We often hear the terms various composite materials in the field of textiles and synthetic materials, such as polyamide, nylon, and polyester fabric. These materials play an important role in modern life, whether in clothing, homewares, or industrial applications. However, for many people, understanding the subtle differences between these materials can be a bit tricky. So with this post, we break down the differences between polyamide, nylon, and polyester and help you better understand their properties, pros, cons, and scenarios where they can be used.
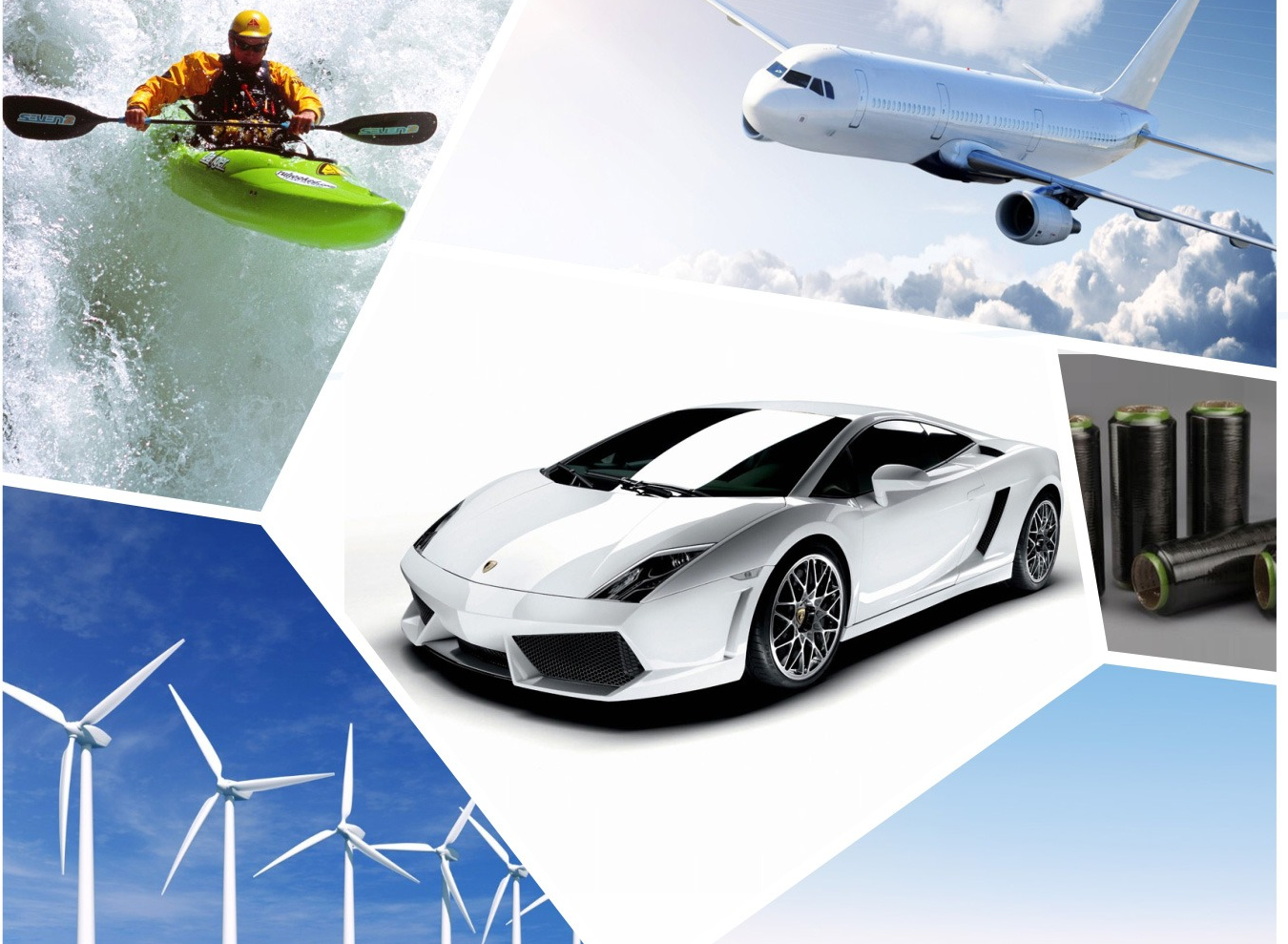
What is Polyamide?
