Threading operations are a daily routine in CNC machining, yet they carry the inherent risk of tap breakage – a setback that can lead to downtime, additional costs, and frustration. This guide breaks down the anatomy of a tap, the various factors leading to its breakage during CNC operations, and the meticulous process of removing a broken tap from a workpiece. Furthermore, it offers an in-depth exploration of preventative measures to avert tap failure, ensuring the continuity and efficiency of your machining processes. Let’s navigate through the causes, removal techniques, and, most importantly, the strategies to prevent tap breakage, securing the integrity and success of your threading tasks.
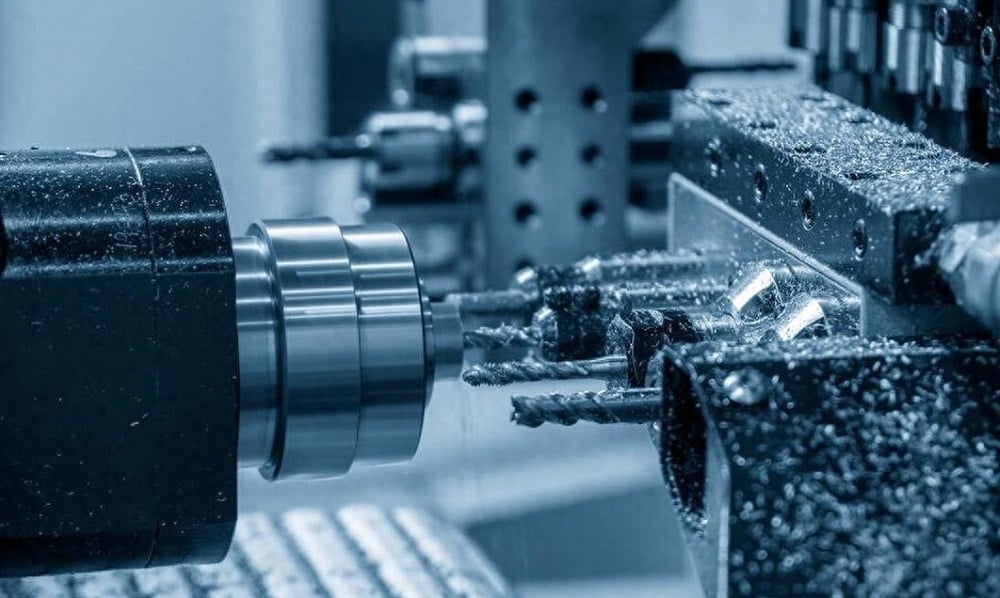
What is Tap in CNC Machining?
A tap is a cutting tool used in manufacturing to create internal threads within pre-drilled holes. It consists of a shank for holding purposes, flutes for chip evacuation, and cutting teeth that come in different chamfer styles (taper, plug, and bottoming) for starting and threading operations. Taps are made from materials like high-speed steel and can have coatings such as Titanium Nitride for increased durability. They are used in both manual and CNC operations, where precision and control are crucial, and the choice of tap type, size, and material, as well as the use of appropriate lubrication and correct machine settings, are essential for producing clean and accurate threads.
What Causes Tap to Break in Machining?
There are generally 10 main reasons why taps break during CNC machining:
1. Incorrect tap selection:
Choosing an improper tap is a common cause of tap breakage in CNC machining. Different quality taps such as cobalt-alloy or coated taps should be selected according to the material hardness. The tap design features such as the number, size and angle of flute also affect chip removal performance, and an incompatible design will increase the risk of breakage.
2. Issues with tap quality itself:
The material, design, heat treatment, machining accuracy and coating quality of the tap will affect its performance. For example, an abrupt cross section transition or lack of rounded transitions can lead to stress concentration and breakage. Issues with heat treatment processes such as insufficient preheating, improper quenching or delayed tempering can also cause cracks and reduce the tap’s overall performance.
3. Issues with the workpiece material:
If the workpiece material has high impurity content, hard spots or pores, the tap may suddenly encounter uneven resistance during machining and break as a result. Therefore, the purity and uniformity of the material are critically important for preventing breakage.
4. Mismatch between tap and material:
The increasing variety of new materials has led to more tool material options. The appropriate tap must be selected according to the material characteristics to handle different machining difficulties and properties before starting CNC machining.
5. Improper bottom hole diameter:
A bottom hole diameter that is too small will subject the tap to excessive cutting forces during thread tapping, increasing the risk of breakage. Selecting the correct bottom hole diameter is key to avoiding this issue, and it should be properly adjusted according to the tap type and workpiece material.
6. Issues with cutting fluid or lubricant:
Using low-quality cutting fluid or lubricant can result in burrs on the machined surface and greatly reduce the tap’s service life. A suitable cutting fluid can not only improve machining quality but also reduce cutting resistance to lower the risk of tap breakage.
