Tapped holes and threaded holes play crucial roles in various industries, from manufacturing to construction and beyond. While they may seem similar at first glance, these two types of holes possess distinct characteristics and serve different purposes. Understanding their differences is essential for selecting the appropriate hole type for specific applications, ensuring structural integrity and optimal performance. Here we will present the disparities between tapped holes and threaded holes, from their definitions to their applications, advantages, and considerations.
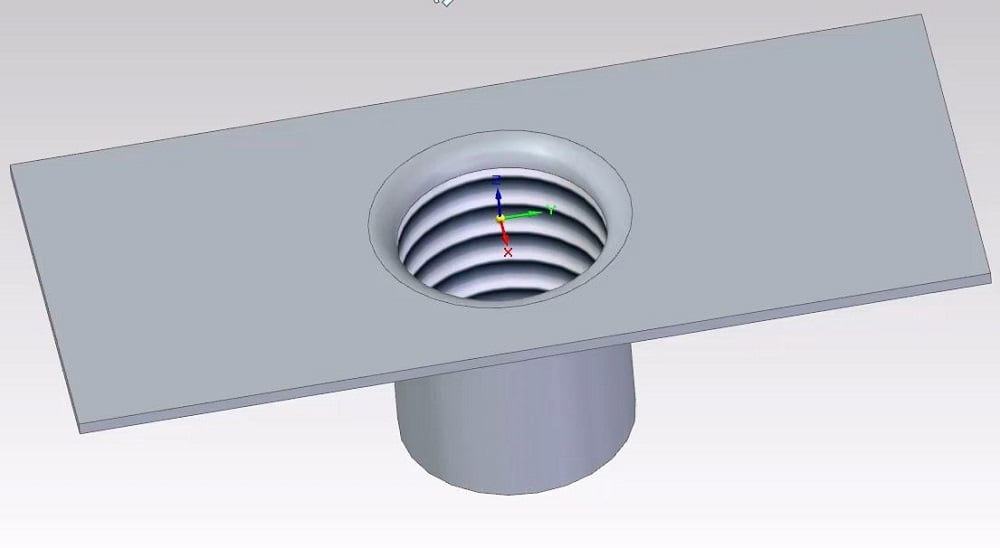
What are Tapped Holes?
A tapped hole is a hole with internal threads that match the threads of a corresponding screw or bolt. The purpose of creating a tapped hole is to enable the insertion of a fastener, creating a secure and reliable connection between two or more components. The thread engagement in a tapped hole ensures that the fastener remains in place and can handle loads and forces.
Tapping Process:
The process of creating a tapped hole involves using a tap, a cutting tool specifically designed for thread creation. The tap is inserted into a pre-drilled hole, and with the help of a tapping wrench or machine, it cuts into the material, removing excess material and creating the threads. Tapping can be done manually or with the aid of automated machinery.
Types of Taps:
There are various types of taps available, and the selection depends on factors such as the material being tapped, the required thread type, and the desired thread size. Some common types of taps include:
- Straight Flute Taps: These taps have straight, continuous flutes and are suitable for through-hole tapping.
- Spiral Flute Taps: These taps have flutes that twist around the tap body, helping to evacuate chips during the tapping process. They are commonly used for blind-hole tapping.
- Bottoming Taps: Also known as plug taps, these taps have a limited number of threads at the tip, making them suitable for tapping near the bottom of a blind hole.
- Taper Taps: These taps have a tapered profile and are used for easy starting and alignment in the tapping process.
Tapped Holes Pros & Cons
Tapped holes are commonly used in various applications, especially in industries like manufacturing and construction. They have their own set of advantages and disadvantages, which depend on the specific context and requirements of the project. Here are some pros and cons of using tapped holes:
Pros:
- Threaded Fastening: Tapped holes provide a reliable and secure method for fastening components together. Bolts, screws, or studs with matching threads can be easily inserted and tightened to create a strong connection.
- Precision: Tapped holes can be precisely machined to meet specific thread standards and tolerances. This ensures a tight fit and minimizes the risk of components loosening over time.
