Swiss lathes have become popular in precision machining in recent years, and many manufacturers choose CNC Swiss-type machines for production. What is a Swiss lathe, and how does a Swiss lathe work? Get into the article and make the choice of whether you should utilize a Swiss machining facility. We’ll also explore the Swiss machining pros/cons, lathe parts, uses, and differences between Swiss turning and conventional turning.
What Is a Swiss-Type Lathe?
A Swiss type lathe, also known as a Swiss automatic lathe, Swiss screw machine, or Swiss turning machine, was originally developed for the Swiss watchmaking industry. The first Swiss-type machine appeared shortly after the collet chuck was patented, which was in the 1870s. Swiss-type machines started to be used in lots of other industries around the 1960s, and the first CNC Swiss machines were released in the 1970s. With the development of machines and tools, massive improvements have been made to the design of Swiss lathes. Gradually, they are used extensively for the production of parts in various fields. A Swiss-style lathe is a type of machine that allows the part to move in the z-axis while the tools remain stationary. The bar stock is held by the collet that is recessed behind the guide bushing and will not be directly exposed to the lathe bed and the tooling, so the material can be turned within the machine rapidly and tightly. This eliminates the deflection and increases the accuracy. Compared to conventional machining, Swiss machining offers lots of benefits.
Advantages of Swiss Lathes/Machining
- Swiss lathes deliver extremely high precision and maintain tight tolerances essential for the medical, aerospace, and electronics industries.
- Swiss machining provides consistent, high-quality parts with excellent repeatability.
- The unique guide bushing system allows Swiss lathes to produce long, slender, and complex parts more effectively than conventional lathes.
- Multiple tool paths enable simultaneous operations such as turning, drilling, and milling, reducing cycle times for complex components.
- Swiss machines often produce parts that are finished or nearly finished in one cycle, minimizing the need for secondary operations.
- The close support of the workpiece by the guide bushing reduces deflection, which causes good surface finishes and dimensional consistency.
- Higher RPM capabilities without vibration enable faster machining and improved surface quality.
- Swiss turning centers are highly automated, combining automatic bar feeding, multiple tools, multi-axis movement, and CAM programming to reduce manual intervention.
Disadvantages of Swiss Lathes/Machining
- Swiss lathes generally accept bar stock sizes only between 2mm and 38mm, requiring consistent diameter stock for proper feeding through the guide bushing.
- Specialized tooling for Swiss machines is expensive, and tool proximity limits the size and geometry of usable tools.
- Using oil as a lubricant results in less effective heat dissipation compared to water, potentially causing heat issues during extended runs.
- Setup time is longer due to the calibration and replacement of multiple cutting tools, along with the need for extensive programming and skilled operator training.
How Does a Swiss Lathe Work?
Unlike conventional lathes, Swiss turning centers have a moving headstock. In the turning operation, the workpiece is clamped onto the chuck or collet in the headstock and moved towards the tooling area through a guide bushing. The headstock moves along the z-axis with the bar stock, and the bar is located radially and precisely. Turning tools are carried on the gang slide and can always contact the material very closely. The movement of the spindle and the supply of the guide bush offer continuous feeding.
What Does a Swiss Lathe Do?
A Swiss lathe was originally developed for the watchmaking industry; it is able to create small, highly detailed, and complex parts with exceptional accuracy. It features a sliding headstock and a guide bushing that supports the workpiece close to the cutting tool, minimizing deflection and vibration. This design enables the lathe to produce long, slender components with tight tolerances, commonly applied for medical, aerospace, electronics, automotive, firearms, and musical instruments. Swiss lathes can perform multiple operations like turning, drilling, threading, and milling in a single setup, often automated through CNC technology, which ensures consistent, repeatable, and efficient production of intricate parts such as surgical instruments, aerospace fasteners, fuel injector nozzles, electronic connectors, and custom prototypes.
Swiss-Type Lathe vs CNC Lathe (Swiss Turning vs Conventional Turning)
The Swiss-type CNC lathes have lots of different components and structures compared to the regular CNC lathe machines, which leads to differences between Swiss turning (machining) and the conventional turning process.
1. Headstock and Material Support
Swiss-type CNC lathes feature a movable headstock, which allows the bar stock to slide through the machine smoothly. This design supports the workpiece close to the cutting area, preventing bending or wobbling during machining. In contrast, conventional CNC lathes have a fixed headstock where the workpiece is clamped firmly, often supported by a tailstock on one end. This setup works well for shorter or sturdier pieces but can lead to instability and deflection when working with long, thin parts.
2. Guide Bushing and Workpiece Stability
One of the key differences lies in how each machine stabilizes the workpiece. Swiss lathes use a guide bushing near the cutting point, which supports the bar stock closely as it passes through. The collet holding the material slides behind this guide, allowing the cutting tools to operate extremely close to the support, which prevents bending and ensures very tight tolerances, even for long parts. Conventional lathes, however, hold the workpiece only in the spindle collet, which is farther from the cutting area, making it prone to deflection and less precise for slender or elongated components.
3. Axis Capability and Machining Complexity
Swiss-type CNC machines usually have more axes—often five or more—that synchronize to perform multiple machining operations in a single setup. This multi-axis control allows the machine to create complex parts by cutting, drilling, and shaping without needing to stop or reset. Conventional CNC lathes generally have fewer axes (three or four) and often require separate steps for roughing and finishing, resulting in longer processing times and increased setup complexity.
