Plasma nitriding is a surface treatment or modification technology with the final purpose is improving the service life of the components. It differs from other finishing methods in that it applies a glow discharge process. In this article, we’ll introduce the plasma ion nitriding principle, process, uses, materials, temperature, depth, comparison with gas nitriding, and more.
What is Plasma Nitriding & How Does It Work?
Plasma nitriding, also referred to as ion nitriding or plasma ion nitriding, is an industrial surface treatment for metals and alloys that utilizes a plasma-assisted thermochemical process to improve hardness, wear resistance, and fatigue strength. This is achieved by forming a hard layer containing compressive stresses on the material’s surface.
The process begins with the introduction of a nitrogen-rich gas mixture into a vacuum chamber, where the parts to be treated are placed. A high-voltage electrical discharge is then applied, creating a plasma of nitrogen ions that accelerate toward the metal surface. The energetic ions bombard the surface, causing nitrogen atoms to diffuse into the metal, forming a hard, wear-resistant layer.
Unlike gas nitriding which can readily form a brittle white layer, plasma nitriding guarantees the even formation of nitrides that reflect the shape of the workpiece without this issue.
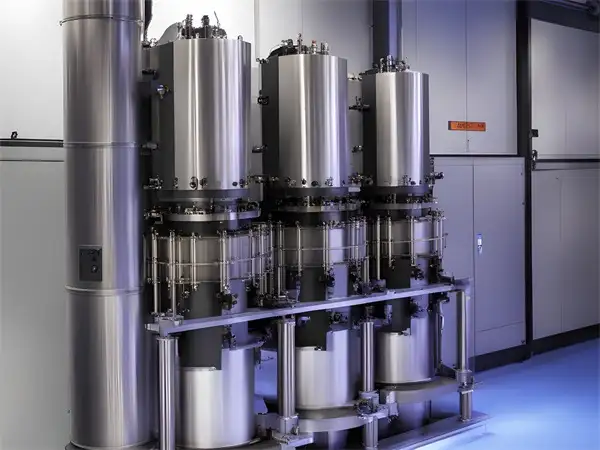
What metals can be plasma nitrided?
Ion nitriding is commonly used for various steel alloys including alloy steels, nitriding steels, and stainless steels, and now widely applied even on nonferrous materials (titanium and aluminum), for a wide range of components like gears, tools, shafts, dies, molds, and bearing rollers. Components are usually processed in their final machined dimensions, ensuring excellent dimensional stability and minimal distortion.
Can aluminum be nitrided?
Yes, you can use ion nitriding as a method for surface modification of aluminum and its alloys in order to improve their hardness and wear resistance. Ion nitriding involves bombarding the material’s surface with energetic nitrogen ions at elevated temperatures, resulting in the formation of an AlN layer that extends beyond the ballistic projected range of the ions due to thermal diffusion.
What is the hardness of plasma nitride coating?
The hardness of plasma nitride coating varies depending on the type of steel used.
- Unalloyed steels: 250-300 HV
- Low-alloy steels: 600-700 HV
- Nitriding and high-alloy steels: 800-1200 HV
- Special chromium and aluminum alloyed nitriding steels: more than 1000 HV
Plasma Nitriding Uses & Applications
– Aerospace: suitable for industrial parts that require high wear resistance and corrosion resistance, such as aircraft engine components.
– Mechanical Manufacturing: It is widely used in producing precision machine parts, critical engine components (such as crankshafts, connecting rods), bearings, and gears, and more high-end machinery parts.
– Tool and Mold: the surface hardness and wear resistance of tool steel and hard alloy molds can be greatly improved.
– Electronic and Semiconductor: Ion nitriding technology, which forms a dense nitride layer on the material surface without changing the original performance of the base material, effectively prevents external environmental corrosion. It is widely used in semiconductor packaging and integrated circuit manufacturing.
– Medical and Biomedical: mainly involves improving the surface performance of medical stainless steel, titanium alloys, and other materials, then extends the service life of medical devices such as surgical instruments and implants.
– Large-scale and complex components: Atmospheric pressure plasma nitriding can treat oversized and elongated components without vacuum equipment, even allowing for on-site treatment. It also enables localized nitriding, focusing the process only on specific areas where needed.
Plasma Nitriding Process
Plasma nitriding is a surface modification process that utilizes a high-voltage electrical discharge to create a plasma of nitrogen ions, which then react with the metal surface to form nitrides. How does the process implemented?
1. Preparation: the parts to be nitrided are thoroughly cleaned to remove any grease, oil, or dirt, and then placed in a vacuum vessel.
2. Heating: the parts are convectively heated to the required process temperature, typically between 750°F-1040°F (400°C-560°C), in an atmosphere of specialty gases, such as a mixture of nitrogen, hydrogen, and an optional carbon-based gas.
