Types of Metal Finishes – Most Common and Durable Metal Finish
High-Quality Lustrous Satin Finish (Paint) Services
Satin Finish Service at CNCLATHING.COM is capable of delivering precise and uniform metal surfaces, focusing on performance and aesthetic appeal – the two most critical requirements for quality metal surface finishing. We offer comprehensive Satin Finish solutions, including industry-leading Long Grain, Non-Directional, Cross-Grain, and standardized #3/#4/#6 satin finishes. Our Satin Surface Finishing expertise extends across multiple materials including stainless steel, aluminum, brass, and architectural bronze, ideal for applications in elevator/escalator components, food processing equipment, pharmaceutical facilities, and high-end architectural projects. Whatever your specific satin finishing needs, our technical team ensures consistent quality and superior aesthetic results while maintaining functional requirements such as non-slip properties and coating preparation.
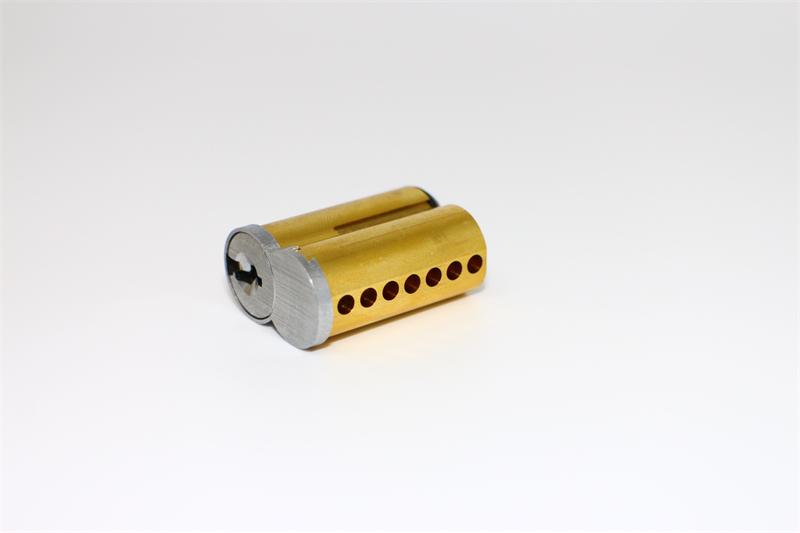
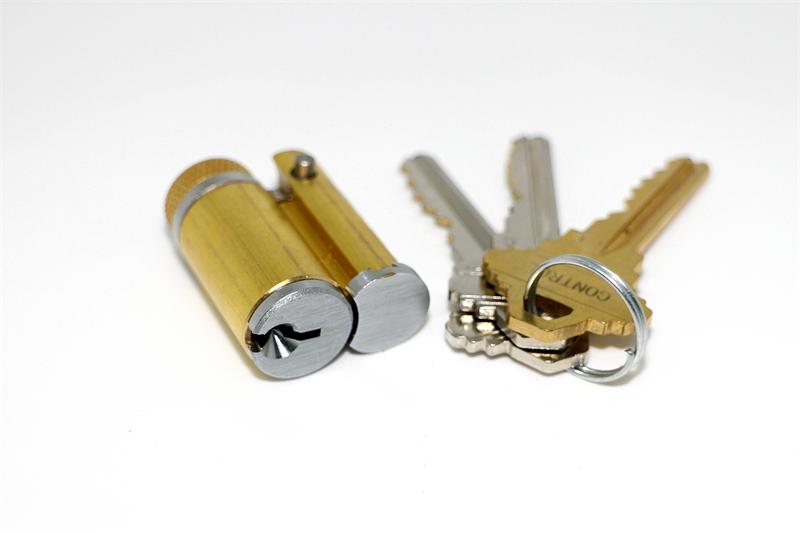
What Is Satin Finish?
The satin finish is a type of paint sheen that offers a medium level of gloss and light reflectiveness, sitting between the low-luster matte or flat finishes and the high-sheen semi-gloss or gloss finishes. It provides a subtle, velvety sheen that is more reflective than eggshell, but not as shiny as semi-gloss. Satin finishes are durable, easy to clean, and work well in high-traffic areas like hallways, family rooms, and children’s rooms. The increased reflectivity compared to matte finishes helps to conceal minor wall imperfections, while still maintaining a softer, less glossy appearance than high-sheen paints. Satin finishes strike a balance between the coverage and flatness of matte paints and the washability and light reflection of glossier paints.
Beyond interior paint, satin finishing is also commonly used as a precision metal surface treatment. It involves using abrasive belts, wheels, or flaps to homogenize the metal surface, removing defects or marks from previous processes like welding or bending. This creates a uniform, matte-like appearance that is durable and easy to maintain, making it suitable for a variety of applications where a subtle, refined look is desired.
