Runout tolerance is a crucial concept in geometric tolerancing used for controlling the variation in rotating parts during their operation. It ensures that CNC parts will run smoothly without wobbling or vibrating, which is essential for the reliability and precision of mechanical systems. This guide will explain the concept of runout tolerance, differentiate between circular runout and total runout, and provide usage guidelines.
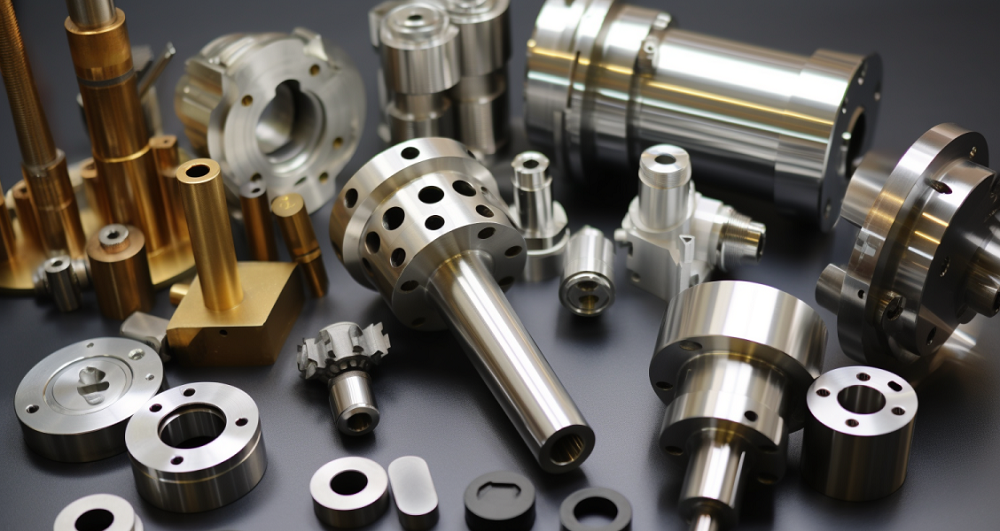
What is Runout Tolerance?
Runout tolerance is a type of geometric tolerance that limits the amount of variation or “wobble” in a rotating component’s surface as it turns around a datum axis. It is primarily used for cylindrical parts such as shafts, rollers, and collets, where regulating the surface variation is critical for the part’s functionality.
Unlike concentricity, which assesses the coaxiality of the cylindrical feature’s axis, runout tolerances focus on the surface deviations of the rotating component.
Also, be aware that runout tolerances are shape tolerances similar to roundness and cylindricity, but they require a datum axis to be specified because the controlled feature relates to that datum.
Types of Runout Tolerances
There are two types of runout tolerances:
- Circular Runout
- Total Runout
What is Circular Runout Tolerance?
Circular runout controls the variation of a surface element (a single line on the surface) when the part rotates around the datum axis. This tolerance limits the radial and axial displacement of the cylindrical surface or end face of a part.
How to Use Circular Runout Tolerance?
Radial Direction: To control the radial displacement, you don’t include a diameter symbol (φ) before the tolerance value because the tolerance zone is defined by two concentric circles.
Axial Direction: For controlling displacement in the axial direction, the tolerance is indicated without the diameter symbol and is defined by two parallel lines.
What is Total Runout Tolerance?
Total runout controls the cumulative variation of the entire surface as it rotates. Unlike circular runout, which only controls a single line element, total runout addresses the entire feature’s variation, including tapering or barrel-shaped surfaces.
How to Use Total Runout Tolerance?
Radial Direction: The indication for total runout is similar to circular runout but evaluates the entire surface’s displacement during rotation. The tolerance zone is between two concentric cylinders.
Axial Direction: For axial displacement control, the entire end face variation is limited, and the tolerance zone is between two parallel planes.
Distinguishing Circular Runout Tolerance from Total Runout Tolerance
Circular Runout: Controls a single surface line’s displacement. The tolerance zone is defined by concentric circles or parallel lines surrounding that line.
Total Runout: Controls the entire surface’s displacement. The tolerance zone is defined by concentric cylinders or parallel planes enclosing the surface.
Applications
Radial Runout: Used for rotating parts like bearings, where the tolerance controls the radial displacement of the surface.
Axial Runout: Applied to control the axial displacement of end faces on parts like gears, camshafts, or seating surfaces of bolts and nuts.
Runout tolerances are essential in ensuring that rotating parts operate smoothly and within acceptable limits of variation. When designing and inspecting parts, it’s critical to understand the type of runout required for the application and how to correctly specify it on technical drawings.
By following the guidelines above, engineers and machinists can effectively apply and measure runout tolerances to maintain the quality and functionality of rotating components.