4. Cycle Time and Efficiency
Because Swiss lathes can combine many processes into one continuous cycle, they significantly reduce the time needed to complete complex parts. This efficiency is especially noticeable when manufacturing small, intricate components. On the other hand, traditional CNC lathes, which often perform machining in multiple stages, tend to have longer cycle times, making them less efficient for detailed or high-precision work.
5. Coolant Usage
The type of coolant used also differs between the two machines. Conventional CNC lathes commonly use water-based coolants to keep the cutting tools and workpieces cool. Swiss-style lathes prefer oil-based coolants, which provide better lubrication and cooling for the highly precise and delicate machining they perform, helping maintain sharpness and accuracy.
6. Programming Differences
Programming these machines requires different approaches, especially concerning axis offsets. Swiss-style lathes use a “plus” offset on the Z-axis for operations like turning long lengths or drilling deep holes, which is the opposite of conventional lathes that use a “minus” offset.
7. Precision and Thermal Stability
Swiss-type CNC lathes excel in delivering ultra-high precision, often achieving tolerances around ±0.0002 inch. They are designed to maintain thermal stability, ensuring measurements stay consistent even as the machine heats up during operation. This makes them ideal for industries like aerospace and medical device manufacturing, where exact dimensions are critical. Conventional lathes typically have lower precision, about ±0.005 inch, generally suitable for parts that do not require such stringent accuracy.
8. Cost and Maintenance
Swiss CNC lathes come with advanced technology and intricate components, which means they are more expensive to buy and require detailed, careful maintenance. On the flip side, conventional CNC lathes have simpler structures, making them easier and more affordable to maintain. For many manufacturers, this makes conventional lathes a more budget-friendly option when ultra-high precision is not essential.
9. Industry Applications
Swiss-type CNC lathes are preferred in sectors that demand miniature, highly precise parts and where multiple machining steps need to be combined into one seamless process. Industries such as aerospace, medical device production, and electronics benefit greatly from their capabilities. Meanwhile, conventional CNC lathes are widely used in general manufacturing for producing larger, less complex parts that require medium levels of precision, offering a cost-effective and flexible solution for many applications.
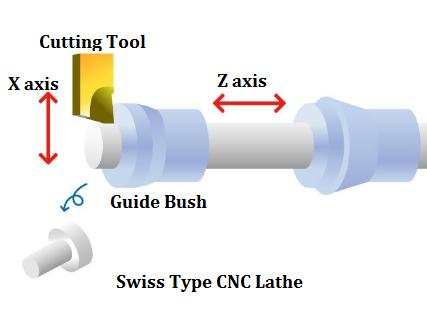
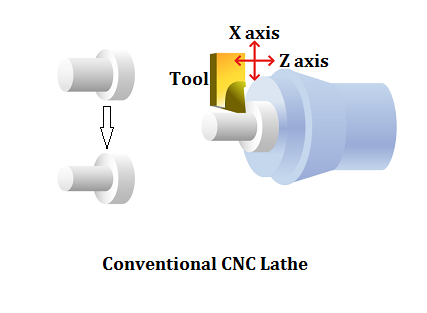
Main Parts of Swiss Lathes/Turning Machines
- Main Spindle: The main spindle holds and rotates the workpiece at high speeds, providing the kinetic energy for cutting tools to shape the material precisely.
- Sub-Spindle: The sub-spindle machines the backside of the workpiece simultaneously with the main spindle, allowing for complex parts to be made in a single setup.
- Tool Headstock: The tool headstock houses and moves multiple cutting tools simultaneously, using a sliding headstock design for rigid and accurate workpiece support.
- Guide Bushing: The guide bushing supports and guides the workpiece close to the cutting area, ensuring stability and precision, especially for long, slender parts.
- Cross-Slide: The cross-slide moves cutting tools laterally with smooth, rigid motion, enabling precise control over machining operations.
- Turret: The turret holds multiple tools and rotates to quickly position the required tool, enhancing efficiency and reducing setup times.
- Bar Feeder: The automatic bar feeder continuously supplies raw bar stock to the machine, enabling uninterrupted production without manual loading.
- Control Panel: The CNC control panel serves as the machine’s interface, allowing operators to program and control machining parameters and tool paths for automated precision.
- Coolant System: The coolant system lubricates cutting tools and dissipates heat during machining, preserving tool life and improving product quality.
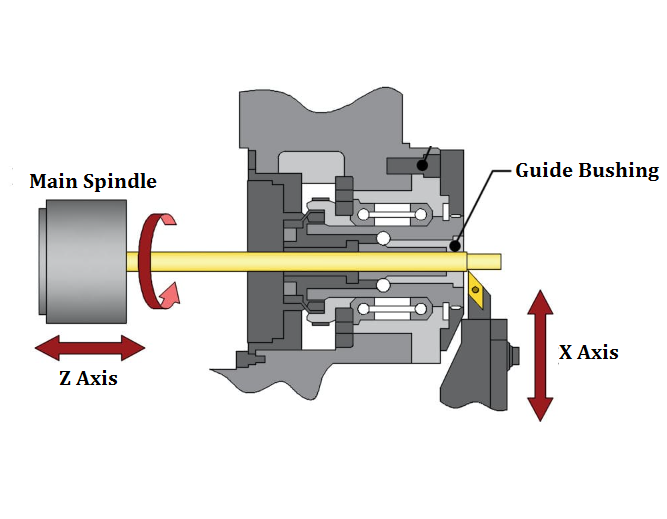