Rivet nuts, also known as rivnuts, nutserts, or threaded inserts, are widely used in both industrial and DIY applications for creating strong, reliable threaded connections in thin or soft materials. From automotive to aerospace, electronics to furniture assembly, rivet nuts offer a practical solution when traditional tapping is not possible.
In many fabrication and assembly scenarios, especially with thin materials such as sheet metal or tubing, creating reliable threaded connections can be a challenge. Traditional tapping methods may not work, and welding is often impractical. This is where rivet nuts come in – offering a practical solution for adding strong threads in one-sided access areas.
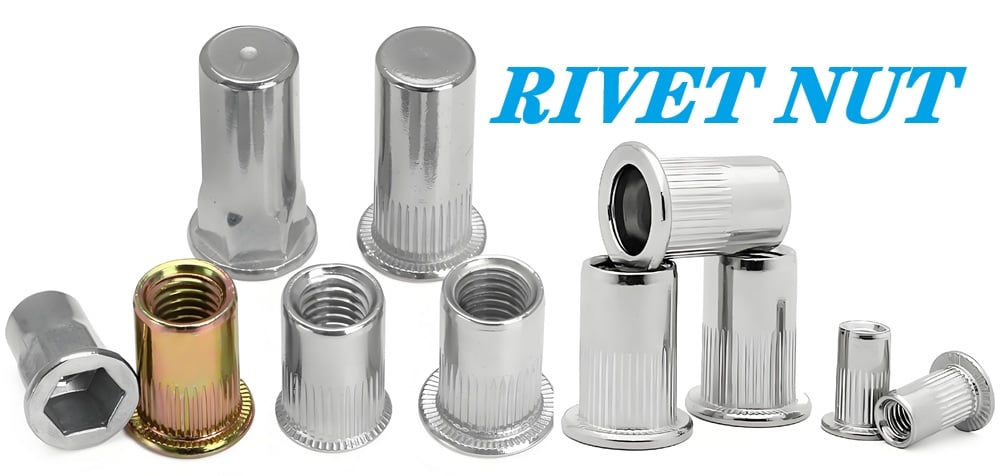
Here we are going to provide a structured overview of rivet nuts, their working principles, types, detailed size charts, including hole and drill bit sizes for accurate installation. And we will also break down rivnut installation process, removal methods, and answers to common questions for users working on professional or DIY projects.
1. What is a Rivet Nut (Rivnut)?
A rivet nut, aka rivnut, is a mechanical fastener that combines the functionality of a rivet and a nut. It is a tubular insert with internal threading that can be installed into sheet metal, plastic, or other thin materials to provide a strong, reusable threaded hole — all from one side of the workpiece. Rivet nuts referred by other names such as blind nuts, POP nuts, self-spacers, clinch nuts, and nutserts.
They are available in various sizes and materials like steel, aluminum, and stainless steel, allowing for compatibility with a wide range of applications.
How Does a Rivet Nut Work?
The installation process involves placing the rivet nut into a pre-drilled hole. A specialized tool then pulls on the internal threads while pushing against the flange, causing the body of the rivet nut to deform outward at the back side, forming a bulge that grips the base material securely.
This crimping action locks the rivet nut in place, providing a strong mechanical bond. Once installed, it acts as a fixed nut, ready to accept bolts or screws.
Rivet Nut (Rivnut) Types
Rivet nuts are available in a wide range of configurations to meet different structural, material, and installation requirements. They can be categorized by their head shape, body style, material, thread type, and other specialized features. Below are the most common types used across industries:
By Head Shape:
The shape of the rivet nut head determines how it interfaces with the surface material. Different head designs are used based on flushness, load distribution, and space constraints.
Flat Head Rivet Nuts
Flat head rivet nuts are among the most commonly used types. They feature a wide flange that provides a large bearing surface, enhancing grip strength and load distribution. These rivet nuts are typically used in general-purpose applications involving sheet metal or tubing.
Flat head rivet nuts may come in two surface textures:
- Smooth body: Suitable for low-torque applications.
- Knurled or vertical grooves: These provide better anti-rotation performance during installation, making them more reliable in high-vibration environments.
Installation typically requires only a standard round hole.
Countersunk Head Rivet Nuts
These rivet nuts have a beveled head, usually at a 90° or 120° angle, allowing the fastener to sit flush with the surface after installation. This makes them ideal for applications where a smooth surface finish is required, such as visible panels.
There are two primary variants:
- Standard Countersunk Head: Requires a pre-chamfered hole to accommodate the head.
- Small Countersunk Head: Designed for thinner materials or cases where chamfering is not feasible. This version has a smaller head diameter and thickness, reducing its surface footprint.
Both types are available with smooth or grooved finishes.
Hex Head Rivet Nuts
Hexagonal body rivet nuts are designed to fit into matching hexagonal holes, offering superior resistance to rotation under torque. These are especially useful in applications involving frequent assembly/disassembly or high-load conditions.
