Passivation Of CNC Tool: What Is It, How Does It Work
Specialized High End Passivation Services for Metals
CNC Lathing offers specialized Passivation Services to a variety of industries, including medical, aerospace, automotive, and military sectors, providing essential protection against corrosion, rust, and chemical attack. Our processes, which include nitric and citric passivation, as well as Acid-Alkaline-Acid (AAA) treatments, are customized to the specific grade of stainless steel or titanium alloys, ensuring compliance with stringent standards such as ASTM A967 (Types II, VI, VII, VIII) and AMS 2700 (Types 1-8). With additional services like ultrasonic cleaning and vapor degreasing, we guarantee optimal surface preparation for passivation. CNC Lathing’s internal quality assurance follows rigorous ASTM and MIL-SPEC standards, ensuring reliable, high-quality results with fast turnaround times. With in-house quality assurance testing, fast quotes, and expedited turnaround times, CNC Lathing guarantees reliable, high-quality passivation solutions for both small-scale precision needs and large commercial orders.
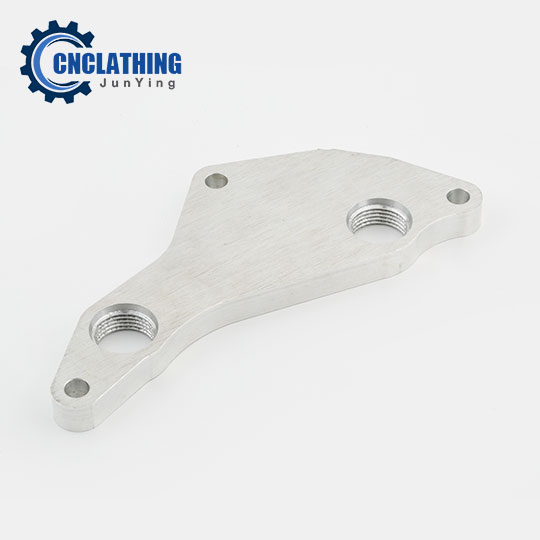
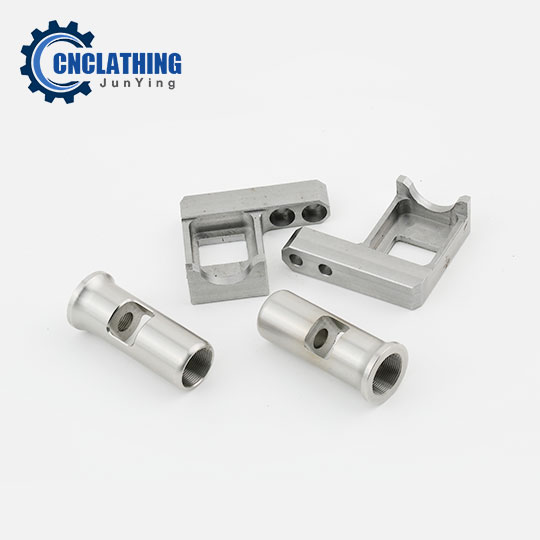
What is Passivation?
What does passivation do? Passivation process is a chemical surface treatment applied to stainless steel aluminum, and other metal components to enhance their resistance to oxidation, rust, and mild chemical attacks. During the manufacturing process, operations like milling, buffing, cutting, and lapping can introduce iron contaminants onto the surface of stainless steel. These contaminants can act as corrosion sites and lead to premature component failure. Passivation does not significantly change the appearance of the metal. The treated surface remains the same, maintaining its natural metallic color.
Benefits of Passivation Surface Treament
Corrosion Resistance: Passivation significantly reduces the risk of rust and corrosion, extending the life of your stainless steel components.
Enhanced Durability: The passivation process forms a robust oxide layer that shields the metal from exposure to harsh environments.
Increased Reliability: By removing contaminants from the surface, passivation minimizes the risk of premature failure, ensuring the long-term reliability of your parts.
The passivation process at CNC Lathing involves the removal of free iron from the surface, creating a chromium- and nickel-rich oxide layer that shields the stainless steel from further corrosion. Our services are tailored to ensure optimal results for your specific grade of stainless steel, ensuring your components meet and exceed industry standards.
How Does Passivation Process Work?
Our passivation process typically follows these steps:
Cleaning Cycle: Removal of oils, residues, and contaminants.
Nitric Acid Bath: Dissolves free iron and other foreign materials. The parameters of this bath are customized to your specific stainless steel grade.
Post-Treatment: Additional cleaning cycles, including ultrasonic cleaning and vapor degreasing, can be applied as pre-treatment for subsequent plating services.
