Types of Polishing Process: Advantages, Disadvantages, Uses & Working Principle | CNCLATHING
Precision Metal Polishing & Buffing Service
Cnclathing.com provides a comprehensive metal polishing service capable of restoring precious metals, brass, bronze and other base materials to their original luster. With years of hands-on expertise, our polishing process meticulously removes tarnish, oxidation and blemishes through a multi-step technique to reveal the innate beauty of the metal subsurface.

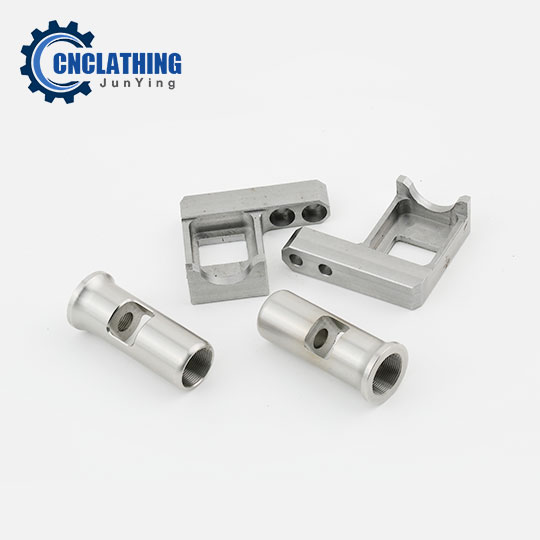
What Is Polishing?
A polishing service provides precision surface finishing through controlled abrasion. By gradually removing minor imperfections and reducing roughness, it renders the workpiece with a smooth, high-quality texture and meticulously achieved lustrous sheen. Whether targeting a satin, semi-bright or mirrored-level polish, the sequential use of specialized abrasives can refinement even the subtlest of details to microscopic precision. Beyond superior aesthetics, it increases durability by eliminating microscopic crevices where corrosion initiates– protecting the substrate in its intended application. Catering profiles and polishing compounds specifically to metal alloys, composites or other materials, an effective polishing service bolsters function through an optimized corrosion-resistant form while imparting an elegant refined quality sought after for both industrial and luxury goods.
Advantages Of Polishing Service
Polishing provides functional and aesthetic benefits that enhance the end product. It creates a smooth, potentially reflective surface that improves durability by removing microscopic scratches and burrs where corrosion and wear typically initiate. This strengthened barrier prolongs the service life of parts. Polishing also boosts precision and dimensional accuracy and can tighten tolerances. Visually, it imparts an elegant high-luster or blemish-free appearance that showcases the innate qualities of the material. This polished effect elevates the perceived quality and value of goods. Additionally, polishing allows for added functionalization, such as easing insertion of tight-fitting parts. Whether targeting performance or marketing gains, implementing a polishing step maximizes both form and function for optimal return through a refined finish.
Types Of Polishing Services Available
The Principle Of Polishing Services
The multi-step polishing process carefully refines the surface through a succession of increasingly finer abrasives to achieve the desired mirror-like perfection. It begins with the basecoat stage, roughly grinding away major irregularities using a coarse wheel or paper to set the canvas for finer work. Next, smoothing further levels lingering imperfections with a medium grit, preparing the substrate for the critical polishing phase. Here, the finest abrasives are applied to scrupulously remove minute flaws and impart a high sheen. When taken to the ultimate conclusion, the mirror finish stage delivers a surface of such exquisite smoothness that it mimics the reflectivity of an actual mirror. This sequential methodology allows for meticulous yet efficient refinement, culminating in a flawlessly blemish-free aesthetic many manufacturing and artistic applications demand.
Common Applications Of Polishing Services
Polishing is crucial for bringing out the shine and brilliance in precious metals and gemstones used in jewelry.
Wheels, trims, and other exterior auto parts are polished to a high gloss finish for aesthetic appeal.
Polishing ensures medical instruments and implants have perfectly smooth surfaces for minimal tissue damage and corrosion resistance.
Lenses, prisms and other optical components require damage-free highly reflective polished surfaces for maximum light transmission.
Doorknobs, faucets, door handles etc. are polished to an elegant luster for use in architecture and home applications.
Chips, CPU heatsinks, connectors and other precision parts rely on polishing for tight tolerances and corrosion protection.
