Duralumin refers to high-strength aluminum alloys. There are various types of aluminum alloys, and Duralumin is one of them. Within Duralumin, there are different variations including Super Duralumin, which is an even stronger material. This article provides a detailed explanation of Duralumin.
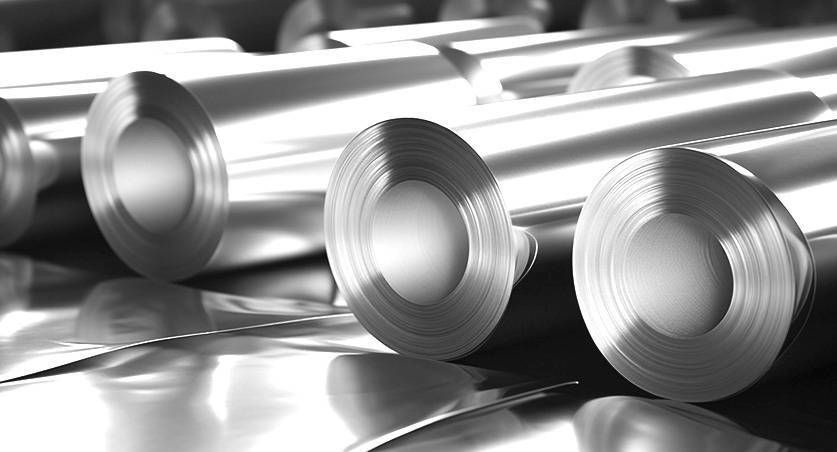
What is Duralumin?
Duralumin might not be a familiar term to many, but it refers to aluminum alloys. There are various types of aluminum alloys, and under the JIS standard, they are categorized by numbers ranging from A2017 Aluminum Alloy (Duralumin) to A7075 (Super Duralumin).
The composition of Duralumin varies depending on its type. The 2000 series, which includes Duralumin and Super Duralumin, mainly consists of aluminum and copper as primary alloys. In the case of the 7000 series, often referred to as Super Super Duralumin, the alloy contains aluminum, zinc, magnesium, and copper.
Duralumin finds its use in everyday items such as sports equipment like skis and metal bats. If we broaden our perspective, it’s also used in aircraft components and aerospace equipment. Doesn’t that make you curious about its applications? In this article, we will continue to delve into Duralumin, so if you’re eager to learn more, please read on.
The History of Duralumin
Duralumin was born in central-west Germany. Around 1903, Dr. Alfred Wilm was experimenting with adding suitable elements to iron to increase its hardness, a concept he had tested with other metals. While these experiments didn’t yield significant results, one day, he found inspiration from cartridge cases.
At that time, cartridge cases were made from a metal called brass. Brass, being an alloy of copper and zinc, led to the idea, “Why not add copper to aluminum?” This led to the creation of aluminum alloys. In September 1906, an aluminum alloy with added elements like copper and magnesium was produced, and its hardness change due to heat treatment was measured. This experiment led to a groundbreaking discovery.
This phenomenon is known as “aging precipitation.” Aging precipitation refers to the fact that the hardness becomes greater after about a day of aging compared to immediately after heat treatment. Duralumin reaches its maximum hardness after approximately 20 hours of aging. While this aging phenomenon was later discovered in other metals such as beryllium copper and chromium copper, it was first identified in Duralumin.
Duralumin Application: Products Utilizing Duralumin
Duralumin, being lightweight and high in strength, plays a vital role in various applications. It is predominantly used in fields where lightweight and high-strength materials are essential, such as aircraft bodies and aerospace equipment. It is said that approximately 70% of an aircraft’s body is manufactured using Duralumin.
Of course, Duralumin can also be found in everyday items around us. While they tend to be more expensive, there are Duralumin smartphone cases available. It’s frequently used in sports equipment like ski boards, poles, and baseball bats. Duralumin-made items can also be found in cooking utensils.
You might have unknowingly used tools made of Duralumin without realizing it. Additionally, Duralumin-made wheels are used in automobiles. The highest-end models of sports wheels, where lightweight and high rigidity are sought after, often use Super Super Duralumin. You’ve probably seen Duralumin cases used in scenes where large sums of money are exchanged in movies and dramas. These cases are commonly used for transporting precision equipment.
As such, there are numerous items in our daily lives that are made from Duralumin without us consciously recognizing it.
