Guide to Painting Aluminum Parts: Preparation, Steps & Best Paint for Aluminum
Professional & Uniform Industrial Painting Services
CNCLATHING.COM offers advanced industrial painting services as one of the surface finish solutions for various metal CNC machining parts or other products requrie post-processing, a variety of metal painting services can be provided, including spray painting, dip painting, brush painting and more, customized to meet your product specifications and performance requirements. Our professional surface treatment technologies ensure superior adhesion, corrosion resistance, and aesthetic appearance of manufactured parts. Our state-of-the-art facility employs skilled technicians who utilize modern painting equipment and techniques to deliver consistent, professional results across a wide range of industrial applications, from small components to large machinery parts.
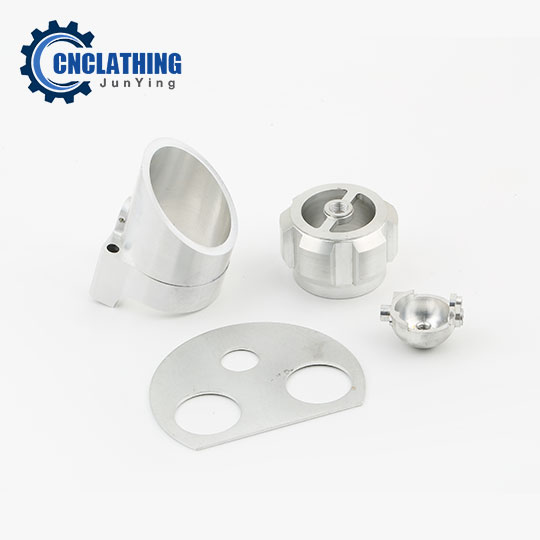
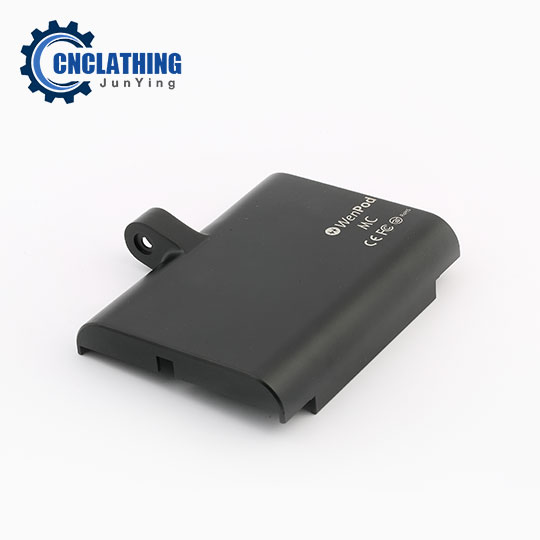
What Is Industrial Painting?
Industrial painting is a specialized finishing process that involves the application of protective and decorative coatings to manufactured parts and equipment using industrial-grade paint materials. This process goes far beyond conventional painting, as it requires extensive knowledge of different coating materials, surface preparation techniques, and application methods to ensure optimal adhesion and durability. Industrial painting can provide crucial protection against corrosion, chemical exposure, and wear, enhances the aesthetic appearance of products and can improve various functional properties such as electrical insulation, heat resistance, or UV protection.
Industrial Painting Process
The painting process typically starts with cleaning and degreasing the surface to remove any contaminants, followed by surface treatment methods such as sandblasting, chemical cleaning, or phosphating to create an ideal surface profile. The painting process itself utilizes various application methods, primarily based on the principle of paint atomization through high-pressure compression, which transforms the coating material into fine droplets for even application. Modern industrial painting often employs electrostatic charging of paint particles to ensure uniform coverage and minimize overspray.
Industrial painting techniques have evolved significantly, incorporating advanced technologies and methods to achieve specific performance requirements and effects. Spray painting remains the most versatile and widely used technique, offering excellent control over coating thickness and uniformity. Powder coating has gained popularity for its superior durability and environmental benefits, as it produces no volatile organic compounds (VOCs) and allows for nearly 100% material utilization.
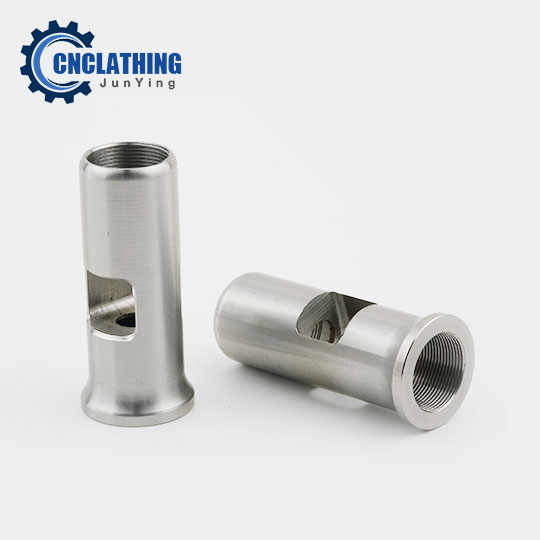
Advantages of Industrial Painting
- Enhanced corrosion resistance, with some coatings providing protection for up to 20 years in harsh environments.
- Improved chemical resistance against acids, solvents, and other aggressive substances.
- Better wear resistance and impact protection.
- Enhanced aesthetic properties with a wide range of colors and finishes available.
- Specialized properties such as anti-microbial protection, fire resistance, or thermal insulation.
The painting treatment requires strict adherence to environmental conditions, including temperature, humidity, and dust control, to ensure optimal results. Quality control measures, such as coating thickness measurement, adhesion testing, and visual inspection, are implemented throughout the process to maintain consistency and meet industry standards. The combination of advanced equipment, skilled technicians, and rigorous quality control procedures at CNCLATHING.COM ensures that our painting finihsing services meet or exceed customer specifications and industry requirements.
