Did you know? The base of Tesla’s vehicle bodies is made from an improved A356 aluminum alloy casting. A356 is arguably the king of casting aluminum alloys – a well-balanced alloy known for its excellent castability, high strength, toughness, and corrosion resistance. If you want to learn about the best casting materials, we recommend starting with this aluminum alloy. This article provides a detailed overview of A356 aluminum specification, including its chemical composition, applications, physical and mechanical properties, equivalent, and its differences from another common aluminum alloy, 6061.
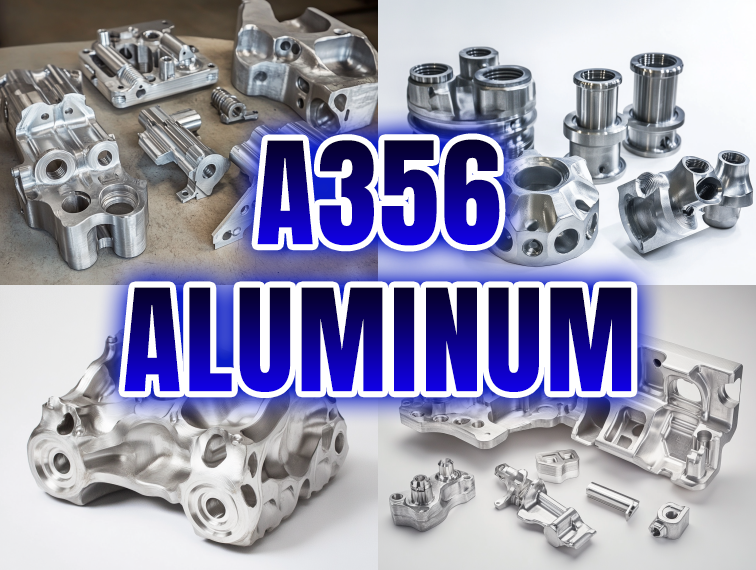
What is A356 Aluminum Alloy?
A356 aluminum is a typical aluminum-silicon alloy, widely used in the die-casting industry. The naming of the A356 aluminum alloy is related to its classification in the American Society for Testing and Materials (ASTM) standards. According to ASTM, the A356 aluminum alloy is part of the standard series under the Aluminum Association standards and belongs to the 356 series. This series includes A356.0, A356.1, A356.2, and other specific grades of aluminum alloy. In the ASTM B26 standard, A356 is a high-strength aluminum alloy, with suffixes like T6 indicating specific heat treatment processes, namely solution treatment followed by a complete artificial aging solution treatment. Therefore, the naming of A356 aluminum alloy originates from its classification and numbering system in the ASTM standards, where “A” represents aluminum alloy, and “356” is a specific grade, used to distinguish different aluminum alloy materials. This naming method ensures the standardization and consistency of aluminum alloy materials, facilitating their identification and use in industrial applications.
A356 Aluminum Equivalent
Standards and specifications for A356 aluminum equivalent in different countries include:
- U.S. Standard: ASTM A356/A356M-2005
- Japanese Standard: JIS H5202 AC4C
- German Standard: DIN 1725.2 G-AlSi7Mg
- International Standard: ISO 3522
These standards and specifications ensure the quality and performance stability of A356 aluminum alloy in various countries.
A356 Aluminum Chemical Composition
The chemical composition of the casting aluminum alloy ingots is governed by ASTM specifications for A356 material:
Element | Composition (wt%) |
---|---|
Cu | ≤0.10 |
Si | 6.5~7.5 |
Mg | 0.25~0.45 |
Zn | ≤0.10 |
Fe | ≤0.20 |
Mn | ≤0.10 |
Ni | ≤0.05 |
Ti | ≤0.20 |
Pb | ≤0.05 |
Sn | ≤0.05 |
Cr | ≤0.05 |
Other | other |
A356 Aluminum Properties
To give you a better understanding of the performance of A356 material, we will use two tables to illustrate its physical characteristics and mechanical properties respectively:
A356 Physical Properties
The physical properties of A356 are listed in the table below:
Property | A356 Material |
---|---|
Density (Mg/m³) | 2.64 |
Liquidus Temperature (℃) | 610 |
Solidus Temperature (℃) | 555 |
Linear Expansion Coefficient (20℃ x 10⁻⁶/℃) | 21.5 |
Linear Expansion Coefficient (20~200℃ x 10⁻⁶/℃) | 22.5 |
Linear Expansion Coefficient (30~300℃ x 10⁻⁶/℃) | 23.5 |
Thermal Conductivity (W/m·℃) | 159 |
Specific Heat (J/kg·℃) | 963 |
When considering carbon neutrality and the subsequent shift to electric vehicles, one characteristic that comes to mind is thermal conductivity. A356 alloy has better thermal conductivity compared to other aluminum materials. Additionally, A356 alloy has good corrosion resistance, which also reduces thermal shielding from oxidation. Therefore, I believe A356 alloy is a good choice for products requiring heat dissipation.
A356 Mechanical Properties
The mechanical properties vary significantly depending on whether heat treatment is applied, so each material lists properties for both F and T6 conditions. You can see that materials treated with T6 have higher strength than those without heat treatment (F). Additionally, A356 with T6 treatment improves elongation.
