In the symphony of machining operations, the art of grooving stands as a distinct and harmonious melody, executed with finesse on the grand stage of a lathe machine. Just as a conductor meticulously directs an orchestra, the operator orchestrates the lathe grooving tool to sculpt intricate designs and functional features into workpieces. In this exploration, we delve into the intricacies of grooving operations, unraveling the facets of grooving, the lathe grooving tool, the methodology behind grooving operations, and the orchestration of this fine-tuned performance.
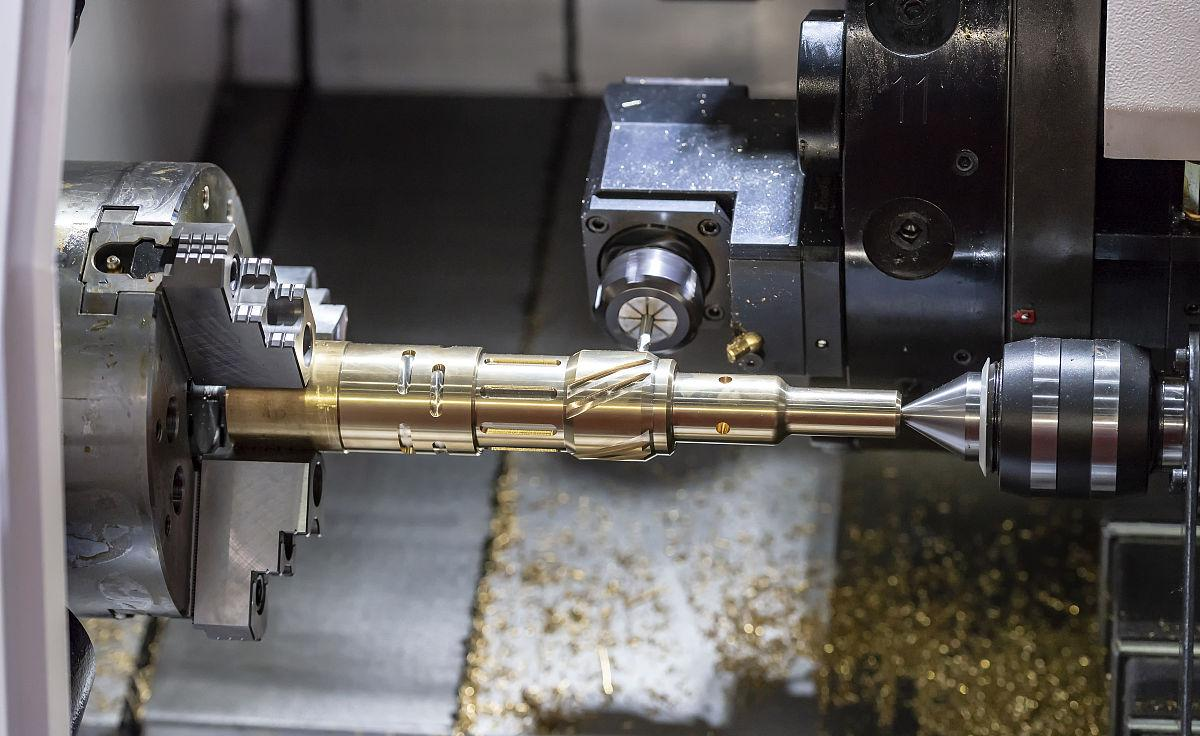
What is Grooving?
Imagine a craftsman etching their mark onto a canvas, infusing it with character and distinction. Similarly, grooving in machining is the act of cutting a channel or groove into a workpiece, a process that bestows both aesthetics and functionality. Just as a river winds its way through landscapes, grooves serve as pathways for fluid flow, structural engagement, or aesthetic embellishment in diverse applications, from automotive components to artistic engravings.
The Choreography of Grooving Operations in Lathe Machines
What is the grooving operation in the lathe machine? Grooving is a machining operation performed on a lathe machine to create a narrow, linear cut or groove on the surface of a workpiece. This operation is used to produce features such as keyways, oil grooves, snap ring grooves, threads, and other similar components that require precise and controlled cuts.