7. Insufficient machine precision:
The precision of the machine and fixtures directly affects the performance of the tap. Insufficient concentricity of the machine could cause excessive torque on the tap during thread tapping, leading to breakage. Ensuring the precision of the machine and clamping components is critical for avoiding tap breakage.
8. Unreasonable cutting speed and feed rate:
Improper setting of cutting speed and feed rate will increase the load on the tap. Excessive feed rate can cause overload, while too slow can reduce tap efficiency and potentially impact thread accuracy and surface quality.
9. Insufficient operator skill:
The technical level of the operator directly impacts the service life of the tap. Errors like failing to slow down as the tap reaches the hole bottom or forcing chips clearance can cause breakage. Operators need a thorough understanding of the entire process and ability to timely adjust operations to prevent accidents.
10. Poor equipment maintenance and wear:
The maintenance condition and long-term wear of the machine will also affect precision in CNC machining. Worn main spindles, loose fixtures and imprecise guides can all potentially cause tap deflection or deviation during machining, increasing the risk of breakage. Regular machine maintenance and inspection are critically important for maintaining machining precision and tap integrity.
How Remove Broken Tap in Different Situations?
The task of removing a broken tap or drill from a hole can be quite challenging, but there are several methods to attempt, each suitable for different situations. Here, we’ll detail those broken tap removel methods for specific scenarios:
Situation 1: The Broken Tap is Accessible and Not Too Hard
If the broken tap is sticking out or accessible and not made of very hard material, flattening the end and center punching to start a smaller drill bit may work. Drill straight down carefully to avoid further damage to the threads. After drilling, an extractor can be used to reverse the tap out. If an extractor is not available, progressively larger drills can be used until the tap begins to break up and can be removed. This method is straightforward and preserves the integrity of the original threads, allowing for retapping with the same size tap afterward.
Situation 2: The Broken Tap is Deep in a Blind Hole
For taps broken deep within blind holes, more sophisticated methods like spark erosion or wire EDM (Electrical Discharge Machining) may be required. These methods use electrical discharges to erode the broken tap without making contact with the workpiece, thus preventing further damage to the threads. Once the bulk of the tap is removed, the remaining fragments can be picked out. This method is precise but can be expensive and time-consuming, and requires specialized equipment.
Situation 3: The Broken Tap is Very Hard or Seized
In cases where the tap is very hard or seized, heating the tap using an oxy-acetylene torch or similar method to anneal it might be necessary. The heat alters the tap’s hardness, making it easier to drill out with a carbide bit. However, care must be taken to avoid overheating and damaging the workpiece. After annealing, if the tap becomes brittle, it may be broken up with a punch and then extracted.
Situation 4: The Broken Tap Cannot Be Drilled
If the tap is undrillable due to its hardness or the risk of damaging the hole, chemical methods like using nitric acid to corrode the tap can be considered. This method requires careful application to avoid damaging the workpiece material and should be carried out with appropriate safety measures in place.
Situation 5: The Tap and Drill are Both Broken in the Hole
When both a tap and a drill are broken in the hole, it may be necessary to use a combination of methods. Starting with a penetrating oil to loosen any corrosion and then carefully attempting to chip, drill, or use EDM to remove the broken pieces is a multi-step approach. Each action must be taken cautiously to prevent further damage to the workpiece.
Situation 6: The Broken Tap is in a Through Hole
If the tap is broken in a through hole, wire cutting to create crosswise cuts in the tap may allow you to break it into smaller pieces which can then be removed more easily. This method takes advantage of the fact that the opposite side of the hole can be accessed to push out the broken pieces.
Situation 7: The Broken Tap is in a Blind Hole
When faced with a broken tap in a blind hole, machinists have several options, although each comes with its own set of challenges. One effective method is Electro-Discharge Machining (EDM), which can precisely erode the tap without damaging the surrounding material, but requires specialized equipment. Alternatively, one could use a tap extractor, which fits into the tap’s flutes and allows for reverse twisting. Left-hand drill bits can sometimes catch and unscrew the tap, while chemical methods, such as alum solutions, may dissolve it without harming the workpiece. Manual chipping with a punch or chisel can also work, albeit with a risk of damaging the thread integrity. In some cases, heat can be applied to expand and then contract the tap, making it easier to remove. If the thread’s preservation isn’t crucial, drilling out the tap to a larger size and retapping or installing a helicoil may be the most straightforward solution. Each technique requires a careful approach to avoid further damage to the workpiece.
Situation 8: Unique Methods for Specific Materials
Certain materials like cast iron, which are brittle, may allow for easier removal of broken taps using wire extractors. For harder materials like steel, high-temperature methods involving heating to around 1200-1300 degrees Celsius and then cooling can make the tap brittle enough to break and remove. However, this could alter the mechanical properties of the steel if not done correctly.
Situation 9: The Broken Tap is Small or in a Delicate Material
For small diameter taps or when working with delicate materials that may be easily damaged, manual methods such as using a pointed awl, chisel, or a homemade tool that fits into the flute spaces of the tap can be effective. Gentle hammering in the reverse direction may gradually loosen the broken piece for extraction. The key here is patience and precision to avoid further damage to the workpiece.
