned opposite end for driving. These pins come in both standard and oversized diameter options, making them ideal for applications requiring precise part location. They excel in scenarios demanding high strength and wear resistance, such as in hardened tool and machine components, or as load-bearing pins and guides.
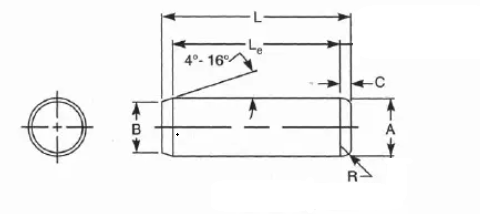
Hardened Ground Production Dowel Pins
Characterized by ground cylindrical sides with rounded ends on both sides, specifically designed to facilitate press-fitting into holes. These pins are particularly well-suited for high-volume manufacturing environments using automated installation equipment, offering the same strength and precision as machine dowel pins but with a design optimized for efficient production processes.
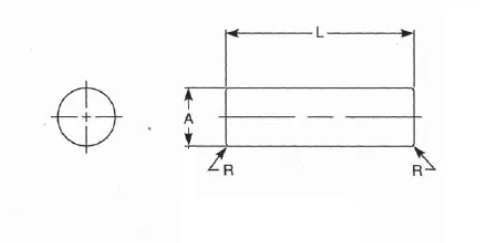
Unhardened Ground Dowel Pins
Maintain ground cylindrical sides but feature chamfered ends on both sides. These pins are the go-to choice for applications with moderate strength and wear requirements, such as pre-alignment of components before final assembly with threaded fasteners, or as guides and pivots in low-wear situations. They provide a cost-effective solution when the enhanced durability of hardened pins isn’t necessary.
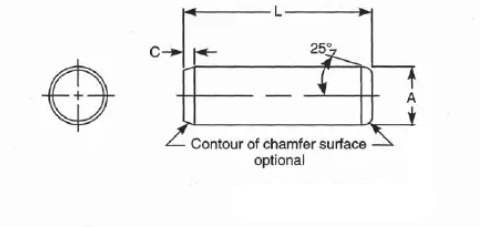
Dowel Pin Sizes Chart (ASME B18.8.2)
1. Hardened Ground Machine Dowel Pins Dimensions
What to note is that the standard series dowel pins have basic diameters of 0.0002 in. Over the nominal diameter, intended for initial installations, and oversize series have 0.001 in. Over the nominal diameter, intended for replacement use.
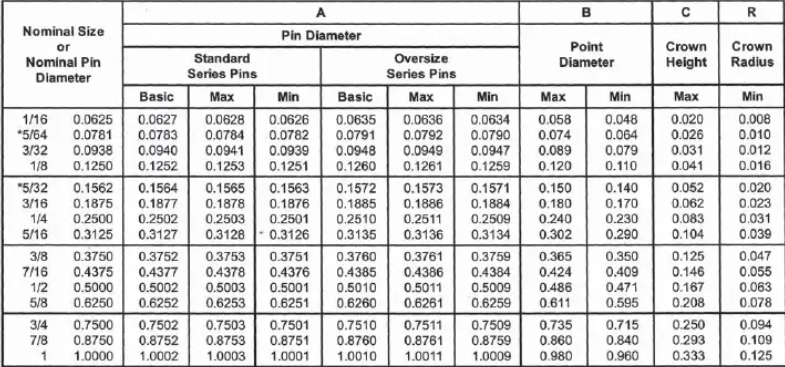
2. Hardened Ground Production Dowel Pins Dimensions
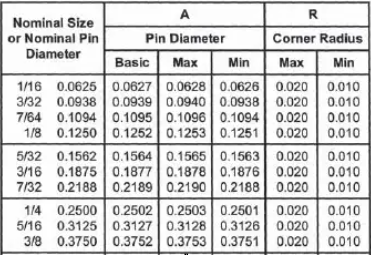
3. Unhardened Ground Dowel Pins Dimensions
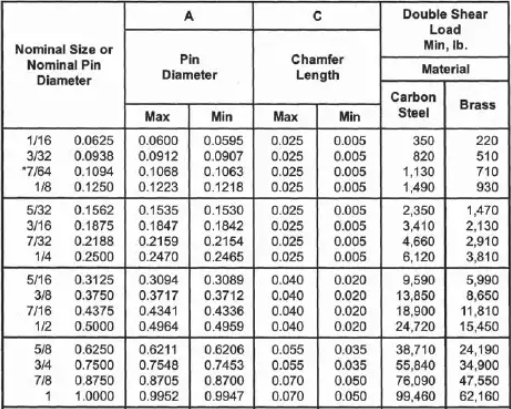
Dowel Pin vs Roll (Spring) Pin – Differences Between Spring Pins and Dowel Pins
1. Design and Structure
- Roll pins, also known as spring pins, are hollow, cylindrical, and headless fasteners made from rolled steel or similar materials. Their unique slotted design allows them to compress when inserted into a hole that is smaller in diameter than the pin itself. This compression creates a snug fit as the pin exerts a retaining force against the walls of the hole. Typically, roll pins have chamfered ends to facilitate easier insertion.
- Dowel pins are solid, cylindrical, and also headless, but they are machined from solid materials to ensure precise dimensions. Unlike roll pins, dowel pins are generally the same diameter as the holes they fit into, providing a tight fit without requiring any compression. Their ends are usually flat and designed for straightforward insertion into aligned holes.
2. Functionality
