Springs are essential mechanical components used in a wide variety of applications, from everyday devices to critical industrial machinery. The materials used to manufacture springs play an important role in determining their performance, durability, cost, and resistance to environmental factors. The selection of spring materials depends on the intended application, environmental conditions, and required mechanical properties. Below is a detailed overview of the materials used for springs, materials used for springs, which include not only metal wire but also rubber, plastic, and even fluid-based springs that utilize gas or oil. We will go over the grades, composition, properties, and common uses for each type of spring material, and talk about important considerations for choosing the appropriate material.
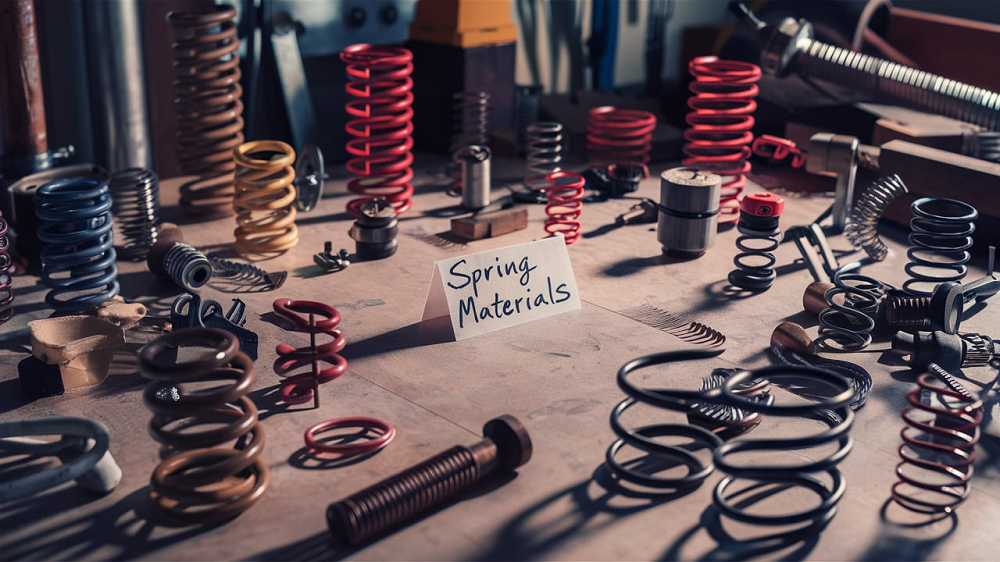
Spring Material Types: Composition, Properties, Grades, and Uses
1. Metal Spring Materials
Metal springs are the most common type, known for their strength and durability. They are typically made from steel wires, such as hard steel or piano wire, but stainless steel and other alloys are also widely used. The following sections detail the primary types of metal materials used in springs.
1.1 Music Wire (SWP-A, SWP-B, SWP-V)
Piano wire is a high-quality steel wire commonly used in precision applications where high reliability is required. It is cold-drawn and heat-treated to achieve its properties. Piano wire is widely used in the automotive industry for components like valve springs and brake springs.
- Grades: Piano wire is classified into three types: A, B, and V.
- SWP-A: Known for its high allowable stress and excellent fatigue resistance, making it ideal for springs under repeated loads.
- SWP-B: Offers higher tensile strength and sag resistance than SWP-A but has slightly lower ductility, making it suitable for springs that require high tensile strength.
- SWP-V: Used for valve springs in engines, especially where high fatigue life is crucial.