Variants include:
- Flat Head Hex Rivet Nuts: These are available in flat and small head options and are used with hex holes to prevent rotation. Their shape allows for higher torque resistance.
- Small Head Hex Rivet Nuts: These have a smaller flange diameter compared to flat heads, making them suitable for applications with limited surface area or aesthetic requirements.
- Full Hexagonal Body Rivet Nuts: These require a hex-shaped hole and are excellent for rotation resistance under torque. Ideal for high-torque or heavy-load connections.
- Half Hexagonal Body Rivet Nuts: These combine features of round and hex bodies. The hex portion engages with the hole to prevent rotation, while the round portion simplifies insertion.
Materials commonly used for hex rivet nuts include zinc-plated steel, 304 stainless steel, and 316 stainless steel. They are typically available in sizes ranging from M3 to M12.
By Body Types:
The shape of the rivet nut head and body plays a key role in how it interfaces with the material and functions in different applications. These features affect load-bearing capability, installation flushness, resistance to rotation, and structural strength.
Round Body Rivet Nuts (General)
The round body is a universal design used across several head types. While simple to install, it offers varying resistance to rotation depending on the surface treatment:
- Smooth Body: Basic grip; best used in rigid, non-vibrating environments.
- Knurled Body: Improved friction and anti-rotation; ideal for softer materials like aluminum or plastic.
Round body styles are widely compatible with flat, countersunk, and small head configurations.
Flat Head, Round Body Rivet Nuts
Flat head rivet nuts with round bodies are among the most commonly used types. The flat head provides a wide flange that distributes load effectively over the surface, improving pull-out strength and stability.
Body Styles:
- Smooth Round Body: Suitable for low-torque applications on materials where rotation resistance is not a major concern.
- Knurled Round Body: Features vertical grooves that improve grip and prevent rotation, especially useful in high-vibration or softer materials.
Applications: General-purpose use in sheet metal, tubing, and soft materials.
Installation: Fits into standard round holes.
Flat Head, Hexagonal Body Rivet Nuts
These rivet nuts combine the wide flange of a flat head with a full hexagonal body, offering excellent torque resistance.
Body Styles:
- Full Hex Body: Requires a matching hexagonal hole; provides superior anti-rotation performance.
- Half Hex Body: The body is partially hexagonal and partially round. Easier to install while still providing some rotation resistance.
Applications: Used in high-load or high-torque applications, including automotive and industrial assemblies.
Installation: Requires a hex-shaped hole for full locking performance.
Small Head, Hexagonal Body Rivet Nuts
This type is similar to the flat head hex rivet nut but with a smaller flange diameter, making it suitable for restricted spaces or when a lower profile is needed.
Body Styles:
- Full Hex Body
- Half Hex Body
Applications: Ideal for aesthetic surfaces or designs with limited flange clearance.
Installation: Also relies on hex-shaped holes for anti-rotation performance.
Countersunk Head, Round Body Rivet Nuts
Countersunk head rivet nuts are designed to sit flush with the surface after installation. The head features a 90° or 120° chamfer, making them suitable for visible or smooth-surface applications.
Variants:
- Standard Countersunk Head: Requires a pre-chamfered hole to accommodate the full head depth.
- Small Countersunk Head: Designed for thinner materials or when minimal chamfering is possible. It has a smaller diameter and thinner profile.
Body Styles:
- Smooth Round Body
- Knurled Round Body
Applications: Used on panels or surfaces where flush installation is required.
Installation: A chamfered hole is typically needed to seat the head properly.
Flat Head, Small Flange Rivet Nuts
These rivet nuts have a flat head with a smaller flange diameter than the standard flat head. They are suitable for compact or aesthetic applications where minimal surface coverage is needed.
Body Styles: Usually round, smooth, or knurled.
Applications: Electronics, enclosures, or tight spaces.
Installation: Requires standard round hole.
By Material:
Material selection affects the rivet nut’s strength, corrosion resistance, weight, and cost.
- Carbon Steel: Offers good strength at a low cost. Common in general industrial applications where corrosion isn’t a concern.
- Stainless Steel: Includes 304 and 316 grades. Provides excellent corrosion and heat resistance, suitable for marine, food-grade, or medical applications.
- Aluminum: Lightweight and corrosion-resistant. Used in lightweight structures or where conductivity is needed.
- Copper (Less Common): Used in specific electrical or aesthetic applications.
By Thread Type:
The internal thread determines compatibility with fastening hardware in different regions or industries.
- Metric Thread Rivet Nuts: Widely used in global applications, especially in automotive and manufacturing.
- Unified Thread (UNC/UNF): Common in North American markets.
- British Standard Thread (BSW/BSF): Used in select regional or legacy applications.