Polyamide, often abbreviated as PA, is a synthetic polymer that belongs to the family of polymeric materials known as “nylons.” Polyamides are characterized by their strong and durable nature, making them suitable for a wide range of applications. These polymers are formed through the condensation polymerization of monomers that contain amide (-CONH-) groups, which are linked together to create long chains.
Polyamides Properties
Polyamides exhibit several desirable properties, including:
- High Strength: Polyamides are known for their excellent tensile strength, making them ideal for applications where durability and resilience are required.
- Abrasion Resistance: They have good resistance to wear and abrasion, which makes them suitable for applications like textiles and mechanical parts.
- Chemical Resistance: Polyamides can resist many chemicals, including oils, greases, and some solvents, depending on the specific type.
- Heat Resistance: Some polyamides, like nylon 6 and nylon 66, have good heat resistance, which allows them to maintain their properties at elevated temperatures.
- Flexibility: They can be engineered to have a range of flexibility, from rigid to highly flexible, depending on the specific formulation.
- Low Friction: Polyamides can exhibit low friction properties, which makes them suitable for applications like bearings and gears.
- Dielectric Properties: They have good electrical insulation properties, making them useful in electrical and electronic applications.
One of the most well-known forms of polyamide is nylon, which comes in various types like nylon 6, nylon 66, and more. Nylon is commonly used in the production of textiles, ropes, automotive parts, and various consumer goods. Polyamides find applications in industries such as automotive, aerospace, fashion, and industrial manufacturing, among others.
Polyamides Advantages & Disadvantages
Polyamides, like nylon and various other types of synthetic polymers, come with a set of advantages and disadvantages. Understanding these can help you make informed decisions about when and where to use polyamides in different applications:
Advantages of Polyamides:
- Strength and Durability: Polyamides have excellent tensile strength and are highly durable. They can withstand wear and tear, making them suitable for applications requiring longevity.
- Chemical Resistance: Many polyamides exhibit good resistance to chemicals, including oils, greases, and some solvents. This makes them suitable for use in various industrial environments.
- Low Friction: Some polyamides have low friction properties, making them useful for applications such as bearings, gears, and sliding components.
- Flexibility: Polyamides can be engineered to have a range of flexibility, from rigid to highly flexible, depending on the specific formulation and processing conditions.
- Electrical Insulation: They have good electrical insulating properties, making them valuable in electrical and electronic applications.
- Heat Resistance: Certain types of polyamides, like nylon 6/6, can withstand elevated temperatures without significant loss of properties.
- Versatility: Polyamides are used in a wide range of applications, from textiles and automotive components to consumer goods and industrial machinery.
Disadvantages of Polyamides:
- Water Absorption: Many polyamides have a tendency to absorb moisture, which can lead to dimensional changes and reduced mechanical properties. This can be a drawback in certain applications.
- UV Sensitivity: Polyamides may degrade when exposed to prolonged ultraviolet (UV) radiation, limiting their outdoor use unless treated with UV stabilizers.
- Creep: Over time, under sustained loads or high temperatures, some polyamides can exhibit creep, which is a gradual deformation that occurs even when the load is below their yield strength.
- High Processing Temperature: Polyamides often require high processing temperatures, which can limit their use in some manufacturing processes.
- Cost: While the cost of polyamides varies depending on the type and application, some high-performance polyamides can be relatively expensive.
- Recycling Challenges: The recycling of polyamides can be challenging due to their moisture absorption and the need to maintain material purity during recycling processes.
- Limited Flame Resistance: Polyamides may not be inherently flame-resistant, although flame-retardant additives can be used to improve their fire resistance.
Polyamides offer a balance of mechanical properties, chemical resistance, and versatility that makes them valuable in various industries. The choice of whether to use polyamides in a particular application should consider these advantages and disadvantages, as well as specific material formulations and processing methods to meet the desired performance requirements.