Passivation Specifications & Standards
Passivation of stainless steel is governed by various industry specifications to ensure consistent quality, safety, and effectiveness. These standards define the specific processes, methods, and testing required to achieve proper passivation. CNC Lathing's passivation services conform to a variety of industry standards, including:
Types of Passivation
There are several types of passivation, each suited to different materials and environmental conditions. At cnclathing.com, we can offer the pro passivation coating service based on the specific properties of the metal and the intended application:
Type | Typical Metal(s) | Process Description |
---|---|---|
Chemical Passivation |
Stainless steel |
Uses acids (nitric or citric) to remove contaminants and promote oxide layer growth. |
Electrochemical Passivation |
Aluminum, Titanium |
Electrolytic process forming a thick oxide layer (e.g., anodizing). |
Thermal Passivation |
Stainless steel, Aluminum |
Heat treatment to form a protective oxide layer. |
Phosphate Coating |
Steel |
Chemical process applying a phosphate layer that resists corrosion. |
Chromate Conversion Coating |
Aluminum, Zinc |
Creates a chromate layer to prevent corrosion, often used in aerospace. |
Natural Passivation |
Aluminum, Stainless steel |
Metals naturally form a protective oxide layer when exposed to air. |
Laser Passivation |
Stainless steel |
Uses lasers to create a controlled oxide layer. |
Plasma Passivation |
Various metals |
Utilizes plasma fields to improve surface oxidation and corrosion resistance. |
Applications of Passivation Surface Treadment
Our passivation services meet the demanding needs of various industries:
Medical-Grade Passivation – CNC Lathing provides precision passivation for medical components, including surgical instruments and implants. Our processes are tailored to meet ASTM F86 standards, ensuring that your medical devices are safe and durable for long-term use.
Aerospace and Military Applications – For aerospace and military clients, we offer specialized passivation for high-performance alloys used in aircraft and military equipment. Our treatments conform to AMS-QQ-P-35A and other military-grade standards, ensuring your parts can withstand extreme conditions.
Automotive and Industrial Solutions – From ball bearings to fasteners, our passivation services protect critical components in automotive and heavy industrial machinery. With our high-volume barrel plating lines, we can handle both large and small orders efficiently.
Related News
FAQs
Why Choose CNC Lathing for Passivation Surface Treament Services?
At CNC Lathing, quality assurance (QA) is a top priority. We perform most of our QA testing in-house, in our qualified laboratory, ensuring that our processes meet ASTM and MIL-SPEC standards. This internal QA allows us to deliver consistent, reliable results for every order—no matter the size or volume.
1. Customized Solutions
Our passivation processes are customized to the specific grade of your stainless steel or titanium alloy. Whether you require commercial passivation or precision medical-grade cleaning, we ensure optimal results that meet your exact specifications.
2. Compliance with Stringent Standards
We adhere to industry-leading standards, including:
ASTM A967 (Types II, VI, VII, VIII)
AMS 2700 (Types 1-8)
ASTM A380
MIL-STD-753
These standards guarantee that corrosion-resistant alloys receive the highest level of protection for your applications.
3. Rigorous Internal Quality Assurance
Our in-house laboratory conducts thorough quality assurance testing, conforming to ASTM and MIL-SPEC standards. We perform tests such as the Water Immersion Test, Salt Spray Test, Copper Sulfate Test, and Potassium Ferricyanide-Nitric Acid Test to confirm the effectiveness of the passivation process.
4. Fast Turnaround
At CNC Lathing, we prioritize efficiency. We offer same-day quotes and expedited turnaround for urgent projects. Our streamlined processes ensure that your order is completed on time, without compromising quality.
When is Passivation of Stainless Steel Required?
Passivation of stainless steel is required when the metal surface has been exposed to conditions that could introduce contaminants, particularly free iron particles, which can lead to corrosion and rusting over time. These contaminants often result from machining, cutting, milling, welding, or other fabrication processes that expose the metal to iron or other non-stainless materials. Passivation is also necessary when stainless steel components will be used in corrosive environments or applications requiring enhanced corrosion resistance, such as in medical devices, aerospace equipment, military hardware, or marine environments. Additionally, passivation is recommended after surface treatments like heat treatment or welding, which can form oxide films or other residues that need to be removed to restore the material’s protective properties.
Which Passivation Type is Best for Marine Environments?
For marine environments, where exposure to moisture, salt, and harsh conditions is constant, the best passivation methods for the metal parts must offer strong corrosion resistance.
1.Nitric Acid Passivation (Chemical Passivation) for Stainless Steel (especially grades like 316 and 304)
Nitric acid passivation enhances the protective chromium oxide layer on stainless steel, which resists corrosion in chloride-rich environments like seawater.
2. Anodizing (Electrochemical Passivation) for Aluminum
Anodizing greatly increases the thickness of the natural oxide layer on aluminum, providing excellent protection against saltwater corrosion.
3. Chromate Conversion Coating (Alodine) for Aluminum
A chromate conversion coating offers good corrosion resistance in marine environments by creating a protective layer that prevents corrosive elements from reaching the metal underneath.
4. Phosphate Coating for Steel (with a Protective Top Coat)
Phosphate coatings by themselves are not enough for marine environments but are often used as a base layer before applying additional coatings such as paint or powder coatings. They improve adhesion and provide basic corrosion resistance.
5. Thermal Passivation for Stainless Steel
Heat treatment can enhance the formation of the chromium oxide layer, especially in high-alloy stainless steel grades like 316, improving their resistance to chloride-rich environments.
6. Natural Passivation for Stainless Steel (316)
Stainless steel grades with higher chromium and molybdenum content (like 316) naturally form a strong oxide layer when exposed to oxygen, providing good resistance to saltwater.