Duralumin Composition
Duralumin is a lightweight, high-strength alloy primarily composed of aluminum, which is commonly used in the aerospace and automotive industries. The major components of duralumin alloy are:
- Aluminum (Al): 90-95%, The primary base metal that provides lightweight properties.
- Copper (Cu): 3.5-5%, Increases strength and hardness but reduces corrosion resistance.
- Magnesium (Mg): 0.5-1%, Enhances strength and improves machinability.
- Manganese (Mn): 0.3-1%, Increases resistance to corrosion and adds to the overall strength.
Some variations of duralumin may also contain trace amounts of other elements like silicon (Si) or iron (Fe), but the above elements are the primary ones that give the alloy its characteristic properties.
Duralumin Properties and Strength
Now, let’s delve into the characteristics and strength of Duralumin. Duralumin is an aluminum alloy with added copper. Consequently, there are certain characteristics to be aware of, including aspects related to corrosion resistance and weldability. To make the explanation more intuitive, we’ll compare its strength to other metals.
- Properties of Duralumin
The major characteristic of Duralumin is its ability to achieve strength by adding copper to aluminum. Copper is present in Duralumin, Super Duralumin, and Super Super Duralumin. We will explain the differences between these three later, but the significant common feature is the addition of copper to aluminum. However, due to the inclusion of copper, certain considerations need to be taken into account for specific properties.
- Corrosion Resistance of Duralumin
Compared to pure aluminum, Duralumin has inferior corrosion resistance. This is due to the presence of copper in the aluminum alloy.
Copper is often associated with being resistant to rust, unlike materials like iron. However, while aluminum alloys (in the 2000 series) exhibit high strength, their corrosion resistance falls on the weaker side within aluminum alloys. They are prone to intergranular corrosion.
Intergranular corrosion is a form of localized corrosion that progresses along the grain boundaries of a metal structure. In severe cases, it can lead to grain boundary separation, making it crucial to exercise caution when using Duralumin in corrosive environments. Adequate corrosion protection measures should be implemented.
- Weldability of Duralumin
Welding Duralumin is challenging, and its weldability generally falls short compared to other metals. It has high susceptibility to cracking, making welding construction extremely difficult.
Resistance spot welding machines, which operate at lower temperatures than regular welding, are commonly employed for Duralumin welding. The choice of welding rod also significantly affects the final outcome, so a certain level of experience and expertise is necessary for successful welding. If Duralumin welding is required, it’s advisable to engage companies with substantial experience in this field. Given the challenges in welding, many Duralumin joints utilize rivets or bolts for connection.
- Strength of Duralumin
We’ve explained earlier that Duralumin is an alloy strengthened by the addition of copper. Let’s now compare the actual strength levels of different materials.
There are multiple units used to measure the hardness of metals. While steel often employs HRC (Rockwell hardness), for this explanation, we will use the unit HB (Brinell hardness). Take a look at the differences in hardness based on different materials:
- – A5052 Aluminum: 65HB
- – A2017 Duralumin: 105HB
- – A2014 Super Duralumin: 120HB
- – A7075 Super Super Duralumin: 160HB
- – SS400 Mild Steel: 130HB
- – SUS304 Stainless Steel: 187HB
These are the respective hardness values. By comparing Duralumin with regular aluminum, you can appreciate how much superior Duralumin’s hardness is.
By adding copper to soft aluminum and creating an alloy, Duralumin attains a hardness and tensile strength comparable to SS400 mild steel. On the other hand, in comparison to stainless steel, which has a hardness of 187HB, Duralumin has a hardness of 105HB, making stainless steel harder. (In terms of specific strength, Duralumin is superior.)
CNC Machining Methods for Duralumin
Duralumin can undergo various processing techniques such as CNC machining, cutting, and pressing, similar to conventional steel materials. It’s possible to manufacture complex and high-strength components like Duralumin bolts, gear parts, bearings, hydraulic components, and more.
Moreover, leveraging its lightweight property, you can achieve component weight reduction. Compared to stainless steel, Duralumin’s weight is about one-third, making it highly effective for achieving lightweight designs.
While Duralumin can be processed similarly to conventional steel materials, there are certain points to be cautious about during processing, which I’ll introduce in the following section.
