“MJF” stands for “Multi Jet Fusion,” which is an abbreviated term for a specific additive manufacturing technology used in HP’s 3D printers. MJF has gained popularity in recent times compared to other 3D Printing methods, it enables the transition from rapid prototyping to direct manufacturing of final products. This technology allows for the production of robust and highly detailed end products while maintaining high productivity. In this discussion, we will explore what is Multi Jet Fusion, how it works and why it is suitable for mass production, the level of precision it can achieve, and highlight its features and recommended applications by comparing actual samples.
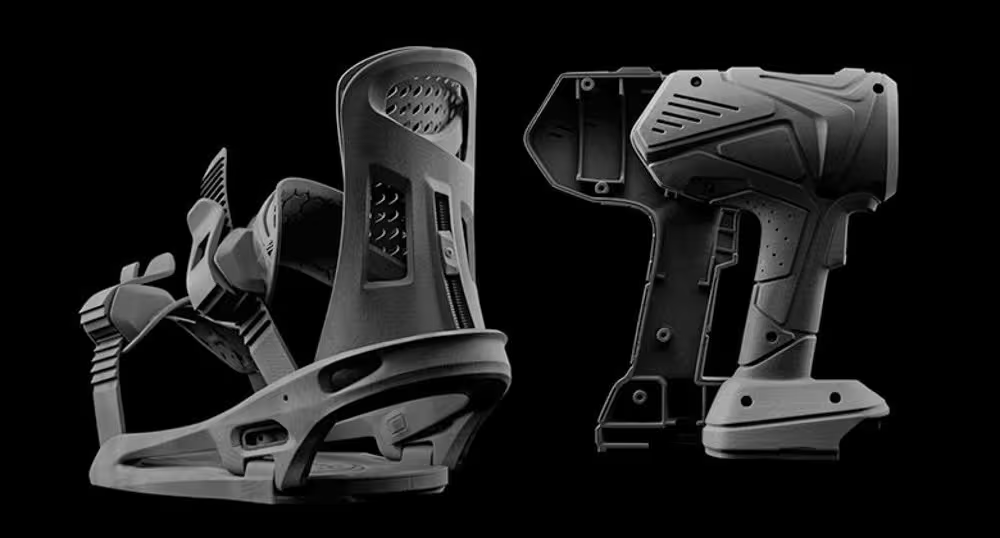
What is Multi Jet Fusion 3D Printing?
Multi Jet Fusion (MJF) is an additive manufacturing technology developed by HP Inc. It is a 3D printing method that involves layering powdered thermoplastic materials to rapidly manufacture intricate and complex parts. In MJF, a thin layer of powdered material, typically a thermoplastic polymer, is spread over a build platform. Then, an inkjet array selectively deposits a fusing agent onto the powdered material, which enables the fusion process. A detailing agent is also applied to improve the surface finish. After each layer is printed, a heating element passes over the entire bed, causing the powdered material to fuse and solidify. This process is repeated layer by layer until the final object is formed. It enables the production of fast, robust, and highly detailed final products. In comparison to traditional 3D printing methods, it significantly improves productivity and reduces costs.
Multi Jet Fusion Features & Advantages
The biggest advantage of MJF is that it allows designers to achieve the desired shape without constraints imposed by the manufacturing process, while still meeting the required strength, uniformity, and robustness for the final product. Furthermore, MJF is specifically designed for mass production, ensuring that the production efficiency remains high even when producing large quantities, while consistently maintaining high-quality parts.
By combining the unique fabrication method of MJF with the capabilities of 3D printing technology, it brings new value to the manufacturing and creative industries.
Key benefits of MJF include:
- Ability to mass-produce custom-made products.
- Quick transition to the production process with just 3D data.
- Manufacture from prototypes to final products without the need for traditional factories.
- Cost reduction and shorter lead times compared to conventional cutting or injection molding methods.
- Capability to produce complex shapes as a single piece, reducing assembly efforts.
- Minimal variation in strength due to isotropy.
- High material reusability, with the need for additional material only when reusing for the next production (in the case of PA12).
- High airtightness, making it suitable for producing parts without air leaks and for pneumatic applications.
- MJF (Multi Jet Fusion) manufacturing method also contributes to sustainability. It recycles and reuses a significant portion of the unused powdered material during the manufacturing process. With precise heat control using two types of agents, it achieves an industry-leading recycling rate of up to 80% (for PA12). Additionally, PA11 is derived from plant-based materials, making it an environmentally friendly option.
Not only MJF, but 3D printed products, in general, align with the concept of sustainable production by enabling manufacturing only when needed, using the necessary materials, and producing as much as required.
MJF Disadvantages
While MJF can achieve cost-effectiveness in terms of per-part manufacturing cost, the initial investment cost (equipment acquisition cost) is relatively high, which may result in higher overall costs depending on the frequency of printing.
HP Multi Jet Fusion Price
The price of HP Multi Jet Fusion 3D printers can vary depending on the specific model and configuration, as well as any additional accessories or options. As of my knowledge cutoff in September 2021, HP Multi Jet Fusion printers range in price from approximately $50,000 to several hundred thousand dollars. However, prices can change over time, so it’s recommended to check with HP or authorized resellers for the most up-to-date pricing information.
