In the realm of manufacturing, casting is a cornerstone process that enables the creation of intricate and complex metal parts. Investment casting and sand casting are two prominent methods within this realm, each offering distinct advantages and drawbacks. This comprehensive article endeavors to explore and dissect these differences, shedding light on the nuances that set investment casting and sand casting apart. By the end, readers will have gained a comprehensive understanding of these casting techniques, aiding them in making informed decisions when selecting the most suitable method for their specific needs.
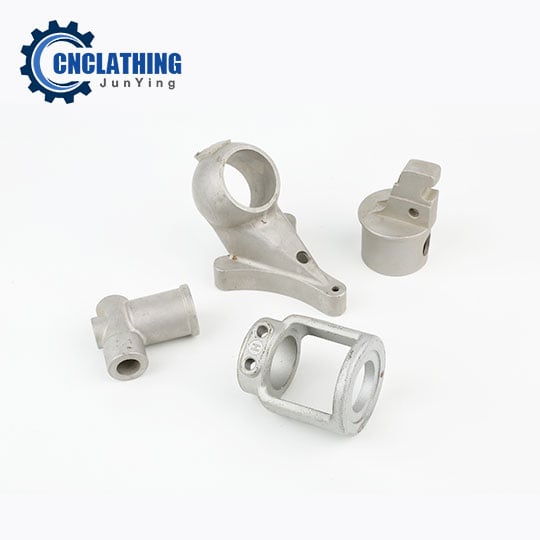
Investment Casting vs. Sand Casting: Comprehensive Comparative Analysis
Casting, an age-old manufacturing process, involves the creation of objects by pouring molten metal into a mold, which then solidifies and takes on the desired shape. Investment casting and sand casting are both widely utilized methods for this purpose, yet they employ contrasting techniques to achieve their end results.
What is Investment Casting?
Investment casting, often referred to as lost-wax casting, stands as a meticulous and intricate process. It involves creating a wax pattern of the desired part, which is then coated with a ceramic shell. This shell is subsequently heated to melt away the wax, leaving behind a hollow mold. Molten metal is then poured into this mold, taking the shape of the intricate interior, and solidifying to form the final component.
The precision offered by investment casting is unmatched, making it ideal for crafting parts with intricate geometries, fine details, and thin walls. The process preserves the intricate design intricacies with exceptional accuracy, resulting in parts that require minimal post-processing.
What is Sand Casting?
On the other hand, sand casting, a method with roots dating back millennia, relies on sand molds to shape molten metal. A pattern, often made of wood or metal, is pressed into a specially prepared sand mixture, leaving behind a cavity. Molten metal is then poured into this cavity, filling the void and solidifying to form the final product.
The simplicity of sand casting makes it a versatile and cost-effective choice, especially for larger components and prototypes. However, the level of detail achievable through this method is generally lower compared to investment casting, and additional machining or finishing might be required to achieve the desired specifications.
Material Suitability Difference: Diverse Alloys and Applications
The choice of casting method can significantly impact the types of alloys that can be used and the resulting mechanical properties of the components.
Investment Casting: A Spectrum of Materials
Investment casting shines when it comes to accommodating a wide range of materials. From stainless steels to superalloys, and even non-ferrous metals, investment casting’s flexibility allows for the production of parts with varying material characteristics. This makes it a go-to choice for industries requiring specialized alloys, such as aerospace, medical, and jewelry.
Sand Casting: Versatility in Materials
While sand casting is also compatible with a variety of materials, its suitability for certain alloys might be limited due to the nature of the process. Materials with high melting points or reactive properties might pose challenges during sand casting. However, for materials that are well-suited to the process, such as cast iron and certain aluminum alloys, sand casting provides a cost-effective and reliable solution.
Surface Finish Difference: The Quest for Perfection
Surface finish plays a crucial role in the functionality and aesthetics of cast components, making it a key consideration when selecting a casting method.