Piano Wire Spring Material Composition, Strength, Properties, Application
Grade | Composition | Tensile Strength (N/mm²) | Key Properties | Common Uses |
---|---|---|---|---|
SWP-A (Piano Wire) | C: 0.80–0.85%, Si: 0.12–0.32%, Mn: 0.30–0.60%, P: ≤0.025%, S: ≤0.025%, Cu: ≤0.20% | 2890–3190 (0.08mm) 2060–2260 (1.0mm) 1420–1570 (10.0mm) | – High allowable stress – Excellent fatigue resistance – Good for repeated load applications | – Clutch springs – Brake springs – Precision instruments – High-end mechanical springs |
SWP-B (Piano Wire) | C: 0.80–0.85%, Si: 0.12–0.32%, Mn: 0.30–0.60%, P: ≤0.025%, S: ≤0.025%, Cu: ≤0.20% | 3190–3480 (0.08mm) 2260–2450 (1.0mm) – (10.0mm) | – Higher tensile strength than SWP-A – Good sag resistance – Slightly lower ductility than SWP-A | – Springs requiring high tensile strength <br> – Automotive components <br> – Heavy-duty spring applications |
SWP-V (Piano Wire) | C: 0.80–0.85%, Si: 0.12–0.32%, Mn: 0.30–0.60%, P: ≤0.025%, S: ≤0.025%, Cu: ≤0.20% | Not specified | – Optimized for very high fatigue life – Used for high-cycle applications | – Valve springs in engines – Springs for high-cycle and high-reliability applications (e.g., automotive, agricultural machinery) |
1.2 Hard Steel Wire (SW-A, SW-B, SW-C)
Hard steel wire is a versatile material used in a wide range of everyday products. It is more cost-effective compared to piano wire and is often used in less demanding applications. Hard steel wire is heat-treated and cold-drawn to achieve its final properties.
- Grades: Hard steel wire is available in three grades—SW-A, SW-B, and SW-C—based on their tensile strength.
- SW-A: Commonly used in items like wire mesh, fences, and seat frames.
- SW-B and SW-C: These grades are used in springs for products like safety pins, switches, scales, bed springs, and toys.
Spring Hard Steel Wire Material Composition, Strength, Properties, Application
Grade | Composition | Tensile Strength (N/mm²) | Key Properties | Common Uses |
---|---|---|---|---|
SW-A (Hard Steel Wire) | C: 0.79–0.86%, Si: 0.15–0.35%, Mn: 0.30–0.60%, P: ≤0.030%, S: ≤0.030% | 2450–2790 (0.08mm) 1720–1960 (1.0mm) 1130–1320 (10.0mm) | – General-purpose wire – Lower strength compared to SW-B and SW- – Cost-effective | – Wire mesh – Fences – Seat frames – Basic structural components |
SW-B (Hard Steel Wire) | C: 0.79–0.86%, Si: 0.15–0.35%, Mn: 0.30–0.60%, P: ≤0.030%, S: ≤0.030% | 2790–3140 (0.08mm) 1960–2210 (1.0mm) 1320–1520 (10.0mm) | – Higher tensile strength than SW-A – Good balance of strength and ductility – Widely used for springs | – Safety pin springs – Switch springs – Scale springs – Chair and bed springs |
SW-C (Hard Steel Wire) | C: 0.79–0.86%, Si: 0.15–0.35%, Mn: 0.30–0.60%, P: ≤0.030%, S: ≤0.030% | 3140–3480 (0.08mm) 2210–2500 (1.0mm) 1320–1520 (10.0mm) | – Highest tensile strength among hard steel grades – Great for high-stress applications – Lower ductility | – Springs for toys – Shutter springs – Bed springs – High-stress mechanical springs |
1.3 Stainless Steel Wire (SUS304, SUS316, SUS631)
Stainless steel is widely used in springs where corrosion resistance and durability under high temperatures are required. There are three main types of stainless steel commonly used in spring manufacturing:
- SUS304-WPB: The most commonly used stainless steel spring material, known for its corrosion resistance and mechanical properties.
- SUS316-WPA: Offers superior corrosion resistance compared to SUS304, making it suitable for more demanding environments.
- SUS631J1-WPC: A precipitation-hardening stainless steel used in high-temperature applications, with excellent heat resistance up to 350°C.Applications: Marine equipment, food processing machinery, and high-temperature environments.
