We compare and discuss the differences between PA6 and PA66 engineering plastics in terms of Chemical Composition, physical properties, application, injection molding process, price, etc.
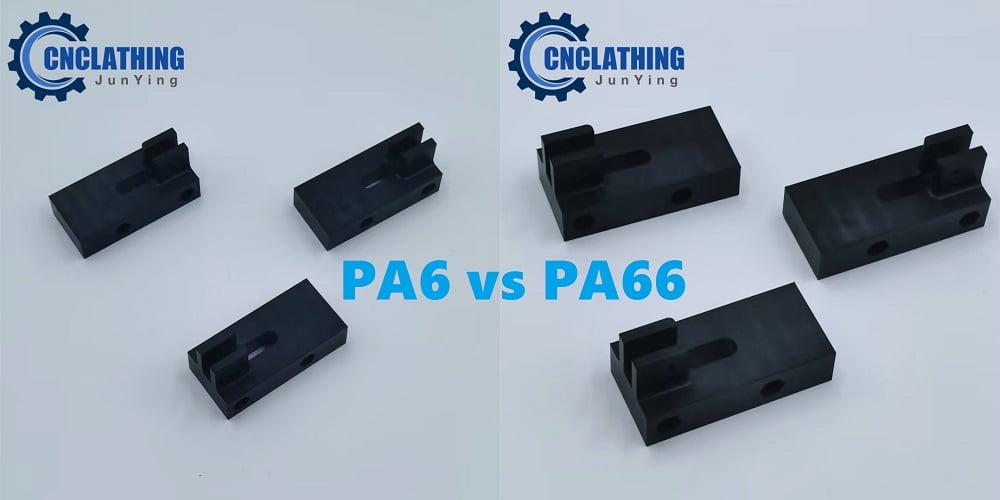
Differences Between PA6 (Nylon 6) & PA66 (Nylon 66) Plastic Material
Polyamide, in short PA, commonly known as Nylon, is a general term for high polymers with amide functional groups in the repeating units of the polymer backbone. PA is the largest in terms of production, most diverse in varieties, and widely used among the five major engineering plastics. It is commonly used in various applications, such as blends with other polymers and alloys, to meet different specific requirements, serving as substitutes for traditional materials like metal and wood.
The main varieties in Nylon are Nylon 6 (PA6) and Nylon 66 (PA66), which hold an absolute dominant position. PA6 and PA66 exhibit characteristics such as thermoplasticity, lightweight, good toughness, chemical resistance, and durability. They are widely used in textile materials such as nylon threads, curtain cords, fishing nets, conveyor belts, high-wear-resistant insulating parts for injection molding, daily necessities, and packaging films. However, there are also subtle differences between these two products. Due to their distinct characteristics, they find applications in different fields. Let’s analyze the essential differences between PA6 and PA66 from various aspects.
What is PA6 Plastic?
PA6 plastic, also known as Nylon 6 or polyamide 6, is a synthetic polymer that belongs to the family of polyamides or nylons. It is produced by polymerizing caprolactam, a cyclic amide consisting of six carbon atoms. PA6 has excellent mechanical properties, good chemical resistance, and offers a balance of strength, toughness, and flexibility.
Some key features of PA6 plastic include:
1. Strength and Stiffness: PA6 exhibits high tensile strength and stiffness, making it suitable for applications that require structural integrity.
2. Impact Resistance: It has good impact resistance, which allows it to endure sudden or repeated impact without breaking.
3. Wear and Abrasion Resistance: PA6 has good resistance to wear and abrasion, making it suitable for applications where durability is important.
4. Heat Resistance: It has a relatively high melting point, typically around 220-230°C, enabling it to withstand elevated temperatures without significant deformation.
5. Moisture Absorption: PA6 has moderate moisture absorption properties, which can affect its dimensional stability and mechanical properties. It is important to consider its moisture content during certain applications or when exposed to humid environments.
6. Chemical Resistance: PA6 exhibits good resistance to many chemicals and oils, making it suitable for applications exposed to various substances.
Due to its versatility, PA6 is used in a wide range of applications, including but not limited to automotive parts, electrical connectors, textiles, fibers, carpets, industrial components, consumer products, and packaging materials. It is a widely used engineering plastic with a well-established presence in various industries.
What is PA66 Plastic?
PA66 plastic, also known as Nylon 66 or polyamide 66, is a type of synthetic polymer from the polyamide family. It is produced by polymerizing adipic acid and hexamethylenediamine, resulting in a polymer with repeating units of six carbon atoms each. PA66 shares similarities with PA6 but has some distinct characteristics:
1. Higher Crystallinity: PA66 has a higher degree of crystallinity than PA6, accounting for improved mechanical properties such as strength, stiffness, and heat resistance.
2. Higher Melting Point: PA66 has a higher melting point compared to PA6, typically ranging from 250-260°C. This higher heat resistance allows it to retain its properties at elevated temperatures.
3. Lower Moisture Absorption: PA66 has lower moisture absorption than PA6, leading to better dimensional stability and reduced moisture-related effects on its mechanical properties.
4. Improved Mechanical Properties: Due to its higher crystallinity and greater strength, PA66 offers enhanced tensile strength, stiffness, and impact resistance compared to PA6.
5. Excellent Wear and Abrasion Resistance: PA66 demonstrates excellent resistance to wear and abrasion, making it suitable for applications where durability and resistance to friction are important.
6. Wide Range of Applications: PA66 is commonly used in automotive parts, electrical connectors, industrial components, mechanical parts, and applications that require high mechanical strength, heat resistance, and dimensional stability.