Investment Casting: Artisanal Smoothness
Investment casting’s meticulous process lends itself to exceptional surface finishes. The ceramic shell molds, coupled with the wax patterns, allow for intricate details to be captured with precision. The resulting parts exhibit minimal surface defects, requiring minimal post-casting finishing. This makes investment casting particularly desirable for components destined for applications where smooth surfaces are critical, such as jewelry and high-end machinery.
Sand Casting: Texture and Realism
Sand casting, while versatile, often yields components with rougher surfaces due to the texture of the sand molds. These surfaces might require additional finishing steps to achieve the desired level of smoothness. However, for applications where a rugged or textured aesthetic is acceptable or even desirable, the inherent texture of sand-cast parts can add character and uniqueness to the final product.
Dimensional Accuracy Difference: Precision Matters
The accuracy with which cast components match their intended dimensions is a vital factor in various industries.
Investment Casting: Nailing the Precision
Investment casting’s meticulous process, involving wax patterns and ceramic molds, leads to exceptional dimensional accuracy. The intricate details of the wax pattern are faithfully recreated in the final metal part. This makes investment casting an ideal choice for components with intricate geometries or critical tolerances, such as turbine blades or medical implants.
Sand Casting: Tolerating Variability
Sand casting, while capable of producing accurate components, might introduce slightly more variability in dimensional accuracy due to factors like the properties of the sand mold and the pouring process. However, this can be mitigated through careful mold design and process control. Sand casting is often favored for applications where strict dimensional tolerances are not the primary concern.
Cost Difference: Balancing Budgets
The financial aspect plays a pivotal role in selecting the most suitable casting method for a project.
Investment Casting: Precision at a Price
The intricate and multi-step nature of investment casting can make it a more expensive method compared to sand casting. The production of wax patterns, the creation of ceramic molds, and the associated labor contribute to higher costs. However, the investment is often justified by the precision and quality achieved, making it an optimal choice for industries where performance and aesthetics take precedence.
Sand Casting: Economical Solutions
Sand casting’s relatively straightforward process and the use of readily available materials contribute to its cost-effectiveness. For large-scale productions or projects with budget constraints, sand casting can provide a cost-efficient solution while still delivering reliable results. This makes sand casting a popular choice for industries such as automotive and construction, where cost plays a significant role in decision-making.
Environmental Impact Difference: The Sustainability Perspective
In an era of heightened environmental awareness, the ecological footprint of manufacturing processes is a growing concern.
Investment Casting: Precision with Care
Investment casting, while resource-intensive due to the creation of wax patterns and ceramic molds, can yield less material waste compared to other methods. The precision offered by investment casting reduces the need for excessive post-processing, which in turn reduces material consumption and waste generation. This makes it a more environmentally conscious choice in applications where precision is paramount.
Sand Casting: Balancing Act
Sand casting, despite its simplicity, can generate larger amounts of waste due to the disposable nature of sand molds. However, efforts are being made to improve the sustainability of sand casting through recycling and reclaiming techniques. When considering the environmental impact, sand casting might be more suitable for projects where higher material usage is acceptable or where recycling initiatives are in place.
Making the Casting Choice: Factors for Consideration
Choosing between investment casting and sand casting is a multifaceted decision influenced by a spectrum of factors that extend beyond technical aspects.
- Design Complexity and Functionality – The level of intricacy required and the functional demands of the component play a pivotal role in selecting the appropriate casting method.
- Material Selection and Properties – The mechanical, thermal, and chemical properties of the chosen material dictate whether investment casting’s precision or sand casting’s adaptability is more suitable.
- Production Volume and Economics – The production volume needed, as well as budget constraints, influence whether investment casting’s intricacy or sand casting’s cost-effectiveness takes precedence.
- Time Constraints and Lead Times – Time-sensitive projects may favor sand casting due to its faster mold preparation and production processes.
- Surface Finish and Aesthetic Goals – The desired surface finish, whether smooth and flawless or textured and rugged, guides the casting method selection.
In the end, whether one seeks the elegance of precision or the pragmatism of versatility, investment casting and sand casting remain steadfast tools, ready to shape the future of manufacturing, one molten metal pour at a time.