S45C/S50C are two types of general-purpose steel known as “carbon steel for mechanical structural use” based on JIS standards. Both have medium carbon content, are versatile, readily available, and suitable for machining and heat treatment, making them widely used for manufacturing mechanical parts. The difference between them lies in their carbon content, which results in noticeable differences in performance and processing. Therefore, the appropriate material should be selected based on the intended use and specifications before determining the best processing method. To this end, we’ve sorted out an overview of S45C & S50C steel, comparing their chemical composition, physical and mechanical properties, processing methods, applications, advantages, and disadvantages.
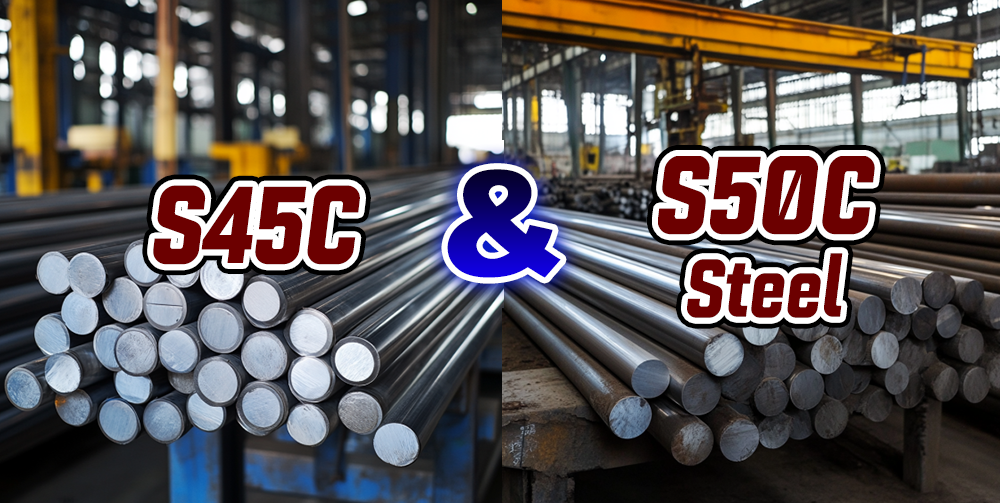
What is S45C Steel?
S45C steel is a type of medium carbon steel classified as SC material (carbon steel for mechanical structural use) with a carbon content of 0.45%. It is frequently used alongside SS materials due to its well-balanced mechanical strength and properties, as well as its high availability and cost-effectiveness. Its ease of processing makes it a commonly considered option when selecting iron-based materials. SC materials have regulations regarding the chemical substances they contain, limiting the amounts of phosphorus and sulfur, which can adversely affect metal strength. This ensures the quality of the steel.
S45C Steel Equivalent Standards
S45C Steel equivalents in other standards are:
- AISI/SAE: 1045
- DIN: C45
- EN: C45E or Ck45
- BS: 080M46
S45C Steel Chemical Composition
The ‘C’ in S45C stands for Carbon, and the ’45’ indicates the carbon content. The carbon content in S45C is between 0.42% and 0.48%, which roughly means around 0.45%. Additionally, in metals like iron and steel, the higher the carbon content, the stronger (and harder) the material becomes. According to JIS standards, low-carbon steels (such as SS400, which are mild steels) typically contain about 0.15 to 0.2% carbon, whereas S45C has a carbon content of around 0.45%, giving it greater strength.
C | Si | Mn | P | S | Cu | Ni | Cr |
0.42-0.48 | 0.15-0.35 | 0.60-0.90 | 0.030 or less | 0.035 or less | 0.30 or less | 0.20 or less | 0.20 or less |
*Extracted from JIS G 4051.
S45C Physical Properties (Density, Specific Gravity, and Magnetism)
Property | Value |
Melting Point | About 1,535°C |
Density (g/cm³) | 7.84 |
Young’s Modulus (GPa) | 205 |
Modulus of Rigidity (GPa) | 79 |
Poisson’s Ratio | 0.3 |
Coefficient of Thermal Expansion (ppm/K) | 11.9 |
Specific Heat at Constant Pressure (J/kg・K) | 490 |
Thermal Conductivity (W/m・K) | 45.0 |
*Density, specific gravity, and magnetism are properties that characterize substances and are classified as physical properties. Modulus of Rigidity is also known as “shear modulus,” “modulus of elasticity in shear,” and “Lamé’s second parameter.”