The grooving operation involves using a specially designed cutting tool called a grooving tool or parting tool. This tool typically has a sharp cutting edge that is perpendicular to the workpiece’s rotation axis. The tool is advanced radially into the workpiece, creating the desired groove width and depth.
Here’s a basic overview of the grooving operation on a lathe machine:
1. Workpiece Mounting: The workpiece, which could be a cylindrical shaft or rod, is securely mounted in the lathe’s chuck or collet. The chuck or collet holds the workpiece and rotates it around its axis.
2. Tool Setup: The grooving tool is mounted in a tool holder and positioned at the desired height and angle relative to the workpiece. The tool’s cutting edge needs to be aligned properly to ensure accurate groove dimensions.
3. Tool Engagement: The lathe is set to the appropriate rotational speed for the material being machined. The grooving tool is advanced radially into the workpiece, cutting a narrow groove along the desired path.
4. Feed and Depth: The feed rate and depth of cut are carefully controlled to achieve the desired groove dimensions. The tool is gradually fed into the workpiece, and the lathe’s cross-slide or compound slide is used to control the depth of cut.
5. Coolant/Lubrication: Depending on the material being machined and the specific setup, coolant or cutting fluid might be used to keep the tool and workpiece cool, reduce friction, and aid in chip evacuation.
6. Finishing and Parting: Once the groove is complete, the grooving tool can be retracted, and the lathe’s feed and depth settings can be adjusted for the next groove or parting operation if necessary. Parting is a similar operation where the tool is used to cut off a section of the workpiece, effectively separating it from the rest.
Step onto the stage of a machining workshop, and the centerpiece is often a lathe machine. This mechanical virtuoso rotates the workpiece, while the lathe grooving tool moves in synchrony, cutting into the material. The depth, width, and contour of the groove are determined by precise movements, just as a dancer’s choreography shapes the performance. The operator deftly maneuvers the lathe grooving tool along predefined paths, sculpting the desired groove with skillful precision.
Lathe Grooving Tool: The Maestro’s Baton
A lathe grooving tool, also known as a parting tool or grooving insert, is a cutting tool specifically designed for the grooving operation on a lathe machine. It’s used to create narrow grooves, slots, and cut-offs on the surface of a workpiece. This tool is characterized by its sharp cutting edge and perpendicular orientation to the workpiece’s rotational axis. Here are the key features and components of a lathe grooving tool:
1. Tool Holder: The grooving tool is usually held in a tool holder that attaches to the lathe’s tool post or turret. The tool holder provides stability and allows for easy adjustment of the tool’s position.
2. Cutting Edge: The most important part of the grooving tool is its cutting edge. The cutting edge is ground to be sharp and is positioned perpendicular to the workpiece’s rotation. This edge comes into contact with the workpiece, creating the groove.
3. Insert: In many modern applications, the cutting edge is made using replaceable carbide or ceramic inserts. These inserts offer consistent cutting performance and are designed to be easily replaced when they become dull. The inserts are available in various sizes and geometries to suit different groove widths and materials.
4. Geometry: Grooving tools can have different insert geometries depending on the desired groove width, depth, and the material being machined. There are grooving inserts with various chip breaker designs and relief angles to optimize chip evacuation and cutting performance.
5. Coolant Channels: Some grooving tools or inserts are designed with built-in channels to facilitate the flow of cutting fluid or coolant. This helps to keep the tool and workpiece cool, improves chip evacuation, and prolongs tool life.
6. Holder Adjustments: The tool holder may have features that allow for adjusting the height and position of the tool relative to the workpiece. This is important for achieving accurate groove dimensions and maintaining proper cutting conditions.
7. Clamping Mechanism: Grooving tool inserts are typically secured in the tool holder using clamping screws or mechanisms. This ensures that the insert remains securely in place during the machining process.
