The chatter in CNC machining can be a pervasive issue, affecting surface quality, tool life, and operational efficiency. Here, we’ll explore the phenomena of chatter, its causes, and practical strategies to mitigate its effects across various CNC machining processes including turning, milling, drilling, and cutting.
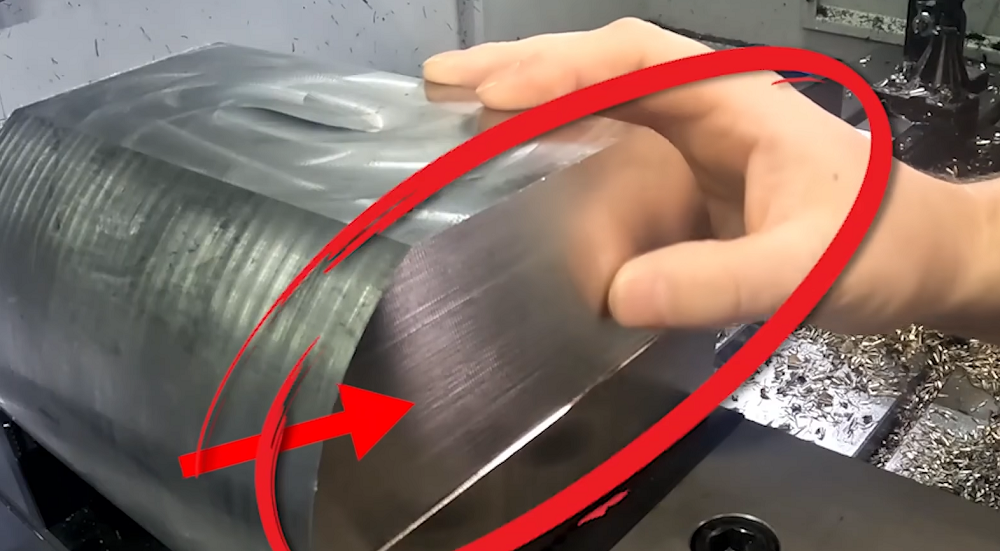
1. What is Chatter in Machining?
The chatter in machining, also known as vibration, refers to the vibration phenomenon in the cutting operation of machining processes such as CNC milling, turning, drilling, etc., which generates waves on the surface of the machined parts. It occurs when the workpiece and the cutting tool are vibrating at different frequencies. In other words, the part and the cutting tool move in different directions.
2. Types of Chatter in Machining
During machining, the deflection of the cutting tool and workpiece, caused by the stress of cutting, leads to a phenomenon known as chatter, which manifests as vibrations on the machined surface. This deflection and the subsequent return to form occur repeatedly, complicating the identification of a single causative factor for chatter. As such, it necessitates a systematic review of various potential factors including tool rigidity, chucking conditions, and the distance and direction of the load from the holding point to the machining point. It is a difficult task to examine each of these in detail, but the major factors that cause it can be narrowed down to a few. The major factors that cause chatter are summarized below, so let’s take a look at the two main types of chatter vibration in CNC machining and the causes of each:
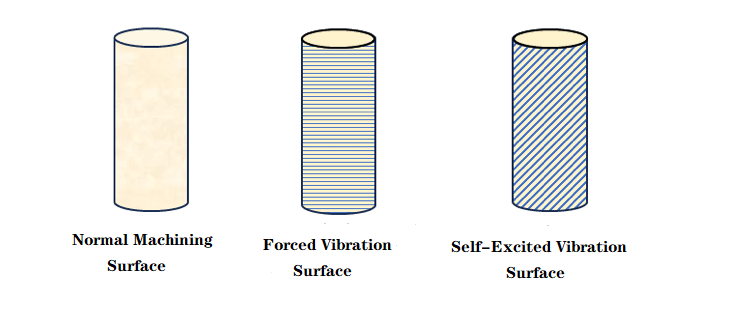
① Forced Chatter & What Causes the Vibrations
Results from external vibrations affecting the machine, such as intermittent cutting forces or mechanical resonances within the machine.
Causes of Forced Vibration
a) Disturbances related to force: Vibrations due to fluctuations in cutting force, intermittent cutting, and intermittent fluctuations in cutting thickness
b) Disturbances related to displacement variation: Vibrations from mechanical components (motors, shafts, gears, etc.), and vibrations transmitted from the machine base
② Self-Excited Chatter
Arises without external excitation, typically due to the interaction between the tool’s and workpiece’s dynamic responses.