S45C Material Mechanical Properties (Hardness (HV) and Shear Strength)
Property | Normalized | Annealed | Quenched and Tempered |
Yield Point or Proof Strength N/mm² (plate thickness t mm) | 345 or more | – | 490 or more |
Tensile Strength N/mm² | 570 or more | – | 690 or more |
Elongation (%) | 20 or more | – | 17 or more |
Reduction in Area (%) | – | – | 45 or more |
Hardness (HBW) | 167-229 | 137-170 | 201-269 |
* Mechanical properties may vary depending on the machinery used, build conditions, and measurement conditions. The data above are measured under specified materials, equipment, and parameter sets according to standard test procedures and do not guarantee all parts made using this material. Hardness is one of the mechanical characteristics of a material, and is classified as a mechanical property.The surface can be hardened by heat treatment, so strength such as tensile strength and hardness will increase further after heat treatment.
Surface Treatments Commonly Used for S45C Steel
Below are some common surface treatments used for S45C:
- Iron Tetroxide Film (Blackening): Commonly used as a primer for painting.
- Parkerizing (Phosphating): Offers better rust prevention and wear resistance than blackening.
- Unichrome (White): Used as a post-treatment for zinc plating.
- Colored Chromate (Yellow and Black): Used as a post-treatment for zinc plating.
- Trivalent Chromate: Does not contain hexavalent chromium.
- Electroless Nickel Plating: Excellent in corrosion resistance, wear resistance, and adhesion.
- Low Temperature Black Chrome Plating: Ultra-thin film that provides excellent rust prevention and corrosion resistance.
- Hard Chrome Plating: Excellent in wear resistance.
These treatments enhance the material properties of S45C, making it suitable for various industrial applications depending on the environmental conditions and required performance characteristics.
S45C Steel Pros & Cons
What are the advantages and disadvantages of S45C? Let’s go through them one by one.
Advantages:
- Strength Through Heat Treatment: S45C can be strengthened by heat treatment.
- Ease of Machining Before Heat Treatment: Cutting is easier before heat treatment.
- High Versatility: It’s a widely distributed general-purpose material, making it cheaper and more accessible compared to other metals. For manufacturing gears, it’s common to perform cutting before heat treatment. For grinding, it’s typical to conduct heat treatment after cutting, followed by grinding for dimensional adjustments.
Disadvantages:
- Not Suitable for Welding: S45C is not ideal for welding.
- Rarely Used in Sheet Metal: It’s not commonly used in sheet metal applications.
- Prone to Rust: Requires surface treatment to prevent rusting.
S45C is well-suited for heat treatment, meaning its properties change easily with heat, which makes it less suitable for welding.
S45C Applications
In most cases, S45C is used as round steel (with mill scale), and square steel is almost not distributed. When using square steel or flat steel, S50C is typically used. Furthermore, S45C is often distinguished from SS400 based on the need for heat treatment; S45C is used where heat treatment is necessary, while SS400 is used where it is not. Due to its relatively low cost, S45C is used in a wide range of fields, primarily in mechanical parts: components, shafts, axles, pins, bolts, nuts, etc.
What is S50C Steel?
S50C is a steel grade specified in JIS G 4051, which sets standards for carbon steels for machine structural use. These carbon steels are referred to as S-C materials and are manufactured with the same level of care as killed steel, similar to alloy steels, hence they are of high quality. Among them, steels of grade S50C and higher are classified as high carbon steels, which means they exhibit greater hardness and tensile strength within the S-C material group. S50C is commonly available as plate material and is used in applications where quenchability may be insufficient to achieve desired hardness due to mass effect.
S50C Steel Equivalent Standards
S50C Steel is equivalents in other standards are:
- AISI/SAE: 1050
- DIN: C50
- EN: C50E
- BS: 050A50
S50C Steel Chemical Composition
The designation “S50C” in steel nomenclature indicates that it is a medium to high-carbon steel. The “50” represents an approximate carbon content of 0.50% in the steel, making it a higher carbon content material which enhances its strength and hardness.
Element | Composition (%) |
Carbon (C) | 0.47 to 0.53 |
Silicon (Si) | 0.15 to 0.35 |
Manganese (Mn) | 0.60 to 0.90 |
Phosphorus (P) | 0.030 max |
Sulfur (S) | 0.035 max |
Copper (Cu) | 0.30 max |
Nickel (Ni) | 0.20 max |
Chromium (Cr) | 0.20 max |
Source: JIS G 4051
Chromium (Cr) can be less than 0.30% if agreed upon by the parties involved in the delivery. Combined Nickel and Chromium (Ni+Cr) can be less than 0.45% if agreed upon by the parties involved. This table shows that S50C steel has a higher carbon content which classifies it as a high-carbon steel, leading to higher hardness and strength. The other elements have maximum values which are set to ensure properties like hardness, machinability, and weldability are within desirable limits.