MJF Materials – What Materials are Compatible with Multi Jet Fusion Method?
The mainstay material for MJF (Multi Jet Fusion) is nylon, particularly polyamide (PA), which is suitable for the final product. The list of MJF 3D printing materials available includes:
- – PA11: A plant-derived nylon material with excellent flexibility, with higher toughness compared to PA12.
- – PA12: A versatile low cost nylon material with excellent strength and physical properties that can be used for various applications.
- – PA12GB (Glass Beads): A enhanced nylon material of PA12 that provides superior stiffness compared to PA12, with glass beads incorporated.
- – PA12W (White): A white nylon material with excellent design aesthetics, suitable for various environments.
MJF Modeling Process – How Does Multi Jet Fusion Work?
MJF (Multi Jet Fusion) follows a process consisting of four main steps, allowing for strong and high-precision 3D printing. This process is executed rapidly. Here are the steps:
Step 1: Powder Bed Preparation
Fine powdered thermoplastic material is laid down across the entire printing area.
Step 2: High-Speed Inkjetting of Agents
The inkjet head, integrated into the 3D printer, rapidly moves across the printing area, dispensing two different types of ink agents unique to HP’s technology:
- – Fusing Agent: A dissolution promoter
- – Detailing Agent: A surface decorating agent
These agents play crucial roles in the printing process. The Fusing Agent facilitates powder fusion, while the Detailing Agent prevents fusion, achieving precise control in the printing process.
Step 3: Thermal Energy Application using a Lamp
After the ink agents are deposited, a halogen lamp applies thermal energy over the entire printing area to melt and fuse the powdered resin. Temperature sensors located on top of the printer ensure precise temperature control for quality management. By effectively providing thermal energy and achieving fast melting and fusion, MJF produces 3D printed products with excellent toughness, strength, and impact resistance.
Step 4: Iterative Layering Process
The aforementioned steps (1-3) are rapidly repeated, layer by layer, to manufacture the solid 3D object. Additionally, as the unused powdered material remains in powder form and is not turned into a printed part, there is minimal material waste. This makes MJF a highly sustainable 3D printing method.
MJF Finishing – What Post-Processing Methods are Required for Multi Jet Fusion?
MJF does not require support structures (structures solely for supporting the object during printing that are removed afterward), making post-processing relatively simple. As mentioned earlier, MJF leaves unused powder material surrounding the printed object, which serves as the support. This eliminates the need for special materials or structures dedicated to support. Therefore, it is possible to create the desired shape based on the designer’s original design.
After the cooling stage, the remaining powder is removed through processes like bead blasting, air blasting, or water jet blasting. Manual post-processing, such as polishing, can also be done using tools or machines like tumblers.
MJF Applications – What are Multi Jet Fusion Used For?
One of the significant features of MJF is its ability to achieve the high strength and precision required for industrial products through 3D printing. As a result, it can be used for a wide range of applications, including functional prototyping, design evaluation, factory tooling, and final product manufacturing. Moreover, due to its high printing speed, MJF is well-suited for both medium-scale production and large-scale production exceeding tens of thousands of units.
Why MJF is suitable for final products? Since 3D printed products are manufactured by laminating layers, it was considered that they were not suitable for the final product level due to variations in strength in the lamination direction. MJF has been able to eliminate these issues by minimizing this variation in strength (anisotropy). It becomes possible to manufacture products that effectively utilize the material properties of nylon materials. In particular, “PA12W White”, which has been introduced in recent years, can be used not only for dyeing purposes, but also as parts with high design qualities even after modeling.
Why MJF is suitable for mass production? The challenges when using 3D printers for mass production were productivity and production cost per unit. MJF has both printing speed and production efficiency that could not be achieved with conventional 3D printers, and has succeeded in greatly improving productivity. By increasing productivity, production costs for each part can be reduced.
MJF Applications by Industry
MJF is unique in its use in industries with high standards, such as the automotive industry and medical technology. Now, let’s take a look at examples of MJF utilization by industry both domestically and internationally.
- Dental/medical industry: prototype of personalized aligners – Orthodontic aligners (mouthpieces) must be personalized to each patient’s oral environment. At the same time, we are able to provide 400 tooth profiles and 50,000 mouthpieces per day with short delivery times and low costs.
- Manufacturing industry (industrial equipment): Cooling duct parts – This is an example of a cooling duct installed inside an HP printer. The parts that were previously manufactured by assembling six parts and screws have been integrated and manufactured in a shape that reflects the analysis results in order to create the optimal air flow. This reduces manufacturing costs by 34% and increases airflow by 22%. Additionally, by printing the required amount at the required time, we are able to review parts inventory management and improve total costs.
- Aerospace industry: Prototype – PA12GB MJF 3D Printing even can be used for their satellite prototype. 3D printed objects are used not only to check mechanical designs, but also as communication tools with internal members.
MJF (Multi Jet Fusion) is HP’s proprietary 3D printing technology that can create products suitable for final production and large-scale manufacturing. It offers excellent strength and can be utilized not only in the manufacturing industry but also in a wide range of sectors such as healthcare, aerospace, and space industries, among others. The appeal of 3D printing lies in the ability to freely fabricate desired objects in the desired quantities. Utilize the features of MJF and explore your own unique applications.