Electron beam machining (EBM) and electrical discharge machining (EDM) are two popular non-traditional manufacturing processes used to machine metals and other electrically conductive materials. While both involve removing material using an electronic energy source rather than mechanical forces, EBM and EDM differ significantly in their setup, applications, machined surface quality, and overall cost.
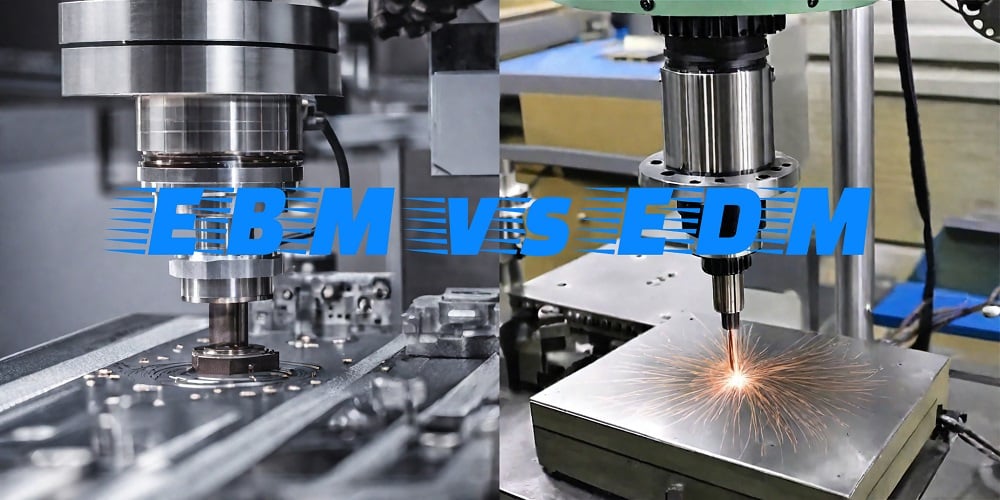
Differences Between EBM (Electron Beam Machining) & EDM (Electrical Discharge Machining)
This post explores the key differences between EBM and EDM to help readers better understand when each process is best suited. We will look at how each operates on a fundamental level, common applications for EBM and EDM, the types of materials that can be machined, the achievable surface roughness, and typical production costs. By comparing and contrasting these two important electronic machining techniques, the goal is to provide a useful overview that can help engineers and manufacturing professionals select the optimal process for their specific part geometry and production needs.
Here is a table comparing electron beam melting (EBM) and electro-discharge machining (EDM) in a visual format:
EBD vs. EDM: Main Differences & Similarities |
||
Aspect |
Electron Beam Melting (EBM) |
Electro-Discharge Machining (EDM) |
Purpose |
Additive manufacturing technique that builds parts layer-by-layer from 3D model data |
subtractive machining process that cuts shapes out of existing workpieces |
Manufacturing Type |
Additive |
Subtractive |
Process |
Uses focused electron beam to fully melt and fuse powdered material according to 3D model |
Erodes material using electric spark between two electrodes submerged in dielectric fluid |
Materials Compatibility |
Metals |
Metals |
Materials |
Can 3D print metal parts from materials like titanium alloys |
Can machine any electrically conductive material such as steel, aluminum, alloys |
Surface Finish |
Produces a rough, as-sintered finish requiring post-processing |
Achieves very smooth, mirror-like finishes on any geometry |
Surface Texture |
Can achieve smooth finishes |
Can achieve smooth finishes |
Precision Capabilities |
High precision tolerances |
Achieves high precision tolerances |
Part Geometry Options |
Complex geometries possible |
Intricate geometries possible |
Tolerances |
±0.005-0.010 inch |
±0.001 inch |
Applications |
Well-suited for complex, low-volume parts like implants |
Excellence at intricate cuts/geometries in high-volume production like dies/molds |
Speed |
Incremental, layer-by-layer approach means slower building |
Much faster material removal compared to additive layering |
Advantages over traditional methods |
Novel geometries, material savings |
Can machine any conductor, uniform wear |
From the above table, we have roughly compared EBM and EDM. In order to give you a more comprehensive understanding of these two processing methods, we will make an in-depth comparison from all aspects below.
EBM vs. EDM: Definition
What is EBM (Electron beam melting)? EBM is an additive manufacturing process that uses a focused electron beam to melt and fuse thin layers of metal powder materials, such as titanium alloys, to build fully dense 3D parts in a layer-by-layer fashion. In the EBM system, a high-energy electron beam is generated from an electron gun and is projected onto a build platform, selectively melting a thin layer of powder according to the programmed pattern from a 3D CAD model. This process is repeated with new layers of powder deposited and melted on top of previous ones to progressively build the final part from the bottom up without supports. The vacuum environment and high control of the electron beam allow for precise fusion of the layers into components with complex geometries and mechanical properties similar to wrought materials.
