Peck Drilling is an effective method for improving chip removal, cooling, and hole accuracy in metal processing. It is widely used in CNC machining, particularly for deep holes and hard materials. By selecting the appropriate drill cycle (G81, G73, or G83) and adjusting parameters like peck depth and feed rate, machinists can optimize performance while extending tool life. For those in the metalworking industry, incorporating Peck Drilling into machining strategies can lead to cleaner, more precise holes and better tool longevity. Today, we want to do a depth explanation for this CNC drilling technique by breaking down Peek Drilling meaning, Cycle G Codes, Uses, Depth Control, and Work Program examples.
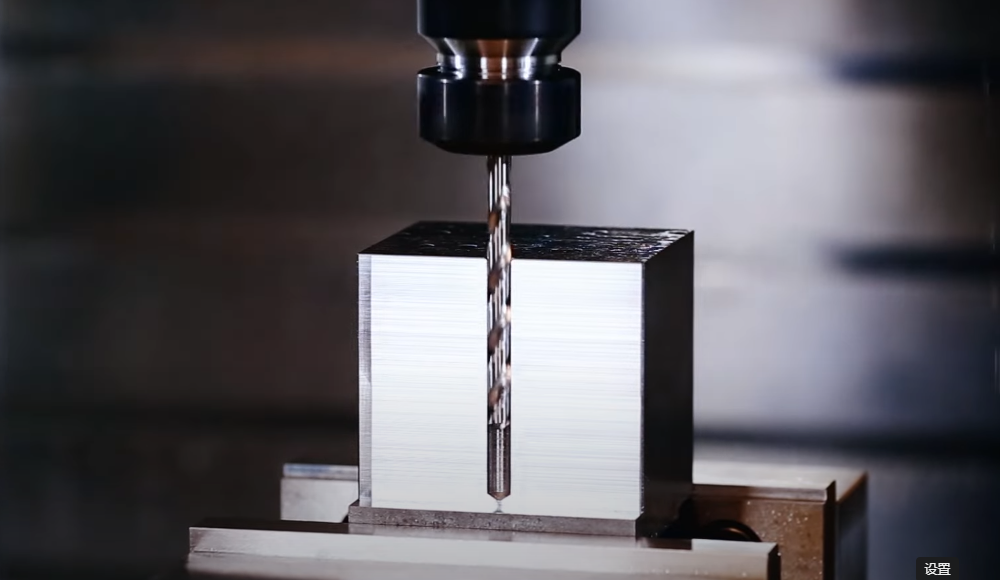
What is Peck Drilling?
Peck Drilling, also called pecking drilling, is a machining technique used to drill deep and precise holes. Instead of continuously advancing into the material, the drill bit retracts intermittently, clearing chips and reducing heat buildup. This method prevents chip clogging, excessive tool wear, and thermal damage, making it ideal for deep hole machining and high-precision applications.
Advantages of Peck Drilling
Peck Drilling offers several benefits that improve machining efficiency and accuracy:
- Effective Chip Removal – Prevents chips from clogging the hole, ensuring a smooth drilling process.
- Heat Reduction – Intermittent retraction allows cooling fluid to reach the cutting edge, reducing thermal damage.
- Improved Hole Quality – Clearing chips prevents surface roughness and enhances dimensional accuracy.
- Extended Tool Life – Reducing heat and chip accumulation minimizes wear, leading to longer drill bit lifespan.
Despite these benefits, Peck Drilling slightly increases machining time compared to continuous drilling, making it important to balance efficiency with quality.
Limitations of Peck Drilling
While Peck Drilling improves machining quality, it has some drawbacks:
- Longer Machining Time – Intermittent retraction adds extra movements, increasing total drilling time.
- Higher Tool Requirements – Drill bits must have high strength and toughness to endure repeated retractions.
- Operational Complexity – Requires precise control of peck depth and frequency to achieve optimal results.
Despite these challenges, Peck Drilling remains a valuable technique for applications demanding precision, chip control, and deep hole accuracy.
When to Use Peck Drilling?
Peck Drilling is useful in situations where chip evacuation, heat control, and precision are critical. It is often applied in:
- Deep Hole Machining – When a hole is too deep to be drilled in a single pass.
- Chip Breaking – Especially for harder materials where long chips can cause tool breakage.
- Chip Removal – Prevents chips from accumulating in the drill flutes.
- Cooling and Lubrication – Improves coolant access to the cutting edge.
- Breakthrough Control – Ensures better control when the drill exits the material.
Industries such as aerospace, automotive, and precision machining frequently rely on Peck Drilling for engine components, gearboxes, molds, and optical parts.
Applications of Peck Drilling
Peck Drilling is widely used in industries that require deep hole machining, such as:
- Aerospace – Aircraft engine components and structural parts require precise deep holes.
- Automotive Manufacturing – Engine blocks, gearboxes, and other parts benefit from controlled drilling.