By Closure:
This classification determines whether the rivet nut is sealed at the bottom.
- Open-End Rivet Nuts: The most common type. The thread runs completely through the body, allowing bolts to pass through.
- Closed-End Rivet Nuts: The bottom is sealed to prevent the passage of fluids, debris, or contaminants. Used in electronics, sealed enclosures, or fluid systems.
By Installation Method:
The way a rivet nut is installed impacts tool selection, speed, and suitability for different environments.
- Pull-Type (Blind) Rivet Nuts: Installed using a rivet nut tool that pulls the internal mandrel, deforming the backside of the insert. Ideal for one-side (blind) installation.
- Press-Fit (Self-Clinching) Rivet Nuts: Installed by pressing into a pre-punched hole with a press machine. Requires access to both sides and is typically used in sheet metal.
- Expansion Rivet Nuts: Expand using a special installation tool to grip the inside of the hole. Suitable for high-strength or precision applications.
- Manual Pressure Rivet Nuts: Installed using a hammer and cone rod. Rarely used, but useful in field repairs or unique setups without access to tools.
2. Rivet Nut (Hole) Size Charts – Rivnut Metric & Imperial Dimensions
Rivet nut sizes refer to the specific dimensional characteristics of rivet nuts (also called rivnuts or threaded inserts), which define their fit, strength, and application compatibility. These sizes are standardized in both metric (M3 to M12) and imperial (#4-40 to 1/2″-13) thread systems and include several key dimensions beyond just thread size.
Rivet Nut Dimensions
- Thread Size (Metric & Imperial) – The internal thread size allows a bolt or screw to be inserted.
- Common metric sizes: M3, M4, M5, M6, M8, M10, M12;
- Common imperial sizes: #4-40, #6-32, #8-32, #10-24, 1/4″-20, 5/16″-18, 3/8″-16, 1/2″-13
- Hole Diameter (D) – This is the outer diameter of the rivet nut body and determines the drill hole size. Must be slightly larger than the thread’s major diameter to allow insertion and deformation.
- Flange Diameter (dk) – The flange (head) sits above the material surface and prevents the rivet nut from pulling through. Available in shapes like flat head, countersunk, and hex flange