How to Get a Satin Finish on Metal Parts – Satin Finishing Process
The satin finishing process for metal parts involves a comprehensive approach using mechanical and sometimes chemical treatments to achieve a uniform appearance with a subtle luster. Essential equipment and materials include various grit sandpapers (coarse to fine), polishing wheels or grinders, cleaning solutions, abrasive pads, polishing fluids or oils, cleaning cloths, and optional protective coatings. The process works on various metals including stainless steel, aluminum, and brass, each requiring specific techniques to achieve optimal results while maintaining the material’s inherent properties and corrosion resistance.
Types of Satin Finishes and Paints
Finish Type | Description | Appearance | Grit Range | Ra Value |
---|---|---|---|---|
#2B/Mill Finish | Unpolished state of cold rolled material from the mill, exhibiting some luster but not reflective | Lustrous, not mirrored | N/A | N/A |
#3 Satin Finish | Polished on a wide belt machine, resulting in a coarser appearance | Coarse | 60-80 Grit | 50 Ra |
#4 Satin Finish | Industry standard satin finish, similar to #3 but with finer final polishing | Smooth, refined | 120-180 Grit | 32 Ra Max |
#4 Long-Grain Finish | #4 satin with grain running continuously along the length, also called “hairline” | Smooth, linear grain | 120-180 Grit | 32 Ra Max |
#4 Cross-Grain Finish | #4 satin with grain running in the horizontal direction | Smooth, horizontal grain | 120-180 Grit | 32 Ra Max |
#4 Non-Directional Satin Finish | #4 satin with random orbital finish, no defined grain direction | Smooth, non-directional | 120-180 Grit | 32 Ra Max |
#6 Satin Finish | Finer and smoother than #4, achieved with 240-320 grit final polishing | Very smooth, refined | 240-320 Grit | 20 Ra Max |
#6 Long-Grain Finish | #6 satin with grain running continuously along the length, also called “hairline” | Very smooth, linear grain | 240-320 Grit | 20 Ra Max |
#6 Cross-Grain Finish | #6 satin with grain running in the horizontal direction | Very smooth, horizontal grain | 240-320 Grit | 20 Ra Max |
#6 Non-Directional Satin Finish | #6 satin with random orbital finish, no defined grain direction | Very smooth, non-directional | 240-320 Grit | 20 Ra Max |
Related News
FAQs
What grade of stainless steel can be used for a satin finish?
Satin finish can be applied to various grades of stainless steel, but the most commonly used type is 304 stainless steel. This grade is favored for its excellent corrosion resistance, good formability, and weldability, making it suitable for a variety of applications, including architectural elements and food processing equipment. Another typical alloy that often applies a satin finish is 316 stainless steel, which offers enhanced corrosion resistance, particularly in marine environments or where exposure to harsh chemicals is a concern. It can also be finished with a satin appearance and is used in similar applications as 304.
Can I use a satin finish with other types of surface treatments?
Yes, you can use a satin finish with other surface treatments, such as semi-gloss or gloss finishes. Mixing satin and semi-gloss paints is a common practice that allows you to achieve a desired sheen that falls between the two, providing both durability and a softer appearance.
Is a satin finish suitable for aluminum?
Yes, a satin finish is suitable for aluminum and is often used in various applications due to its appealing aesthetic and functional properties. Satin finishes provide a lightly glossed surface that is smoother than matte finishes but less reflective than high gloss, making it an ideal choice for those who want a balance between shine and subtlety. This type of finish effectively conceals imperfections and is easier to clean, as it does not show fingerprints or watermarks as prominently as high gloss finishes do. Additionally, satin finishes can enhance the durability of aluminum by providing a protective layer that helps resist corrosion and wear, which is particularly important in environments where aluminum components are exposed to moisture and contaminants.
Satin vs matte vs gloss finish, what are the differences, and which one to choose?
Satin paint is a hybrid finish that sits between matte and gloss. It has a slight sheen, creating a gentle, inviting glow. Satin paint is more durable and moisture-resistant than matte, making it a popular choice for high-traffic areas. The slight sheen helps to hide minor surface imperfections, and the smooth finish is easy to clean.
Matte paint, also called flat paint, has no sheen or shine. It has a velvety, uniform appearance that diffuses light rather than reflecting it. Matte paint is great for concealing surface imperfections, as the lack of sheen minimizes the visibility of flaws. It is less durable and harder to clean than glossier finishes. However, matte paint offers better coverage and is easier to touch up than higher-sheen options.
Gloss paint has the highest level of sheen, creating a bright, reflective, and polished finish. It is extremely durable and stain-resistant. Gloss paint’s high sheen can help to visually brighten and enlarge spaces. However, it is not as forgiving of surface imperfections, as it will highlight any bumps or textures. Gloss paint requires a smooth, well-prepared surface for the best results.
Brushed vs satin finish stainless steel, which one to choose?
Brushed Finish is best suited for applications where a textured, industrial look is desired. It hides small scratches well but requires more maintenance. A satin finish is ideal for a sleek, refined look with lower maintenance needs. It is versatile for both residential and commercial use but can show scratches more easily.