Causes of Self-Excited Vibration
a) Regenerative effect: Variations in the machined surface caused by vibrations from a previous turn or previous tool pass affecting the current machining process (regeneration), and most self-excited vibrations are due to the regenerative effect, which causes large vibrations.
b) Mode coupling: Many vibration modes interacting to produce large vibrations.
3. What Causes Chatter in Machining?
Measures to deal with chatter vary depending on the shape of the workpiece being machined and the rigidity of the machine, but here are 6 points that are particularly likely to be the cause:
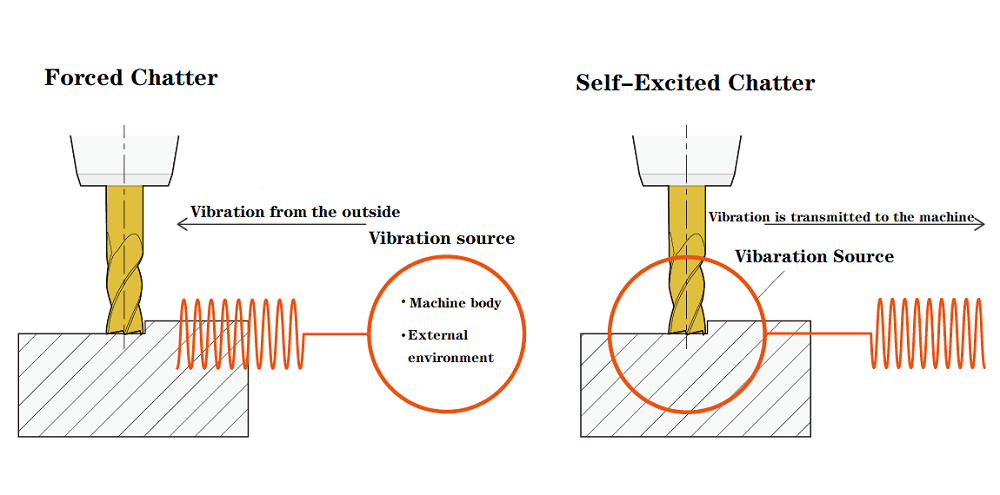
① Machining conditions
When chatter occurs, first review the machining conditions. The best way to eliminate chatter while maintaining the current equipment status is to change the machining conditions. The basic measure is to change the machining conditions so that the cutting resistance is reduced. In general, the following three machining conditions have a large effect on the occurrence of chatter.
Circumferential speed (rotation speed)
A slower circumferential speed reduces cutting resistance and can reduce chatter. When chatter occurs, it is a good idea to first slow down the circumferential speed and check how chatter occurs.
Feed amount (distance the tool travels per revolution)
Regarding the feed amount, whether it is large or small, chatter can occur. Changing the feed amount can change the vibration and eliminate chatter, so change the feed amount around the value at which chatter occurs and check how chatter occurs.
Depth of cut (cutting depth)
As with the feed amount, chatter can occur whether the depth of cut is large or small. Similarly, change the value around the depth of cut at which chatter occurs and check how chatter occurs by changing the vibration.
Note that changing the machining conditions may affect the cycle time, so consider making changes based on both the cycle time and the degree of chatter.
② Tool overhang length
One of the major factors in vibration is the tool overhang length. The longer the overhang length, the more likely vibration will occur. The calculation of the amount of deflection is roughly determined by the “length,” “thickness,” and “load” of the tool, but “length” has a particularly large impact. “Thickness” also has an equally large impact, but it would be difficult to significantly improve the thickness in reality. Also, as mentioned at the beginning, internal diameter processing is a process that often results in long overhangs. It is ideal to use a tool with as short an overhang length as possible for each workpiece.
③ Workpiece thickness
If the workpiece is thin, it is more likely to vibrate. This pattern occurs when the workpiece cannot withstand the cutting resistance and deflects. If external diameter machining is performed before internal diameter machining, it is a good idea to check whether vibration can be suppressed by changing the order of machining. By performing internal diameter machining while the workpiece is still thick, vibration can be suppressed.
④ Tip nose R
The smaller the nose R, the smaller the cutting resistance and the less likely vibration will occur.
Regardless of the nose R, if the cutting tool is damaged, the cutting resistance may be increasing, so if vibration appears after long use, consider replacing it with a new one. “Introducing angle” and “rake angle” Items related to the cutting edge include “introducing angle” and “rake angle”.