Spring Stainless Steel Wire Material Composition, Strength, Properties, Application
Grade | Composition | Key Properties | Common Uses | Temperature Resistance |
---|---|---|---|---|
SUS304-WPB | C: ≤0.08%, Si: ≤1.00%, Mn: ≤2.00%, Ni: 8.00–10.50%, Cr: 18.00–20.00%, Mo: – | – Most commonly used stainless steel for springs – Excellent corrosion resistance – Good mechanical properties | – Household appliances – Springs in food processing equipment – Automotive components | Up to 290°C |
SUS316-WPA | C: ≤0.08%, Si: ≤1.00%, Mn: ≤2.00%, Ni: 10.00–14.00%, Cr: 16.00–18.00%, Mo: 2.00–3.00% | – Superior corrosion resistance compared to SUS304 – Good resistance in chloride environments – Non-magnetic | – Marine equipment – Chemical processing machinery – Medical devices | Up to 290°C |
SUS631J1-WPC | C: ≤0.09%, Si: ≤1.00%, Mn: ≤1.00%, Ni: 7.00–8.50%, Cr: 16.00–18.00%, Mo: – | – Precipitation-hardened stainless steel – Excellent strength and heat resistance – High fatigue resistance | – High-temperature applications – Engine components – High-stress environments | Up to 350°C |
1.4 Oil-Tempered Wire
Oil-tempered wire is a high-strength material often used for larger springs or applications requiring excellent fatigue resistance. The material is processed by oil quenching and tempering, which gives it high yield strength and elasticity. Oil-tempered wire is commonly used in suspension springs and industrial machinery. Here are main oil-tempered wire types to used for manufacturing springs:
- Carbon Steel Oil-Tempered Wire: A cost-effective option with good strength and elasticity, suitable for general-purpose heavy-duty springs like those used in automotive suspensions and industrial machinery.
- Silicon-Chromium (SiCr) Oil-Tempered Wire: Offers superior fatigue resistance and heat resistance compared to carbon steel wire, making it ideal for valve springs, heavy-duty coil springs, and applications exposed to high temperatures.
- Chromium-Vanadium (CrV) Oil-Tempered Wire: Known for its high tensile strength and resistance to both high stress and high temperatures, this wire is often used in high-performance automotive suspensions and precision mechanical springs.
- Silicon-Manganese (SiMn) Oil-Tempered Wire: Provides enhanced elasticity and fatigue resistance, making it suitable for dynamic loads in automotive suspensions and industrial applications.
Applications: Heavy-duty springs in automotive suspensions, industrial machinery, and valve springs.
Spring Oil-Tempered Wire Material Composition, Strength, Properties, Application
Grade | Composition | Key Properties | Common Uses | Temperature Resistance |
---|---|---|---|---|
Carbon Steel Oil-Tempered Wire | C: 0.50–0.85%, Si: 0.15–0.35%, Mn: 0.60–1.00% | – High yield strength – Good elasticity – Cost-effective – Fatigue-resistant | – Automotive suspension springs – Industrial machinery springs – General-purpose heavy-duty springs | Up to 160°C |
Silicon-Chromium (SiCr) Oil-Tempered Wire (SWOSC-B) | C: 0.50–0.70%, Si: 1.20–2.00%, Cr: 0.50–1.50% | – Superior fatigue resistance – Excellent heat resistance – Stronger than carbon steel wire | – Valve springs – Heavy-duty coil springs – High-temperature applications | Up to 300°C |
Chromium-Vanadium (CrV) Oil-Tempered Wire | C: 0.50–0.65%, Si: 0.15–0.35%, Mn: 0.60–1.00%, Cr: 0.80–1.10%, V: 0.05–0.15% | – High tensile strength – Good resistance to high stress & temperature – Excellent durability | – Valve springs – High-performance suspension springs – Precision mechanical springs | Up to 300°C |
Silicon-Manganese (SiMn) Oil-Tempered Wire | C: 0.50–0.80%, Si: 1.20–1.80%, Mn: 0.50–1.20% | – Enhanced elasticity – Good fatigue resistance – Suitable for dynamic loads | – Automotive suspension springs – Industrial applications – High-stress mechanical components | Up to 250°C |
1.5 Copper and Copper Alloy Wire
Copper and its alloys, such as brass, phosphor bronze, and beryllium copper, are used in applications requiring high conductivity, corrosion resistance, and non-magnetic properties. These materials are more expensive than steel but offer unique advantages in specialized applications.