Types of Painting
Type of Painting | Description | Suitable for | Advantages | Disadvantages |
---|---|---|---|---|
Spray Painting | Atomized paint droplets for even distribution | General industrial applications | Cost-effective, fast, high coverage | Limited precision, potential for overspray |
Powder Coating | Electrostatic powder application with thermal curing | Metal components, structures | Durable, corrosion-resistant, environmentally friendly | Requires specialized equipment, thermal curing |
In-Mold Painting | Painting injection mold cavity before plastic injection | Plastic injection-molded parts | Color transfer via chemical bond, no post-molding painting | Limited to specific applications, requires specialized equipment |
Brush Painting | Traditional method using brushes or spray guns | Uneven surfaces, detailed work | High precision, control, and flexibility | Time-consuming, labor-intensive, potential for brush strokes |
Flow Painting | Liquid paint application with controlled pressure | General industrial applications | Fast, even distribution, high coverage | Similar to spray painting, potential for overspray |
Dip Coating | Immersing objects in liquid paint | Components and parts of various shapes and sizes | Easy to apply, uniform coating, cost-effective | Limited to certain shapes and sizes, potential for drips and runs |
Solvent-Based Coating | Fast-drying, temperature-resistant coating | Industrial applications, extreme weather conditions | Fast-drying, resistant to temperature fluctuations | Potential for environmental and health hazards, limited to certain substrates |
Texture Coating | Sustainable, textured coating for exterior surfaces | Exterior surfaces, concrete, weatherboard, painted brick | Durable, waterproof, prevents cracks and peeling | Limited to exterior surfaces, potential for texture inconsistencies |
Spin Coating | Uniform film application using centrifugal force | Flat surfaces, industrial applications | Thin, superhydrophobic, transparent, and organic | Limited to flat surfaces, requires specialized equipment |
Electrostatic Air Spraying | Modern painting application technique for smooth finishes | Automotive industry, metals, doors, windows, railings | Smooth, solid finish, efficient | Requires specialized equipment, potential for electrostatic charging issues |
High Volume Low Pressure (HVLP) Spraying | Turbine-based spraying for increased adhesion | Industrial applications, metals, plastics | Increased adhesion, reduced waste, and blowback | Requires specialized equipment, potential for turbine maintenance issues |
Airless Paint Spraying | Large-scale spraying for glossy, smooth coatings | Large-scale industrial applications, glossy coatings | Fast, efficient, high coverage | Limited to large-scale applications, potential for nozzle clogging |
Related News
FAQs
What is the purpose of industrial paint?
Protection: It provides a protective coating against corrosion, rust, and environmental damage, extending the lifespan of materials and structures.
Durability: Industrial paints are formulated to withstand harsh conditions, including extreme temperatures, chemicals, and abrasion, making them ideal for industrial environments.
Aesthetics: While functionality is key, industrial paint can also enhance the appearance of machinery, equipment, and structures, contributing to a more professional look.
Safety: Certain industrial paints are designed to be reflective or brightly colored to improve visibility, helping to prevent accidents in workplaces.
Compliance: Many industries must adhere to specific regulations and standards regarding materials and safety; industrial paints can help meet these requirements.
Ease of Maintenance: High-quality industrial paints can make surfaces easier to clean and maintain, reducing downtime and maintenance costs.
Insulation: Some industrial paints offer thermal or acoustic insulation properties, contributing to energy efficiency and noise reduction.
What are the applications of industrial painting?
Aerospace: aircraft components such as fuselages, wings, and interior components like seats.
Consumer Goods & Electronics: housings for smartphones, tablets, keyboards, and chargers, as well as industrial cabinets and enclosures.
Medical Devices: medical equipment such as MRI machines, X-ray devices, monitors, and infusion pumps to ensure a hygienic and corrosion-resistant surface.
Industrial Equipment: gears, casings, control panels, and safety guards to enhance their appearance and extend their lifespan.
Household Appliances: efrigerators, ovens, washing machines, and dryers.
Construction Industry: such as beams, columns, doors, and window frames to protect them from corrosion and enhance their appearance.
Manufacturing and Machinery: manufacturing equipment and machinery.
Military, Government, Energy, and Utilities: equipment and parts.
What is the difference between commercial and industrial painting?
Commercial painting typically involves painting the interior and exterior of commercial buildings such as offices, retail stores, restaurants, and hotels. The surfaces being painted are usually walls, ceilings, doors, and windows. Commercial painting projects often focus on aesthetics, providing a pleasant and professional appearance for customers and employees. These projects may also involve the application of specialty coatings for durability, cleanliness, or specific performance requirements.
Industrial painting, on the other hand, is performed on industrial and manufacturing facilities, warehouses, factories, and other heavy-duty structures. Industrial painting projects often include the painting of machinery, equipment, piping, storage tanks, and other large-scale surfaces. The primary goal of industrial painting is to protect the substrate from corrosion, abrasion, and other forms of damage, ensuring longevity and functionality. Industrial painting projects often require the use of specialized equipment, such as lifts and scaffolding, and may involve working in challenging environments, such as high temperatures or confined spaces.
What materials can be painted?
Various materials can be effectively used as painting substrates, each requiring specific preparation and consideration for optimal results. Metals like steel, aluminum, and galvanized steel need thorough cleaning and often primers to ensure proper adhesion and prevent corrosion, while plastics such as polyethylene, polypropylene, and ABS require surface preparation and adhesion promoters to overcome low surface energy.