Polyamide Uses
Polyamides have various uses across different industries. Here are some common applications of polyamides:
- Textiles: Polyamides, such as nylon, are extensively used in the textile industry for manufacturing apparel, lingerie, hosiery, and activewear. They offer excellent durability, strength, and resistance to abrasion, making them suitable for applications requiring high-performance fabrics.
- Engineering Plastics: Polyamides are widely used as engineering plastics due to their mechanical properties, including high tensile strength, toughness, and heat resistance. They find applications in automotive components, electrical connectors, gears, bearings, and structural parts in various industries.
- Packaging: Polyamides play a crucial role in the packaging industry. They are commonly used for manufacturing flexible films, bags, and containers due to their excellent barrier properties, moisture resistance, and ability to maintain the freshness of packaged goods.
- Electrical Insulation: Polyamides are used as electrical insulating materials in the production of wires, cables, and connectors. They provide good dielectric properties, mechanical strength, and resistance to high temperatures, making them suitable for electrical and electronic applications.
- Sports Equipment: Polyamides, particularly nylon, are widely used in the production of sports equipment such as racquets, skis, snowboards, and protective gear. They offer a balance of durability, lightness, and impact resistance required for sports applications.
- Industrial Applications: Polyamides find utility in various industrial applications, including manufacturing conveyor belts, hoses, seals, gaskets, bearings, and gears. Their toughness, chemical resistance, and ability to withstand harsh environments make them suitable for demanding industrial processes.
It is important to note that the specific type of polyamide and its formulation can vary based on the desired properties for each application.
What is Nylon?
Nylon is a synthetic polymer and a type of polyamide. It was first developed by a team of scientists at DuPont in the 1930s and was introduced as a versatile and revolutionary material. Nylon is known for its exceptional strength, durability, and versatility, making it one of the most widely used synthetic fibers and engineering plastics in various industries.
Nylon Properties
Key characteristics and properties of nylon include:
- High Tensile Strength: Nylon is known for its excellent tensile strength, making it suitable for applications where durability and resistance to stretching or deformation are essential.
- Abrasion Resistance: It has good resistance to wear and abrasion, making it ideal for products like clothing, ropes, and mechanical parts.
- Chemical Resistance: Nylon can resist many chemicals, oils, and greases, which makes it useful in a variety of industrial applications.
- Low Friction: Nylon can exhibit low friction properties, making it suitable for components like bearings and gears.
- Flexibility: Nylon can be engineered to have a range of flexibility, from rigid and stiff to highly flexible, depending on its specific formulation.
- Moisture Absorption: Nylon has a tendency to absorb moisture from the environment, which can affect its dimensions and properties. This characteristic is both an advantage and a disadvantage depending on the application.
- Heat Resistance: While nylon can withstand moderate temperatures, it may soften or deform at high temperatures, so it’s important to consider its heat resistance in specific applications.
Nylon Advantages & Disadvantages
Nylon is a versatile synthetic polymer with various advantages and disadvantages that make it suitable for a wide range of applications. Understanding these pros and cons can help you make informed decisions about using nylon in specific contexts:
Advantages of Nylon:
- High Strength: Nylon is renowned for its exceptional tensile strength, making it one of the strongest synthetic fibers. It is commonly used in applications requiring durability and resistance to stretching or deformation.
- Abrasion Resistance: Nylon exhibits good resistance to wear and abrasion, making it suitable for products such as clothing, ropes, and mechanical parts.
- Chemical Resistance: Nylon is resistant to many chemicals, oils, and greases, which makes it valuable in various industrial applications where exposure to chemicals is a concern.
- Low Friction: Nylon has inherent lubricity and can exhibit low friction properties, making it suitable for components like bearings, gears, and sliding elements.
- Flexibility: Nylon can be engineered to have a range of flexibility, from rigid and stiff to highly flexible, depending on its specific formulation. This adaptability allows for versatility in design and application.
- Moisture Absorption: Nylon has a moderate degree of moisture absorption, which can be advantageous in certain applications, such as textiles where moisture-wicking properties are desirable.
- Thermal Stability: While nylon softens and may deform at high temperatures, it can withstand moderate temperatures, making it suitable for a wide range of applications within its temperature limits.