- Brass Wire: Known for its good electrical conductivity and moderate corrosion resistance, brass wire is commonly used in applications requiring non-magnetic properties, such as electrical contacts, connectors, and decorative springs.
- Phosphor Bronze Wire: Offers excellent fatigue resistance and high strength, making it ideal for springs in electronic devices, precision instruments, and electrical connectors. It also has high corrosion resistance.
- Beryllium Copper Wire: A premium material with superior strength and excellent fatigue resistance, beryllium copper is used in high-performance applications such as aerospace, military equipment, and electrical contacts. It offers very high corrosion resistance and is non-magnetic.
- Nickel Silver Wire: With good corrosion resistance and a non-magnetic nature, nickel silver wire is often used in decorative applications, musical instruments, and electrical connectors. Its attractive appearance makes it suitable for aesthetic purposes as well.
- Applications: Electrical connectors, precision instruments, and telecommunications equipment.
Spring Copper Wire Material Composition, Strength, Properties, Application
Material Type | Composition | Key Properties | Common Uses | Corrosion Resistance |
---|---|---|---|---|
Brass Wire | Cu: 60–70%, Zn: 30–40% | – High electrical conductivity – Good corrosion resistance – Non-magnetic | – Electrical contacts – Springs in electronic connectors – Decorative springs | Moderate |
Phosphor Bronze Wire | Cu: 85–90%, Sn: 5–10%, P: ≤0.35% | – Excellent fatigue resistance – High strength and corrosion resistance – Non-magnetic | – Electrical connectors – Springs in electronic devices – Precision instruments | High |
Beryllium Copper Wire | Cu: 96–98%, Be: 0.5–2.0%, Co: ≤0.25% | – Superior strength and conductivity – Excellent fatigue resistance – Non-magnetic | – High-performance springs – Electrical contacts – Springs in aerospace and military applications | Very High |
Nickel Silver Wire | Cu: 55–65%, Ni: 10–20%, Zn: 15–30% | – Good corrosion resistance – Non-magnetic – Attractive appearance | – Springs in musical instruments – Decorative springs – Electrical connectors | High |
2. Plastic Spring Materials
Plastic springs, primarily used for vibration damping, offer distinct advantages over metal springs. Their flexibility allows them to absorb shocks and vibrations effectively, making them ideal for noise reduction and enhancing comfort in various applications.
Advantages of Rubber Springs:
- High flexibility and design freedom
- Superior vibration damping properties
- Quiet operation
- Lightweight and cost-effective
However, rubber springs are susceptible to degradation from heat, oil, and ozone, and material selection is critical to avoid these issues.
Plastic Spring Material Composition, Strength, Properties, Application
Rubber Type | Abbreviation | Properties | Temperature Range (°C) |
---|---|---|---|
Natural Rubber | NR | Excellent elasticity, good low-temperature performance | -30 to 60 |
Neoprene (Polychloroprene) | CR | Good weather resistance, moderate oil resistance | -20 to 80 |
Nitrile Rubber | NBR | Excellent oil resistance, good heat resistance | -10 to 80 |
Silicone Rubber | Q | Excellent heat and cold resistance | -40 to 130 |
3. Fluid Spring Materials
Fluid springs utilize gases or liquids to provide spring-like properties. They have adjustable strength through pressure control, and prevent damage by releasing excess pressure when overloaded These springs are typically used in applications requiring variable damping, such as automotive suspensions, industrial machinery, and building shock absorbers.
How Fluid Springs Work:
Fluid springs consist of a sealed container filled with gas or oil. When pressure is applied, the fluid compresses, generating resistance based on Pascal’s principle. The strength of the spring can be adjusted by controlling the pressure within the container.
- Gas Springs: Utilize compressed gas, usually nitrogen, to provide spring force. They are commonly used in automotive suspensions and office chairs due to their high adjustability and responsiveness.