- Flange Thickness (K) – The vertical height of the flange. Important when clearance is limited.
- Body Length (L) – The total length of the insert body, excluding the flange. It varies based on grip range and thread size.
- Grip Range (e) – The material thickness the rivet nut can securely fasten to. Always choose a rivet nut with a grip range that matches your material thickness.
- Installed Length (h) – The length of the rivet nut after installation, when the body is deformed and clamped. This affects how much space is needed behind the panel.
Standard Metric Rivet Nut Size Chart
Thread Size | Grip Range (mm) | Outer Body Dia. (mm) | Head Dia. (mm) | Body Length (mm) |
---|---|---|---|---|
M3 x 0.5 | 0.5 – 1.5 | 5.0 | 6.5 | 10.0 |
M4 x 0.7 | 0.5 – 2.0 | 6.0 | 9.0 | 11.0 |
M5 x 0.8 | 0.5 – 2.5 | 7.0 | 10.0 | 13.0 |
M6 x 1.0 | 0.5 – 3.0 | 9.0 | 12.3 | 15.0 |
M8 x 1.25 | 1.0 – 4.0 | 11.0 | 14.5 | 18.0 |
M10 x 1.5 | 1.0 – 5.0 | 13.0 | 17.0 | 21.0 |
Standard Imperial Rivet Nut Size Chart
Thread Size | Grip Range (in) | Outer Body Dia. (in) | Head Dia. (in) | Body Length (in) |
---|---|---|---|---|
1/4″-20 UNC | 0.020 – 0.120 | 0.250 | 0.345 | 0.520 |
5/16″-18 UNC | 0.030 – 0.180 | 0.340 | 0.460 | 0.600 |
3/8″-16 UNC | 0.050 – 0.250 | 0.460 | 0.580 | 0.700 |
While rivet nuts come in a variety of head styles, body types, and materials, so are also available in a wide range of thread sizes. Now, below we list the Rivnut Size Charts for the most commonly used rivet nut types in the global market now:
Flat Head Rivet Nut Size Chart (Smooth Body)
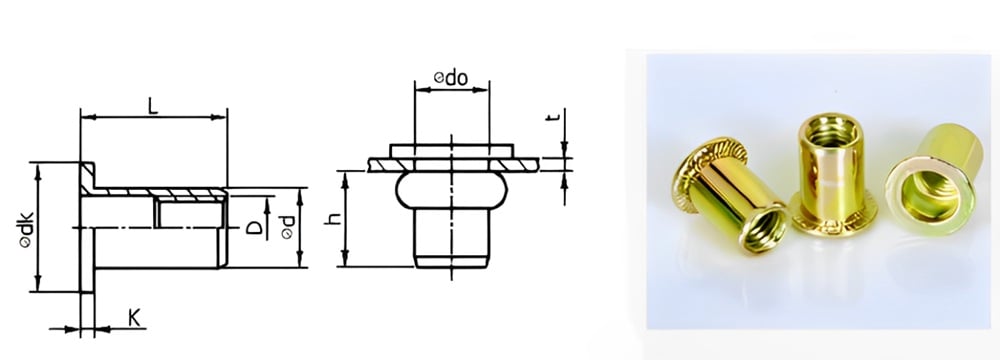
Size | Hole Dia. (D) | Head Dia. (Dk) | Head Height (K) | Body Length (L) | Grip Range (t) | Installed Length (h) | Inch Thread Equivalent |
---|---|---|---|---|---|---|---|
M3 | 5.0 mm (0.197″) | 7.0 mm | 0.8 mm | 8.5 mm | 0.5–1.5 mm | 5.0 mm | #4-40 |
M4 | 6.0 mm (0.236″) | 9.0 mm | 0.8 mm | 11.0 mm | 0.5–1.5 mm | 6.0 mm | #8-32 |
M5 | 7.0 mm (0.276″) | 10.0 mm | 1.0 mm | 13.0 mm | 0.5–2.0 mm | 7.0 mm | #10-24 / #10-32 |
