Stainless steel has become an indispensable material in modern industry, but it isn’t a single alloy but rather a diverse family of metal alloys. Countless combinations of various elements create different types of stainless steel, today we’ll explore stainless steel families and grades with comparison charts, to learn about each type with chemical composition, properties, and uses.
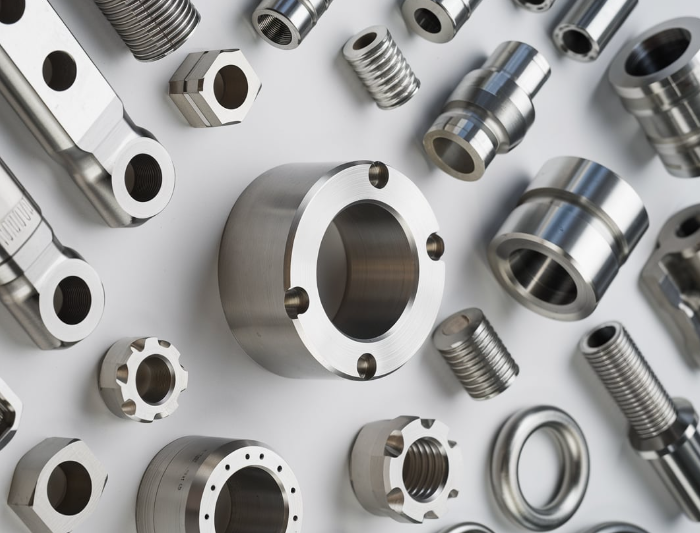
Stainless Steel Families – Common Types and Categories of Stainless Steels
1. Austenitic Stainless Steel
This is the most common family of stainless steel, representing the majority of stainless steel production. Their non-magnetic nature and face-centered cubic crystal structure contribute to excellent formability and weldability. The high chromium and nickel content give them superior corrosion resistance. Common examples include grades 304 (18% chromium, 8% nickel) and 316 (with added molybdenum for enhanced chloride resistance in marine and chemical environments).
2. Ferritic Stainless Steel
These magnetic stainless steels, with a body-centered cubic crystal structure, are the second most common type. Containing 10.5-30% chromium and minimal to no nickel, they are a more economical option than austenitic grades. However, this cost-effectiveness comes at the expense of somewhat reduced corrosion resistance, formability, and weldability. Grades like 430 (16-18% chromium for moderate corrosion resistance) and 446 (23-27% chromium for high-temperature applications) are typical examples.
3. Martensitic Stainless Steel
This least common category of stainless steel is magnetic and possesses a body-centered tetragonal crystal structure. Their composition of 11.5-18% chromium and up to 1.2% carbon allows for hardening through heat treatment, resulting in high strength, hardness, and wear resistance. While their corrosion resistance is generally lower than ferritic or austenitic grades, they excel in applications demanding high tensile strength and impact resistance. Sometimes, a protective polymer coating is used to enhance corrosion resistance. Common grades include 410 (moderate corrosion resistance) and 420 (higher carbon content for increased hardness and wear resistance, often used in cutlery).
4. Duplex (Ferritic-Austenitic) Stainless Steel
Living up to their name, duplex stainless steels possess a mixed microstructure of austenite and ferrite, inheriting advantageous properties from both families. This hybrid structure results in superior corrosion resistance (particularly against chloride pitting) and higher tensile strength compared to standard austenitic grades. These qualities make them well-suited for demanding applications in the oil and gas industry, such as pipelines and pressure vessels. Common grades include 2205 (suitable for harsh environments) and 2507 (a “super duplex” grade with even higher corrosion resistance and strength).
5. Precipitation-hardening (PH) Stainless Steel
This category offers a unique combination of high strength and corrosion resistance. These alloys can be strengthened through heat treatment, achieving strengths several times greater than standard austenitic stainless steels. Their corrosion resistance is comparable to austenitic grades due to their high chromium and nickel content. This combination of properties makes them valuable in demanding industries like aerospace, nuclear, and oil and gas. Common examples include 17-4PH and 15-5PH (both with 17% chromium and 4% nickel, but 15-5PH offers improved weldability and stress corrosion cracking resistance due to lower carbon content).