- The functionality of roll pins revolves around their spring action, which enables them to compress and expand within a hole. This mechanism generates friction against the hole walls, allowing for self-retention. Roll pins are commonly used in applications where components need to be secured in rotating assemblies, such as shafts or other moving parts that may experience vibrations.
- Dowel pins serve primarily to provide fixed alignment and location between components. They do not possess the spring mechanism of roll pins; instead, they create a stable connection that can absorb lateral forces. Dowel pins are especially useful in assemblies where precise positioning is essential, ensuring that parts remain correctly aligned over time.
3. Materials
- Roll pins are typically constructed from high carbon steel, stainless steel, or alloy materials like 6150, which lend them both flexibility and strength. The use of rolled materials not only enhances their durability but also allows for a lightweight design, making them suitable for various mechanical applications.
- Dowel pins come in a variety of materials, including stainless steel, wood, aluminum, and titanium. High-carbon steel and zinc-plated options are particularly popular due to their corrosion resistance. This versatility in materials allows dowel pins to be used in diverse environments, from woodworking projects to industrial machinery.
4. Installation and Removal
- Roll pins require a tool, such as a punch, to insert them due to their need to compress. This installation process can make removal more challenging, as the pins expand tightly to fit the hole, creating a secure but sometimes difficult-to-remove connection.
- Dowel pins can typically be inserted by hand or with a light tap, making the installation process straightforward and convenient. Removal is also relatively easy; a simple pull or gentle tap is usually sufficient to dislodge them, thanks to their non-compressed design.
5. Applications
- Roll pins are particularly well-suited for dynamic applications where components may shift due to movement or vibration. They are often used in motors and machinery to secure parts with symmetrical hole locations or to fasten components on rotating shafts.
- Dowel pins are frequently employed in woodworking and furniture assembly as well as in machine assembly. Their primary role is to ensure parts align correctly and maintain stability, making them an ideal choice for applications that require high precision and load-bearing capabilities.
6. Cost and Availability
- Roll pins are generally economical due to their mass production, though they might be slightly more expensive than dowel pins because of the complexity of their manufacturing process. Their specific design and material requirements can also affect price.
- Dowel pins are often very affordable and widely available in various materials and sizes. This accessibility makes them a popular choice for many projects, whether in manufacturing settings or DIY endeavors, allowing users to easily find the right pin for their needs.