M6 | 9.0 mm (0.354″) | 12.7 mm | 1.5 mm | 12.0 / 15.0 mm | 0.5–2.0 mm | 7.0 / 9.0 mm | 1/4″-20 / 1/4″-28 |
M8 | 11.0 mm (0.433″) | 15.0 mm | 1.5 mm | 17.0 mm | 0.8–2.5 mm | 10.5 mm | 5/16″-18 |
M10 | 13.0 mm (0.512″) | 17.0 mm | 1.8 mm | 19.8 / 22.8 mm | 0.8–3.0 mm | 12.5 / 13.5 mm | 3/8″-16 |
M12 | 15.0 mm (0.591″) | 18.0 mm | 1.8 mm | 22.5 mm | 0.8–3.0 mm | 13.5 mm | 1/2″-13 |
Flat Head Knurled Rivet Nut Size Chart
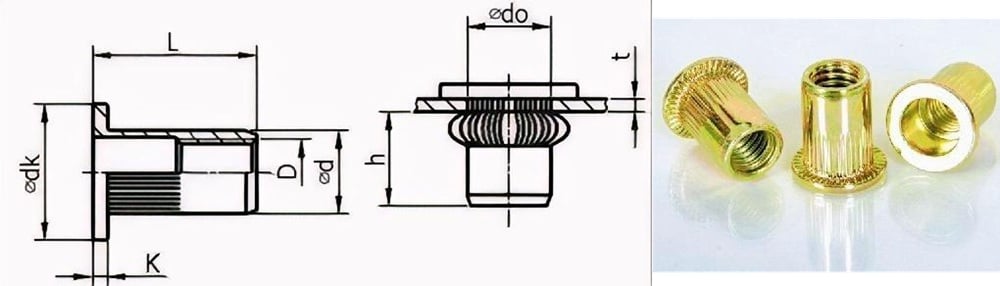
Size | Hole Dia. | Head Dia. | Head Height | Body Length | Grip Range | Installed Length | Inch Equivalent |
---|---|---|---|---|---|---|---|
M4 | 6.0 mm | 9.0 mm | 0.8 mm | 11.0 mm | 0.5–1.5 mm | 6.0 mm | #8-32 |
M5 | 7.0 / 7.6 mm | 10.0 / 10.2 mm | 1.0 mm | 13.0 / 14.0 mm | 0.5–2.0 mm | 7.0 / 7.5 mm | #10-24 / #10-32 |
M6 | 9.0 mm | 12.7 mm | 1.5 mm | 15.0 mm | 0.5–2.0 mm | 9.0 mm | 1/4″-20 |
M8 | 11.0 mm | 15.0 mm | 1.5 mm | 17.0 mm | 0.8–2.5 mm | 10.5 mm | 5/16″-18 |
M10 | 13.0 mm | 17.0 mm | 1.8 mm | 19.8 / 22.8 mm | 0.8–3.0 mm | 12.5 / 13.5 mm | 3/8″-16 |
M12 | 15.0 mm | 19.0 mm | 1.8 mm | 22.5 mm | 0.8–3.0 mm | 13.5 mm | 1/2″-13 |
Flat Head Hex Rivet Nut Size Chart
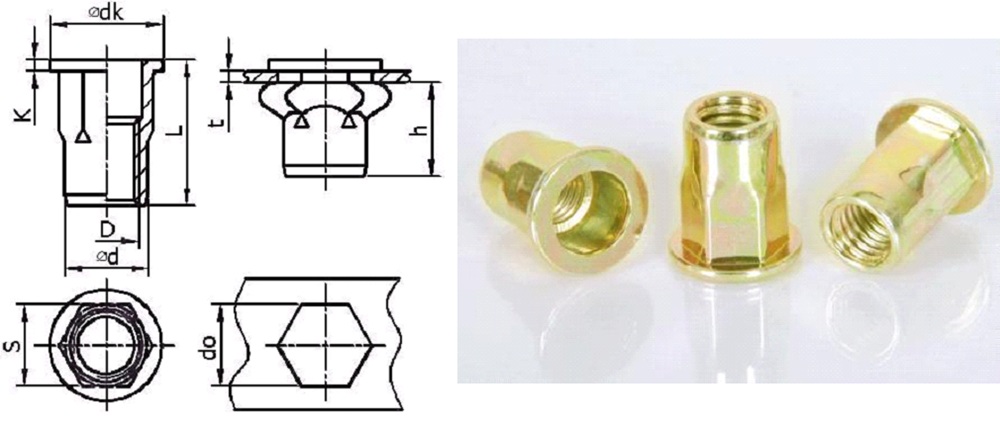
Size | Hole Dia. | Head Dia. | Head Height | Body Length | Grip Range | Installed Length | Inch Equivalent |
---|---|---|---|---|---|---|---|
M4 | 6.0 mm | 9.0 mm | 0.8 mm | 11.0 mm | 0.5–1.5 mm | 6.0 mm | #8-32 |
M5 | 7.0 mm | 10.0 mm | 1.0 mm | 13.0 mm | 0.5–1.5 mm | 7.5 mm | #10-24 |
M6 | 9.0 mm | 12.0 mm | 1.0 mm | 12.0 / 14.5 mm | 0.5–2.0 mm | 6.0 / 8.0 mm | 1/4″-20 |
M8 | 11.0 mm | 15.0 mm | 1.5 mm | 18.0 mm | 0.8–2.5 mm | 10.5 mm | 5/16″-18 |
M10 | 12.0 / 13.0 mm | 17.0 / 18.0 mm | 1.8 mm | 19.8 / 22.8 mm | 0.8–3.0 mm | 12.5 / 15.0 mm | 3/8″-16 |
M12 | 15.0 mm | 19.0 mm | 1.8 mm | 24.3 mm | 1.0–3.5 mm | 16.5 mm | 1/2″-13 |
Flat Head Inside & Outside Hex Rivet Nut Size Chart (Full & Half)
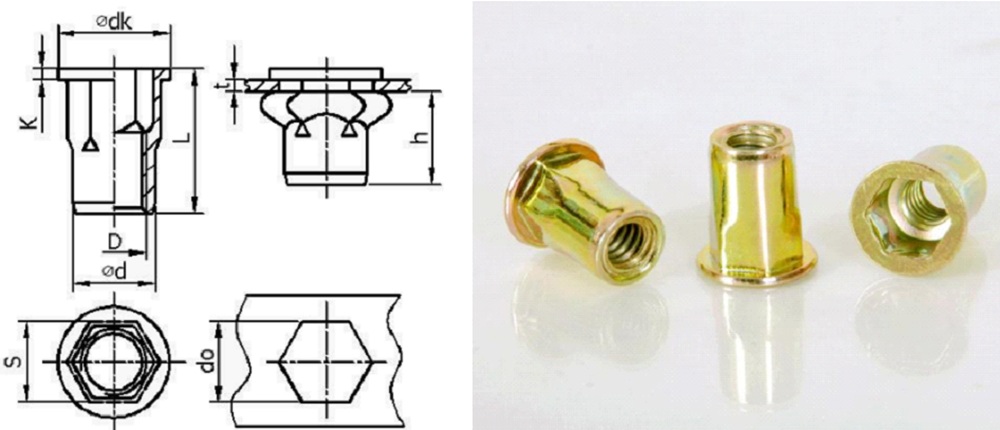
Size | Hole Dia. | Head Dia. | Head Height | Body Length | Grip Range | Installed Length | Inch Equivalent |
---|---|---|---|---|---|---|---|
M4 | 6.0 mm | 9.0 mm | 0.8 mm | 11.0 mm | 0.5–1.5 mm | 6.0 mm | #8-32 |
M5 | 7.0 mm | 10.0 mm | 1.0 mm | 13.0 mm | 0.5–1.5 mm | 8.0 mm | #10-24 |