Stainless Steel Designation Standards
1. SAE/AISI (Society of Automotive Engineers/American Iron and Steel Institute)
SAE/AISI uses a three-digit system, which is one of the most widely recognized. For example, 304 is the most common grade, while 316 offers better corrosion resistance. The first number indicates the family (2xx for austenitic chromium-nickel-manganese, 3xx for austenitic chromium-nickel, 4xx for ferritic and martensitic).
2. ASTM/UNS (American Society for Testing and Materials/Unified Numbering System)
ASTM/UNS standard uses a letter followed by five numbers. The letter ‘S’ designates stainless steel, followed by a number that often corresponds to the SAE grade. For example, S30400 corresponds to 304 grade, while S31600 corresponds to 316 grade.
3. EN (European Standard) uses both numerical and name-based designations.
The numerical system starts with 1.4xxx, where xxx relates to the alloy composition. The name system uses letters and numbers to indicate composition, like X5CrNi18-10 for 304 grade, where X5 indicates 0.05% carbon, and CrNi18-10 shows 18% chromium and 10% nickel.
4. DIN (German Standard)
DIN historically used a system similar to the EN name-based system, such as X5CrNi18-10 for 304 grade. Many DIN standards have been replaced by EN standards, but the naming convention is still commonly used.
5. BS (British Standards)
BS standard uses a combination of numbers and letters, like 304S15, where 304 corresponds to the basic grade and S15 indicates specific variations. This system is gradually being replaced by EN standards but remains in use for certain applications.
6. JIS (Japanese Industrial Standards)
JIS uses the prefix SUS (Steel Use Stainless) followed by the grade number, such as SUS 304 or SUS 316. Additional suffixes may indicate special properties or processing methods, like SUS 304-CSP for cold-stretched wire.
7. GB (Chinese Standard)
GB follows a system similar to international standards but with its own designations. For example, 0Cr18Ni9 corresponds to 304 grade, where the numbers indicate the chromium (18%) and nickel (9%) content.
8. ISO (International Organization for Standardization)
ISO provides international standards that often align with other major systems. They use both chemical composition designations and steel names, helping to harmonize different national standards. For example, ISO 683-13 covers general-purpose stainless steel.
Stainless Steel Family Chart
Family | Magnetic Response | Work Hardening Rate | Corrosion Resistance | Hardenable By | Ductility | High-Temperature Resistance | Low-Temperature Resistance | Weldability | Uses |
---|---|---|---|---|---|---|---|---|---|
Austenitic | No | Very High | High | Cold Work | Very High | Very High | Very High | Very High | Food, Healthcare, Outdoor Enclosures |
Duplex | Yes | Medium | Very High | Quench & Temper | Medium | Low | Medium | High | Heat Exchangers, Off-shore Oil & Gas, Chemical Plants |
Ferritic | Yes | Medium | Medium | Quench & Temper | Medium | High | Low | Low | Cooking Utensils, Automotive Industry |