Situation 10: The Tap Breaks Off Flush or Below the Surface
When a tap breaks off flush or below the surface, and there’s no protruding part to grip, a slot may be carefully chiseled or ground into the broken end. Then, a flat-head screwdriver or a specialized tap removal tool can be used to unscrew the tap. This method requires a steady hand and a delicate touch to ensure the slot is properly cut without damaging the surrounding threads.
Situation 11: The Tap is Made of a Material Resistant to Drilling
In cases where the tap material is resistant to drilling, such as hardened steel or special alloys, a portable EDM tool can be used to disintegrate the tap without physical contact. This is useful when traditional drilling is not an option due to the risk of damaging the workpiece or when carbide drills are ineffective.
Situation 12: The Workpiece Cannot be Moved to a Machine
If the workpiece is too large or cumbersome to move to a machine for processes like EDM, chemical removal methods might be necessary. For example, applying a rust penetrant or a mixture that includes alum can slowly dissolve the tap material over time. This process can be slow and requires monitoring to ensure that only the tap is being dissolved and not the workpiece.
Situation 13: All Else Fails
If all else fails and the broken tap cannot be removed, or it is not economical to do so, the workpiece may be modified to bypass the issue. For instance, drilling a new hole adjacent to the one with the broken tap and reconfiguring the design to accommodate the change might be a practical solution. Alternatively, if the hole is not critical to the part’s function, it may be filled with a weld, ground down, and left in place.
How To Avoid Tap Breakage in CNC Machining?
Removing the broken tap is sometimes simple, but in other cases it is time-consuming and costly. Therefore, it is also crucial to avoid tap damage and breakage. Explore the key methods to prevent the costly and time-consuming issue of tap breakage in CNC machining, ensuring smoother operations and higher-quality threading.
- Proper Tap Selection
Avoiding tap breakage during CNC machining starts with the correct tap selection. It is crucial to choose a tap that matches the material being machined. Hard materials may require taps with specific coatings or geometries to reduce wear and prevent breakage. Moreover, selecting the correct tap size and type (such as spiral point or spiral flute for chip evacuation) is essential for the material and hole specification. A tap that is too large can cause excessive stress, while a tap that is too small may break under the pressure. Taps with appropriate flute designs help in chip removal, reducing the risk of clogging and snapping. Additionally, using a tap designed for through-holes or blind holes accordingly can significantly reduce the risk of breakage.
- Speed and Feed Optimization
Optimizing the spindle speed (RPM) and feed rate is critical in preventing tap breakage. Each material has an optimal cutting speed and feed that should be adhered to. Exceeding these rates can cause overheating and tap wear, while too low rates can lead to poor thread quality and increased tap stress. CNC machines often have recommended settings for various materials, but it can also be beneficial to refer to the tap manufacturer’s specifications. The use of a tapping cycle that matches the tap type and material, such as a peck tapping cycle for blind holes to break chips and allow coolant to reach the tap, can also help prevent breakage.
- Correct Tool Holding and Alignment
The tap must be held correctly in a high-quality collet or tapping chuck that provides proper alignment and consistent grip to prevent wobbling and misalignment, which can lead to tap breakage. A tap that is not held straight can bind in the hole and snap under the lateral forces. Additionally, a floating tap holder or tension/compression tap holder can compensate for any synchronization issues between the spindle and the feed, ensuring that the tap engages with the material smoothly without any axial forces that could cause breakage.
- Adequate Lubrication
Sufficient lubrication is paramount to prevent tap breakage. The right cutting fluid not only cools the tap and the workpiece but also lubricates the cutting action, reducing friction and heat build-up. This is especially important in materials that are prone to creating stringy chips or are particularly tough to machine. In some cases, a tapping fluid specifically designed for difficult-to-machine materials can make a significant difference. Regularly checking and maintaining the coolant system ensures that the flow and pressure are adequate to reach the cutting zone and effectively reduce the risk of tap breakage.
- Machine Maintenance and Condition
Regular maintenance and ensuring the CNC machine is in good condition can prevent many issues, including tap breakage. Calibration of the machine ensures accurate spindle alignment and reduces the chance of misfeeds or off-center tapping. Additionally, maintaining the spindle and feed motors in good working condition ensures that the feed rate and speed are consistent and accurate. Regular checks for wear and tear on tool holders, collets, and spindles can also prevent misalignment and imprecise tapping, which can otherwise lead to tap breakage.
- Gradual Engagement and Exit
When starting the tap into the hole, a gradual engagement helps to distribute the cutting forces evenly and prevent an initial shock to the tap that can cause breakage. Similarly, as the tap exits the material, particularly in through-hole applications, it is important to reduce the feed rate to ease the tap out of the material. This gradual exit allows the tap to cool down and reduces the potential for binding, which can occur if the tap is suddenly released from the workpiece material’s engagement.