Types of Coating on Aluminum – How to Choose the Best Coating for Aluminum
Superior Custom Powder Coating Service
We offer full-service powder coating that can improve the durability and extend the lifespan of many metal components.We use fine-grain powders and can produce smooth, high-gloss finishes ideal for applications needing an attractive, long-lasting appearance while also increasing the part’s resistance to the elements.
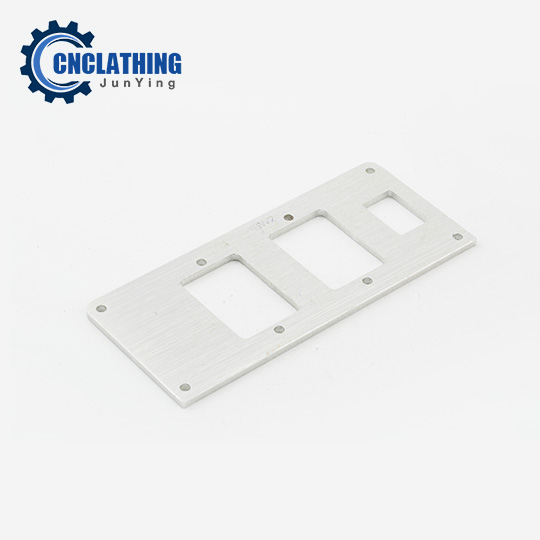
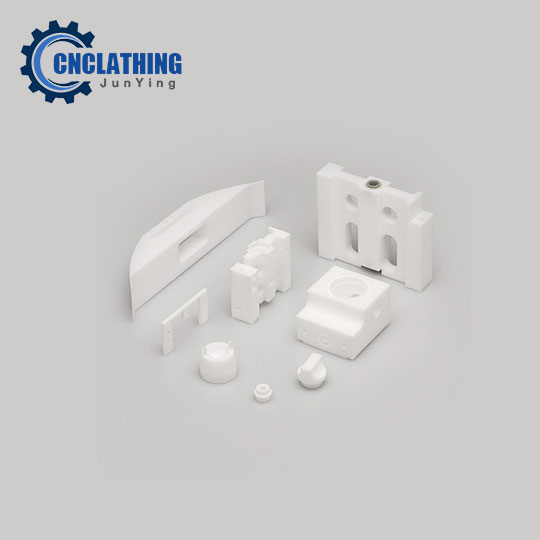
What is Powder Coating?
Powder coating is a finishing process that involves applying a dry, electrostatically charged powder to a surface, typically metal, to create a protective and decorative coating. The powder, made from thermoset or thermoplastic polymers, is sprayed onto a grounded surface using a specialized spray gun. After application, the coated surface is heated or cured, causing the powder to melt and bond into a smooth, durable layer.
This process offers excellent resistance to corrosion, scratches, and general wear, making it ideal for metal products exposed to harsh environments. Besides protection, powder coating also provides a vibrant, long-lasting color finish, enhancing both the appearance and lifespan of the coated objects.
Advantages of Powder Coating
Powder coating provides several key benefits over other surface finishing methods. It produces a very durable, long-lasting finish that protects metal parts from wear, corrosion and abrasion, helping to extend their lifespan considerably. Thanks to its hard protective layer, powder coated parts retain their like-new appearance for many years of use. Additionally, powder coating is solvent-free and emits virtually no VOCs, making it more eco-friendly than liquid paints. It can also be applied in a wide variety of vibrant colors and specialized finishes, from high-gloss to textured looks. Whether outdoors or in demanding industrial environments, powder coated parts maintain their good looks and structural integrity with resistance to rust, weathering, scraping and more.
What’s the Working Process of Powder Coating?
What Are The Different Types Of Powder Coating Available?
Instead of a chemical reaction, it softens when heated and hardens on cooling. Nylon and polyolefin types are thermoplastic.
Contains properties of both thermoset and thermoplastic powders for the best of both worlds. Cures like thermoset but provides flexibility like thermoplastic.
Includes coatings with extra features like Anti-microbial, anti-fingerprint, low-gloss or high-gloss textures. Self-healing variants are also available.
Creates brilliant metallic sheen in color patterns like bronze, gold, nickel or chrome effects. Gives a luxurious look.
Makes ordinary colors glow under UV/black light conditions. Used for safety markings.
Tailor made as per specifications for unique visual appearances, surface properties or curing behaviors.