Coins and medals minted or produced for collections undergo rigorous polishing to preserve mint condition.
Critical components like rifled gun barrels benefit from polishing’s ability to ease assembly and enhance durability.
Parts made through CNC, milling and turning are often polished for added quality control and corrosion resistance.
Polishing vs Buffing, What’s The Difference?
Polishing | Buffing | |
---|---|---|
Purpose | To achieve a high-shine, mirror-like finish |
To remove scratches, marks and |
oxidation to create a smoother | ||
surface | ||
Level of abrasion | Less aggressive, does not | More aggressive, uses abrasive |
remove surface layers | compound to remove flaws | |
Works best for | Already smooth surfaces that just need shine |
Surfaces with visible scratches or marks |
Possible to damage surface? |
Less likely as it is not very | Possible if too much pressure is |
applied as it can remove | ||
abrasive | surface layers | |
Effectiveness on deep flaws |
May not be as effective for | Ideal for removing visible scratches, marks or oxidation |
deep scratches or dents | ||
Resulting surface | High-shine, mirror-like and reflective |
Smoother with flaws removed |
but may still not be perfectly | ||
smooth | ||
Recommended application |
Jewelry, furniture restoration |
Car paint restoration, furniture restoration, metal workpieces |
Key steps | Apply polishing compound, polish using soft wheel/pad |
Apply buffing compound, buff |
using wheel to smooth out | ||
marks |
Related News
FAQs
What polishing methods are best for different materials?
Buffing wheel – Works well for smoothing softer metals like aluminium, copper, brass and tin. Also used for buffing paint finishes on vehicles.
Muslin buffing wheel – Suitable for buffing harder metals like steel due to its softer texture. Commonly used as a final polishing step.
Felt wheel – Excellent as a final polishing and lapping method for very hard metals like tool steel. Achieves a high luster.
Leather buffing wheel – Effective on plastics, composites and synthetics to impart a bright shine without marring sensitive surfaces.
Pumice – Coarse-grained volcanic stone used for initial smoothing of enamel, ceramic, porcelain and glass. Cuts quickly.
Rouge – Finely ground iron oxide compound is applied using muslin or felt for the final polishing of precious metals like gold and silver.
Zam/tripoli – Softer polishing compound suitable for final steps on brass, copper and bronze to achieve mirror finish.
Diamond slurry – Used to hone very hard materials like gemstones, tungsten carbide and monocrystalline tools to an ultra-smooth surface.
Silicon carbide paper – Durable papers suitable for intermediate polishing of hardened tool steels, carbide and other industrial materials.
What materials can you polish?
We can polish a wide variety of materials including metals, stones, ceramics, plastics and wood. Some common materials include brass, copper, aluminum, silver, granite, marble, glass and acrylic.
How long is the turnaround time?
For most standard polishing jobs on CNCLATHING, the turnaround time is 1-2 weeks. However, we can also offer rush services for urgent jobs with a shorter lead time.
Do you polish CNC machined parts?
Yes, we have extensive experience polishing aluminum, steel and stainless steel parts produced through CNC machining, milling and turning. This helps enhance features and protects against corrosion.
Can polishing improve the surface finish of CNC parts?
Absolutely. The polishing process can tighten tolerances and delivers mirror-like sheen to surfaces. This yields quality, precision and aesthetics beyond standard machining alone and aids quality assurance.
What’s routine care and maintenance of a polished surface?
● Dust regularly with a soft, dry cloth to prevent accumulation of dust particles that can act as an abrasive.
● Wipe down with a microfiber cloth moistened with glass cleaner or mineral oil. This picks up fingerprints and smudges.
● Apply a thin coat of car wax or natural oils like lemon or vegetable oil on metal surfaces monthly. This maintains protection.
● Stone surfaces can be cleaned with a pH-neutral stone cleaner and soft brush or polishing pad. Avoid acidic or alkaline cleaners.
● Plastic and acrylic surfaces should only be cleaned with diluted glass cleaner or plastic polish and a microfiber cloth.
● Avoid using harsh cleaners, abrasive scouring pads or chemicals on polished surfaces as they may dull the finish over time.
● Store delicate items in anti-tarnish boxes or with inhibitant papers if not in regular use to prevent oxidation.
● Have surfaces professionally re-polished every 6-12 months for maintained luster depending on delicate nature and use.