- Hydraulic Springs: Filled with oil or other fluids, hydraulic springs offer precise motion control and high load-bearing capacity, making them suitable for automotive shock absorbers and heavy machinery.
- Hydropneumatic Springs: These springs combine gas and oil, offering excellent load control and durability. They are used in high-performance applications, such as advanced automotive suspensions and building seismic isolation systems.
Fluid Spring Material Composition, Strength, Properties, Application
Type | Composition | Key Properties | Common Uses | Adjustability |
---|---|---|---|---|
Gas Springs | Gas-filled (typically nitrogen) | – Adjustable spring strength via gas pressure – High responsiveness – Good damping characteristics | – Automotive suspensions – Office chair height adjustments – Industrial machinery – Building shock absorbers | Easily adjustable via gas pressure |
Hydraulic Springs | Oil or other fluid-filled | – Smooth, precise motion control – High load-bearing capacity – Excellent damping properties | – Automotive shock absorbers – Heavy machinery – Hydraulic presses – Construction equipment | Adjustable via fluid pressure |
Hydropneumatic Springs | Combination of gas (nitrogen) and oil | – Combines advantages of both gas and hydraulic springs – Excellent load control – High durability | – High-end automotive suspensions – Heavy-duty industrial equipment – Building seismic isolation systems | High adjustability via gas and fluid |
Best Spring Materials: Optimal Selection for Your Project
When selecting the best spring material, several factors need to be considered, including load capacity, environmental resistance, fatigue strength, and cost.
Differences Between Each Type of Spring Materials
Below is a comparison table for various spring material types, covering key characteristics such as material type, composition, common uses, properties, and cost.
Material Type | Symbol | Composition | Common Uses | Key Properties | Cost (Relative) |
---|---|---|---|---|---|
Music Wire | SWP-A, SWP-B, SWP-V | High-carbon steel | Automotive valve springs, clutch springs, brake springs | High tensile strength, fatigue resistance, good for high-reliability applications | Moderate |
Hard Steel Wire | SW-A, SW-B, SW-C | Medium to high-carbon steel | General-purpose springs, pins, switches, toys | Strong, cost-effective, widely used for general applications | Low |
Stainless Steel Wire | SUS302, SUS304, SUS316, SUS631 | Chromium-nickel steel alloys (with or without molybdenum) | Corrosion-resistant springs, electrical devices, medical equipment | Excellent corrosion and heat resistance, non-magnetic (SUS316), high strength (SUS631) | High |
Oil-Tempered Wire | SWOSC-B, SWOSC-V | Silicon-chromium alloy, chromium-vanadium steel | Large coil springs, valve springs, heat-resistant springs | High heat resistance, fatigue resistance, high yield strength, used for large or high-stress springs | Moderate |
Spring Steel (Hot-Formed) | SUP6, SUP9, SUP10 | High-carbon steel | Large coil springs, leaf springs, torsion bars | Requires post-formation heat treatment for strength, used for large-diameter springs | High |
Brass Wire | – | Copper-zinc alloy | Non-magnetic springs, electrical conductors | High conductivity, corrosion resistance, non-magnetic | High |
Phosphor Bronze Wire | – | Copper-tin-phosphorus alloy | Corrosion-resistant springs, electrical components | Good balance of strength and conductivity, corrosion resistance | High |
Beryllium Copper Wire | – | Copper-beryllium alloy | High-performance non-magnetic springs, electrical components | Excellent strength and conductivity, non-magnetic, high fatigue resistance | Very High |
Nickel Silver Wire | – | Copper-nickel-zinc alloy | Non-magnetic springs, electrical components | High electrical conductivity, corrosion resistance, non-magnetic | High |
Best Spring Materials for Each Type of Spring
Here we summarize the best spring materials for each type of spring based on common applications, material properties, and performance requirements:
Type of Spring | Best Materials | Reason/Properties | Common Applications |
---|---|---|---|