3. Ionization: applying high voltage between the workpieces and the furnace wall, which causes the process gases to activate and ionize, resulting in a corona discharge (violet glow) or plasma formation in the treatment chamber.
4. Ion Bombardment: the high voltage reacts with the positive gas ions, energizing and accelerating them toward the workpieces with high energy, creating an “ion bombardment” on the surface; the intense heat generated by this ion bombardment must be precisely controlled via very fast on-off voltage transition times or “pulse ionization.”
5. Nitride Formation: the controlled ion bombardment reacts with carbon atoms in the workpieces, forming nitrides, which eventually channel their way through the material’s grain boundaries, diffusing into the parts and leaving behind a hard, non-distorted, smooth surface.
6. Shielding (optional): a shielding stage may be included, where certain areas of the parts are covered with a metal blanket to shield them from the nitriding process.
7. Layer Formation: the creation of tailor-made layers and hardness profiles by adapting the gas mixture, such as adding a carbon-based gas; this stage can produce a range of nitrided layers, from a compound layer-free surface with low nitrogen content (up to 20 microns thick) to a compound layer with high nitrogen content and an added carbon-based gas (plasma nitro-carburation).
Note: carefully controlling several parameters within an individual process, such as voltage, gas mixture, pulse frequency, temperature, and time; unique combinations of these variables can be developed for specific applications and saved as custom settings that can be run repeatedly with absolute repeatability.
Plasma Nitriding Temperature & Depth/Thickness of Nitriding Layer
The temperature of the plasma ion nitriding needs to be controlled to get an optimal result.
Grades |
Temperature |
Max. Depth of Layer |
1045 Steel |
540 – 570°C |
0.20 mm |
5120 Steel |
540 – 570°C |
0.50 mm |
5140 Steel |
530 – 540°C |
0.50 mm |
4140 Steel |
530 – 540°C |
0.50 mm |
H12 Steel |
520 – 550°C |
0.50 mm |
4820 Steel |
520 – 540°C |
0.50 mm |
A48 Steel |
540 – 560°C |
0.30 mm |
H13 Steel |
520 – 560°C |
0.30 mm |
P20 Steel |
500 – 530°C |
0.30 mm |
M35 Steel |
500 – 540°C |
0.05 mm |
T42 Steel |
500 – 540°C |
0.05 mm |
Gas Nitriding vs Ion/Plasma Nitriding, What Are the Differences
Gas and ion plasma nitriding are often compared because they are both surface hardening processes that involve diffusing nitrogen into the surface of a metal to form a nitrided layer or case. What are the differences between them and which one should you choose?
1. Nitriding Medium
– Gas nitriding: Ammonia (NH3) or nitrogen-rich gas.
– Plasma nitriding: Pure nitrogen (N2) or other gases like hydrogen or argon.
2. Surface Conditions
– Gas nitriding: Depends more on surface cleanliness. Parts need to be thoroughly cleaned before processing.
– Plasma nitriding: Less influenced by surface contaminants. Ion bombardment helps clean the surface, eliminating the need for copper plating or masking paint.
3. Temperature Control
– Gas nitriding: Temperature control is crucial, it is usually carried out within the temperature range of 500-600 ° C for optimal results.
– Plasma nitriding: Has relatively less superior temperature control, with a broader temperature range (260°C to 600°C) viable.
4. Hardness
– Gas nitriding: Typically produces nitrided case depths of 0.1-1 mm with a surface hardness of 1000-1200 HV. The hardness gradually decreases with depth below the surface.
– Plasma nitriding: Can produce thinner yet harder nitrided layers than gas nitriding, the hardness ranges from 1100-1300 HV and remains high over a greater depth.
5. Nitriding Layer
– Gas nitriding: Forms a thick, brittle white layer, which can be a disadvantage.
– Plasma nitriding: Forms a thin, compact layer, allowing for precise control of nitrided microstructure.
6. Equipment Cost
– Gas nitriding: Relatively low equipment cost.
– Plasma nitriding: Higher equipment cost, but with more precise control and better results.
7. Production Cycle
– Gas nitriding: Longer production cycle due to slower nitriding process.
– Plasma nitriding: Faster production cycle due to faster nitriding process.
8. Surface Quality
– Gas nitriding: May require additional machining or polishing steps.
– Plasma nitriding: Produces a high-quality surface finish, with no need for additional machining or polishing.
9. Energy Efficiency
– Gas nitriding: Higher energy consumption.
– Plasma nitriding: Lower energy consumption, with reduced environmental impact.
10. Applications
– Gas nitriding: Suitable for large batch sizes, simple to operate, and widely used in various industries.
– Plasma nitriding: Suitable for high-precision applications, with precise control of nitrided microstructure, and used in industries requiring high-performance materials.
11. Environmental Impact
– Gas nitriding: May produce harmful emissions and require special handling.
– Plasma nitriding: Environmentally friendly, with minimal emissions and no special handling required.