S50C Steel Physical Properties
Physical Property | Units | Values |
Melting Point | °C | Approximately 1,660 to 1,680 |
Density | g/cm³ | 7.84 |
Young’s Modulus (Longitudinal Elastic Modulus) | GPa | 205 |
Rigidity Modulus (Transverse Elastic Modulus) | GPa | 82 |
Poisson’s Ratio | – | 0.25 |
Coefficient of Thermal Expansion | ppm/K | 11.7 |
Specific Heat at Constant Pressure | J/kg・K | 489 to 494 |
Thermal Conductivity | W/m・K | 44 |
The Rigidity Modulus is also referred to as the Shear Modulus, Shear Elasticity, or Lame’s Second Constant.
S50C Mechanical Properties
The higher carbon content of S50C compared to S45C (which typically has around 0.45% carbon) means that it has higher strength but less ductility, making it somewhat more brittle.
Property Type | Tempered | Annealed | Quenched and Tempered |
Yield Strength N/mm² (plate thickness t mm) | 365 min | – | 540 min |
Tensile Strength N/mm² | 610 min | – | 740 min |
Elongation (%) | 18 min | – | 15 min |
Reduction of Area (%) | – | – | 40 min |
Hardness (HBW) | 179 to 235 | 143 to 187 | 212 to 277 |
Note that mechanical properties can vary based on the specific application, build conditions, and measurement settings.
Surface Treatments Commonly Used for S50C Steel
The basic heat treatment conditions for S50C as defined by the Japanese Industrial Standards (JIS) are as follows. It is not necessary to strictly adhere to these conditions, as they should be modified to achieve the desired strength and hardness.
Process | Temperature and Cooling Method |
Normalizing | 810-860°C, Air cooling |
Annealing | About 800°C, Furnace cooling |
Quenching | 810-860°C, Water cooling |
Tempering | 550-650°C, Rapid cooling |
These heat treatment conditions are merely basic guidelines and do not have to be followed exactly. When manufacturing large and complex shapes from high-carbon steel such as S50C, there is an increased risk of cracking during heat treatment. If deformation is a concern, using a salt bath for martempering can be expected to improve the situation.
S50C Steel Pros & Cons
The advantages and disadvantages of S50C are largely similar to those of S45C:
Advantages:
- Hardness can be increased through heat treatment.
- Easily machinable before heat treatment.
Disadvantages:
- Prone to rusting, thus requiring surface treatment.
- Susceptible to cracking during heat treatment depending on the shape.
Since S50C is a high-carbon material, it is prone to cracking when heat treated, especially in thin or intricate shapes. It’s important to be aware that caution is needed with certain shapes, as they may require special considerations during processing.
S50C Steel Applications
S50C is utilized across various applications due to its high tensile strength and hardness. It is commonly used in parts where there are high local surface pressures or where high wear resistance is required. Consequently, it is employed in the manufacturing of components that are subject to strong forces such as pins, nuts, keys, shafts, bolts, and jigs, as well as in durable molds that demand high endurance. In our company, using S50C for mold parts larger than 400×400 mm provides a cost advantage. Despite its high hardness, S50C is easy to machine, allowing for straightforward drilling operations with general tools. To improve machining accuracy, increasing the cutting speed and preventing adhesion to the cutting edge are effective strategies. Additionally, since S50C is susceptible to magnetism, it is also well-suited for grinding and electrical discharge machining (EDM).
S45C vs S50C Steel Material: Which Is Better? Difference Between S45C and S50C Steel
Here’s a table to effectively compare the differences between S45C and S50C steel materials:
Property | S45C Steel | S50C Steel |
Carbon Content | 0.45% carbon | 0.50% carbon |
Form Shapes | Mainly round (wire, rods, polished bars) | Mainly square (plate, bar stock) |
Hardness | Slightly lower than S50C | Slightly harder due to higher carbon |
Applications | Mechanical parts, gears, general use | High-strength machinery parts, tools |
Strength | Moderate strength and toughness | Higher strength and wear resistance |
Weldability | Good, easier to handle during welding | Requires careful handling to avoid issues |
Cost | Generally comparable to S50C | Generally comparable to S45C |
Choosing between S45C and S50C steel should be based on the specific requirements of the application, including needed strength, desired form (round vs. square), and the processing techniques to be applied. Neither steel is inherently “better,” but each has characteristics that may make it more suitable for particular uses.