Triiron tetroxide coating, also known as “Black dyeing” or “fermite treatment,” is a surface treatment method that blackens the surface of steel materials, as the name suggests. However, it does not really “dye it black.” A chemical reaction is used to create a black film on the surface. Black dyeing has various advantages, such as being able to impart rust prevention properties, being inexpensive, not changing dimensions, and being difficult to peel off. We will explain in detail the principles, characteristics, processes, and precautions of black dyeing on Steel materials.
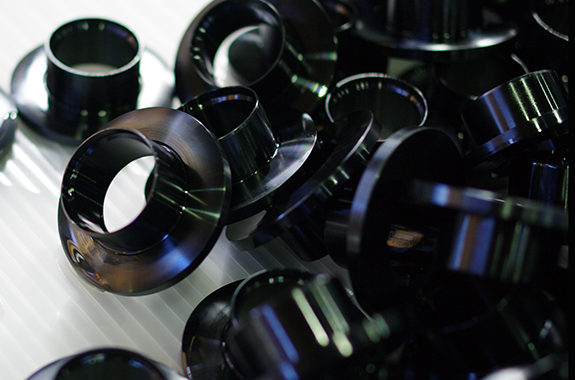
What is Triiron Tetroxide Coating?
Triiron tetroxide coating aka blackening treatment is a process that forms a black oxide film of Fe3O4 (iron(II,III) oxide) known as ‘black rust’ on the surface of the steel, thereby protecting the interior of the steel. In addition to blackening and iron(II,III) oxide film, it is also known by other names such as SOB treatment, alkaline triiron tetroxide treatment, and alkaline coloring.
When performing the blackening treatment, steel components are immersed in a solution of approximately 35-45% sodium hydroxide with oxidants (such as sodium nitrate) and reaction accelerators at around 130-150°C. In this process, the iron on the surface of the component oxidizes to produce a substance known as sodium ferrate. Subsequently, this sodium ferrate is reduced, forming an iron(II,III) oxide film on the surface of the component. Typically, the components are then treated with rust-preventive oil (either by immersion or application). Ultimately, the characteristic feature is the appearance that resembles having been ‘dyed black.
Where is Triiron Tetroxide Coating Used?
Triiron Tetroxide is ideal for applications where dimensional accuracy needs to be maintained, an attractive black color is desired, and a certain level of corrosion resistance is required.
Specifically, Triiron Tetroxide Coating is used for various applications, including steel products such as screws and bolts, various tools, precision machinery components, molds, automotive parts, interior products, and art pieces. However, it is not suitable for components intended for outdoor use, especially in locations with high moisture levels or near the sea, as it may not provide adequate corrosion resistance.
How Does Triiron Tetraoxide Finish Treatment Work & Process?
The Triiron Tetroxide process consists of the following steps. The required time is approximately 50 minutes, which is a significant advantage compared to other surface treatment methods in terms of processing time.
1. Degreasing: To prevent uneven coloring during Triiron Tetroxide, immerse the parts in a degreasing solution at 50-60°C for about 2-5 minutes to remove surface oils and grease. If the parts have already been rust-proofed with oil, wipe off the oil with a cloth before immersing them in the degreasing solution. Be cautious not to immerse parts in the degreasing solution for too long, as it may cause rust.
2. Rinsing: To ensure proper progress of Triiron Tetroxide Coating, rinse the parts thoroughly while overflowing water, as any remaining degreasing solution can hinder the process. If there is rust or dirt (smut, etc.) on the surface of the parts, additional acid cleaning may be required. Be careful when rinsing after acid cleaning, as introducing even a small amount of acid into the blackening treatment solution can cause it to boil over.
3. Blackening Treatment: Place the parts in a boiling Triiron Tetroxide solution within a mesh basket and boil them for about 15-20 minutes while agitating them to ensure complete wetting. Ensure that the temperature is appropriate, as excessively high temperatures can cause the parts to turn red. For parts with many flat surfaces, you may need to use special hanging techniques to prevent marks from the mesh on the treated surfaces.