- Aesthetics: Tapped holes can be designed to be flush with the surface, providing a clean and professional appearance in applications where aesthetics matter.
- Cost-Efficiency: Tapped holes are often more cost-effective than alternative methods of fastening, such as welding or using inserts. They require fewer components and less specialized equipment.
- Assembly and Disassembly: Tapped holes allow for easy assembly and disassembly of components, making maintenance and repairs more accessible.
- Versatility: Tapped holes can be used in a wide range of materials, including metals, plastics, and composites, making them versatile for various applications.
Cons:
- Weakened Material: Creating tapped holes involves removing material, which can weaken the structural integrity of the workpiece, especially in thin materials. This may necessitate reinforcement or larger fasteners.
- Limited Load Capacity: Tapped holes may have a lower load-bearing capacity compared to other methods like through holes with nuts or welds, which can limit their use in heavy-duty applications.
- Thread Damage: Threads in tapped holes can be susceptible to damage if over-tightened or subjected to excessive loads. Cross-threading or stripping the threads can compromise the connection.
- Limited Adjustment: Once a component is fastened into a tapped hole, adjustment or alignment may be challenging without re-machining or drilling a new hole.
- Size and Depth Constraints: Tapped holes have size and depth limitations, and if the required hole size is too large or the material too thin, alternative fastening methods may be necessary.
- Complexity: Creating accurate tapped holes requires precision machining, which can be more complex and time-consuming than other fastening methods, such as welding or adhesive bonding.
What are Threaded Holes?
A threaded hole is an aperture or cavity with internal threads that correspond to the threads on the shank of an external fastener. The purpose of threaded holes is to provide a means of connecting components securely and allowing for the easy disassembly and reassembly of parts when needed.
Thread Process:
apping is the process of creating threads in a hole using a tap, as mentioned earlier. On the other hand, thread cutting involves cutting or machining threads into a pre-drilled hole using tools such as thread milling cutters or thread forming dies. Thread cutting is typically used when greater thread strength or accuracy is required, but it may be more time-consuming and costly compared to tapping.
Types of Threads:
Threads can have various profiles and configurations based on the application requirements. The most common types of threads used in threaded holes are:
- Unified Thread Standard (UTS): UTS includes thread profiles like UNC (coarse), UNF (fine), and UNEF (extra fine), which are widely used in general-purpose applications.
- Metric Thread Standard: Metric threads follow the International Organization for Standardization (ISO) metric thread system and are commonly used in many countries for mechanical applications.
- Pipe Threads: Pipe threads, such as NPT (National Pipe Thread) and BSP (British Standard Pipe), are used specifically for fluid-carrying applications.
Threaded Holes Pros & Cons
Threaded holes, like tapped holes, have their own set of advantages and disadvantages. Here’s a brief overview of the pros and cons of threaded holes:
Pros:
- Reliable Fastening: Threaded holes provide a dependable method for securely fastening components together, using matching screws or bolts.
- Uniform Threads: Threads in pre-made holes are typically manufactured with precision and uniformity, ensuring a tight and consistent fit.
- No Material Weakening: Threaded holes are pre-made and don’t involve removing material from the workpiece, preserving its structural integrity.
- Load Distribution: The load is distributed more evenly along the length of the threaded hole, which can enhance overall strength.
- Standardization: Many industries adhere to standardized thread sizes and types, making it easier to select the appropriate fasteners.
- Quick Assembly: Components can be easily and quickly assembled using threaded holes without the need for additional machining.
Cons:
- Limited to Pre-Existing Holes: Threaded holes are only available where they have been pre-drilled or pre-machined, which can limit design flexibility.
- Alignment Challenges: Achieving precise alignment for mating components can be more challenging with pre-made threaded holes.
- Not Suitable for Thin Materials: In thin materials, threaded holes may compromise the structural integrity more than other fastening methods.
- Limited to Standard Sizes: The availability of standardized threads may restrict options for non-standard or custom applications.
- Thread Wear: Threads in pre-made holes can wear over time, potentially reducing the holding strength of the fastener.