Compression Springs | – Piano Wire (SWP-A, SWP-B) – Hard Steel Wire (SW) – Stainless Steel (SUS304) | – High tensile strength – Excellent fatigue resistance – Corrosion resistance (SUS304) | – Automotive components – Industrial machinery – Electronics |
Tension (Extension) Springs | – Piano Wire (SWP-A) – Hard Steel Wire (SW) – Phosphor Bronze | – High elastic limit – Good fatigue resistance – Corrosion resistance (Phosphor Bronze) | – Door hinges – Automotive suspension – Electrical devices |
Torsion Springs | – Silicon-Chromium Oil-Tempered Wire (SWOSC-B) – Beryllium Copper – Stainless Steel (SUS631) | – High yield strength – Excellent heat resistance (SWOSC-B, SUS631) – Non-magnetic (Beryllium Copper) | – Automotive suspension – Industrial machinery – Aerospace |
Leaf Springs | – Spring Steel (SUP6, SUP9) <br> – Silicon-Manganese Steel | – High strength – Good resistance to heavy loads and cyclic stress | – Heavy-duty vehicles (trucks) – Railways – Agricultural equipment |
Valve Springs | – Silicon-Chromium Oil-Tempered Wire (SWOSC-V) – Piano Wire (SWP-V) | – Superior fatigue resistance – High heat resistance | – Automotive engines – Industrial valves |
Non-Magnetic Springs | – Beryllium Copper – Phosphor Bronze – Nickel Silver | – High electrical conductivity <br> – Non-magnetic <br> – Corrosion resistance | – Medical devices – Aerospace – Electronics |
Heat-Resistant Springs | – Stainless Steel (SUS316, SUS631) <br> – Silicon-Chromium Oil-Tempered Wire | – Excellent heat resistance – Corrosion resistance | – High-temperature industrial equipment – Automotive exhaust systems |
Corrosion-Resistant Springs | – Stainless Steel (SUS304, SUS316) – Phosphor Bronze – Beryllium Copper | – Excellent corrosion resistance – Non-magnetic (Phosphor Bronze, Beryllium Copper) | – Marine equipment – Chemical processing – Outdoor applications |
Conductive Springs | – Beryllium Copper – Brass – Phosphor Bronze | – High electrical conductivity – Good fatigue resistance | – Electrical connectors – Switches – Relays |
Large Coil Springs | – Spring Steel (SUP6, SUP9) – Silicon-Manganese Steel | – High strength – Excellent resilience under heavy loads | – Industrial machinery – Heavy-duty automotive parts (suspension, shocks) |
Precision Springs | – Piano Wire (SWP-A) – Stainless Steel (SUS304) – Phosphor Bronze | – High fatigue strength – Corrosion resistance (SUS304, Phosphor Bronze) | – Precision instruments – Clocks – Measuring devices |
Flat Springs | – Stainless Steel (SUS304) – Phosphor Bronze – Beryllium Copper | – Good corrosion resistance – High fatigue strength – Excellent conductivity (Beryllium Copper) | – Electrical contacts – Switches – Relays |
Which Type of Spring Material is Good For Your Project?
Below are some guidelines for choosing the most suitable spring material based on application requirements:
- For high-stress applications such as automotive valve springs or heavy-duty industrial machinery, piano wire (SWP-A, SWP-B, SWP-V) is often the best choice due to its high tensile strength, fatigue resistance, and ability to withstand repeated loads.
- For corrosion resistance in harsh environments, stainless steel (SUS304, SUS316, SUS631) is the preferred option. SUS316 is particularly suitable where higher corrosion resistance is required, while SUS631 is ideal for high-temperature applications due to its excellent heat resistance.
- For applications requiring electrical conductivity or non-magnetic properties, copper and copper alloys such as phosphor bronze and beryllium copper are typically the best choices despite their higher cost. These materials are often used in electrical connectors and other electronics-related applications.
- For vibration damping and noise reduction, rubber springs are the most suitable, especially in environments where quiet operation is critical. Materials like natural rubber and neoprene are commonly used for their excellent damping properties.
Each spring material offers unique benefits depending on the specific requirements of the application. The best spring material is one that provides the optimal balance between performance, durability, and cost for your particular use case.