Are you familiar with sheet metal fabrication? Sheet metal stock is made from a common flat sheet. and the process of blanking or cutting is when you profiling the unfolded part to create a flat pattern. when the part is formed, then it can be inserted, welded, partly marked, or have some surface treatments. here at CNCLATHING, we want to help you understand why should you use sheet metal, and knowing the tools of the trade will help you be mindful of your design along the way, then we will go into specific design guidelines for sheet metal. so without further ado, let talk about sheet metal!
The Benefits of Sheet Metal Fabrication
There’s a lot of advantages to sheet metal fabrication. when we’re talking about volume, we can get extremely affordable, high-quality parts of it, it scales to volume production even with the most common best practice approaches to sheet metal, not the super high-end fancy type volume production, but you’ll see prices reduce greatly by using the normal processes that you’d see in the shops across the nation. aluminum is a cheaper material and the first super material. it has an amazing high strength-to-weight ratio, that’s one of the reasons that we have such fantastic aircraft. you can leverage that power in your designs to make sheet metal parts. it’s also affected for very large parts. you can make the outside skin of a Boeing aircraft or you can make a small little bracket.
Sheet Metal Standard Gauges Chart
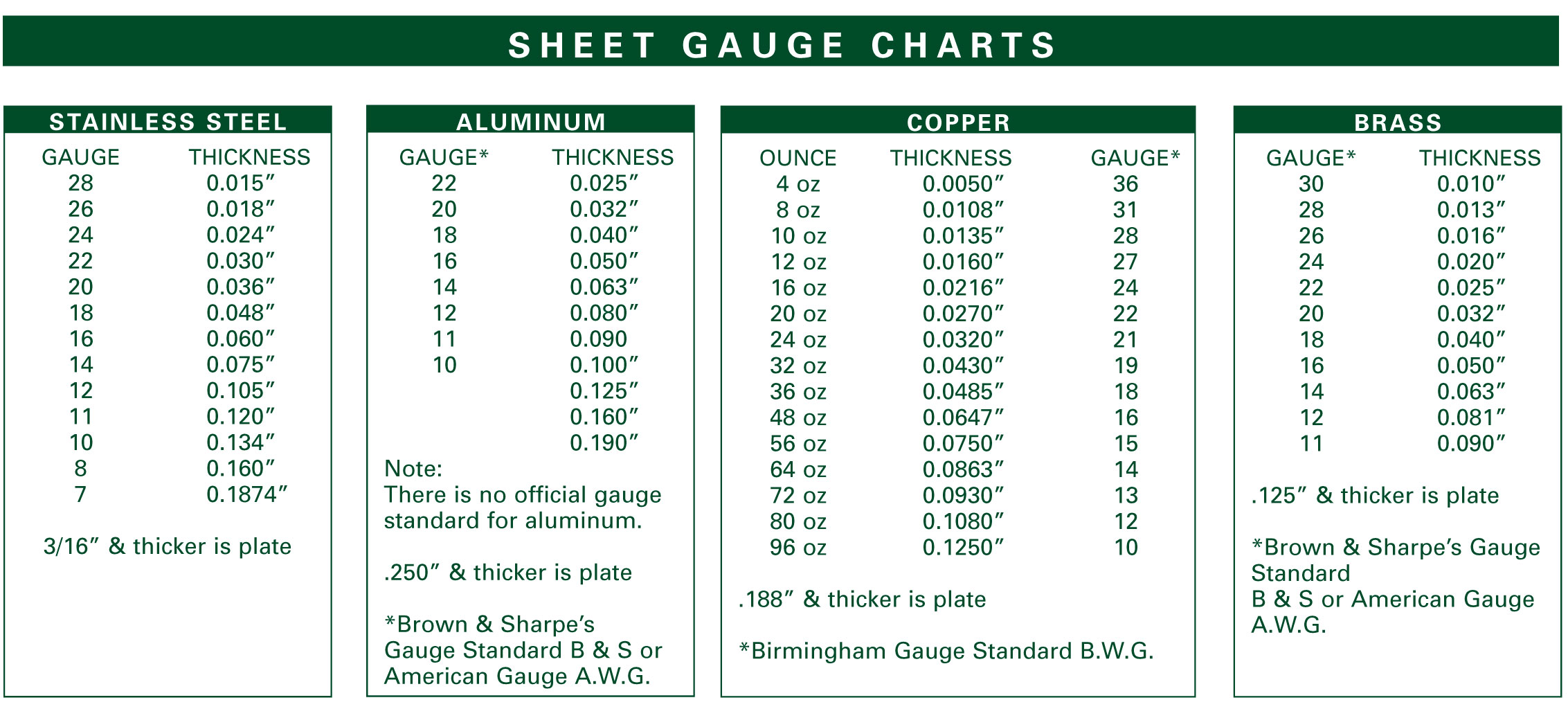
Another nice thing about sheet metal is that we have a wide variety of materials to choose from, each of those materials has its own alloys blends and options. but you can see the chart above, some of the materials also come in fractional sizes in the states. if you’re overseas, particularly aluminum steels can come in fractional sizes, if you’re in Europe, that would be in millimeters.