The part that actually cuts the workpiece is the contact part of the tool (chip), so chatter can be reduced by slightly improving this part. By changing the entering angle, the machining resistance can be shifted to a direction that reduces deflection. Also, machining resistance can be reduced by machining with a positive rake angle.
⑤ Chucking condition
If the chucking force is weak, the workpiece is more likely to shake and chatter. It would be fine if you could simply increase the chucking force, but be aware that you also need to take into account the deformation of the workpiece. Even if it is difficult to chuck a workpiece with strong chucking, if the workpiece can be center-pushed, center-pushing can be used to reduce shaking to some extent. Also, if the machine has a lower turret, you can stabilize the workpiece by supporting it with the lower turret while machining.
⑥ Resonance due to natural frequency
It is possible that chatter is caused by resonance between the workpiece and the tool. You can determine whether resonance is occurring by using a vibration measuring device to check.
If it is caused by resonance of the natural frequency, it may be improved by slightly changing the machining conditions.
4. How To Reduce & Stop Chatter on a Lathe?
We will introduce how to deal with each type of chatter vibrations based on the causes:
Methods To Reduce Forced Vibration on a Lathe
Forced vibration occurs when some external force is amplified by the machine. Although the analysis calculation of the amplification rate is omitted, the amplified vibration can be determined.
Type of Vibration | Response Method | Specific Examples of Response Methods | Remarks |
Vibration due to fluctuation in cutting force | – Reduce cutting force <br> – Change forced vibration | – Change tool shape <br> – Change number of blades <br> – Change to unequal pitch | Fewer blades reduce vibration <br> Unequal pitch is adopted in end mills |
Vibration of machine parts | – Replace vibrating parts <br> – Change natural frequency of vibrating parts <br> – Change or block vibration path | – Change type of parts such as motors <br> – Change vibration path from linear to circular | Changing parts alters natural frequency <br> (also leads to change in vibration path) |
External vibrations from base, etc. | – Change or block vibration path <br> – Vibration damping measures | – Change to a vibration-damping base <br> – Install rubber mounts | – |
Other | – Improve dynamic rigidity of mechanical system | – Increase motor rigidity | Rigidity against dynamic forces during acceleration and deceleration (e.g., motors) |
Methods To Reduce Self-Excited Vibration on a Lathe
Self-excited vibrations are due to characteristics related to the machining system’s vibration.
Reduce & Stop Self-Excited Vibration
Characteristic | Response Method | Specific Examples of Response Methods | Remarks |
Cutting characteristics | Change tool | – Increase helix and rake angles <br> – Adopt unequal pitch | Unequal pitch avoids resonance |
Cutting characteristics | Change cutting conditions | – Reduce cutting speed <br> – Reduce feed rate <br> – Increase spindle speed <br> – Decrease spindle speed | – |
Dynamic characteristics of machine | Improve dynamic characteristics of machine structure | – Use high-rigidity machines <br> – Use resin concrete structure | Resin concrete has superior compressive, tensile, and bending strength |
Dynamic characteristics of tool | Improve dynamic characteristics of tool | – Use helix bars | Treats the shank as a spring to suppress vibrations |
Strageties to vibration have been organized into forced vibration and self-excited vibration. Vibration is rarely caused by a single factor; often, several factors overlap, resulting in significant vibration. Therefore, when vibration occurs, it is essential not to focus on a single cause but to consider all possible factors, regardless of whether they are forced or self-excited, and respond accordingly.
Methods To Reduce Chatter on Machining Tools
Countermeasures for chatter vibration can be considered for each cutting tool. Here, as an example, we introduce responses to chatter vibration from the troubleshooting of end mills.
Reduce & Stop Chatter Vibration in End Mills
Type | Cause | Response | Remarks |
Machining conditions | High cutting speed | Reduce cutting speed | Lower the RPM |
Machining conditions | Slow feed rate | Adjust the feed per tooth | – |
Machining conditions | High cutting resistance | – Make shallower cuts <br> – Use tools with fewer flutes | – |
Machining conditions | High rake and clearance angles | Adjust angles or change the tool | – |
Tool | Low rigidity | – Increase tool diameter <br> – Use solid carbide, etc. | Increases rigidity |
Tool | High helix angle | Use tools with smaller helix angles | High helix angles can lead to decreased corner strength, tool pullout, and flexing of thin workpieces |
Tool | Long protrusion length | Minimize as much as possible | Increases bending moment during cutting |
Tool | High number of flutes | Reduce the number of flutes (2-3) | More flutes increase rigidity, improve surface finish, and extend tool life, thus requiring a trade-off adjustment |
This table has introduced responses to chatter vibration for end mills, but similar factors can be considered for other tools as well. This is because chatter vibrations are caused not solely by the tool itself but also by external vibrations and differences in machining conditions and cutting forces. Moreover, from the mechanism of chatter vibrations, similar conditions occur in any machining operation, and if conditions are not matched, chatter vibrations will occur. It would be beneficial to apply the response methods listed in the table to other tools to address chatter vibrations.