- Precision Machining – Molds, optical components, and other high-accuracy parts demand clean, accurate holes.
This technique is particularly effective for hard materials where chip control is a challenge and for situations where coolant access is limited.
How Peck Drilling Works?
Peck Drilling follows a cyclic process that consists of several stages:
- Initial Drilling – The drill bit starts cutting into the material, generating chips.
- Retraction – After reaching a certain depth, the drill bit pulls back slightly, allowing chips to be removed.
- Cooling and Cleaning – This retraction action improves coolant access and prevents chip clogging.
- Re-drilling – The drill resumes cutting deeper into the material, repeating the cycle until the desired depth is reached.
The depth and frequency of retraction are key factors that must be adjusted based on material type and hole depth. If the retraction is too shallow, chips may not be effectively cleared. If it’s too deep, machining time increases unnecessarily. Additionally, the drill bit must be strong enough to withstand continuous forward and backward movements, requiring careful tool selection.
What is Peck Drilling Cycle?
The Peck Drilling Cycle involves drilling in increments instead of a single continuous motion. The cycle consists of the following steps:
- Drill Advances – The drill feeds into the material to a predefined depth (Q-value).
- Retraction – After reaching the set depth, the drill retracts to clear chips and allow coolant to reach the cutting edge.
- Cooling and Cleaning – The retraction helps flush out chips and prevents heat buildup.
- Repeat Until Final Depth – The drill continues this cycle until it reaches the required hole depth.
The depth of each peck must be carefully controlled to balance machining time and chip removal efficiency. If the increments are too small, machining becomes slow. If they are too large, chips may not clear properly.
Peck Drilling Cycle G Codes
In CNC programming, different G codes are used to control the Peck Drilling process based on the required depth and chip removal needs. The primary drilling cycles include:
G81 – Simple Drilling Cycle
- Used for shallow holes where chip removal is not a major issue.
- The drill moves in one continuous feed to the final depth.
- Not suitable for deep holes due to poor chip evacuation.
G81 Perk Drilling Cycle Example Lathe Code: N10 G99 G81 X3.5 Y5.0 R0.1 Z-1.0 F8.0
- G81 – Simple drill cycle.
- X, Y – Hole position.
- R0.1 – Retract plane.
- Z-1.0 – Final depth.
- F8.0 – Feed rate.
G73 – High-Speed Peck Drilling Cycle
- Suitable for moderate-depth holes (3D–5D).
- The drill retracts a small distance (0.5–1 mm) after each peck.
- Faster than G83 but less effective for deep holes.
G73 Perk Drilling Cycle Example Lathe Code: N20 G99 G73 X3.5 Y5.0 R0.1 Z-2.0 Q0.5 F8.0
- G73 – High-speed peck drilling.
- Q0.5 – Peck depth.
- Other parameters similar to G81.
G83 – Deep Hole Peck Drilling Cycle
- Used for deep holes (5D or more).
- The drill retracts fully to the R plane after each peck.
- Ensures better chip removal and coolant penetration.
G83 Perk Drilling Cycle Example Lathe Code: N30 G99 G83 X3.5 Y5.0 R0.1 Z-3.0 Q0.6 F8.0
- G83 – Deep hole peck drilling.
- Q0.6 – Peck depth.
- Retracts fully after each peck.
Choosing the Right Peck Drilling Cycle G Code
The choice between G81, G73, and G83 depends on hole depth and material properties:
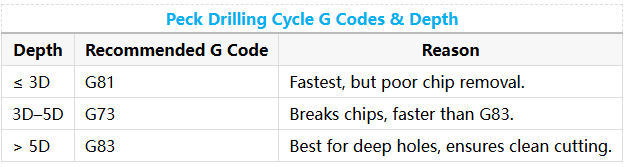
For harder materials, G83 is often preferred, even for moderate depths, as it prevents chip clogging and tool failure.
How To Control Peck Drilling Depth?
Proper depth control is essential for efficient machining and tool longevity. The Q value (peck depth) determines how much material the drill removes before retracting.
Formula for Calculating Number of Pecks
To determine the number of pecks required for a given hole depth:
Pn=Td/Q
Where:
- Pn = Number of pecks.
- Td = Total hole depth.
- Q = Peck depth.
Example Calculation:
If drilling a 1.225-inch deep hole with a 0.5-inch peck depth:
Pn=1.225/0.5=2.45
Since pecks must be whole numbers, round up to 3 pecks.
Controlling Breakthrough Depth
When drilling through materials, controlling how the drill exits the hole is important, especially for hard materials. To avoid excessive force at breakthrough:
- Reduce the final peck depth before exiting.
- Slow down feed rate near the end.
- Use a dwell time for smoother finishing.
Example Breakthrough Control Using G83: N40 G99 G83 X3.5 Y5.0 R0.1 Z-1.8 Q1.2 F6.0
- Z-1.8 – Stops just before full penetration.
- Q1.2 – Adjusted to prevent sudden breakthrough.