Tapped Holes vs. Threaded Holes Compared (Differences)
Now that we have examined the definitions, purposes, process, types, advantages and disadvantages of Tapped Holes and Threaded Holes, let’s explore the main part of the article, focusing on the differences between them.
1. Cost Considerations
Let’s begin our exploration by looking at one of the most fundamental factors that influence the choice between tapped and threaded holes: cost.
Tapped Holes: Tapped holes typically have a lower initial cost compared to threaded holes. The process of creating tapped holes involves fewer steps, which translates to reduced labor and tooling expenses. In addition, tapped holes require less precise machining equipment, further contributing to cost savings. For manufacturers operating on tight budgets, this can be an attractive option.
Threaded Holes: Conversely, threaded holes generally incur higher initial costs. The creation of threads within the hole necessitates specialized tooling and more precise machining, leading to increased expenses. However, it’s essential to consider the long-term cost benefits, as threaded holes often provide better durability and longevity, potentially reducing maintenance and replacement costs over time.
2. Drill Size and Hole Preparation
Drill size and hole preparation play a crucial role in the choice between tapped and threaded holes.
Tapped Holes: When it comes to tapped holes, the drill size used for hole preparation is typically smaller compared to threaded holes. This is because tapped holes do not require as much material removal, resulting in a more conservative approach to hole sizing. Smaller drill sizes can be advantageous in applications where space is limited or when working with delicate materials.
Threaded Holes: Threaded holes, on the other hand, require larger drill sizes to accommodate the threading process. The larger hole size can be a drawback in some cases, as it may weaken the component or reduce available space for other features. However, it also allows for stronger threads and improved load-bearing capacity, making threaded holes suitable for heavy-duty applications.
3. Material Compatibility
The choice between tapped and threaded holes can significantly impact material compatibility and the overall performance of the assembly.
Tapped Holes: Tapped holes are generally more forgiving when it comes to material compatibility. They can be successfully created in a wide range of materials, including metals, plastics, and composites. This versatility makes tapped holes a go-to option for manufacturers working with diverse materials or when quick assembly is required.
Threaded Holes: Threaded holes can be more demanding in terms of material compatibility. The threading process, which involves cutting grooves into the material, can be challenging with certain materials like brittle plastics or very hard metals. In such cases, specialized tools and techniques may be necessary to ensure the threads are formed correctly. However, when used with compatible materials, threaded holes offer superior holding power and reliability.
4. Speed of Operation
The speed of operation is a critical consideration in many manufacturing processes, and the choice between tapped and threaded holes can impact efficiency.
Tapped Holes: Tapping is generally a faster process compared to threading. The creation of tapped holes involves fewer steps, with the primary operation being the tapping itself. This can result in shorter cycle times, making tapped holes a preferred choice in high-volume production environments where speed is of the essence.
Threaded Holes: Threading, due to its complexity and the need for larger drill sizes, can be a slower process. It requires careful alignment and precision to create threads that meet the desired specifications. Manufacturers with a focus on precision and quality may be willing to trade speed for the superior thread strength and durability offered by threaded holes.
5. Flexibility in Design
The flexibility to adapt to different design requirements is another pivotal aspect when comparing tapped and threaded holes.
Tapped Holes: Tapped holes offer greater design flexibility, especially in applications where the hole’s size or depth needs to be adjusted easily. Since tapped holes involve fewer material removal steps, it is simpler to modify them as per the evolving design needs. This flexibility can be particularly advantageous in prototype development and design iterations.
Threaded Holes: Threaded holes, once created, are less flexible in terms of design changes. Modifying threaded holes can be challenging and may require more extensive rework or even the creation of entirely new components. Consequently, manufacturers need to carefully consider design specifications and potential changes when opting for threaded holes.
6. Production Method and Volume
The choice between tapped and threaded holes can also influence the production method and volume of a manufacturing process.
Tapped Holes: Tapped holes are well-suited for high-volume production due to their speed and ease of creation. In mass production settings, where components need to be manufactured quickly and cost-effectively, tapped holes often take center stage. The simplicity of the tapping process also means that it can be easily automated, further enhancing production efficiency.