M6 | 9.0 / 9.6 mm | 13.0 mm | 1.0 / 1.5 mm | 15.0 mm | 0.5–2.0 mm | 9.0 mm | 1/4″-20 |
M8 | 11.0 mm | 15.0 mm | 1.5 mm | 18.0 mm | 0.8–2.5 mm | 10.5 mm | 5/16″-18 |
M10 | 13.0 mm | 14.9 mm | 0.8 mm | 19.8 mm | 0.8–3.0 mm | 15.0 mm | 3/8″-16 |
Countersunk Head Rivet Nut Size Chart
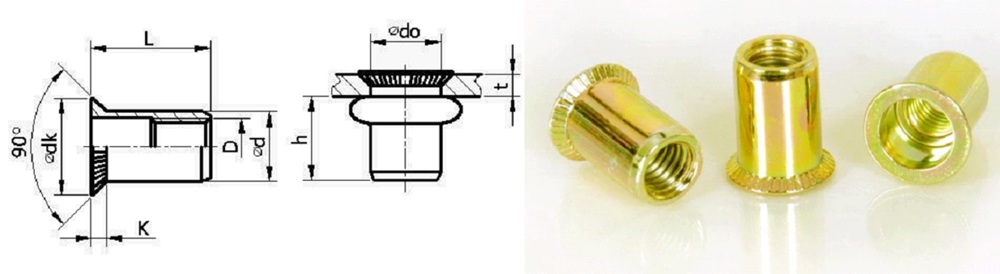
Size | Hole Dia. | Head Dia. | Head Height | Body Length | Grip Range | Installed Length | Inch Equivalent |
---|---|---|---|---|---|---|---|
M3 | 5.0 mm | 8.0 mm | 1.5 mm | 9.5 mm | 1.6–2.5 mm | 4.5 mm | #4-40 |
M4 | 6.0 mm | 9.0 mm | 1.5 mm | 11.0 mm | 1.6–2.5 mm | 6.0 mm | #8-32 |
M5 | 7.0 mm | 10.0 mm | 1.5 mm | 14.0 mm | 1.6–3.5 mm | 8.5 mm | #10-24 |
M6 | 9.0 mm | 12.0 mm | 1.5 mm | 15.0 mm | 1.6–3.5 mm | 9.0 mm | 1/4″-20 |
M8 | 11.0 mm | 14.0 mm | 1.7 mm | 17.0 mm | 1.6–4.5 mm | 10.5 mm | 5/16″-18 |
M10 | 13.0 mm | 16.0 mm | 1.7 mm | 21.0 mm | 2.0–5.0 mm | 13.0 mm | 3/8″-16 |
M12 | 15.0 mm | 18.0 mm | 1.7 mm | 22.5 mm | 2.0–5.0 mm | 14.5 mm | 1/2″-13 |
Blind Rivet Nut Size Chart (Metric & Imperial)
Blind rivet nuts (also called rivnuts or threaded inserts) are used to install strong, load-bearing threads in thin materials. Below is the standard size chart for open-type blind rivet nuts, based on metric and imperial drill diameters, grip ranges, and performance metrics.
Open-Type Blind Rivet Nut Size Chart
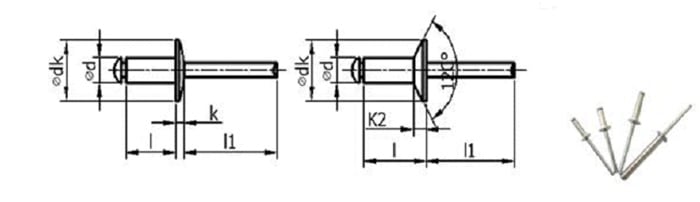
Rivet Ø (d) | Drill Hole Ø (Do) | Grip Range (mm) | Flange Ø (dk) | Flange Thick (k) | Body Length (l1) | Tensile Strength (N) | Shear Strength (N) | Imperial Equiv. |
---|---|---|---|---|---|---|---|---|
Φ3.2 mm | 3.3 mm | 0.5–1.0 to 11.0–13.0 | 6.0 mm | 1.2–1.4 mm | 6.0–17.0 mm | 1200–2500 | 850–2000 | ~1/8″ |
Φ4.0 mm | 4.1 mm | 0.5–2.0 to 9.0–11.0 | 8.0 mm | 1.4–1.7 mm | 7.0–16.0 mm | 1860–4000 | 1350–3000 | ~5/32″ |
Φ4.8 mm | 4.9 mm | 0.5–1.0 to 18.0–20.0 | 9.5 mm | 1.6–2.0 mm | 6.0–25.0 mm | 2840–5500 | 1950–4500 | ~3/16″ |
Φ6.4 mm | 6.5 mm | 1.0–3.0 to 17.0–19.0 | 12.7 mm | 2.2–2.7 mm | 10.0–26.0 mm | up to 7800 | up to 9500 | 1/4″ |
Sealed-Type Blind Rivet Nut Size Chart
Sealed blind rivets are designed to prevent liquid, gas, or dust penetration.