- Electrical Insulation: Nylon exhibits good electrical insulating properties, making it valuable in electrical and electronic applications.
Disadvantages of Nylon:
Moisture Absorption: While moisture absorption can be an advantage in some cases, it can also lead to dimensional changes and a reduction in mechanical properties, particularly in high-humidity environments.
- UV Sensitivity: Nylon can degrade when exposed to prolonged ultraviolet (UV) radiation, limiting its outdoor use unless treated with UV stabilizers or used in specific formulations.
- Creep: Over time and under sustained loads or elevated temperatures, nylon can exhibit creep, a gradual deformation that occurs even when the load is below its yield strength.
- Flame Resistance: Nylon is not inherently flame-resistant, and it may burn and melt when exposed to an open flame. Flame-retardant additives are often used to enhance its fire resistance.
- High Processing Temperature: Nylon typically requires high processing temperatures during manufacturing, which can limit its use in certain production processes.
- Cost: While the cost of nylon varies depending on the type and application, high-performance nylon grades can be relatively expensive compared to some other materials.
- Environmental Impact: Like many synthetic polymers, nylon production is associated with environmental concerns, including the consumption of non-renewable resources and the generation of waste.
Nylon offers a unique combination of strength, flexibility, and chemical resistance, making it suitable for a wide range of applications across different industries. However, its sensitivity to moisture, UV radiation, and high processing temperatures, as well as its potential for creep, should be considered when choosing it for specific uses. Proper material selection and, when necessary, the use of additives or modifications can help mitigate some of nylon’s disadvantages.
Nylon Uses
Nylon is used in a wide range of applications across various industries:
- Textiles: Nylon is commonly used in the production of clothing, hosiery, and activewear due to its strength, flexibility, and moisture-wicking properties.
- Automotive: Nylon is used in automotive components like engine parts, gears, and bushings for its durability and resistance to heat and chemicals.
- Industrial: Nylon is used in machinery and equipment components such as bearings, rollers, and conveyor belts due to its low friction and wear-resistant properties.
- Consumer Goods: It is used in everyday items like toothbrush bristles, zippers, and backpacks.
- Cables and Ropes: Nylon’s strength and durability make it an excellent choice for manufacturing ropes, fishing lines, and cables.
- Engineering Plastics: In the form of nylon resin, it is used in the production of various plastic parts, such as gears, bearings, and electrical connectors.
There are different types of nylon, such as nylon 6, nylon 66, and nylon 12, each with unique properties and suitable for specific applications. Nylon’s versatility and wide range of applications have made it a staple material in modern manufacturing and industry.
What is Polyester?
Polyester is a synthetic polymer and a type of plastic that is widely used in various industries for its versatility and desirable properties. It is known for its strength, durability, and resistance to wrinkles and shrinking, making it a popular choice for clothing, textiles, and a wide range of other applications. Polyester is made from long chains of repeating units of ester groups and is produced through a process called polymerization.
Polyester Properties
Key characteristics and properties of polyester include:
- Strength and Durability: Polyester fibers are known for their high tensile strength, making them robust and resistant to tearing and stretching.
- Wrinkle Resistance: Polyester fabrics tend to resist wrinkles and hold their shape well, which makes them low-maintenance and suitable for travel and everyday wear.
- Moisture Resistance: Polyester has low moisture absorption properties, meaning it dries quickly and resists moisture-related issues like mold and mildew growth.
- Chemical Resistance: It is generally resistant to many chemicals, which makes it suitable for applications where exposure to chemicals is a concern.
- Colorfastness: Polyester fabrics are known for retaining their color well over time, even after repeated washing and exposure to sunlight.
- Versatility: Polyester can be blended with other fibers or modified to achieve a wide range of properties, such as flame resistance, moisture-wicking, and insulation.
- Affordability: Polyester is typically less expensive than natural fibers like cotton and silk, making it a cost-effective choice for various applications.
- Recyclability: Polyester can be recycled and used to produce new polyester products, contributing to sustainability efforts.
Polyester Uses
Polyester is used in a wide array of applications across different industries:
- Textiles and Apparel: It is commonly used to make clothing, including shirts, dresses, jackets, and activewear, due to its durability and resistance to wrinkles and stains.