Threaded Holes: Threaded holes, with their intricate threading process and larger drill sizes, are better suited for low to medium volume production or applications where precision and durability are paramount. While not impossible, automating the threading process can be more complex and expensive, making it less practical for high-volume manufacturing.
7. Application
The choice between tapped and threaded holes ultimately depends on the specific application and its requirements. Different industries and projects may lean towards one method over the other.
Tapped Holes: Tapped holes are commonly used in applications where cost-effectiveness, speed, and simplicity are paramount. These include woodworking, assembly lines, and low-torque applications.
Threaded Holes: Threaded holes find favor in industries where precision and strength are critical, such as aerospace, automotive, and heavy machinery manufacturing. They are also preferred when working with high-torque applications.
Understanding the unique demands of the application is essential in making the right choice between tapped and threaded holes.
Relationship Between Tapped and Threaded Holes
It’s important to note that tapped and threaded holes are not mutually exclusive. In fact, they can often coexist within the same assembly, complementing each other’s strengths.
For instance, a component may feature tapped holes for quick and easy assembly during initial manufacturing stages, while threaded holes may be strategically placed in areas where increased load-bearing capacity or resistance to wear and tear is required. This hybrid approach allows manufacturers to optimize both cost-efficiency and performance in their products.
Similarities Between a Tapped Holes and Threaded Holes
Tapped holes and threaded holes are terms often used interchangeably, but they can refer to slightly different things depending on the context. Here, I will describe the similarities between the two:
- 1. Threaded Features: Both tapped holes and threaded holes involve the creation of threads within a hole or recess in a material. These threads are helical grooves that allow for the insertion of screws, bolts, or other threaded fasteners.
- 2. Fastener Compatibility: Tapped holes and threaded holes are designed to accommodate threaded fasteners. The threads on the fastener must match the threads in the hole for a secure and functional connection.
- 3. Fastening Purpose: Tapped and threaded holes are primarily used for fastening purposes. They provide a means to join two or more components together, typically by using a threaded fastener to create a secure and removable connection.
- 4. Common Materials: Tapped and threaded holes can be found in a variety of materials, including metals, plastics, and wood. The creation of threads allows for the installation of fasteners in different types of materials.
- 5. Thread Standards: Both types of holes adhere to specific thread standards and pitch sizes. Common thread standards include metric threads (e.g., M6, M8) and unified threads (e.g., 1/4-20, 5/16-18). These standards ensure compatibility between the threaded holes and fasteners.
- 6. Tooling: Similar tools and equipment are often used to create tapped holes and threaded holes. Tap and die sets, thread mills, and other cutting tools are commonly employed to cut threads in these holes.
- 7. Fastener Types: Tapped and threaded holes can accommodate a wide range of fastener types, including screws, bolts, studs, and more. The choice of fastener depends on the specific application and load requirements.
- 8. Thread Engagement: In both cases, the threaded portion of the fastener engages with the threads in the hole, providing a mechanical connection that resists loosening and maintains the integrity of the assembly.
While there are similarities between tapped and threaded holes, it’s essential to note that the terminology and context can vary. “Tapped hole” typically refers to a hole that has been specifically designed and threaded for a fastener, while “threaded hole” may refer to any hole with threads, including those created by a threaded fastener being inserted into an unthreaded hole. Understanding the specific context and intended use is crucial for accurate communication and engineering applications.
The choice between tapped and threaded holes is a decision that can significantly impact the cost, performance, and overall success of a manufacturing or assembly project. Each option has its distinct advantages and disadvantages, making it crucial for engineers and manufacturers to carefully consider their specific needs and priorities.
Tapped holes offer cost savings, speed of operation, and flexibility, making them ideal for high-volume production and applications where material compatibility varies. Threaded holes, on the other hand, excel in terms of thread strength, durability, and load-bearing capacity, making them suitable for heavy-duty applications where precision is paramount.
Ultimately, the relationship between tapped and threaded holes is one of synergy. By strategically incorporating both into their designs, engineers and manufacturers can achieve the perfect balance between cost-efficiency and performance, ensuring that their products meet the highest standards of quality and reliability.