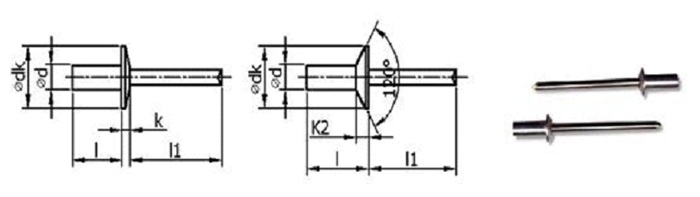
Rivet Ø (d) | Drill Hole Ø (Do) | Grip Range (mm) | Flange Ø (dk) | Flange Thick (k) | Body Length (l1) | Tensile Strength (N) | Shear Strength (N) | Imperial Equiv. |
---|---|---|---|---|---|---|---|---|
Φ3.2 mm | 3.3 mm | 0.5–1.0 to 11.0–13.0 | 6.0 mm | 1.2–1.4 mm | 6.0–17.0 mm | 490–1240 | 450–1070 | ~1/8″ |
Φ4.0 mm | 4.1 mm | 0.5–1.5 to 11.5–13.5 | 8.0 mm | 1.4–1.7 mm | 6.0–18.0 mm | 712–2130 | 580–1560 | ~5/32″ |
Φ4.8 mm | 4.9 mm | 0.5–1.0 to 18.0–20.0 | 9.5 mm | 1.6–2.0 mm | 6.0–25.0 mm | 1120–3070 | 900–2230 | ~3/16″ |
Φ5.0 mm | 5.1 mm | 1.0–3.0 to 23.0–25.0 | 9.5 mm | 2.0 mm | 8.0–30.0 mm | — / 3500 | — / 2420 | ~13/64″ |
Φ6.4 mm | 6.5 mm | 1.0–3.0 to 11.0–13.0 | 12.7 mm | 2.7 mm | 10.0–20.0 mm | — / 5000 | — / 3950 | 1/4″ |
3. Rivet Nut (Rivnut) Drill Bit Size Chart
The hole diameter is the key for proper Rivnut installation. It must match the rivet nut’s outer diameter with minimal clearance. To prepare the installation hole, use a drill bit that matches the recommended hole size.
How to Determine & Calculate the Drill Hole Sizes for Rivet Nuts?
Here’s how to accurately calculate the three key dimensions: hole diameter, hole pitch (spacing), and hole depth:
1. Drill Hole Diameter
The drill hole diameter refers to the diameter of the hole that must be drilled into the base material. This diameter is typically slightly larger than the thread’s major diameter, allowing the rivet nut to fit snugly and deform properly during installation.
Formula: Hole Diameter ≈ Thread Outer Diameter + 0.3–0.5 mm
Example (M6 rivet nut):
- M6 thread outer diameter = 6.0 mm
- Recommended drill bit size = 6.4 mm
This allows for proper insertion and deformation of the rivet nut during compression.
2. Hole Spacing (Pitch)
Hole pitch is the center-to-center spacing between two rivet nuts. It depends on the thread size and base material thickness.
A commonly used formula is: Hole Pitch = 1.5 × Thread Diameter
Example (M6 in 1.0 mm aluminum plate):
- D = 6.0 mm
- Hole Pitch = 1.5 × 6.0 = 9.0 mm
- Note: For thicker plates, increase spacing slightly to ensure proper deformation and fastener integrity.
3. Hole Depth
Hole depth should accommodate the entire rivet nut body, plus space for the mandrel and a safety clearance.
Formula: Hole Depth = Nut Length (L1) + Mandrel Length (L2) + Clearance (S)
Example (M6 rivet nut with 8 mm length, 15 mm mandrel):
- L1 = 8.0 mm
- L2 = 15.0 mm (1.5×L1 recommended)
- S = 1.0 mm (clearance)
- Total Hole Depth = 8.0 + 15.0 + 1.0 = 24.0 mm
Rivnut Drill Bit Size Charts (Metric & Imperial)
Below are the recommended drill bit sizes for different rivet nut types and thread sizes. Always refer to manufacturer specs for special body types or knurled/hex bodies.