4. Hot Water Rinse: Quickly transfer the parts to hot water at 50-80°C (for about 5-6 seconds) and rinse them thoroughly while overflowing water. Be cautious about prolonged exposure to air when transferring parts to the hot water rinse stage, as it can lead to red rust formation due to evaporating surface moisture.
5. Rinsing: Rinse the parts thoroughly while overflowing water, ensuring that the innermost areas are adequately cooled. Insufficient rinsing can lead to premature rust formation.
6. Rust Prevention Treatment: After blackening treatment, treat the parts with rust-inhibiting oil (immersion or application) and allow them to dry thoroughly at room temperature. When using immersion, use a separate basket from the one used in the previous steps.
Benefits of Using Triiron Tetroxide Coating on Steel
Blackening treatment has the following characteristics and is used in various applications:
1. Improved Corrosion Resistance
The black oxide film (black rust) on the surface of components is robust and stable. This film helps to partially inhibit the formation of red rust (corrosion that deteriorates iron) on the iron surface. Additionally, the black oxide film is porous, with numerous small holes and irregularities. By post-treating these holes with rust-inhibiting oil, moisture ingress can be prevented, further enhancing corrosion resistance. While it may not provide the same level of corrosion resistance as zinc plating or nickel plating, blackening treatment is recommended when you want to provide some corrosion resistance while maintaining aesthetics. Moreover, post-treating with rust-inhibiting oil can enhance the lubricity of tools and mechanical components.
2. Increased Resistance to Peeling
Plating or painting involves attaching a different material layer to the surface of components, which can lead to the layer peeling off. On the other hand, blackening treatment is a process that chemically transforms only the surface of the component into another substance (black oxide film), making it less prone to peeling. It can be considered a relatively long-lasting surface treatment.
3. Minimal Impact on Dimensional Accuracy
In Triiron Tetroxide Coating, the rate of film formation is not very fast, resulting in a final film thickness of only about 1-2μm. Furthermore, the film is formed from the component’s surface towards the inside. Since the treatment temperature is below 150°C, there is little concern about the component deforming due to heat. Consequently, the dimensions of the component remain largely unchanged before and after blackening treatment. This advantage makes blackening treatment suitable for components that require high precision.
4. Attractive Appearance
Triiron Tetroxide Coating gives components an appearance as if they were dyed black. Surface roughness remains unchanged before and after treatment, and components that had glossiness before treatment acquire a glossy black color, while those that were matte become a non-reflective black color. This characteristic adds a sense of luxury, making blackening treatment suitable not only for industrial products but also for interior and art products.
5. Cost-Effective
Triiron Tetroxide Finish is cost-effective because the raw materials for the treatment solution are inexpensive, and electrodes and fixtures are not required. If a large number of components are processed together in a basket, the processing cost per unit can be further reduced. Since components of different sizes and shapes can be processed at once, blackening treatment is recommended when you want to process various components while keeping costs low.
Points to Consider When Applying Triiron Tetroxide Coating:
While blackening treatment offers numerous benefits, there are some points to consider:
– Not Suitable for All Materials: Triiron Tetroxide Coating is suitable for iron-based materials. However, castings, hardened parts, and wire-cut parts may achieve a black color with a reddish tint rather than a pure black. Additionally, alloy steels containing high levels of chromium or nickel may turn gray instead of black.
– Rust Progression When Oil Wears Off: The black oxide film itself has relatively low corrosion resistance, so as mentioned earlier, the surface is usually treated with rust-inhibiting oil. If this oil wears off, moisture and air can enter the fine holes inside the black oxide film, leading to red rust formation. It’s important to be aware of the limitations of blackening treatment’s corrosion resistance.
Triiron Tetroxide Coating is a surface treatment method that forms an iron-oxide film on the surface of steel components. It provides a beautiful appearance similar to being “dyed black” while maintaining dimensional accuracy. Its cost-effectiveness and the ability to provide a certain level of corrosion resistance make it an attractive option. However, it’s important to be aware that some components may not achieve a pure black color and that the effectiveness of corrosion resistance depends on the maintenance of the surface rust-inhibiting oil.