PA66 is considered a versatile engineering plastic, renowned for its robustness, toughness, and thermal stability. It finds use in a diverse range of industries and applications that demand high-performance materials.
PA6 vs PA6: Chemical Composition Difference
PA6 and PA66 have slight differences in their chemical structures. PA6 has a carbon atom count of 6, while PA66 has a carbon atom count of 6-12. This means that PA6 has a lower molecular weight and lower strength, stiffness, and hardness compared to PA66, which exhibits higher performance including strength, stiffness, and heat resistance.
PA6 vs PA6: Physical Properties Differences
PA6 Performance:
- Excellent thermal stability, high heat resistance, good dimensional stability, high surface quality, and good resistance to warping.
- Melting point: 210 – 220°C
- Decomposition temperature: >300°C
- Flash point: >400°C
- Autoignition temperature: >450°C
- Physical state: Solid particles
- Odor: Non-toxic
- Recycling: Can be recycled
- Final disposal: Soil (harmless industrial waste)
- Fire extinguishing agents: Can be extinguished using various agents (water, foam, powder, CO2, sand)
- Transportation: Non-hazardous, suitable for various modes of transportation
- EU standard: Non-hazardous
PA66 Performance:
- Excellent abrasion resistance, good high-impact resistance, and good dimensional stability.
- Melting point: 250-270°C
- Decomposition temperature: >350°C
- Flash point: >400°C
- Autoignition temperature: >450°C
- Physical state: Solid particles
- Odor: Non-toxic
- Recycling: Can be recycled
- Final disposal: Soil (harmless industrial waste)
- Fire extinguishing agents: Can be extinguished using various agents (water, foam, powder, CO2, sand)
- Transportation: Non-hazardous, suitable for various modes of transportation
- EU standard: Non-hazardous
PA6 vs PA6: Physical Properties Differences
PA6, or nylon 6, is a polymer made from hexamethylenediamine, while PA66, or nylon 66, is made from adipic acid and hexamethylenediamine. PA66 is generally harder than PA6 by 12%. PA6 and PA12 share similar chemical and physical properties. However, PA6 has a lower melting point and a wider range of process temperatures. It offers better impact resistance and solubility resistance compared to PA66, but it is more prone to absorbing moisture. Moisture absorption can affect the quality characteristics of plastic parts, so it is important to consider this when designing products with PA6.
- – PA6 engineering plastics possess high tensile strength, good impact resistance, excellent wear resistance, chemical resistance, and a low friction coefficient. The overall performance of PA6 can be enhanced through modifications with glass fiber, mineral fillers, and flame retardants. These plastics find primary applications in the automotive industry and electronics/electrical field. Glass is the most frequently added additive, while synthetic rubbers like EPDM and butyl rubber are occasionally used to improve impact resistance. Without additives, PA6 exhibits a shrinkage rate of 1% to 1.5%. Incorporating glass fiber additives reduces the shrinkage rate to 0.3% (with slightly higher shrinkage perpendicular to the process). The shrinkage of molded parts is primarily influenced by crystallinity and moisture absorption.
- – PA66 is a semi-crystalline material with a higher melting point, enabling it to maintain strength and stiffness at elevated temperatures. It offers excellent overall performance, including high strength, good rigidity, impact resistance, oil resistance, chemical corrosion resistance, wear resistance, and self-lubrication. Notably, it excels in hardness, stiffness, heat resistance, and creep resistance. PA66 is readily available and cost-effective, making it widely used in various industries such as industrial manufacturing, textiles, packaging, automotive, decoration, and engineering plastics. Given its superior strength compared to PA6, PA66 is commonly employed in industrial applications like tire cord production.
PA6 vs PA66: Usage Differences
PA6 is generally used for products in textile, packaging, home furnishings, automotive components, mechanical parts, electronic appliances, and engineering accessories.
PA66 is more widely applied in the automotive industry, instrument casings, and other products that require impact resistance and high strength, such as marine propellers, gears, rollers, pulleys, shafts, impellers in pump bodies, fan blades, high-pressure sealing rings, valve seats, gaskets, bushings, various handles, support brackets, inner layers of wire harnesses, etc.
PA6 vs PA66: Injection Molding Process Differences
When it comes to injection molding, some processing differences to consider include the following:
- – Injection temperature: The recommended injection temperature for PA6 is typically lower than that for PA66.
- – Mold design: Due to the differences in shrinkage rates and crystallinity, the mold design needs to account for these variations to ensure proper dimensions and minimize warpage.
- – Injection speed and pressure: The appropriate injection speed and pressure profiles may differ between PA6 and PA66 to optimize filling and reduce the risk of defects.
- – Drying: Proper drying of PA6 is crucial to remove moisture content and prevent issues such as splay or void formation during the molding process.
PA6 vs PA6: Price Difference
The polymerization of PA6 is a ring-opening reaction, and the input-output ratio of caprolactam and slices (or precursor) is about 1:1.03; the polymerization of PA66 is a shrinkage reaction, and the input-output ratio of 66 salt and slices (precursor) is about 1.13 -1.15. Generally speaking, due to different production processes and raw materials, the price of PA66 is higher than that of PA6. At the same time, in terms of price and performance, the application rate of PA6 is much higher than that of PA66. But among engineering plastics, PA66 has more advantages.
PA6 and PA66 are two high-performance plastics in the nylon 6 series. They have certain differences in molecular structure, melting point, glass transition temperature, impact resistance and wear resistance. Understanding these differences can help in selecting the appropriate material based on specific application needs.