Metric Rivet Nut Drill Size Chart
Thread Size | Thread Ø (mm) | Drill Hole Size (mm) | Common Use |
---|---|---|---|
M3 | 3.0 mm | 5.0 mm | Electronics, light-duty |
M4 | 4.0 mm | 6.0 mm | Sheet metal, small appliances |
M5 | 5.0 mm | 7.0 mm | Furniture, metal enclosures |
M6 | 6.0 mm | 6.3–6.5 mm | Automotive, panels |
M8 | 8.0 mm | 10.8–11.0 mm | Industrial, structural |
M10 | 10.0 mm | 12.8–13.0 mm | Structural, heavy-duty |
M12 | 12.0 mm | 14.8–15.0 mm | Structural steel, large panels |
Imperial Rivet Nut Drill Size Chart
Thread Size | Thread Ø (inch) | Drill Hole Size (inch) | Drill Bit No. |
---|---|---|---|
#4-40 | 0.112″ | 0.191″ (4.85 mm) | #11 |
#6-32 | 0.138″ | 0.219″ (5.56 mm) | #2 |
#8-32 | 0.164″ | 0.250″ (6.35 mm) | 1/4″ |
#10-24 | 0.190″ | 0.281″ (7.14 mm) | 9/32″ |
1/4″-20 | 0.250″ | 0.343″ (8.7 mm) | 11/32″ |
5/16″-18 | 0.312″ | 0.437″ (11.1 mm) | 7/16″ |
3/8″-16 | 0.375″ | 0.500″ (12.7 mm) | 1/2″ |
1/2″-13 | 0.500″ | 0.625″ (15.9 mm) | 5/8″ |
4. Rivnut Installation – How to Install a Rivet Nut (Nutsert)?
Rivet nuts (also known as nutserts, threaded inserts, or blind rivet nuts) are a game-changing solution when you need to create strong, reusable threads in sheet metal, alloy, or even plastic – especially when you can only access one side of the material. Here, we’ll walk you through how to install a rivet nut using both a dedicated tool and offer tips on the manual installation method.
Rivet Nut Installation Tools
Tools recommended for accuracy and durability:
- Rivet nut tool (long handle preferred for leverage)
- Correct-size die and mandrel
- Drill and drill bits
- Rivet nuts (nutserts)
- Caliper (optional, for precise measurement)
Step-by-Step Installation Instructions
Step 1: Choose Your Bolt and Rivet Nut Size
Start by selecting the bolt size you intend to use. Then, choose a rivet nut that matches it. This ensures compatibility and avoids mismatching threads.
Step 2: Drill the Correct Hole Size
Use a drill bit that matches the outer body diameter of the rivet nut. Refer to a rivet nut drill size chart for exact specs.
Example: For an M8 rivet nut, use a 11.0 mm drill bit.
Step 3: Prepare the Work Surface
Make sure the surface is flat and clean. A flat surface ensures the collar of the rivet nut sits flush, which is essential for secure installation.
Step 4: Load the Rivet Nut Tool
- Select the correct mandrel and nosepiece for your rivet nut size.
- Attach the mandrel and locking collar to the tool.
- Thread the rivet nut onto the mandrel until it sits tight against the collar.
Step 5: Insert the Rivet Nut into the Hole
Place the rivet nut into the pre-drilled hole. Ensure the flange is flush with the surface.
Step 6: Compress the Rivet Nut
Squeeze the handles of the tool. This will pull the mandrel and compress the back of the nutsert, forming a bulge that locks it against the material.
You’ll feel resistance and then a “set” once the nutsert is fully compressed.
Step 7: Remove the Tool
Unscrew or release the tool from the rivet nut. You should now have a secure, threaded insert.
Step 8: Test with a Bolt
Thread your bolt into the installed rivet nut to confirm proper installation.
How to Install a Rivet Nut Without a Tool
If you don’t have a rivet nut tool, you can use this DIY method:
What You Need:
- A bolt
- A nut
- Washers
Steps:
- Thread the nut and washers onto the bolt.
- Insert the rivet nut into the hole.
- Thread the bolt into the nutsert.
- Hold the bolt with a wrench and tighten the nut against the washers.
- The nut compresses the rivet nut, locking it in place.
- Remove the bolt and nut — your rivet nut is now installed.
5. FAQs about Rivet Nuts & Rivnut Sizes
Here are more most commonly asked questions to undertand how to properly use, size, and maintain rivet nuts:
How to Use & Install a Rivet Nut?
1. Preparation – Select the correct rivet nut and bolt size. Drill a hole using the correct drill bit.
2. Placement – Insert the rivet nut into the hole with the flange flush against the material.
3. Tool Setup – Attach the rivet nut to the mandrel of the rivet tool. Squeeze the handles to compress the rivet nut and form the bulge at the back.
4. Completion – Unscrew the tool. Insert the bolt to check the thread engagement.
How to Remove a Rivet Nut?
There are two simple ways to remove a rivet nut:
Method 1: Standard Drill Bit – Use a slightly larger drill bit than the hole size. Drill out the center until the flange detaches.
Method 2: Step Drill Bit – Use a step drill bit to gradually remove the flange without damaging the material. Caution: The rivet nut may become hot during removal. Use gloves or allow it to cool before touching.
Is a rivet nut the same as a threaded insert?
Yes, rivet nuts are a type of threaded insert specifically designed for blind installations in thin materials.
Can I install a rivet nut without a proper tool?
Yes, it’s possible using a bolt, nut, and washers, but the results may not be as consistent.
How do I choose the right hole size?
Check the manufacturer’s chart or measure the outer diameter of the rivet nut. The hole should allow a snug fit.
Can rivet nuts be reused?
The nut remains in place, and the internal threads can be reused unless damaged.