Martensitic | Yes | Medium | Medium | Quench & Temper | Low | Low | Low | Low | Knife Blades, Surgical Instruments, Razor Blades |
Precipitation Hardening | Yes | Medium | Medium | Age Harden | Medium | Low | Low | High | Nuclear Waste Casks, Turbine Blades, Aerospace Industry |
Stainless Steel Grades Chemical Composition Chart
AISI/SAE | C, ≤ | Mn, ≤ | P, ≤ | S, ≤ | Si, ≤ | Cr | Ni | Mo | N, ≤ | Others, ≤ |
---|---|---|---|---|---|---|---|---|---|---|
Austenitic | ||||||||||
302 | 0.15 | 2.00 | 0.045 | 0.03 | 0.75 | 17.0-19.0 | 8.0-10.0 | – | 0.10 | – |
303 | 0.15 | 2.00 | 0.2 | ≥0.15 | 1.00 | 17.0-19.0 | 8.0-10.0 | – | – | – |
304 | 0.08 | 2.00 | 0.045 | 0.03 | 1.00 | 18.0-20.0 | 8.0-11.0 | – | – | – |
304L | 0.03 | 2.00 | 0.045 | 0.03 | 1.00 | 18.0-20.0 | 8.0-11.0 | – | – | – |
308 | 0.08 | 2.00 | 0.045 | 0.03 | 1.00 | 19.0-21.0 | 10.0-12.0 | – | – | – |
310 | 0.25 | 2.00 | 0.045 | 0.03 | 1.5 | 24.0-26.0 | 19.0-22.0 | – | – | – |
316 | 0.08 | 2.00 | 0.045 | 0.03 | 1.00 | 16.0-18.0 | 10.0-14.0 | 2.00-3.00 | – | – |
316L | 0.03 | 2.00 | 0.045 | 0.03 | 1.00 | 16.0-18.0 | 10.0-14.0 | 2.00-3.00 | – | – |
317 | 0.08 | 2.00 | 0.045 | 0.03 | 1.00 | 18.0-20.0 | 11.0-15.0 | 3.0-4.0 | 0.10 | – |
321 | 0.08 | 2.00 | 0.045 | 0.03 | 1.00 | 17.0-19.0 | 9.0-12.0 | – | 0.10 | ≥Ti 5×(C+N), ≤0.70 |
347 | 0.08 | 2.00 | 0.045 | 0.03 | 1.00 | 17.0-19.0 | 9.0-12.0 | – | – | ≥Cb 10×C, ≤1.00 |
904L | 0.02 | 2.00 | 0.045 | 0.035 | 1.00 | 19.0-23.0 | 23.0-28.0 | 4.00-5.00 | 0.1 | Cu 1.00-2.00 |
Ferritic | ||||||||||
409 | 0.03 | 1.00 | 0.040 | 0.015 | 1.00 | 10.50-12.50 | – | 6×(C+N) to 0.65 | – | |
430 | 0.12 | 1.00 | 0.04 | 0.03 | 1.00 | 16.0-18.0 | – | – | – | |
430F | 0.12 | 1.25 | 0.06 | ≥0.15 | 1.00 | 16.0-18.0 | – | – | – | |
444 | 0.025 | 1.00 | 0.04 | 0.03 | 1.00 | 17.5-19.5 | 1.00 | 1.75-2.50 | 0.035 | Ti+Cb 0.20+4×(C+N)-0.80 |
Martensitic | ||||||||||
410 | 0.08-0.15 | 1.00 | 0.04 | 0.03 | 1.00 | 11.5-13.5 | – | – | – | |
416 | 0.15 | 1.25 | 0.06 | ≥0.15 | 1.00 | 12.0-14.0 | – | – | – | |
420 | ≥0.15 | 1.00 | 0.04 | 0.03 | 1.00 | 12.0-14.0 | – | – | – | |
431 | 0.2 | 1.00 | 0.04 | 0.03 | 1.00 | 15.0-17.0 | 1.25-2.50 | – | – | |
440A | 0.60-0.75 | 1.00 | 0.04 | 0.03 | 1.00 | 16.0-18.0 | – | ≤0.75 | – | |
440B | 0.75-0.95 | 1.00 | 0.04 | 0.03 | 1.00 | 16.0-18.0 | – | ≤0.75 | – | |
440C | 0.95-1.20 | 1.00 | 0.04 | 0.03 | 1.00 | 16.0-18.0 | – | ≤0.75 | – | |
Duplex | ||||||||||
2205 | 0.03 | 2.00 | 0.03 | 0.02 | 1.00 | 22.0-23.0 | 4.5-6.5 | 3.0-3.5 | 0.14-0.20 | – |
2304 | 0.03 | 2.5 | 0.04 | 0.03 | 1.00 | 21.5-24.5 | 3.0-5.5 | 0.05-0.60 | 0.05-0.60 | – |
PH | ||||||||||
15-5 PH | 0.07 | 1 | 0.04 | 0.03 | 1 | 14.0-15.5 | 3.5-5.5 | – | – | 2.5-4.5 Cu; 0.15-0.45 Nb |
17-4 PH | 0.07 | 1 | 0.04 | 0.03 | 1 | 15.5-17.5 | 3.0-5.0 | – | – | 3.0-5.0 Cu; 0.15-0.45 Nb |
Stainless Steel Grades Properties Chart
Grade | Tensile Strength | Max Temperature | Melting Point | Resistance |
---|---|---|---|---|
301 | 515 MPa (75 Ksi) | 871 °C (1600 °F) | 1399-1421°C (2550-2590°F) | Excellent corrosion resistance |