- Home Furnishings: Polyester is used in curtains, upholstery, bedding, and carpets due to its resistance to fading and durability.
- Technical Textiles: In industries like automotive and construction, polyester fabrics are used for applications such as seat belts, airbags, and geotextiles.
- Packaging: Polyester films are used in packaging materials, including food packaging and labels.
- Electronics: Polyester films are used in the manufacturing of capacitors and insulating materials for electrical components.
- Fiberfill: Polyester fiberfill is used as stuffing in pillows, comforters, and stuffed toys.
- Industrial Applications: Polyester can be found in various industrial applications, including conveyor belts, ropes, and filter fabrics.
- Recycled Polyester (rPET): Recycled polyester, made from post-consumer plastic bottles, is used in sustainable fashion and product manufacturing.
Polyester’s versatility, durability, and cost-effectiveness have made it a widely used material in many aspects of modern life. However, its synthetic origin and environmental concerns related to microplastic pollution and energy-intensive production have led to increased interest in sustainable alternatives and recycling efforts.
Polyester Advantages & Disadvantages
Polyester, a synthetic polymer, offers several advantages and disadvantages in its various applications. Here are some key points to consider:
Advantages of Polyester:
- Durability: Polyester is known for its exceptional durability, making it resistant to stretching, shrinking, and wrinkling. This quality makes it ideal for long-lasting clothing and textiles.
- Easy Care: Polyester is relatively easy to care for. It is machine washable, quick-drying, and generally does not require ironing.
- Moisture-Wicking: Polyester has moisture-wicking properties, meaning it draws moisture away from the skin and quickly evaporates it. This makes it suitable for athletic wear and outdoor clothing.
- Versatility: Polyester is a versatile material that can be used in a wide range of applications, including clothing, home furnishings, automotive interiors, and industrial uses. It can be blended with other fibers to enhance its properties.
- Colorfastness: Polyester has excellent color retention properties. It retains its color well, even after repeated washing and exposure to sunlight.
- Affordability: Polyester is often less expensive compared to natural fibers, making it a cost-effective choice for many consumers.
Disadvantages of Polyester:
Lack of Breathability: Polyester is not as breathable as natural fibers like cotton or linen, which can lead to a less comfortable wearing experience in hot and humid conditions.
- Synthetic Feel: Some people find that polyester has a synthetic feel and lacks the softness and natural comfort of fabrics like cotton or silk.
- Heat Sensitivity: Polyester has a lower melting point compared to some other fibers. High heat can cause it to melt, shrink, or lose shape.
- Static Build-Up: Polyester has a tendency to generate static electricity, leading to static cling and discomfort in certain situations.
- Environmental Impact: Polyester is derived from petroleum products, making it non-biodegradable. Its production process also consumes energy and produces greenhouse gas emissions.
It is worth noting that advancements in technology have led to the development of eco-friendly or recycled polyester options, which aim to reduce the environmental impact of polyester production and waste.
Differences Between Polyamide, Nylon, and Polyester
Polyamide, nylon, and polyester are all types of synthetic polymers, but they differ in terms of their chemical composition, properties, and uses. Here are the key differences between polyamide, nylon, and polyester:
Composition:
– Polyamide: Polyamide is a general term for a class of polymers with amide linkages in their molecular structure. It includes various types such as nylon, aramid, and Kevlar.
– Nylon: Nylon is a specific type of polyamide that is commonly used. It is made from the condensation polymerization of diamines and dicarboxylic acids or from a single lactam molecule.
– Polyester: Polyester is another type of synthetic polymer that contains ester functional groups in its molecular structure. It is formed through the condensation polymerization of a diol and a dicarboxylic acid.
Properties:
– Polyamide: Polyamides generally exhibit high tensile strength, good flexibility, abrasion resistance, and excellent resilience. They have a relatively high melting point and are known for their toughness.
– Nylon: Nylon is known for its exceptional strength, durability, and abrasion resistance. It has excellent resilience, good elasticity, and is lightweight. Nylon can also withstand high temperatures.