Material | Characteristics | Advantages | Common Applications |
---|---|---|---|
5052 H32 Aluminum | Moderate strength, excellent corrosion resistance | – Good formability – High fatigue strength – Excellent marine resistance |
Marine equipment, fuel tanks, aircraft components, home appliances |
6061 T6 Aluminum | Heat-treatable, medium to high strength | – Excellent machinability – Good weldability – Good corrosion resistance |
Structural components, bicycle frames, automotive parts, electronics housings |
7075 T6 Aluminum | High-strength aluminum alloy | – Highest strength of common aluminums – Good fatigue strength |
Aerospace applications, high-stress components, military equipment |
MIC6 Aluminum | Precision cast aluminum plate | – Excellent stability – Consistent thickness – Good machinability |
Machine bases, fixture plates, inspection equipment |
AR400 & AR500 Steel | Abrasion-resistant steel | – Excellent wear resistance – High hardness – Impact resistant |
Mining equipment, heavy machinery, armor plating |
4140 & 4130 Chrome-moly Steel | Medium carbon alloy steel | – High strength – Good fatigue resistance – Heat treatable |
Aircraft parts, automotive components, industrial machinery |
304 Stainless Steel | Austenitic stainless steel | – Excellent corrosion resistance – Good formability – Non-magnetic |
Food processing equipment, kitchen appliances, architectural applications |
316 Stainless Steel | Marine-grade stainless steel | – Superior corrosion resistance – Better chemical resistance than 304 – Good strength |
Marine equipment, chemical processing, medical devices |
A36 Steel | Low carbon structural steel | – Good weldability – Cost-effective – Readily available |
Structural components, general fabrication, construction |
Hot Rolled Steel | Basic carbon steel | – Most economical – Good formability – Easy to weld |
Construction, heavy equipment, industrial applications |
Tool Steel | High carbon, high hardness steel | – Very high hardness – Excellent wear resistance – Good edge retention |
Cutting tools, dies, molds, industrial tooling |
Related News
FAQs
What safety precautions are necessary during powder coating?
Use appropriate protective equipment like gloves, gowns, respirators etc. depending on the materials being used. This prevents skin and respiratory exposure.
Work in a well-ventilated area and use local exhaust ventilation near powder application equipment to control airborne particles.
Powders should be properly contained and stored in their original labelled containers when not in use to avoid spills or accidental mixing.
all electrical equipment should be properly grounded to prevent static discharge and sparking during powder application and handling.
Smoking, eating and drinking should be prohibited in the powder coating work area to prevent accidental ingestion.
Properly label and dispose of any hazardous wastes like used powders, solvents or overspray according to regulations.
Follow the powder manufacturer’s safety data sheet for handling guidelines of specific powders. Some may require respiratory protection.
Use appropriate personal protective equipment like goggles to prevent dust and overspray from getting into the eyes.
In case of skin contact, promptly wash the area with soap and water. Contact a physician in case of eye contact.
Avoid powder contact with oxidizable materials and take fire prevention steps considering powder’s combustible nature.
Keep powder coating area clean and organized to prevent any trip and fall hazards.
How does the cost of powder coating compare to other finishes?
Upfront Equipment Costs: Powder coating requires specialized booths and guns which have higher initial setup costs than conventional spray equipment. However, these are offset over time by lower material and labor costs.
Material Costs: Powder raw materials are cheaper than liquid paints on a cost-per-gallon basis. There is also very little overspray waste compared to wet spray techniques.
Labor Costs: Powder coating has simpler application processes with less prep work than painting. This translates to less labor hours needed per coated part. Curing also takes place in stationary curing ovens versus additional time for drying/curing of wet paints.
Overhead Costs: Powder booths require significantly less space than wet paint spray booths. There are no solvents used so ventilation and emissions treatment are less expensive to implement and operate.
Re-Coat Costs: Powder coated finishes are more durable and last much longer than wet paint, often doubling the time before a re-coat is needed. This saves on long term maintenance costs.
Energy Costs: Curing powders consumes 25-50% less energy than baking liquid paints due to their 100% transfer efficiency and reduced.
What types of metal are best suited for powder coating?
The metals best suited for powder coating are steel, aluminum and other alloys that can withstand the high baking temperatures required to cure the powder finish. Steel and aluminum are ideal candidates as they have good stability at elevated heat levels without adverse effects like distortion or degradation. These metals form a strong bond with the electrostatically-applied powder, resulting in a exceptionally durable, corrosion-resistant coating.
What is the typical turnaround time for a powder coating project with Cnclathing?
Cnclathing aims to complete most powder coating jobs within 5-7 business days from receiving parts, though more complex projects may take up to 2 weeks depending on workload. Rushing is available for urgent requests.
Does Cnclathing offer powder coating of small custom batches?
Yes, while Cnclathing is best suited for volume production runs, they can powder coat small custom batches as low as 10-15 pieces. A smaller minimum quantity surcharge may apply.
What surface prep options does Cnclathing provide before powder coating?
Cnclathing’s surface preparation services include degreasing, derusting, passivation and mechanical treatments like blasting. This ensures parts get the precise profiling needed for optimal coating adhesion and longevity.