Below we also list some common ways to reduce and eliminate vibration in different processing types.
5. How To Reduce & Stop Chatter Vibrations in CNC Milling?
To reduce and stop chatter in CNC milling, which can significantly impair the quality of machined parts, it’s crucial to address several key factors as explained in the original text. Here’s a breakdown of the strategies to handle chatter:
1. Ensure Rigidity in Fixtures or Setup
Insufficient support for the piece being machined can lead to vibration and chatter. Use high-quality, rigid clamping systems and fixtures. In the text, serrated jaws that grip the material strongly from both sides are mentioned. Also, re-tightening the grips after the initial setup can ensure a secure hold.
2. Ensure Rigidity in Tool and Tool Holder
A tool that is not sufficiently rigid can also vibrate, contributing to chatter. Utilize robust tool holders with features that enhance stability. For instance, the text mentions a dual-contact holder (Big Plus holder) that contacts both the taper and the flange face of the spindle, increasing stability. Additionally, using a hydroforce holder with a large diameter near the tool also helps in reducing flexibility and vibration. The shorter the tool projection from the holder, the better, as it reduces the leverage effect that can induce vibrations.
3. Adjust Tool Pressure and Cutting Parameters
Incorrect cutting parameters, like speed and feed, can lead to inadequate tool pressure, causing the tool to bounce or vibrate. Adjusting the surface footage (cutting speed) and feed rate can help. Reducing the RPM while maintaining the feed rate increases the chip load, which in turn increases the cutting pressure, stabilizing the tool. Alternatively, increasing the feed rate while keeping the speed constant can also increase the pressure on the tool, reducing chatter.
4. Optimize Stock and Cutting Depth
Adjust the amount of material left for finishing cuts. Sometimes, leaving too little or too much material can lead to chatter during the final passes.
5. Tool Path Optimization
Sometimes modifying the tool path can help reduce chatter by distributing the load on the tool more evenly or by avoiding resonance frequencies that may cause vibrations.
6. How To Reduce & Stop Chatter Vibrations in Drilling?
Chatter in CNC drilling can significantly affect the quality of drilled holes, lead to tool breakage, and decrease productivity. It’s caused by vibrations between the workpiece and the tool, which can result in poor surface finishes and inaccurate hole dimensions. Here’s how you can reduce and stop chatter in CNC drilling:
1. Use the Correct Tooling
Drill Type and Material: Select the appropriate drill material and geometry for the workpiece material. For instance, carbide drills are better for harder materials due to their higher rigidity and wear resistance.
Tool Coatings: Consider coated tools which can enhance tool life and performance, reducing vibrations caused by wear.
Sharp Tools: Ensure that drills are sharp and well-maintained. Dull tools increase cutting forces, leading to more vibration and chatter.
2. Optimize Cutting Parameters
Cutting Speed and Feed Rate: Start with manufacturer-recommended speeds and feeds but be prepared to adjust. Generally, increasing the speed and reducing the feed can help reduce chatter, but this can vary based on the material and tooling.
Peck Drilling: Use peck drilling cycles for deep holes. This technique involves periodically retracting the drill bit to clear chips and cool the tool, which can help reduce buildup of forces that lead to chatter.
3. Enhance Machine and Workpiece Rigidity
Secure Clamping: Ensure that the workpiece is securely clamped. Any movement during drilling can initiate or worsen chatter.
Machine Condition: Regular maintenance of the CNC machine is crucial. Loose components, such as spindle bearings or worn guideways, can exacerbate vibrations.
Minimize Overhang: Use the shortest possible tool overhang from the tool holder to increase rigidity and reduce deflection.
4. Use Dampening Techniques
Vibration Dampeners: Install anti-vibration devices or use tool holders with built-in damping features to absorb vibrations.