What is EDM (Electric discharge machining)? EDM is a non-traditional machining process that uses electrical sparks to erode material from a conductive workpiece. In EDM, a rapidly pulsing current is passed between an electrode tool and the workpiece submerged in a dielectric fluid, creating a spark discharge gap. This causes momentary melting and vaporization of small amounts of workpiece material. By precisely controlling the tool using computerized numerical control and repetitively generating electrical sparks at desired locations, EDM can accurately shape the workpiece to duplicate complex internal and external geometries without any mechanical contact between the tool and workpiece. This thermal machining method enables shaping very hard conductive materials like advanced alloys into intricate profiles, micro-scale features, and parts with undercuts and cavities that are challenging using traditional machining techniques.
EBM vs. EDM: Process Differences
EBM: EBM utilizes an electron beam as the heat source to melt a metal powder layer by layer, resulting in the formation of the final part. The electron beam is directed onto the powder bed, causing it to melt and solidify.
EDM: EDM, on the other hand, relies on localized spark erosion to remove material. It uses rapid electrical discharges to generate heat, which melts and vaporizes the material, leaving behind the desired shape.
EBM Process vs. EDM Process | ||
Aspect | Electron Beam Melting (EBM) | Electrical Discharge Machining (EDM) |
Heat Source | Beam of concentrated electrons | High-intensity spark |
Energy Source | Focused electron beam | Focused electric spark |
Electrode Requirement | No electrode required | Shaped or form electrode (tool) required |
Workpiece Polarity | Workpiece is not made an electrode, but it is grounded to maintain electrical neutrality | Workpiece is made positive polarity electrode, while the tool is made the negative polarity electrode |
Dielectric Fluid | Not required, the machining is carried out in a low-pressure (vacuum) chamber | Immersed in suitable dielectric fluid |
Controlled via CAD Data | 3D model data guides process | CAD used for toolpath generation |
Machining Environment | Low-pressure (vacuum) chamber | Open environment |
Clean Processing | No mechanical forces, avoids contamination | No contact forces, avoids contamination |
Material Removal Rate (MRR) | High, but time-consuming due to vacuum chamber requirement | Low, time-consuming |
X-Ray Generation | Mild X-Ray generation takes place | No X-Ray generation |
Surface Finish | Slightly worse surface finish due to its larger beam width, resulting in a rougher appearance between each layer | Better surface finish compared to EBM |
Surface Influence | Surface asperities and waviness do not influence machining performance | Surface asperities and waviness play a crucial role in machining performance |
Recast Layer Formation | No recast layer formation | Recast layer formation is a major drawback |
Aspect Ratio Machining | Can generate high aspect ratio features, suitable for drilling | Usually does not offer high aspect ratio machining, not suitable for drilling |
EBM vs. EDM: Applications
EBM: EBM finds extensive use in the aerospace, medical, military, and research and development industries to produce advanced components. It is particularly well-suited for manufacturing turbine blades and orthopedic implants.
EDM: EDM is commonly employed in various industries, including automotive, aerospace, and medical, for applications such as mold making, die sinking, and creating complex shapes. It is especially useful for producing intricate and precise parts.
EBM vs. EDM: Materials
EBM: EBM can typically work with titanium alloys, cobalt/nickel alloys, and pure copper. It is limited to a smaller group of raw materials compared to other additive manufacturing methods.
EDM: EDM is compatible with a wide range of electrically conductive materials, including metals such as steel, aluminum, copper, and brass. It offers more flexibility in terms of material selection.
EBM vs. EDM: Surface Roughness
EBM: EBM parts tend to have a rougher surface finish compared to EDM. The wider electron beam used in EBM can result in more visible surface roughness.
EDM: EDM can achieve a smoother surface finish due to the localized spark erosion process. It eliminates the need for post-processing in many cases.
EBM vs. EDM: Cost
EBM: EBM machines are generally more complex and expensive compared to EDM machines. Entry-level EBM machines can cost upwards of $250,000, excluding the cost of metal powders.
EDM: EDM machines have a lower initial cost compared to EBM machines. However, they may require more frequent tool replacements, resulting in additional costs over time.