How To Control Peck Drilling Cycle Time?
Peck Drilling significantly impacts cycle time due to the repeated retractions of the drill bit. Each time the drill retracts, it moves a greater total distance than the actual hole depth, increasing machining time. Below, we break down how Peck Drilling cycle time is calculated and how it can be optimized.
Understanding Peck Drilling Movement
When using a standard G83 Peck Drilling cycle, the drill does not simply move straight to the final depth. Instead, it follows a repetitive pattern:
- Drill Advances – The bit moves forward by a set depth (Q-value).
- Retraction to R Plane – The drill moves back to allow chip removal and cooling.
- Repeat Until Final Depth – The process continues until the hole reaches its required depth.
This means the total distance traveled by the drill is far greater than the actual hole depth, affecting cycle time.
Example: Cycle Time in a Standard G83 Peck Drilling Cycle
Consider drilling a 2.5-inch deep hole with a Q-value of 0.5D (half the drill diameter). This results in 21 pecks to complete the hole.
- Each peck requires drilling in, retracting, and re-entering the hole.
- The total movement is nearly 60 inches to drill a 2.5-inch hole.
- With 21 entries into the material, tool wear increases.
This method is inefficient, leading to excessive cycle time and tool degradation.
Optimizing Cycle Time with G83 IJK Parameters
Instead of using a fixed Q-depth for every peck, we can improve efficiency by progressively reducing the peck depth using IJK values in G83:
- I (Initial Peck Depth): The first peck can be 3-5 times the tool diameter (D).
- J (Reduction per Peck): Each subsequent peck removes less material to reduce tool stress.
- K (Minimum Peck Depth): The smallest depth for the final pecks.
Example Optimization for a 0.25-inch Diameter Drill
- I = 4D → First peck = 1 inch (4 × 0.25).
- J = 2D → Each peck reduces by 0.5 inches (2 × 0.25).
- K = 1D → Minimum peck depth = 0.25 inches.
By switching from G83 Q to G83 IJK, the peck count drops from 21 to 7, cutting cycle time in half (from 18 seconds to 9 seconds per hole).
Comparing Cycle Speed of Different Peck Drilling Methods
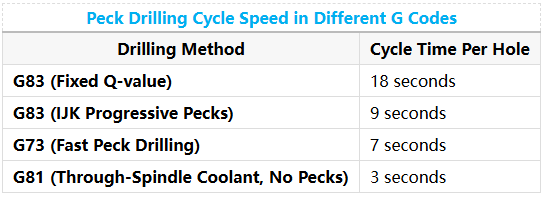
For high-production environments, G81 with Through-Spindle Coolant (TSC) is the fastest method, eliminating unnecessary retractions.
Worked Example: CNC Program with Peck Drilling
The following CNC program demonstrates a drilling sequence using different tools and peck cycles:
O2601 (Peck Drilling Example)
(T01: Spot Drill)
N1 G20
N2 G17 G40 G80 T01
N3 M06
N4 G90 G54 G00 X3.5 Y5.0 S900 M03 T02
N5 G43 Z0.1 H01 M08
N6 G99 G82 R0.1 Z-0.2338 P300 F4.0
N7 G80 Z1.0 M09
N8 G28 Z1.0 M05
N9 M01
(T02: U Drill)
N10 T02
N11 M06
N12 G90 G54 G00 X3.5 Y5.0 S1100 M03 T03
N13 G43 Z0.1 H02 M08
N14 G99 G83 R0.1 Z-2.125 Q0.6 F8.0
N15 G80 Z1.0 M09
N16 G28 Z1.0 M05
N17 M01
- T01 – Spot drill for centering.
- T02 – U drill for initial drilling.
- G83 – Used for deep hole peck drilling.
This approach ensures chip removal, heat control, and precise depth management.
More FAQs About Peck Drilling
1. What is the difference between drilling and peck drilling?
Drilling is a continuous process, where the drill moves into the material without stopping until the final depth is reached. This works well for shallow holes but can cause chip clogging in deeper holes.
Peck Drilling, on the other hand, involves intermittent retractions, allowing chips to be cleared and coolant to reach the cutting edge. This method is preferred for deep holes and hard materials to avoid overheating and tool wear.
2. How do I determine the best peck depth?
The peck depth (Q value) depends on material hardness, drill bit size, and hole depth. A smaller Q value provides better control but increases machining time.
3. When should I use G73 instead of G83?
Use G73 for moderate-depth holes (3D–5D) where chip breaking is needed but full retraction is unnecessary. G83 is better for deep holes (5D+) where chip evacuation is critical.
4. Can Peck Drilling be used for all materials?
Yes, but adjustments are needed. Harder materials require smaller pecks and more coolant flow, while softer materials allow for larger pecks.
5. How does Peck Drilling affect tool life?
By removing chips and reducing heat, Peck Drilling extends tool life, preventing excessive wear or tool breakage.