Through-Spindle Coolant: This can provide both cooling and damping effects by reducing heat buildup and flushing away chips efficiently.
5. Adjust Drill Geometry
Point Angle and Helix Angle: Adjust these based on the material. A larger point angle or a different helix angle can improve chip evacuation and reduce the forces acting on the drill, thereby minimizing chatter.
6. Software and Monitoring Tools
Simulation Software: Use CNC software to simulate the drilling paths and identify potential problems before actual machining.
Monitoring Systems: Advanced CNC systems equipped with monitoring tools can detect and adjust to vibrations in real-time, automatically modifying parameters to reduce chatter.
7. How To Reduce & Stop Chatter Vibrations in Turning?
To reduce and stop chatter in CNC turning, especially when dealing with long, slender parts that are prone to vibration, it’s important to consider several factors that affect the stability of the machining process. Here’s a detailed guide based on the provided text, focusing on the tooling, machining parameters, and setup adjustments:
1. Tooling Selection
Boring Bars: Choose the right type of boring bar material based on the rigidity needed for the operation. The text mentions three types: steel, heavy metal, and solid carbide. Carbide bars, being the most rigid, generally provide the best resistance to chatter, followed by heavy metal, and then steel.
Inserts: The choice of insert can significantly affect chatter. Inserts with different nose radii (0.031″, 0.156″, and 0.078″) were tested, showing that larger nose radii generally perform better in reducing chatter due to their reduced cutting forces.
2. Machining Parameters
Speed and Feed: Adjusting the cutting speed can have a profound effect on chatter. It was noted that reducing the speed as the tool moves deeper into the part (where the setup is less rigid) can help minimize chatter. The feed rate was kept constant to meet surface finish requirements, but adjusting it may also be necessary depending on the outcome.
Depth of Cut: Reducing the depth of cut from 30 thou to 20 thou showed some improvements in reducing chatter. A shallower cut reduces the load on the tool, thereby decreasing the tendency to vibrate.
3. Setup Adjustments
Boring Bar Length: Keeping all boring bars at the same length helps eliminate variations that could lead to instability and chatter. The closer the tool is to the turret, the more stable it is.
Support Near the Cutting Zone: Increasing support near the jaws or the cutting zone can enhance stability. The text suggests that closer to the jaws (where the part is more rigid), chatter was reduced.
8. How To Reduce & Stop Chatter Vibrations in Grinding?
Chatter in CNC grinding is characterized by vibrations between the grinding wheel and the workpiece, which can significantly degrade the surface quality and precision of the machined parts. It manifests as unwanted, repetitive patterns or waves on the surface of the workpiece.
Proper Wheel Maintenance:
Maintain and dress the grinding wheel regularly to ensure it remains sharp and well-balanced. This reduces vibration caused by uneven wheel surfaces.
Balancing and Mounting of the Wheel:
Ensure the grinding wheel is perfectly balanced and correctly mounted. Any imbalance or misalignment can induce vibrations.
Optimal Workpiece Fixturing:
Secure the workpiece properly to minimize vibrations. Check the setup for any misalignments or looseness.
Use of Optimal Grinding Fluids:
Utilize the correct type and amount of grinding fluid. Grinding fluids help in cooling, lubricating, and removing debris from the grinding area, which can reduce friction and chatter.
Machine Condition and Setup:
Regular maintenance of the grinding machine is crucial. Ensure all mechanical components are in good working condition and that the machine settings are optimized for the specific grinding operation.
Adjust Grinding Parameters:
Modify the depth of cut, feed rates, and the speed of the grinding wheel based on the material and the type of grinding operation. Experiment with these parameters to find a setting that minimizes chatter.
Use of Advanced Wheel Technologies:
Consider using special grinding wheels like the “Vitrified CBN Wheel ‘Sakura’” mentioned in the article, which features a structure that reduces grinding resistance and thus minimizes the occurrence of chatter.
Vibration Damping Techniques:
Implement vibration damping solutions in the machine setup, such as using anti-vibration mounts or pads under the machine.
Handling chatter effectively requires understanding the interaction of machine dynamics, tooling, and workpiece properties. By adjusting machine settings, enhancing rigidity, and using appropriate tooling, manufacturers can significantly reduce the occurrence of chatter, leading to improved productivity and product quality. Each situation may require a unique combination of these strategies, emphasizing the importance of a tailored approach to CNC machine operations.