– Polyester: Polyester offers good strength and abrasion resistance. It has a low moisture absorption rate, excellent wrinkle resistance, and retains its shape well. Polyester also has good resistance to chemicals and UV radiation.
Uses:
– Polyamide: Polyamides find applications in various industries, including textiles, engineering plastics, electrical insulation, automotive components, and industrial applications that require high strength and durability.
– Nylon: Nylon is widely used in clothing, hosiery, carpets, ropes, and outdoor gear due to its strength, abrasion resistance, and moisture-wicking properties. It is also used in engineering applications and as a substitute for metal in some instances.
– Polyester: Polyester is commonly used in apparel, including clothing, sportswear, and outdoor gear due to its durability and wrinkle resistance. It is also used extensively in the textile industry for manufacturing home furnishings, carpets, and upholstery. Polyester is an important component in many industrial applications, such as packaging materials, electrical insulation, and reinforcement fibers.
Polyamide vs Polyester vs Nylon
Here’s a comparison table that highlights the differences between Polyamide, Polyester, and Nylon:
Property/Aspect | Polyamide | Nylon (Type of Polyamide) | Polyester |
---|---|---|---|
Chemical Composition | General term for polymers with amide linkages | A specific type of polyamide made from diamines and dicarboxylic acids or lactam molecules | Synthetic polymer made from diols and dicarboxylic acids (ester linkages) |
Tensile Strength | High tensile strength | Excellent tensile strength, durable | Good tensile strength, but generally lower than polyamides |
Abrasion Resistance | Excellent | Excellent | Good abrasion resistance, but slightly lower than nylon |
Heat Resistance | High, especially for nylon 6 and nylon 66 | High, withstands high temperatures | Moderate heat resistance, sensitive to high heat |
Moisture Absorption | Absorbs moisture, leading to dimensional changes | Absorbs moisture, can cause dimensional changes | Low moisture absorption, dries quickly |
Flexibility | Can be engineered for various levels of flexibility | Flexible, can range from stiff to highly flexible | Moderate flexibility, often blended for desired properties |
UV Resistance | Sensitive to UV radiation (without stabilizers) | Degrades under UV exposure (without treatment) | Better natural UV resistance than nylon or polyamide |
Chemical Resistance | Good resistance to many chemicals, oils, and greases | Good resistance to chemicals, oils, and greases | Excellent resistance to most chemicals, including acids and bases |
Wrinkle Resistance | Moderate | Moderate | High wrinkle resistance, retains shape well |
Friction (Low Friction) | Low friction properties | Low friction properties | Moderate friction properties, less smooth compared to nylon |
Dielectric Properties | Good electrical insulation | Good electrical insulation | Good electrical insulation |
Water Absorption | Absorbs moisture, leading to potential dimensional changes | Absorbs moisture (up to 8% of its weight) | Low moisture absorption, dries quickly |
Cost | Can be expensive, especially high-performance types | Generally more expensive than polyester | Generally more affordable compared to nylon and polyamide |
Recyclability | Challenging due to moisture absorption | Similar recycling challenges as polyamide | Easier to recycle, especially recycled polyester (rPET) |
Environmental Impact | Derived from petroleum, non-biodegradable | Non-biodegradable, production impacts the environment | Non-biodegradable, but can be made from recycled materials (rPET) |
Flame Resistance | Limited flame resistance | Not inherently flame-resistant, requires additives | Generally low flame resistance, but can be treated with flame retardants |
Applications | Textiles, engineering plastics, automotive components, electrical insulation | Clothing, carpets, ropes, outdoor gear, automotive parts, gears, bearings | Clothing, home furnishings, packaging, technical textiles, industrial applications |
Advantages | High strength, chemical resistance, flexibility, low friction | Exceptional durability, abrasion resistance, versatile | Wrinkle resistance, moisture-wicking, affordable, versatile |
Disadvantages | Moisture absorption, UV sensitivity, creep, high processing temperatures | Moisture absorption, UV sensitivity, creep, high processing temperatures | Lack of breathability, synthetic feel, static build-up, lower heat resistance |
These are general differences between polyamide, nylon, and polyester. It is important to note that there are various types and formulations within each category, and their specific properties and applications may vary.