302 | 585 MPa (85 Ksi) | 870 °C (1,679°F) | 1400-1420 °C (2550-2590 °F) | Excellent corrosion resistance |
303 | 690 MPa (100 Ksi) | 760 °C (1,400 °F) | 1400-1420 °C (2550-2590 °F) | Lower corrosion resistance |
304 | 621 MPa (90 Ksi) | 870 °C (1,679 °F) | 1399-1454°C (2,550-2,650°F) | Good overall resistance to corrosives |
309 | 620 MPa (89 Ksi) | 1000 °C (1,832 °F) | 1400-1455°C (2550-2651°F) | Excellent corrosion resistance |
316 | 579 MPa (84 Ksi) | ~800 °C (1,472°F) | 1371-1399°C (2500-2550°F) | Excellent chloride resistance |
317 | 585 MPa (85 Ksi) | 816 °C (1,500°F) | 1370-1400°C (2500-2550°F) | Good chloride resistance |
321 | 620 MPa (90 Ksi) | 816 °C (1,500°F) | 1400-1425°C (2,550-2,600°F) | Excellent corrosion resistance |
347 | 690 MPa (101 Ksi) | 816 °C (1,500°F) | 1400-1425°C (2,550-2,600°F) | Excellent corrosion resistance |
405 | 585 MPa (85 Ksi) | 815 °C (1,499°F) | 1480-1530°C (2,700-2,790°F) | Good acid corrosion resistance |
408 | 505 MPa (73 Ksi) | 815 °C (1,499°F) | 1400-1455°C (2,550-2,650°F) | Resists most oxidizing acids and salt spray |
409 | 448 MPa (65 Ksi) | 815 °C (1,499°F) | 1425-1510°C (2,597-2,750°F) | Good corrosion resistance |
420 | 760-1702 MPa (110-247 Ksi) | 427 °C (800°F) | 1455-1510°C (2,651-2,750°F) | Fairly corrosion resistant |
430 | 450 MPa (65 Ksi) | 815 °C (1,499°F) | 1425-1510°C (2,597-2750°F) | Good nitric acid resistance |
434 | 540 MPa (78 Ksi) | 815 °C (1,499°F) | 1426-1510°C (2,600-2750°F) | Superior pitting resistance |
436 | 459 MPa (67 Ksi) | 815 °C (1,499°F) | 1425-1510°C (2,600-2,750°F) | Excellent citric and nitric acid corrosion resistance |
442 | 515-550 MPa (77-80 Ksi) | 925-980 °C (1,700-1,800°F) | 1065-1120°C (1,950-2,050°F) | Good corrosion resistance |
444 | 415 MPa (60 Ksi) | 950 °C (1,752°F) | 1405-1495°C (2,561-2,723°F) | Good oxidation resistance |
410 | 500-1400 MPa (73-203 Ksi) | 650 °C (1,202°F) | 1482-1532°C (2,700-2,790°F) | Good corrosion resistance to air, water, and some chemicals |
410S | 444 MPa (64 Ksi) | 705 °C (1,300°F) | 1482-1532°C (2,700-2,790°F) | Good oxidation resistance |
416 | 517 MPa (75 Ksi) | 760 °C (1,400°F) | 1480-1530°C (2,696-2,786°F) | Poor chloride resistance |
420 | 586 MPa (85 Ksi) annealed 1,586 MPa (230 Ksi) hardened |
650 °C (1,202°F) | 1454-1510°C (2,649-2,750°F) | Resistant to mild acids, alkalis, and water |
440 | 758 MPa (110 Ksi) | 760 °C (1,400°F) | 1483°C (2,700°F) | Limited corrosion resistance |
2205 | 620 MPa (90 Ksi) | 300 °C (572°F) | 1385-1443°C (2,525-2,630°F) | Excellent corrosion resistance |
2304 | >600 MPa (>87 Ksi) | 570 °C (1,058°F) | 900-1150°C (1,650-2,100°F) | Resistance to corrosion cracking |
2507 | 800 MPa (116 Ksi) | 300 °C (572°F) | 1350°C (2,460°F) | Excellent chloride corrosion resistance |
17-4 | 1103 MPa (160 Ksi) | 316 °C (600°F) | 1404-1440°C (2,560-2,625°F) | Excellent corrosion resistance |
15-5 | 1380 MPa (200 Ksi) | 316 °C (600°F) | 1404-1440°C (2,560-2,625°F) | Excellent corrosion resistance |