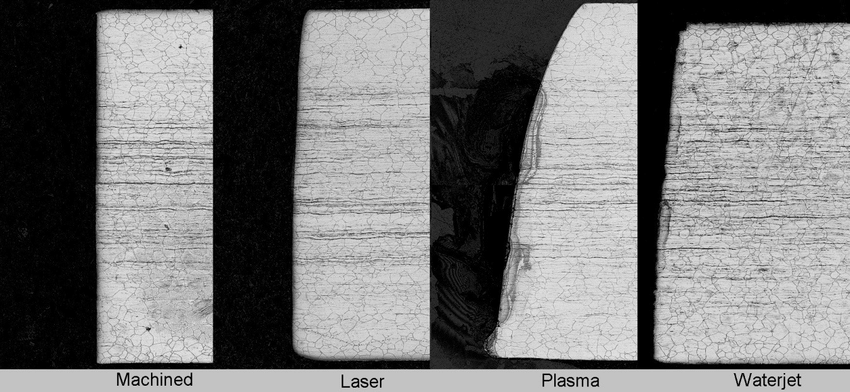
Flat Pattern Prep – Water Jet, Laser Cutting & Plasma Cutting
There are there major cutting platforms – water jet, laser cutting, and plasma cutting. laser cutting or water jet would be seen more moving towards the bigger sheet because handling is the labor, that’s where the cost is. the machines are so fast that the bigger the sheet the better. if you want the wide variety of shops to be able to pull your part, 4*10 is good. when we talk about the flat pattern, another one of those packages fusion that allows you to create sheet metal then unfold it flat, it’s created a flat pattern, then we can use a variety of different processes to create that pattern. depending on which one you choose, it can do some or all of those features. there are trade-offs in everything, that’s why there are different machines or shops like a cape on why we have one of each of these machines. because they all have their efficiencies, good and bad qualities. The water jet has pretty good accuracy, fairly slow, but it can cut anything. people always ask when they see the water jet, how thick can it cut? the answer is pretty much anything. you can squeeze underneath that head, that’s what it’s going to cut, but reasonably it can cut very thick pages in comparison to the other processes. laser cutting is probably the most common process that you’re seeing right now because it’s an extremely high accuracy, the costs of fiber lasers have come down, the speed has gone up. those are extremely highly accurate features. it’s very fast, so we can cut sixteenth-inch steel at a thousand inches a minute for reference. the head moves quickly, it would scare you the first time you see it. you can cut thinner gauges of materials down below. we can’t avoid foil cutting, but you can cut very thin things. we can cut up to one inch thick steel, but you can only cut metal. it’s best for metals. plasma cutting is like a blend of the two, and in-between. it has good accuracy, maybe in some ways not as good as water jet, it puts a lot of heat into the part, you may have to worry about distortion possibly. it has a higher speed, you can do thick gauges metal only.