Considerations When CNC Processing Duralumin
The notion that Duralumin, being an “aluminum” material, is highly corrosion-resistant is not entirely accurate. As briefly explained in the characteristics of Duralumin, Duralumin with added Cu (copper) exhibits high strength but comparatively lower corrosion resistance. While aluminum is often associated with rust resistance, the properties of aluminum alloys can vary significantly based on the added elements. Understanding this is crucial for proper processing.
For example, let’s highlight some characteristics of different aluminum alloys. For 1000-series aluminum (pure aluminum), its strength is low and it’s quite gummy, making machining more challenging. In the case of 2000-series aluminum, it’s prone to weld cracking, generally making it unsuitable for welding and requiring skilled technicians. 5000-series aluminum, with the addition of Mg (magnesium), enhances corrosion resistance and strength. It’s widely used as a machining material due to its good machinability.
Given the variation in properties due to additives in aluminum alloys, it’s essential to understand these characteristics when processing. Particularly, for the 2000-series Duralumin discussed in this article, it’s important to note its characteristics of “low corrosion resistance” and “poor weldability” when processing.
Duralumin vs Aluminium: What are the Differences
When comparing Duralumin and Aluminium, it’s essential to understand their differences in terms of composition, properties, and applications. Both metals have distinct advantages, and the choice between them depends on the specific requirements of your project.
Here’s a comparison table between Duralumin and Aluminium that outlines the key differences:
Property | Aluminium | Duralumin |
---|---|---|
Composition | Pure aluminium (Al) | Aluminium alloy with copper (~4%), magnesium (0.5-1%), manganese (0.5-1%), and sometimes silicon |
Strength | Moderate mechanical strength | High mechanical strength, much stronger than aluminium (higher tensile and yield strength) |
Weight | Very lightweight (density: ~2.7 g/cm³) | Slightly heavier than aluminium (density: ~2.8-2.9 g/cm³), but still lightweight |
Corrosion Resistance | Excellent; naturally forms a protective oxide layer | Lower corrosion resistance due to copper content; usually requires protective coating |
Malleability | Highly malleable and ductile | Malleable, but less so than pure aluminium due to added alloying elements |
Thermal & Electrical Conductivity | High thermal and electrical conductivity | Moderate thermal and electrical conductivity |
Heat Treatability | Cannot be heat-treated | Can be heat-treated to further enhance strength |
Cost | Relatively affordable | More expensive due to the alloying elements |
Applications | Packaging, construction, transportation, electronics | Aerospace (aircraft structures), automotive parts, sports equipment |
Use in 4×4 Lower Guards | Lightweight, corrosion-resistant, suitable for wet/muddy conditions | Stronger, more impact-resistant; ideal for high-shock environments but requires corrosion protection |
Strength-to-Weight Ratio | Good, but not as high as Duralumin | Unmatched strength-to-weight ratio, providing high strength without adding significant weight |
Duralumin vs Stainless Steel: Is Duralumin Stronger Than Steel?
Duralumin alloy, is not stronger than stainless steel in terms of tensile or yield strength, with typical tensile strengths around 450–550 MPa compared to stainless steel’s 500–1500 MPa range. However, Duralumin has a much better strength-to-weight ratio, making it ideal for applications where minimizing weight is crucial, such as in aerospace and automotive industries. While Duralumin is lighter and more ductile, stainless steel offers superior corrosion resistance, durability, and overall strength, making it more suitable for environments requiring high durability and resistance to harsh conditions.
Comparing Duralumin’s hardness with that of other metals clearly illustrates the differences. Rather than simply remembering that “Duralumin is a high-strength material,” it’s helpful to remember that within the realm of aluminum alloys, Duralumin is indeed an exceptionally strong material. However, when compared to general metals, it’s either on par or slightly lower in terms of hardness. By keeping this in mind, you can prevent misconceptions.
Differences Between Duralumin and Other Metals
One significant difference between Duralumin and other metals is its superior specific strength. Specific strength refers to the tensile strength per unit density, indicating how strong a metal is relative to its weight. You’re likely familiar with the combination of aluminum’s lightness and strength, which allows it to be both lightweight and sturdy. The sensation of picking up aluminum, its surprising lightness, and its resistance to easy bending are experiences many of us have encountered in our daily lives.
You might have even had experiences where you thought, “This feels so light, it must be made of aluminum,” simply by holding an object. Have you had this experience before?