8. Tool Overhang: It’s important to consider the tool overhang (the distance from the tool holder to the cutting edge) when setting up the grooving tool. Excessive overhang can lead to tool chatter, poor surface finish, and decreased tool life.
9. Material Compatibility: The choice of grooving tool and insert material depends on the type of material being machined. Carbide inserts are commonly used for a wide range of materials due to their hardness and wear resistance.
As a painter wields a brush, a machinist wields a lathe grooving tool, a tool meticulously designed for precision and control. These tools come in various shapes and sizes, each tailored to carve out a specific groove profile. With geometries ranging from square to round, and cutting edges designed to chip away material with utmost accuracy, the lathe grooving tool is the maestro’s baton that transforms raw material into a work of art. Using the appropriate grooving tool and insert, along with proper machining parameters and techniques, ensures accurate and efficient grooving operations on a lathe machine.
Harmonizing Depth and Width: The Dynamics of Groove Dimensions
The dimensions of a groove, much like the tempo in a musical piece, significantly influence the final outcome. Groove depth and width are carefully orchestrated to balance structural integrity, functional requirements, and aesthetic appeal. A deep groove might enhance fluid flow, while a shallow but wide groove can offer ample space for retaining seals. The lathe grooving tool, guided by the operator’s expertise, cuts through the material with harmonious precision, ensuring these dimensions are in perfect cadence.
Material Matters: The Ballet of Machining Materials
Just as different instruments contribute to diverse musical compositions, various materials demand specific machining approaches. Grooving operations span an array of materials, from metals like steel and aluminum to exotic alloys and even non-metals like plastics. The lathe grooving tool, akin to a virtuoso musician who adapts their technique to suit the melody, adjusts its cutting parameters to gracefully glide through the material, leaving behind a meticulously crafted groove.
The Grand Overture: Approaches to Grooving
Grooving operations offer a spectrum of approaches, much like musical overtures that set the tone for a symphony. External grooving carves the outer surface, internal grooving navigates within the material, and facing grooves span the breadth of the workpiece. Each approach demands finesse and precision from both the operator and the lathe grooving tool, transforming a plain workpiece into a masterpiece of contours and functionality.
Tool Selection and Geometry: Crafting the Right Notes
Selecting the appropriate lathe grooving tool is akin to a composer selecting instruments for an ensemble. The tool’s geometry, including cutting edge angles and relief angles, influences chip formation, heat dissipation, and cutting forces. Just as the choice of instruments shapes the sonic landscape, the lathe grooving tool’s geometry shapes the cutting landscape, ensuring a harmonious interaction between tool and workpiece.
Unveiling the Performance: Surface Finish and Integrity
A symphony’s beauty lies not only in the melodies but also in the harmonious blending of its elements. Similarly, a groove’s beauty is reflected in its surface finish and integrity. Smooth surface finishes enhance aesthetics and minimize friction, while precise cutting depths ensure structural integrity. The lathe grooving tool’s finesse, guided by the operator’s expertise, creates grooves that seamlessly integrate functionality and artistry.
Beyond Machining: Grooving as an Art Form
Just as an artist’s creation resonates with emotions, a grooving operation in a lathe machine resonates with engineering prowess. Beyond the realm of pure functionality, grooving embraces creativity and innovation. Intricate patterns, embossed logos, and decorative engravings transform machined components into artistic expressions, revealing the multidimensional nature of grooving operations.
Crafting Excellence Through Grooving
In the grand tapestry of machining, grooving emerges as a finely tuned performance that marries precision with artistry. The lathe grooving tool, akin to a master musician’s instrument, collaborates with the operator’s skill to carve out channels of functionality and elegance. With grooves that channel fluids, create structural engagements, or manifest artistic expressions, this operation transforms raw materials into purposeful and captivating creations. As we conclude our exploration, let us appreciate the intricate choreography of grooving operations, where the lathe machine becomes a stage, the operator a conductor, and the grooves themselves, a mesmerizing symphony of craftsmanship.