Property | A356-F Material | A356-T6 Material |
---|---|---|
Yield Strength (MPa) | 95 | 260 |
Tensile Strength (MPa) | 160 | 260 |
Elongation (%) | 10.7 | 16.8 |
Hardness (HB) | 55 | 70 |
These values are measured under different casting methods, and specific values may vary depending on casting methods, heat treatment, and other factors. Factors affecting the mechanical properties of A356 aluminum alloy include:
- Distribution and size of eutectic silicon particles: Fine and evenly distributed eutectic silicon particles can improve the alloy’s microstructure, thereby enhancing mechanical properties.
- Casting method: Liquid and semi-solid extrusion casting can significantly reduce casting defects, enhancing the alloy’s density and improving mechanical properties.
- Thermal conductivity: Factors such as the integrity of the alloy’s crystal structure, dislocation density, and grain boundary area can affect thermal conductivity and thereby influence mechanical properties.
Advantages of A356 Aluminum Alloy Material
A356 aluminum alloy offers several significant advantages, making it widely used in industrial and manufacturing sectors. Here are some detailed descriptions of its main advantages:
- Excellent castability: A356 aluminum alloy exhibits excellent flow properties, no tendency for hot cracking, small linear shrinkage, and good airtightness, all of which make it perform well in casting processes.
- Lightweight yet robust: The alloy’s low specific gravity combined with high specific strength and stiffness makes it very suitable for applications requiring weight reduction while maintaining high strength, such as automotive lightweighting.
- Corrosion resistance and wear resistance: A356 aluminum alloy maintains stability and durability under various environmental conditions due to its good corrosion and wear resistance.
- Easy to machine and weld: This aluminum alloy is easy to gas weld and heat treat (such as T5 and T6 states), further enhancing its mechanical properties through these processes.
- Excellent overall mechanical performance: A356 aluminum alloy not only has good castability but also possesses high comprehensive mechanical properties, including tensile strength, elongation, and fatigue strength.
- Cost-effectiveness: Compared to some other materials, A356 aluminum alloy is reasonably priced and consumes less energy during production, thus offering economic benefits in large-scale production.
- Compatibility with advanced manufacturing technologies: By using advanced manufacturing techniques such as vacuum low-pressure lost foam casting and cast-forging composite forming, the performance and application range of A356 aluminum alloy can be further enhanced.
Applications of A356 Aluminum Alloy Material
The main uses of A356 aluminum alloy are very diverse, including the following aspects:
- Automotive manufacturing: Due to its excellent castability, high specific strength, and corrosion resistance, A356 aluminum alloy is widely used in the production of various automotive parts, such as engine cylinder heads, slider components, and wheel hubs. Additionally, A356 aluminum alloy is also used in manufacturing automotive transmissions, pulleys, fuel tanks, and other components.
- Aerospace: Due to its low density, formability, and good corrosion resistance, A356 aluminum alloy is also extensively used in aerospace manufacturing. It can be used to manufacture aerospace pump components, aerospace connectors, and other high-strength stress mechanical parts.
- Other mechanical tool parts: A356 aluminum alloy is also used to manufacture various housings, brackets, and volutes that require the highest heat resistance and support stress.
- New energy vehicles and the electronics industry: With the development of new energy vehicles, A356 aluminum alloy has also been applied in the fields of new energy vehicle motor housings, robots, and more.
A356 Aluminum vs 6061: What are Differences Between Them?
A356 and 6061 are two commonly used aluminum alloys, and they differ in composition, performance, and application areas. Here are detailed introductions to the characteristics and differences of these two aluminum alloys:
- Composition:
- A356 aluminum alloy is an Al-Si binary alloy, with magnesium added to form the strengthening phase Mg2Si, significantly enhancing the alloy’s age-hardening capability and improving mechanical properties through heat treatment.
- 6061 aluminum alloy contains magnesium and silicon, offering good machinability, welding characteristics, plating properties, corrosion resistance, and toughness.
- Performance:
- A356 aluminum alloy exhibits good castability, such as good fluidity, small linear shrinkage, no hot cracking tendency, and excellent airtightness. Through heat treatment, it can achieve higher strength, good plasticity, and high impact toughness.
- 6061 aluminum alloy has medium strength, good plasticity, and excellent corrosion resistance, especially no tendency for stress corrosion cracking. It has excellent machinability, welding characteristics, plating properties, good corrosion resistance, high toughness, and does not deform after processing, ensuring dense material with no defects, and is easy to polish, color, and achieve excellent oxidation effects.
- Manufacturing processes:
- A356 aluminum alloy is typically produced by casting methods, making its forming state cast, with relatively poor weldability.
- 6061 aluminum alloy is often produced by extrusion forming, with higher purity and better weldability.
- Application areas:
- A356 aluminum alloy is mainly used for automotive casting wheel hubs, aerospace pump parts, aerospace connectors, automotive transmissions, pulleys, fuel tanks, and other mechanical tool parts requiring the highest heat resistance and support stress.
- 6061 aluminum alloy, due to its good mechanical properties and machinability, is widely used in construction, automotive, aerospace, and other fields, especially in products requiring high strength and good weldability.