EBM and EDM are distinct additive manufacturing processes with their own advantages and applications. Understanding the differences in process, applications, materials, surface roughness, and cost can help manufacturers make informed decisions when choosing between EBM and EDM for their specific manufacturing needs. If you are looking for precision EDM Machining services, please contact us now!
Related Articles:
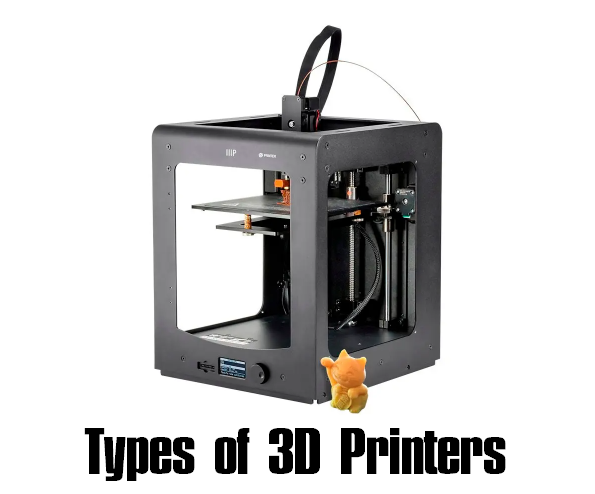
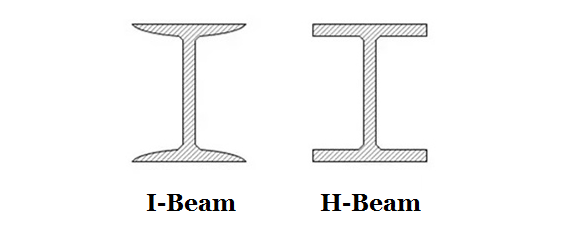
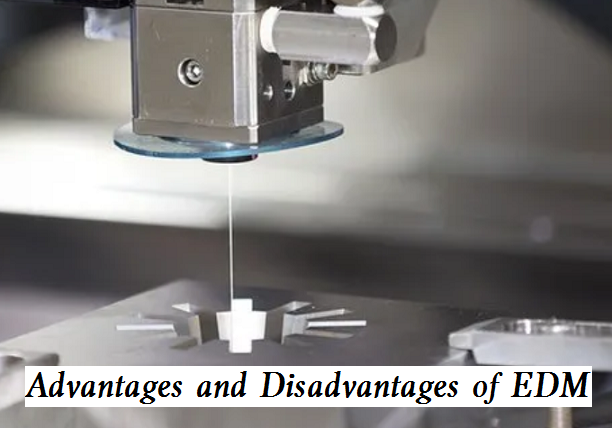
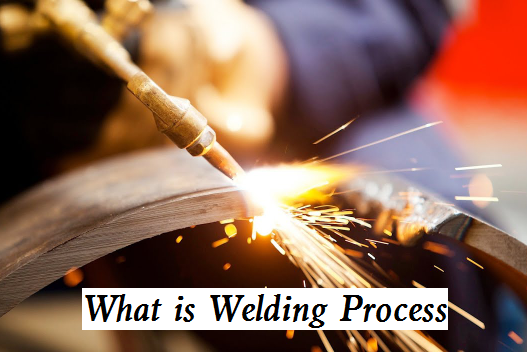
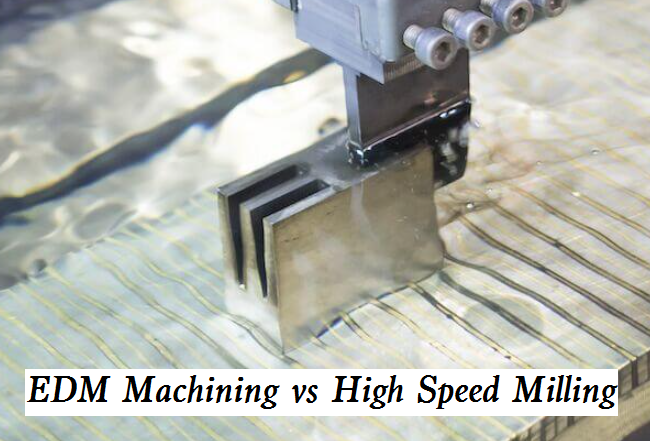
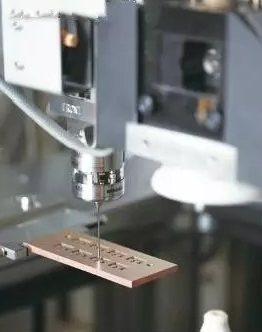