In the realm of precision manufacturing, CNC machining has revolutionized the way complex parts and components are fabricated. Among the various CNC machining capabilities, 4-axis and 5-axis machining stand out as vital techniques, each offering distinct advantages in their respective applications.
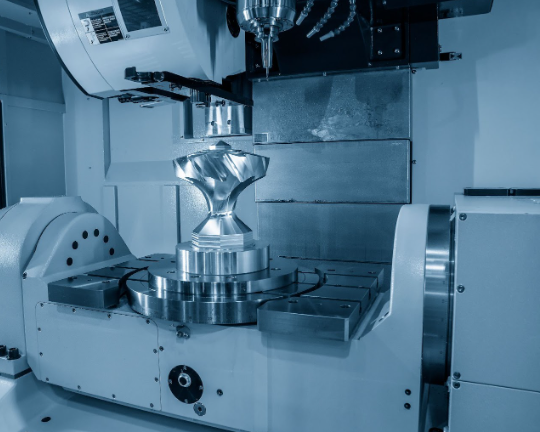
4-Axis CNC Machining
4-axis CNC machining involves cutting tools capable of movement along the X, Y, and Z axes, along with an additional rotary axis. Typically, this fourth rotary axis allows the workpiece to be rotated around the X, Y, or Z axis to enable cutting at different angles. This means that a 4-axis machine can produce complex, multi-sided parts more efficiently than traditional 3-axis machines.
This capability makes 4-axis machining particularly well-suited for producing parts that require intricate features on multiple sides, such as aerospace components, propellers, or engine parts. The additional rotational axis permits the machinist to access various angles without requiring repositioning of the workpiece, thereby streamlining the manufacturing process.
Index 4-axis CNC machining is when the 4th axis (A-axis) rotates whilst the machine is not cutting material. Once the correct rotation is selected, a brake is applied and the machine resumes cutting.
In continuous 4-axis machining, the machine can cut material at the same time as the A-axis rotation, simultaneously. This allows complex arcs to be machined, such as the profile of cam lobes, and helixes.
4-axis machining gives us the ability to machine angled features, otherwise not possible with a 3-axis machine. Bear in mind that 4-axis machining allows a single axis of rotation per fixture setup, so all angled features must be angled about the same axes, or additional fixtures put in place.
5-Axis CNC Machining
Moving beyond the capabilities of 4-axis machining, 5-axis CNC machines offer an additional level of freedom. In addition to the three linear axes (X, Y, Z) and the rotary axis, 5-axis machines include a second rotary axis, typically referred to as the A and B axes. This added degree of freedom enables the cutting tool to approach the workpiece from multiple angles and orientations.
The advantage of 5-axis machining is its capacity to create exceedingly complex geometries with a high degree of precision. This capability is particularly beneficial in industries such as automotive, medical, and aerospace manufacturing, where intricate, organic shapes are often required. By allowing the tool to reach areas that would be inaccessible with fewer axes, 5-axis machines can significantly reduce setup times and improve the overall accuracy of the machined parts.
There are two main types of 5-axis CNC machines: 3+2 machines, and fully continuous 5-axis machines.
In 3+2 axis machining two rotational axes operate independently to each other, meaning that the workpiece can be rotated to any compound angle in relation to the cutting tool for features to be machined. However, two axes rotation at the same time as machining is not possible. 3+2 machining can produce highly complex 3D shapes. Fully continuous 5-axis machining can simultaneously rotate the two rotation axis, at the same time as machining and the cutting tool moving linearly in XYZ co-ordinates.
Differences Between 4-Axis and 5-Axis CNC Machining
– 4-axis machining allows rotation on the A-axis, while 5-axis machining allows rotation on two of the three axes (A-axis, B-axis, and C-axis).
– 4-axis machining is suitable for machining parts that require machining on multiple sides without fixture change-overs, while 5-axis machining is capable of more complex and versatile operations.
– 5-axis machining offers the ability to machine angled features and complex curved 3D surfaces that are not possible with 4-axis or 3-axis machines.
Which is Better, 4-Axis, or 5-Axis CNC Machines?
Here is a comparison of 4-axis vs 5-axis CNC machines to assess which may be better depending on application needs:
– Machining Capabilities: 5-axis can machine complex geometries and internal/external features simultaneously from any approach angle. 4-axis is limited to rotary plus linear motions.
– Programming Effort: 4-axis programming involves linear and rotary interpolation. 5-axis requires complex simultaneous 5D interpolation, making it more difficult to code.
– Part Fixturing: 4-axis often requires multiple set-ups for complex parts. 5-axis can complete more in a single clamping due to more DOF, reducing fixture costs.
– Capital Investment: 4-axis machines have a lower upfront cost compared to a full 5-axis machine and controls. However, 5-axis saves overall with reduced setup/labor costs.
– Applications: 4-axis excels at rotary surface features. 5-axis is best for molds, dies, aerospace parts with deep internal contours/pockets at any angle.
– Productivity: When applicable, 5-axis processing time is significantly less than indexing multiple set-ups on a 4-axis machine.
In general, 5-axis machines are more versatile and suitable for very complex parts but require more expensive machinery and advanced programming skills. 4-axis remains viable for simpler profile work. The right solution depends on specific manufacturing needs and budgets.